Introduction: Hen House From Old Garage Cupboards
Nothing is as wonderful as home grown eggs. For our hen house I used a pile of one-by-twelve pine boards left over from removing our old garage cupboards. I have found that with any project, I spend much more time planning than on construction, and I cannot overemphasize the importance of getting your plans straight before you begin cutting lumber.
The size of our hen house was largely dictated by the quantity and dimensions of the boards I had available. In addition to considering the materials, I wanted to make the hen house predator proof, easy to clean and care for, with food and water available at all times. It also seemed like a good idea to make room to store the hen food and other paraphernalia in the hen house. This is the third hen house I've built, and in the past I have always attached a nest box to the outside of the hen house. This time, I felt that I needed a more secure, weather-proof nest box, so I decided to incorporate the nest box and food storage area inside a walled-off cupboard at one end of the hen house.
Step 1: Framing the Hen House
You will be surprised at how many two-by-fours it takes to build the basic frame for the hen house. Note the metal plates at the end member joints. The two end frames and inner-wall frame were laid out on a flat surface and secured with Simpson Strong Ties (on both sides).
It's a bit tricky standing the end members up and getting them to stay in place while you're screwing them to horizontal cross members. A helper would be handy for this step. I also dipped the bottoms of the legs in a can of wood preservative.
Not all of the framing is shown in this photo. Initially I was just going to have the cupboard doors extend up to the roof, but I decided to make the door tops square, so I added a few pieces of framing above the doors. Note, this added framing needs to extend an inch below the upper siding pieces to act as door stops.
Step 2: Sorting the Lumber
One of the most complicated aspects of this project was dealing with the old lumber. Many of the boards were warped, and I had to figure out how to make the most from every board. I found the best approach was to first figure out all the longest boards I would need, and where they would go. I saved the best boards for the front of the hen house, and the worst boards went on back and on the roof.
Note: the wood shown in this picture is mostly in stacks of four boards of each length, which is difficult to see in the photo. Also, the roof boards are not shown in this photo.
Step 3: Nest Box Detail
The nest box was the most complicated bit of carpentry for this project. I got some general recommendations from the internet about the size of the nest box and the height above the floor. The nest boxes are about twelve inches in all dimensions. I put the openings about twelve inches above the floor. I also decided to add a roost in front of the nest boxes. In the past, I have had problems with the hens roosting on the entrance to the nest boxes and fouling the nest. I'm hoping that adding a roost in front will solve that problem. I'm not thrilled at the idea of having the roosts cross over each other, but I could add a guard on the upper roost later, if it becomes a problem.
Note that the floor screen rests on top of the lowest two-by-four cross members. One consideration for me was to position the nest box (and roost) high enough so the floor screen could be lifted up enough on the back edge to let the front edge of the floor clear the front two-by-four rail and drop down for cleaning.
In the photos you can see that some of the two-by-four cross members around the nest boxes and cupboard are positioned with the narrow edges facing outward. This was to allow more room to get things in and out of the cupboards. It did, however, present a problem for adding the latches later, as the edge of the vertical two-by-four divider wasn't wide enough to put both latches in the same position.
For the bottom of the cupboards, I had the option of mounting the boards on top of the framing or underneath the framing. I opted for attaching the bottom boards underneath so I would have a bit more room and less spider habitat. I added extra screws to hold the weight of the feed sack. I also added some upper shelves for storage.
Step 4: Finished Nest Box and Food Cupboard
Here's the nest box with the doors and additional siding pieces in place. I don't think it was really necessary to add the "half moon" cut outs and fill-strip for the back of the nest box to the door, but it seemed like nice idea at the time. If I had it to do over again I would leave those pieces out.
Note the "bird-house" structure mounted on the back left side of the hen house in this photo, this houses their water tank, which is connected to the automatic watering system (discussed in a later step).
Step 5: Notes on Design and Materials
When you are using reclaimed lumber, the dimensions of your boards will play a role in the design. When I first measured a couple of the boards in my stack of old lumber I mistakenly assumed that all the boards were nearly twelve inches wide (they were actually 3/4-inch thick by 11 1/2- to 11 3/4-inches wide). Because of this oversight, in the final design I ended up having to rip some fill fill strips to make up the difference. The lesson here is to be sure you know what materials you've got before you start cutting boards.
The overall dimensions for the hen house frame were five feet wide, by three and a half feet deep. Finished dimensions are 63-inches by 43 1/2-inches, with the siding. The main structure is 49-inches tall on the front side, and 43-inches tall in back. The roof boards are 45-inches long with a one-inch overlap on the back side. I extended the siding an inch or so lower than the bottom framing cross members to make room for the cupboard bottom boards be screwed to the bottom of the frame and still be covered by the vertical siding.
Using these nearly twelve-inch wide boards, the front, back, and roof are five boards wide, the side walls are cut at a 1:5 slope, 49-inches on the tall end to 43-inches long on the short end. It took about three and a half boards per side, and remember, there are three side walls, counting the inner wall and cupboard doors. With doors on each end and nest entrance holes on the inner wall, the side walls were pretty complicated. One end is all doors, and there is a door on the other end for the hens to get into their pen. Because of all the doors I needed to rip a lot of the side boards to make the doors come out the right width and to cover the frame parts where the hinges mount.
In addition to the re-purposed one-by-twelve pine boards, I bought 18 8-foot fir two-by-fours, five or six pine one-by-twos (actually 3/4 by 1 1/2-inches) for screen frames, a two-by-three stud (I didn't know they made these) for the roost. I liked the shape of the some stair rail that they had, so I bought a six-foot piece of this for the main roost (this stuff turned out to be pretty expensive, and I could have just used more of the two-by-three stud material). In the past I have used closet dowels (coat hanger rail) for the roosts, but the internet says chickens like to roost flat footed, rather than clutching, so I went with the wider lumber for the roosts.
The two-by-fours were pretty inexpensive compared to the other materials ($2.50 each). The single biggest expense for this project was the hardware: screws (several boxes for framing and attaching siding), hinges, latches, Simpson Strong Ties (about 30 of these at $0.75 each, I could have probably gotten by with just putting these on one side instead of both sides of the end frames).
There are probably over a hundred individual wooden parts in this project, each part has to be measured cut and mounted at each end, that works out to a lot of sawing and screwing. I bought special "flip-drill-drive" attachments (size 8 and 10) for the power drill that have a drill bit for making pilot holes on on one end and a screw driver on the other, you just slide a little ring forward to flip between the drill bit and screw driver. This was a big time saver and well worth the money.
If you can start with all your joints as square as possible the rest of the job will go much easier. I have a power miter saw, but it takes a lot of tweaking to get this saw to make a square or 45 degree angle cut. I don't trust the pre-set notches on the miter saw, and I test all my saw set ups on scrap boards to check for squareness. For the 45 degree angle cuts, I make a test cut and position the two 45 degree angle pieces so I can check them with a square. Try to get as many cuts done as you can without having to reset your saw. For ripping boards, I used a Skill Saw and eye-balled it to try to stay on line. This doesn't work very well, but since I don't own a table saw, the next best thing was to clamp a long board at the appropriate distance from the line and run the Skill Saw along the edge of the clamped board. A belt sander is also helpful for truing up the edges a bit.
The final pictures show a number of boards that don't quite reach the top, or meet correctly at the corners. That's just how it is when you're using scrap lumber. We're making a hen house, not a piano. After a final sanding and sealing, I am going to put some angled metal flashing (two inch by two inch) on the corners and around the top to hide some of the defects.
For the roof I bought a sheet of poly-carbonate plastic roofing (26-inches by 12-feet) cut into three 48-inch long pieces. This would be enough roofing to cover a six-foot width, but I overlapped the sheets by about six inches. You can cut this material with a jig saw, but I found that a pair of tin snips worked best. You also need to buy the plastic supports that go under the roof panels where you screw them down. You will need enough plastic support pieces for at least two rows of screws. They sell special screws with rubber grommets to use with this roofing, but I had enough of these left over from a previous project to finish this job.
I also had some half-inch mesh wire on hand. I used three pieces, all about 45 1/2-inches wide: one 41 1/2-inches long for the floor panel; one 28 inches tall for the front door, and one about six inches long for the back vent.
Tools: Power miter saw, Skill Saw, jig saw, lots of clamps, power drill/screw driver, sanders, square, chisel, tin snips, assorted drill bits, file, hammer and nails.
Screws: I used 2 1/2-inch number two deck screws [Correction: the screws are #10, the philips head size was #2] for the framing, it took at least one full box of these, I had some on hand and used them all and had to go back for more, so you may need two boxes. Same for the 1 5/8-inch number 2 screws I used for the siding. I also bought some shorter 1 1/4-inch screws to mount the treads to the ramp. I used 2-inch long number 8 wood screws for mounting the door boards to the rails that the hinges attach to. I went through a lot of these, something like eight per board, so figure on buying a lot of them.
U-Nails: We used to call these staples, 3/4 inch size works well for attaching the screens, but hold them with pliers and keep them straight while you're pounding them in or they'll poke through the sides of the frame.
Recycled Pine 1 x 12-inch Boards:
Front: four 29-inch boards (for the hatch), four 16 1/2-inch boards (for the lower front), one 49-inch board (for the closet side), one 3 1/2-inch wide 49-inch long top trim strip (above hatch), plus various fill strips to even things up. There is also a 1 1/2-inch by 3/4-inch trim strip placed on edge next to the screen door to fill in the edge of framing at the left side of front opening. This piece acts as a door stop for the front hatch on that side.
Sides walls: (three including the inner wall) for each wall you need three and a half boards, cut on an angle to fit the roof line. These ranged from 49 inches long to 43 inches long. Many of these side boards had to be ripped at appropriate widths for making the doors and hinge mounting pieces. You can cut round holes for the hens, or just cut the openings square.
Back: four 34 1/2-long pieces below the vent (vent is 4 1/2-inches tall), one 42 1/2-inch nest box side (I positioned this to cover the entire nest box between the framing so there wouldn't be a gap in the side of the nest. Because I didn't measure my boards correctly, I had to cut a one-inch wide fill strip to cover the exposed framing at the corner, and another 2 1/2-inch wide by 42 1/2-inch long fill strip for the other corner. This strip extends up to the roof and covers the side of the screen vent. Next time I would make the whole hen house a bit narrower to avoid having to cut so many fill strips. I also needed to buy one piece of new 3 1/2-inch by 3/4-inch trim 46 1/2-inches long to cover the upper part of the back wall, above the screen vent.
Roof: five 45-inch boards (because there is a stud running running down the middle of the hen house roof, these boards can be pieced together from scraps).
Nest box and cupboards: I used thirteen 14-inch long boards for the nest boxes, the divider between the cupboards and the nest box, and the closet bottom boards. The divider between the two nest boxes needs to be 3/4-inch shorter to make room for the nest back board. I started with a straight board, but the opening seemed too narrow to get at the eggs, so I made half-moon cuts in the nest back.
Screen frames: 5 8-foot 1 1/2-inch by 3/4 inch pine boards- choose good straight-grained boards, don't buy the "finger-jointed," pieced-together, wood molding, it won't hold up. I made diagonal cuts for the screen frame joints and bought metal brackets to beef up the corners. The dimensions for the screen frames are roughly the same as what I've shown above for the screen pieces, you want to do these last to make sure they will fit. You can see in the photos that I've done quite a bit of rough sanding and filing to get the corners to fit. Note that these one-by-two boards were also needed for some trim parts and fill strips and for the stick used to prop the hatch open. I had a few pieces of this material left over from a previous project that got used here, so it's a good idea to get an extra one of these. The scraps will be used for treads on the hen's ramp to their pen. Note also, the screen for the front door needs to be attached to the inside of the screen frame so there will be room for the two-by-four hatch cross members to fit inside the screen frame. Also note, I drilled an extra hole in each of the metal hatch hinges so I could get an extra screw into the two-by-four hatch rail. You need to allow room (about 7/8-inch) for the upper board of the screen door frame to fit between the hatch rail and the hen house framing. This makes it impossible to use all the pre-drilled holes, so I felt it was necessary to add another hole. It sounds tricky, but you will see why this is necessary to get the screen door and the hatch rails to nest inside the framing.
Ramp: As discussed later, the ramp that I have now is built from one of the side wall boards, with an extension. I don't like it that way, and I am going to revise that set up to use a single board for the ramp and make a sliding door for the hen's access door to the pen. The ramp is about 50-inches long, and I cut a dozen or so 6-inch wide treads, mostly made from scraps left over from the screen frames.
Water tank house: I pieced this together from scraps, and it doesn't cover as much of the tank as I would have liked. It's basically one long back piece with a bottom, two sides, and two roof pieces. Make this to fit whatever tank you buy.
Step 6: Feeders and Water System
I bought two 7-inch wide metal bunny feeders and cut holes in the front wall to mount them. I used some plumbers metal tape and found some "draw screw" bolts that had flat pieces to anchor the feeders. I also had to chisel out slots behind the feeders to make room for the lids to open. I think in the past I got away with putting the feeders high enough to open the tops without having to cut these notches. If you do that you may need to cut notches in the bottom edge of the hatch to clear the feeders. There may be other systems that would work better, but with a plastic flap to shed the rain, these bunny feeders seem like they will work.
The water system was more complicated. I wanted something that I could hook up to our drip irrigation system for refilling, but since the drip system doesn't run every day, I needed a tank for storage. There are a variety of waterers available that would work with this system; I settled on these little cup waterers that attach to 1/2-inch PVC pipe. I found them on line, five for $20, including the half-inch PVC parts the cups screw onto. That seems expensive, but I felt it was worth it. I also wanted the water tank to be in the shade, so that meant mounting the tank on the back of the hen house and routing the plumbing from the tank to the water cups, which I wanted to have at the front where I could keep an eye on them.
Note, the tank housing is mounted to quarter-inch thick wood strips between the hen house and the tank. This is to keep space between the tank box and the hen house so the wood won't rot. I used "tee" fittings on the tank (1-inch male pipe thread with two barbed hose fittings) to attach a top fill tube for the inlet from the drip system. The bottom hose goes to another "tee" fitting for a drain/lower fill fitting, and the one-inch pipe fitting attaches to the half-inch PVC pipe with a reducer to bring the water into the hen house. I could have run the inlet tube from the drip system through the tank vent hole, but that vent is really necessary for the system to work, so I used the "tee" fitting for the inlet tube instead. I ran the half-inch PVC water pipe through the cupboard section walls from the back of the hen house, and angled the pipe up to make the turn through the cupboard wall to get the water to the front of the hen house. Make sure to get this connection high enough above the bottom framing to clear the 1 1/2-inch tall floor screen panel. It also needs to fit below the feeders, so take your time and get this connection right. Note, you will need an extra set of hands when gluing some of these connections.
I extended the water pipe through the right outside wall to so it would act as a hold down for the front side of the floor screen. I used a "tee" connection on the half-inch PVC to raise the water pipe up to the desired elevation for the cup manifold. I built the manifold first and the glue job was pretty messy. Where the feed pipe extends through the right side wall, I added a sight tube so I could easily see how much water was in the tank. This is sort of overkill, but with our hot summers, water is a big concern. I would have used smaller tubing for the sight tube, but it was difficult to find the plastic fittings that I needed to connect the PVC piping to the hose fittings. The one-inch clear vinyl tubing was pretty pricey ($20 for 10 feet), and if I had it to do over again, I think I would have looked a bit harder to find the right fittings so I could use something smaller and easier to work with. I probably could have just skipped the sight tube entirely, as you can easily see the water level in the tank. Since I already have it in place, I plan to have this sight tube act as the overflow so the system gets flushed regularly when the tank is refilled from our drip irrigation system.
Step 7: Finishing Touches
I used one of the right side wall boards to act as both door and ramp (with an extension) for the hens to access their pen. The whole thing is attached to the hen house with a large hinge, and I added an elaborate pulley system that I planned to hook to a counter weight. The idea being to raise up their ramp at night to make it harder for raccoons to get at the hen house. The counter balance system turned out to be impractical, and I'm planning to replace this door and ramp with a simple sliding door mounted in aluminum channel tracks. I'll attach a new ramp to the bottom side of the hinge I'm currently using, so I will still have the option of raising that ramp if necessary. Eventually, I hope to add a solar powered door opener that will open the door when it's light out and close it when it gets dark. But that's a project for another day.
I used 3/8-inch diameter carriage bolts for the front screen pivot points and for holding the screen closed. I also used these to hold down the back of the floor screen (you can see these in the last photo). I put the pivot points for the screen door about six inches down from the top of the frame (you can see these in some of the other photos). The idea was that with this lower pivot position, I could just use the screen door to brace against the bottom hatch rail to keep both doors open, but that turned out to be pretty impractical, as the hatch is really heavy. Also, with the hinge pivot points being lower on the screen frame, the screen door bumps into the hatch boards when you try to push the door inward. I may re-drill those hinge pivot points higher up to make it easier to check their food and water.
Because the hatch rails had to be shorter than the width of the hatch to allow room for the hatch rails to fit inside the screen door frame, the prop stick gets in the way when it's braced between the hen house and the bottom rail. You can't open the screen door outward without the hatch falling down. To fix this problem I added an off-set metal tab on the under side of the front hatch to rest the door prop on so the heavy door won't fall down when you open the inner screen door. I had to cut a small notch in the front of the door opening for this metal tab to fit into when the hatch closes. I also added a hook on the underside of the hatch to hold the screen door up while fussing with the hens.
Step 8: A Note on Drawings
This is really "step one," but my drawings are so bad that I hid them back here. Drawing the design out is a good way to spot problems and solve them before you start cutting lumber. You will need some graph paper, an engineer's scale, a sharp pencil, and plenty of patience. Take your time and think about how each board meets and attaches to the adjacent boards. Make drawings of each wall and a floor plan. Pay particular attention to the measurements where boards overlap, and include this overlap in the final dimensions. I think the only effective way to do this type of project is with scaled drawings for each wall. There will almost always be minor design changes as you build, and when you make changes be sure to look at every part that will be affected by those changes. It's a lot easier to make changes on paper than to re-cut boards. Some of my drawings are pictured here, and you can see that I went through many iterations to try to figure out the best way to put things together. Much will depend on what materials you have available. If this was going to be made from plywood or some other material, the design would have been different. Even with all my planning, I still ran into plenty of problems during the build, there is always a solution, just be patient and think through the problem. If things don't work right, go back to the drawing board (see last step).
I had no idea this was going to turn out so long, thanks for reading, and I hope this instructable has been helpful.
Step 9: Back to the Drawing Board
My first attempt at the hen house door-ramp combination worked, sort of, but it was really impractical. Sometimes you just have to try things out to see if they work, and admit to yourself when they don’t. This one didn’t, so I went back to the drawing board. I built a new ramp, and used a piece of plywood to make a sliding door.
The tracks for the sliding door were made from an eight-foot piece of half-inch aluminum channel (about $8), and I had a piece of half-inch thick plywood that I sanded to fit in the channel. I tried to counter- sink the holes for attaching the track, to keep the door from dragging on the screws, but it was a pretty sloppy job with a hand drill. With sand paper and files I got the door to slide fairly well, but I'm not throwing my hat up in the air about it. This door will work for now, but I'm hoping to improve on it. In the meantime I needed to figure out a latch to keep the hens safe.
Years ago, we lost all but one of our hens to a raccoon attack; it was horrible. I have seen some awesome predator-proof sliding door designs on other instructables, but I only have basic hand tools, and putting these latching mechanisms together seemed beyond my ability. I needed something simple, and reliable that I could put together with basic tools.
Whenever I have to make something like a latch, I go through my bins of old parts and scraps to try and find something that I can use or modify to fit the need. In this case, I found an old gate latch that seemed like a good start. I drilled out the rivet that holds the latch mechanism, and played around with the parts to position the hook part so it could engage some sort of latch. I drilled a new hole at the end of the hook part, and relocated the mounting holes for the pivot point so the hook would extend beyond the base of the latch mechanism. The photos show the new holes in the latch parts and the completed latch assembly. I also drilled a hole for a new rivet to help hold the spring in place and act as a pulley-point for the latch release string. If you look closely at the pictures you may be able to see this. Now I just needed to figure out how to attach this latch to the sliding door.
The latch assembly slides into a notch in the plywood door, and the base of the latch is recessed in a chiseled out notch, so it sits flush with the back of the door. I wanted to add some extra weight to the door and also wanted to beef up the latch assembly, so I cut a notch in a piece of scrap two-by-six, and used that to beef up the door and provide backing for the latch assembly.
The latch also needs a return spring. I used a steel bristle from a street sweeper machine (I find these all the time walking around town). I bent the spring in a “U” between the latch mechanism and the new rivet I installed at the lower end of the latch. The spring keeps the hook extended past the inside face of the door (I may double up on this spring, as it seems a bit weak). This spring is also a bit tricky because you don't want the end of it wearing on the string that has to slide over the new rivet. With a bit of patience, I was able to pinch the spring in place when I reset the rivet that holds the hook in place.
When the hook is extended past the door, it engages a short piece of metal strap (just an old corner brace that I flattened out) mounted against the hen house wall. I cut a slot in the hen house wall for the hook to slide in so it can catch against the metal strap. I also did a little filing on the hook part to make it catch the hook a little easier.
A short piece of string connects the latch release arm to the door-raising string in such a way that when you pull on the door string, the short string that disengages the hook gets tight before the door starts to slide up. This mechanism worked well enough, but the plywood just didn't work as smooth as I wanted it to be. In the end I made a new door from quarter-inch thick plexiglass. It's got a good weight to it, is fairly easy to cut with a jig saw, and you can bond pieces together with acetone.
Step 10: Followup, Two Years Later
Arduino Microcontroller:
I finally got the hen house door to work with an Arduino Microcontroller. This is basically a VERY stripped down version of the excellent instructable for the "El Pollio Palace" posted by David Naves. I used all the same components that he listed, except for the ambient light sensor (https://www.amazon.com/gp/product/B01K563B22/ref=o...) that I substituted for the photo cell that Mr. Naves used. Otherwise, all credit goes to Dave Naves, who has my eternal gratitude; I never would have gotten this project off the ground without his generous assistance in posting a really excellent instructable. Thanks Dave! (https://www.instructables.com/id/Automatic-Chicken-Coop-Door-2/ )
I made minor modifications to his code, solely because I didn't know what I was doing and I made changes to try to fix something that in the end turned out to be something I had added. If I knew then what I know now, I wouldn't have had to make changes to his code (except for commenting out parts that this project doesn't include). For this reason, I wasn't going to post the mess that I made of Dave's excellent code, but since it might help someone, and with apologies to Dave and anyone else who I borrowed code from, I am posting the "Coop de Ville" code. It's a minor miracle that it works at all; I don't pretend to understand all of what it does, and I'm sure there are parts that don't do anything, so please don't ask. I would urge you to FIRST try Dave Naves original code. It is a work of art.
I only used the parts of Dave's code that open and close the door. Due to my own errors, I messed up Dave's code for the indicator lights, and ended up having to write a tiny bit of code for that. I am certain that there is nothing wrong with Dave's indicator light function, I just didn't know what I was doing, and at this point I'm afraid to ask.
It was wonderful the first time that the door opened the way it was supposed to, and I tested it many times before I was confident that it worked. The second day of operation, the upper door switch did not stop the motor from continuing to reel up string, and the motor made some gruesome snapping noises (probably jumping gear teeth) before I got it shut down. This intermittent problem was really mind boggling, and I ended up reading a lengthy thread about a similar problem that was discussed on the Arduino Forums. I did not have the heart to go back and change the wiring to pull-up resistors (instead of a pull-down resistors for the door switches), which would also have required rewriting the code (I think). Here's a link to the thread:[ http://forum.arduino.cc/index.php?topic=437162.0 ]
Since I couldn't bring myself to make those changes, I gave the matter some thought and realized that it was probably a really bad idea to have bundled all my wires together in the run from the door and motor setup to the controller box. I had the power cord for the motor nestled in with those door switch wires, and I suspect the juice to the motor was interfering with reading the status of the door switches. I rerouted the power cord, and it seemed to work perfectly. However, I would always wonder what if the thing glitched again.
I ended up mounting a cheap momentary switch that I found at the hardware store (see photo) in a block of wood, and mounting that above the door switch. If, for any reason a switch does not do its thing, the kill switch stops the motor, and the door lights blink to let me know the door is stuck. I am sure that this safety feature could have been written into the code, but not by me. I sort of like having the kill switch, for peace of mind, and I'm planning to put a little rubber cap over the button to waterproof that part.
Other Changes:
I never did get the door to slide correctly in the aluminum channel material I started with. The way I had mounted it, there were screw heads on the inside of the channel. I finally found some stuff called "file rail" that has an "h" cross section (http://www.orangealuminum.com/index.php/press-fit-.... It was actually pretty cheap, but it took me weeks to find the stuff. This provides a clean channel for the door to slide in, and a flange to put screws into.
As much as I liked the locking mechanism, the linkage was wonky and it kept causing jams. I ended up disabling the latching part, and just fixed the magnet that engages the lower door switch so it stays in the forward position. The door is pretty heavy, and if an animal tried to raise the door, the motor would turn on, which I think would spook most vermin.
My idea of having a screen floor didn't really work out the way I thought it would. I ended up covering the screen floor with a few pieces of cardboard and adding a couple of inches of shavings/litter. This worked much better, as it kept the hens warmer during the winter. I think I'll keep the cardboard/litter floor, as it seems healthier for the hens, and they already have plenty of ventilation. Also, they seem to spend a lot of time scratching and dust-bathing under the hen house (about the only dry place during our wet winter), and I didn't want all that poop accumulating where they bathe. It's pretty easy to just lift out the cardboard pieces with all the waste and litter, and just use new cardboard pieces to start fresh.
I also happened to have some door-screen left over from a different project, and I covered the front and back openings of the hen house with this screen to keep the mosquitoes from bothering the hens at night.
The water cups seemed to constantly get dirty, so I swapped them out and use little dribblers that fit in the same holes. The hens use them fine and their water is much cleaner.
July 2019 update: I had intermittent problems with the door motor not stopping when the door passed the reed switch. I suspect that there was a problem with the debounce function in the code that I had previously posted. I revised that part of the code and have uploaded the newer version, which seems to be working consistently. I also deleted the rather lengthy set of instructions for un-jamming the door, as these instructions are no longer necessary (I fervently hope they are no longer necessary). It's a good idea to find something you can use to cover the light sensor, so you can test the system.
Attachments
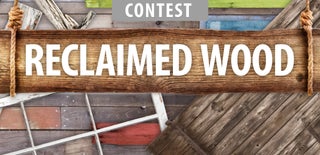
Participated in the
Reclaimed Wood Contest 2016