Introduction: Homemade Carbon Fiber Mountain Bike
It's been done a number of times before here on Instructables. Heck, it's one of the places I learned to do it. But this was my attempt to build a carbon fiber mountain bike.
I do have a Mechanical Engineering degree and have spent some time working with a small local custom frame builder who makes aluminum and steel frames.
Although it had been years since I owned a hardtail mountain bike, but I have to make sure I can build a basic bike before moving up to a much more complex full suspension frame. The not too common elevated chainstays on my frame came from wanting short chainstays, but not wanting to build a tight clearance chainstay yoke at the bottom bracket.
But before I build a frame, there are a few things to do.....
Step 1: Getting Your Ducks in a Row
What you'll need:
Materials:
- Carbon
- Epoxy
- Head tube and bottom bracket shell
- Fiberglass
- Electrical tape
- "optional" Aluminum bar stock for dropout inserts
- Insulation foam board
Tools:
- Frame Jig
- Basic hand tools (scissors, hacksaw, files, sandpaper, etc.)
- Hot Glue Gun
Other:
- Time, possibly lots of it.
- Patience, definitely lots of it.
You can get you carbon, epoxy, and fiberglass from anywhere you like. I found a company that is somewhat local to me and has great quality; Soller Composites
Carbon: I got woven fabric for nice looking top layers and uni-directional fabrics in a few widths and thicknesses for structural layers.
Fiberglass: This is used to wrap the aluminum parts to eliminate corrosion between the carbon and aluminum. *NOTE* A thin layer can also be wrapped as a final outer layer something like a 3.2oz 4HS fiberglass. When it is wetted out, it basically becomes invisible. A friend who makes custom kayak paddles uses this as a final layer on his carbon fiber paddles to protect from rocks and the river bottom. I didn't do it on this frame, but will on future ones.
Epoxy: I used a West Systems UV stable. I got it with the metering pumps to allow for easy measuring and mixing.
Head tube & Bottom Bracket: I used aluminum parts for these, allowing for machining and threading, and the durability for the install of multiple headsets, and bottom brackets. These parts can be acquired at many places like Paragon Machine Works You could also take an old yard sale frame and cut these parts out, just make sure that since standards have changed, your new components will work with the old frame parts.
Electrical tape: You will be using a lot of this, so don't go for the really good 3M stuff. I got mine in bulk from Harbor Freight: 10 pack of electrical tape
Insulation Foam Board: This will be the cores of the frame tubes. I used pink insulation board from Home Depot.
Frame Jig: I borrowed mine from a local frame builder I worked with, but you can easily (or very complexly) build your own. It could be a simple Wood Jig or a fancy metal one made from 80/20 extrusions.
Hot glue gun: This is how you stick the foam to itself and the other components before you wrap it in carbon.
Time and Patience: I have no hints and tips on these... or any of either to spare!
Step 2: Figuring Out Carbon
So how the heck do you do this??. Materials aren't cheap, but it is much cheaper to screw up a test piece than the actual frame.
I decided to use the foam insulation core and electrical tape compression method for my frame. Wet out the carbon fiber with epoxy, wrap the carbon around the foam core. Add the compression wrap, electrical tape, sticky side out. Once wrapped you use a pin or needle to prick holes in the tape to allow the excess epoxy to weep out.
To begin with I built a test tube. This allows me to try multi-layer layups and compression wrapping. I was also able to see how strong it was at different thicknesses.
I made a rough foam cylinder, and then laid up 2 layers of woven carbon on it.
With that being successful, I decided to do a BIG layup, and put 5 more layers on all at once. 4 unidirectional layers at +/-45 degrees and +/-60 degrees, then a top layer of woven.
The final piece once cured was TOUGH. I was happy to find I could stand on the tube (I weigh 230lbs) without any problem, or much deflection.
Time to start building.
Step 3: Building the Main Triangle
I set my frame jig up using the geometry from a bike that I like and rode well for me.
I started with the anchor points for the frame jig. On the jig I am using, those points are the headtube, bottom bracket and the top of the seat tube.
I scuffed the headtube and bottom bracket shells to promote adhesion. I wrapped the aluminum parts in fiberglass first to eliminate the galvanic corrosion between the aluminum and the carbon fiber that would happen if they were in direct contact. This corrosion would lead to the weakening of joints, and possible failure.
Now on to the "tubes". It's time to start playing with foam. You can make the tubes in any shape you want with the foam, but the simpler the shape the easier it will be to get good compression on the carbon plies with the electrical tape. I made tubes somewhere between octagons and circles, and they were ovalized at the ends to allow for more contact area at tube junctions. I added small pieces between the tubes at junctions for gussets. Make sure before you start laying carbon to check clearances for your drivetrain (including chain line at the extremes), wheel/tires and brake rotor.
Now it is time to wrap, wait, and wrap more. For my bike, I used 4-6 layers on the tubes and more at tube junctions (sometimes up to 15). Depending on the timing between layers, you can either lay the new right over the last layer or if it has sat for long enough to fully set, you can lightly sand the surface epoxy to promote adhesion.
As you continue with the layup on the front triangle, keep in mind how you are going to build the rear end. You want to make sure not to build up areas too much before being able to attach the rest of the frame.
Step 4: Dropouts and Stays
Congratulations on your completed front triangle! Now on to the back of the bike.
The biggest thing to keep in mind is clearance. I know I mentioned it before, but it bears repeating. You want to make sure to have space for your tires of choice, and maybe some mud on that tire. Also, drivetrain clearance, the new crop of wide range cassettes in 10, 11 and 12 speed systems lead to some odd chain angles, so take some time and test out your setup. I did a mock-up on mine with an older drivetrain that had different sized chainrings and ended up with interference on my chainstay. Brakes, brakes are good. you will need a place to put the brake caliper, and it will need to line up correctly with the rotor. That rotor will also need to clear the stays. So, please check everything out, then double check.
I made my dropout of an aluminum core, wrapped with fiberglass then carbon. I built these to suit a replaceable derailleur hanger from a '90's Cannondale that sandwiched it. There are many replaceable hangers in hundreds of different styles that you can use. The dropouts and the correct angle for the slot the wheel sits in became a problem for me and ended up being the failure point for my completed bike after over a year of riding it. All of my future bikes will use through axle dropouts to eliminate this problem.
I set the front triangle, with a fork on an aluminum beam to align the rear end. It could easily be wood, steel or whatever you have handy. I attached an old rear hub with a cassette to mount the dropouts on, it also allowed me to put a chain in place to check clearance on the chainstay.
From here, it is just shaping foam, and laying carbon fiber. When making up the chain and seat stays you have the ability to build them with some compliance, or super stiff, depending on how you wrap, direction of the carbon, and number of layers. This is a place where small experimentation and test pieces will allow you to figure out how you will build these.
Step 5: Brakes, They Are Good to Have.
I built up the seat stay to allow me to use an off the shelf brake adaptor to mount the rear brake caliper. You could also make your own from aluminum stock.
I wrapped the adaptor with a few layers of carbon, and presto! A working bike!
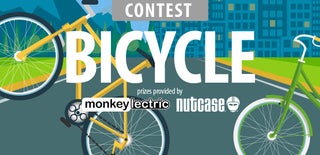
Second Prize in the
Bicycle Contest 2016
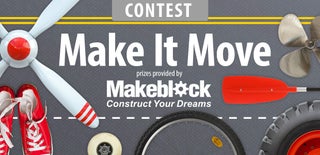
Participated in the
Make it Move Contest 2016