Introduction: Rescueing a Rotho Laundry Basket
Yes, I'm sure that there exist laundry baskets equipped as standard with predetermined breaking points. My laundry basket was heavily used for more than five years when it started to show symptoms of fatigue. I wasn't amused with that. Even if a new laundry basket wouldn't have been that expensive, I refused to trash it but thought about fixing it instead, because a laundry basket is a lot of material to send to the landfill.
Supplies
- Hardwood rod, e.g. beechwood, approx. 16 mm dia. (max. length shown in step 2)
- Box knife
- 15 mm dia. manual hole punch
- Sander (or sand paper, or rasp/file, or whittling knife)
- (Cordless) drill
- Hot-melt glue gun
Step 1: The Problem
My laundry basket was manufactured by Rotho. This seems to be a company based in Switzerland that sell their plastic products worldwide. In the picture above you can see the weakest point close to the handle, seen from below. It even shows some discolouration due to mechanical strain. I suspect that these weak points are introduced deliberately by the manufacturer in order to have the basket fail early and to sell a next one once the first fails (planned obsolescence is the keyword here, right?).
Sorry, Rotho, you've got to count me out on that!
Step 2: But How to Fix It?
As you can see in the 1st detail picture above, some additional, bright gray plastic pieces are inserted at the handles on all four sides that suggest strength but in fact are weak points. At the longer edges, at the locations where the blue plastic was almost broken, these pieces are already removed - easily done because they are only snapped in place.
So, how to reinforce the (almost) broken handle? I thought about inserting a cylindrical, wooden rod somewhat longer than the original handle. In my junk box I had some beech rod with a diameter of 16 mm. Make sure that it is not longer than indicated in the 2nd picture; if it is longer it will become very difficult to be inserted.
How to get it in place, anyway?
In the 3rd picture above (a view from below the basket's rim) you see a small rectangular hole already provided. These need to be increased in order to slide the wooden rod inside. I had bought my faithful 15 mm dia. sheet metal punch (4th picture) many years ago, mainly for making holes for the now almost obsolete DIN sockets. It requires an 8 mm dia. pilot hole - but drilling this hole was impossible because the rectangular hole was rather off-center compared to the one I wanted. So I used a box cutter to coarsely enlarge the rectangular holes until the 8 mm thread of my punch could be inserted. It then in fact punched nice, round holes. The new problem was that this hole, unfortunately, was 1 mm too small for my wooden rod...
Step 3: Making It Fit
But once the right idea came, it was peanuts! I remembered that most plastic stuff gets soft or melts when it becomes hot, regardless whether that heat comes from an open flame, a hot air gun, strong solar irradiation, or, e.g., friction. I sharpened one of the ends of my wooden rod (you can use a rasp, a file, a whittling knife, sand paper or an electrical sander), shown in the 1st picture above. It doesn't have to be pretty but just functional instead. The other end will then be inserted into a cordless power drill to make it rotate fast. But stop - the chuck of my drill only accepts drills up to 10 mm dia.! So what to do? Of course, a disc-type sander (or a file, etc.) may also be used to (roughly) reduce the diameter of a wooden rod on a length of, say, 2 cm, as shown in the 2nd picture above. This as well needs to be only functional rather than beautiful. And once it can be clamped in your drill chuck, you can easily make it rotate.
I inserted the pointed end of the wooden rod from below into the hole that I had punched before and powered up the drill for a little while. It didn't take long befor the 15 mm hole was, by melting plastic due to friction, enlarged to the diameter of the wooden rod. I did this from the other side, too. After removing the rod from the drill I could slide it through both holes (3rd picture, view from below). Since this is a rather tight fit it needn't be fixed otherwise.
Step 4: Further Reinforcement
The gap between the wood and the plastic on the upper side of the handles can be filled with the hot-melt glue gun for some additional strenght, but I'm not sure whether this really is necessary.
And my fixed laundry basket will now hopefully escort me to the laundry room for several more years :-)
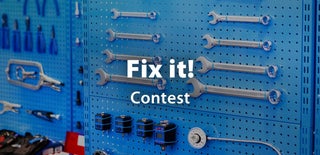
Participated in the
Fix It Contest