Introduction: How I Turned Fabric Sample Books Into Chair Upholstery
Ten years ago, we bought these chairs for our dining room. While I absolutely dig their design (they look super elegant and minimalistic) and their build quality is also top-notch ( they're made of rubberwood), the upholstery on them hasn't aged well. The fabric feels to the touch like velour and absorbs any liquid it comes in contact with. Thus, it stains very easily and even water drops leave nasty rings on it when dry.
While wandering around in Brussels, I found two abandoned fabric sample books. They regroup a variety of furniture fabrics out of which some are even water and stain resistant!
This was the perfect opportunity for me to finally take out my parent's cheap sewing machine and learn how to use it.
Supplies
Sewing machine
Stapler gun
Fabric sample books
Matching thread
Step 1: Watch the Video
As always, I did a video on the project to show you all the important steps and resume two weeks of my life in under 4 minutes:
Step 2: Dissasembling the Books and the Chairs
The books were held together with some hot glue and the beefiest staples I've ever seen. Luckily, they came out fairly easily with the help of a flat screwdriver and a bit of elbow grease.
Once the staples were gone, the individual fabric sheets were also easy to remove, as the fabric fibres had already weakened the glue.
That left me with a pile of fabric samples I then sorted according to their colour - different chairs will be made of samples that revolve around the same colour palette.
For the chairs, it was just a matter of removing four screws under the seats.
Step 3: The Problem With the Thin Fabrics..
The samples had all a water-resistant paper glued to the back with the technical details on the pattern and the material. The backsides won't be seen, so aesthetically there's no problem for most of the samples. However, some of the fabrics were very thin - because so, there were sharp changes in texture and smoothness on the fabrics when they were bent.
I tried to remove the backings using an air gun to soften the adhesive. That job turned out to be very time consuming, so decided to throw the thin pieces away and use only the thicker fabrics.
Step 4: Sewing - the Technique
Now that all the pieces are prepared, it's time to set up the sewing machine.
As the fabrics we'll be sewing are quite thick, we need to use the right needle size (I learned that the hard way). A size 100 needle in the European system and 16 in the American system did the job but you can go thicker if you want.
For the sewing process, I started with a simple seam connecting two samples together (with their 'pretty' sides facing in and a seam allowance of about half an inch).
Then, I trimmed one of the fabric flaps on the backside to about a quarter of an inch.
After that, I folded the other fabric flap over the first one to get a flat surface.
Finally, I made a second seam parallel to the first one that connected the longer flap on the back to the main surface.
It's difficult to describe the process with words, so please consult the picture series to get a better understanding of the technique I used.
Step 5: Sewing Larger
Once the individual pieces are connected into large bands, these bands can be connected using the same method as before - however, you have to be more careful in order to not break the thread (I suggest you to use the handwheel to have total control over the speed and where the needle lands).
In the beginning, I also drew lines to guide me before sewing using a ruler and a fabric pencil.
If you have trouble keeping the two layers of fabric where you want during sewing, you can use positioning pins.
Step 6: Upholstering
After a week of work to finish the six fabric pieces, it's finally time to put everything together.
A staple gun does a quick job of attaching the new upholstery to the seats and it's pretty inexpensive too. I've heard that some people have reupholstered their chairs with box nails, so if you're on a budget, you can try that too.
To begin the upholstering, place your seat on the fabric and ensure that there's enough material to cover all of the sides (I decided to attach the fabric under an angle to make it visually more interesting).
Then, staple all the edges in place (make sure there's no loose fabric but do not overtighten it either.)
After that, move towards the corners while keeping the fabric under constant tension and adding staples whenever you feel like it (in the video, you can see that I did the mistake of jumping right to the corners after attaching the edges - it's not catastrophic, as it's easy to tension the loose parts later, but it's better to do it correctly right away).
For the corners, you have to make three folds - first, one under an angle of 45° and two in the direction of the edges of the chair.
As some of the fabric I used was quite thick, my staple gun didn't always manage to connect the fabric to the wood. To resolve that issue, I cut some indentations in the parts that weren't under stress to make the pile of fabric thinner.
Finally, remove all of the excess using a pair of well-sharpened scissors.
Step 7: Done!
Last step: connect the new seat back to the frame with some screws - if you can, use new screws that are a tad thicker than the original ones to ensure a snug fit.
And with that, the project is finally done!
It took me a bit less than two weeks to finish all the chairs. This is my first sewing project and I'm very happy with how it turned out! I'm happy that I decided to attach the fabric under an angle - it makes the chairs more interesting and ties them all together with a common design element.
In addition to having chairs that are unique on the entire planter, I also now have the basic skills to use a sewing machine! :)
Thank so much you for reading this far! I hope you liked this project. If you have any thought or suggestions, please leave them in the comments below.
Have a good day! :D
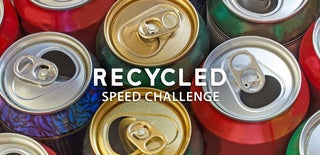
Participated in the
Recycled Speed Challenge