Introduction: Homemade or Makeshift Tools to Make a Leather Pendant
For my first Instructable I wanted to show how to make and use a couple of basic tools for leather working, in this case making a leather pendant.
I remember what it was like when I first started working with leather, and didn't have some of the tools that where needed or wanted.
Well here I am, making a couple of punches for stitching holes and a (not so swivel) knife.
I made two pendants in this project, one using tools bought specifically for leather working and the other with the homemade/makeshift tools.
I turned a two forks into punches and a butter knife into a (not swivel) knife. A nail file was used as a makeshift stylus and modeling spoon.
If you have access to a bench vice and an anvil (or something similar) the tool making process will be much easier. I have these, but worked as little with them to show that it can be done.
The tools I used where, a hammer, hacksaw, clamp, file, marking pen, sharpening stone and hard wooden blocks, plus a small anvil for comparison.
Step 1: Materials I Used
I had some off-cut leather I chose to use, this is about 4oz leather (about 2mm thick). Some leather dyes and paraffin based wax, this is used to give the project a shiny finish and to protect the leather.
Step 2: Starting the Punches
First start with flattening out the tinges of the forks, a pair of pliers may be useful for this to make little adjustments, or to do it completely.
Step 3: Making the Punches
Next I drew across the tinges to shorten them by about half.
Once clamped down I hacksawed the tinges to length on both the forks, then chose one to be a 2 prong punch and marked it out for cutting.
I found it easiest to cut from the base of the tinges towards the fork handle.
The four prong punch was marked out to were I wanted the width to be brought down to, so that each of the tinges are approximately even.
Step 4: Filing the Punches to Shape
The two prong punch is filed on the sides to smooth off the rough sides and burs, the four prong is filed down to width.
The points are filed to shape by using the file at an angle, the insides of the points are achieved by using and switching the facing and side edges along each tinge (so that the corner of the file is between tinges).
Step 5: The (not Swivel) Knife
I marked out just past halfway of the knife blade (looking for a comfortable length and weight for balance), and cut it off with the hacksaw. Because knife blades are usually hardened, it will take a little longer to cut through than the forks.
Once cut off, I filed off the original cutting edge to smooth it off.
The end that was cut off will be our new cutting edge, because a swivel knife is used almost vertically.
A file can be used to develop the cutting edge, but a sharpening stone is much easier.
The finer and sharper you can make this edge the better. So if you happen to have a honing stone go for it. I chose not to use it, because I know not everyone has one, and I was attempting to use fewest tools possible.
Step 6: Stencils and Tracing Tools
Ideally Tracing Film is the choice for transferring patterns onto leather, but I have made do with the image on paper. The standard practice is to trace the image onto the tracing film, then trace onto the leather.
Now is the time that the tools at hand are makeshift, here I am using a nail file in place of a stylus and modeling spoon. The stylus is used for tracing patterns onto the leather, and the modeling spoon for "tooling" the leather.
Step 7: Casing the Leather and Transfering the Pattern
"Casing the leather" is the term for dampening the leather so that transferring the pattern is easier, and the tooling marks can be made sufficiently deep enough.
Using a damp sponge, evenly case the leather (do not saturate the leather). Allow the moisture to soak in and the colour of the leather to "return to normal".
Position the pattern the way that you want it, then trace your outlines. Whilst keeping the pattern in position, lift it to check you have traced all the lines necessary.
I repeated this process with tracing film and bought tools.
Step 8: "Carving" the Leather
So the (Not so Swivel) Knife is now about to be put to use. Holding the knife so that the edge faces the leather, tilt it back slightly so that the trailing point is used. Draw the knife around the pattern that you traced. Once all the lines have been cut, it's time to go back to the nail file.
I started with the outer ring of the pattern, then the inside edges of the patterns by "smoothing" the point (tilted) across the leather. I then proceeded to "tool" the rest of the pattern by smoothing and pressing the leather.
Again I repeated these steps with bought tools.
Step 9:
Here I have used a 20 cent piece (Australian) to add an out diameter to the pattern on the Tracing Film (yes i should have thought of this at the beginning). And then transfered it to both leather pieces. This line as well as a vertical tab is where I am cutting away the excess leather (but we try not to be wasteful when cutting out the leather).
the last picture in this series shows the two pendants with the respectively used tools beside them.
Step 10: Burnishing the Edges
The edges of cut leather can be a little rough, so to give them a nice smooth look and feel (as well as a bit shiny), we burnish them. Ideally Gum Tragacanth is used to moisten the leather and to help build friction, but water can be used to achieve a similar result, which is what I did here for the pendant that is being made using homemade/makeshift tools.
I have two burnishing tools, the horizontal one pictured is the first one I owned. I made it from a piece of wooden chair (it came from the back support), I trimmed it to length, filed the tip and sanded it smooth.
Once the edges have been dampened (with water or gum trag.) I rub the edges with the burnishing tool, using the grooves or tip of the tool to smooth out the edges. Don't be afraid to move the tool quickly or to use a little bit of pressure (just not too heavy handedly), the idea is to build up friction to essentially polish the edges.
Step 11: Punching Holes for Stitching
Sometimes I will dye the leather before punching holes for stitching sometimes after, this is one of the later cases.
Unfortunately the prongs of the homemade punches are too wide to use on this project, so i used only the one outer prong of the four prong punch to put two holes in for stitching. The bought tool was a comfortable size to do it in one go.
Step 12: Stitching
There are a few different ways to stitch up leather projects, Because there is only two holes there isn't a lot of choices how to do this. With this I used one leather needle (you could make do with a medium sized darning needle) it has a large eye (for thick thread) and doesn't have a sharp point.
With this project I ran the thread most of the way of the first hole, through the next, around the outside. The return stitches went through the opposites sides of the holes and around the other side and then tied off with the initial tail of the thread. the excess thread was trimmed off close to the knot.
Step 13: The Final Step "Polishing/Sealing"
I finished this project by sealing the leather with "Dubbin" (a paraffin based wax) on the makeshift version. Using a rag cloth I rubbed a little dubbin into the leather.
The bought tools version, I used a product from Eco Flow called Super Sheen.
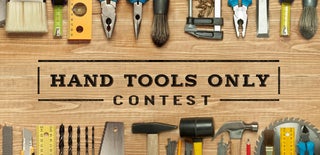
Participated in the
Hand Tools Only Contest 2017
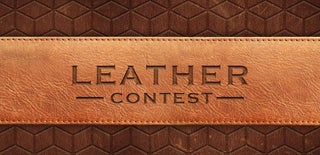
Participated in the
Leather Contest 2017