Introduction: Illuminated Waterways of the United States Map
I just started playing around with laser cutters and was looking for a project. I wanted to do a map-related laser cutter project, but wasn't exactly sure what. I saw the Earth Art Australia Etsy shop while browsing random things online. After seeing some of the maps there, I got the idea to etch the the rivers of the USA map.
Eventually the idea evolved into filling the etched area with blue epoxy resin. Then I realized it would be cool to cut all the way through and fill the cuts with epoxy resin. The idea of backlighting came after I made some smaller test pieces and saw how much of a difference it made to have light behind the blue epoxy resin.
Epoxy resin is a really fun material to work with. You just mix two parts together and pour it! I've had a lot of fun experimenting with mixing different colors, thickeners, and all sorts of other random things in with it.
Step 1: Materials & Tools
Between Amazon and Home Depot, I was able to find everything I needed for this project. I used the laser cutter at a local makerspace.
Materials
- 1/4 inch plywood
- Two part clear epoxy resin
- Blue pigment or dye
- Melamine board
- Vaseline
- Assorted sandpaper
- 1/4 inch thick hobby wood planks
- Wood Stain
- Wood Glue
- LED strip lighting + 12V power supply
- Switch to control LEDs
- Mounting hardware
- 3/8 inch diameter rubber feet
Tools
- Laser Cutter (Can be found in local maker spaces, community colleges, and some city libraries)
- Hand Saw (Miter saw would have been better, but you gotta use what you got!)
- Random orbital sander (optional)
- Soldering iron (optional)
- Brush / rag
- Hot glue gun
- Drill
- File
Step 2: Create Laser Cutter Files
This part probably took 8 hours in total. I ended up starting over multiple times while figuring out the best process for going from flat image to a vector cut path that worked best with the laser cutter. The goal is to get the cut areas into a vector file and the etch areas into a regular raster image.
Once I worked out the scale of how big I wanted to make the map, I realized that the smaller rivers would only be fractions of a millimeter wide. I decided to cut the main rivers and just etch the smaller ones. Luckily the larger rivers were a slightly different color than the small ones on the original image. This made things much easier to get the main rivers selected for vectorization (adjustment filters and select by color in Photoshop).
I used Illustrator to remove any overlapping objects in the vector file and found some Illustrator scripts that could automate removing small objects.
Lots of planning went into making sure that the cut regions wouldn't cause sections to break off. I broke the cut out regions into a grid of smaller pieces so that it would be easier to pop them out of the plywood once they were cut by the laser.
Step 3: Testing Laser Parameters
This was my first real laser cutter project, so I ended up spending a lot of time testing out different cut and etch parameters to see what would work best. Keeping a project notebook is usually a good idea, but it was a necessity here.
Experiment with cutting and etching the kind of patterns that will be on the final map. This is the time to find any major errors in the cutting parameters and design files.
I did a test cut of the big map which revealed the issue of pieces being completely cut out.
Step 4: Epoxy Resin Testing
The epoxy resin comes in two parts (A and B) that begin hardening about 30 to 40 minutes after being mixed together. Getting a consistent color with the pigment mixed into part B before combining the two parts made it much easier to get a consistent color throughout the mix.
Epoxy resin loves bonding to things, so you need to get something that it won't stick to. I used a plastic cutting board as the base to do the initial test pours on. It worked okay, but was a bit tough to get things off.
I tried again using melamine board with a coat of vaseline, which worked much better. Melamine board is used for storage shelving and can be found at most big hardware stores.
Seeing the test coasters finally cut and filled got me really excited for the final map.
Step 5: Final Cut and Etch
Materials
- 1/4 inch plywood
Tools
- Laser cutter
I was able to get minimal burn marks when laser cutting from the back side of my work piece. I realized I could etch the front, then flip the piece over and perform a mirrored cut. This required more planning and testing of the process since everything would need to be lined up perfectly between the etch and the cut.
The total time for etching and cutting ended was around two hours.
Step 6: Epoxy Resin Pour
Mixing the color and seeing the map come together was probably the most fun and exciting part of the entire project for me. We'll be pouring the resin with the map sitting on some vaseline covered melamine board so we can easily release the map from our working area.
Materials
- Two-part epoxy resin
- Blue pigment
- Melamine board
- Vaseline
Tools
- Mixing cup
- Stirring stick (plastic fork in my case)
- Something to spread the epoxy resin around (I used a cheap plastic cutting board that I cut in half)
- Lighter or heat gun to pop bubbles
Steps
- Apply a generous coat a vaseline to the melamine board and put the map down on it. The vaseline will help the resin release from the board and will help hold the flexible sections of the map in place during the pour.
- Mix up about 16 ounces (~500mL) of epoxy resin with some blue pigment. It should look very dark when mixing.
- Pour some resin on. Don't pour it all in one shot, as it takes time for the resin to work its way into all of the rivers.
- Use something flat to spread it out and push the resin into all of the nooks and crannies.
- Use your heat source to pop any bubbles that start forming.
I ended up doing two pours of the epoxy resin. The first pour leaked through the bottom of the map and left some of the rivers only half full.
Step 7: Sanding
I wasn't very clean with wiping up excess epoxy resin around the edges of the map, so I decided to sand the excess down. If I were to do the project over again, I would put masking tape over the entire piece of plywood, then use the laser cutter to cut the outline of the map out so that I could peel it away after applying the epoxy resin. Lessons learned.
Tools
- Sand paper (120 grit worked well for me)
- Random orbital sander (optional, but will cut down the time by a lot)
- Respirator
- You should always wear a respirator when sanding, but it is especially important when working with epoxy resin. You don't want to be breathing this stuff.
Steps
- Use the orbital sander to remove excess resin from the big areas
- Work by hand to get the smaller areas that the orbital sander can't reach.
Step 8: Build the Frame
I wanted a dark frame for the map so that there would be a some contrast between the frame, map, and wall that it is hung on. I've built similar frames around cheap canvases before and it always turns out very nice.
Materials
- 1/4 inch Pine hobby wood
- Wood stain
Tools
- Saw & cutting box
- Brush
- Rag
- Wood glue
- Thin rope (or clamps if you can make it work)
Steps
- Measure twice and cut once! (or buy extra wood and inevitably need it like I always do)
- Apply the stain according to the instructions. Mine said to let it sit for a few minutes, then wipe excess off.
- Put some scrap pieces of the 1/4 inch pine under the map when attaching the frame so that the map will sit slightly recessed in the frame.
- Apply wood glue to attach the frame pieces to the map. I used some rope to hold everything in where the frame pieces were warping a bit out.
Step 9: Epoxy Clear Coat
I didn't like the look of the map area being glossy and the surrounding plywood looking matte, so I went over everything with a clear coat of epoxy resin.
Materials:
- Two part epoxy Resin
Tools:
- Brush
- Hot glue gun
Steps:
- Make sure that your frame is completely sealed around the back edges. I went around with the hot glue gun just in case there were spots where the wood glue didn't fill it.
- Mix and pour one to two cups of epoxy resin on the top of the map
- Use the brush to even everything out and get the resin up and into the edges.
Step 10: LED Strip Lighting
Time for the exciting part: light!
Materials
- LED Strip Lighting
- 12v power supply (One came with the strip light kit I bought)
- White Cardstock
Tools
- Hot glue gun
- Scissors
Steps
- Begin attaching the LED strip lighting from the place where you will like your switch and power input to be. (My strip lighting had adhesive backing which worked ok)
- Use hot glue to attach any places that aren't holding up very well
- Be sure that you leave some space somewhere on the frame for the switch and power attachment (next step)
Once everything is attached, plug it in and see how it looks. I had some light bleeding though sections of the plywood, so I hot glued white cardstock around areas of the map that shouldn't have light showing through.
Step 11: Power and Switch
A simple switch wired in series with the LEDs is all we need to control the light. My LED strip lighting came with a power jack and power supply. I got the switch and wire at Microcenter.
Materials
- Switch
- 12V DC Power adapter break-out
- Wire
Tools
- Drill
- File
- Soldering Iron (optional, you could just twist and electrical tape the wires together if you don't have one)
Steps
- Measure out and mark where you want the switch and power adapter. Make sure that you'll have space and aren't interfering with any LED strip lighting.
- Drill out the main area of each hole you'd like to create
- Go to town with the file to shape it out until everything fits
- Solder the switch to the +12v supply and the positive side of the strip lighting, then connect the other end of the led lighting to the ground connection of the power supply.
Step 12: Final Touches
I wanted to have some of the light from the LEDs bleed out around the frame. If you want, you could add a backing so that no light bleeds out, but I liked the look of having it.
Materials
- Rubber feet
- Mounting hardware
Tools
- Hammer
Once everything is ready, hang it up and turn it on!
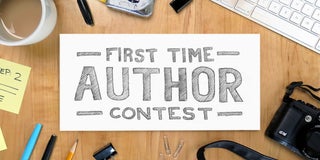
First Prize in the
First Time Author Contest
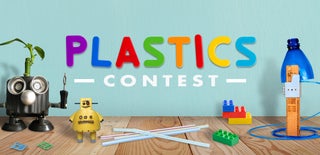
First Prize in the
Plastics Contest