Introduction: Kissing the Frog V2.0 - Back Horn Bluetooth Speaker Fully Printable
Introduction
Let me start with a little background. So what is a back loaded horn speaker? Think of it as a reversed megaphone or gramophone. A megaphone (basically a front horn loudspeaker) uses an acoustic horn to increase the overall efficiency of the driving element (i.e. the sound coming out at the front). A back loaded horn speaker does pretty much the same thing. However, here the horn is mounted to the back of the speaker. So you get the direct output from the front of the driver PLUS the one from the horn at the back. Which frequencies are amplified and how well depends on the air chamber, throat (the narrow part), and on the length, design, and diameter of the horn. Particularly with small (and cheap) drivers this can very much improve the sound quality.
I would call this concept "Kissing the frog". You take that little tweeter and hope it turns into a prince. And yes, it actually does. It is amazing how much sound you can get out of a $10 3.3" driver.
You will find loads of books, papers, and online references for how to design an optimal horn speaker. The problem is that your calculated optimal horn will likely end up taking up most of your living room. However, I found these tools incredibly helpful to better understand the dynamics (i.e. what happens when I change the diameter, length, design of the horn?). Ultimately, the design of a (back) horn speaker (definitely a 3D printed one) will largely be guided by the available space while trying to get as much sound out of a relatively small enclosure / driver.
For this design you will need to have access to a 3D printer. I am using a $ 200 Creality Ender 3 3D printer, which can do prints up to 220x220x250 mm (and does a great job at that). The body is designed to fit a standard 200x200 mm build plate, so most (even budget) printers should be capable of printing this. If you want to use it as a Bluetooth speaker you will need basic electronic and soldering skills. Make sure that you know what you are doing (particularly dealing with high voltage! So take care, all at your own risk and no warranty whatsoever). However, remember, you can always use the enclosure as a passive speaker, which omits all the soldering.
Step 1: Electronic Supplies
Basically this is a super cheap project. All electronic supplies you need for the Bluetooth version should cost around $20.
- First of all you will need an MP3 Bluetooth Decoder Board (approx. $ 1) (the same on Amazon). You could in theory use an amplifier with integrated BT board. The problem is that this way you will inevitably end up with a stereo speaker signal - good if you want to connect 2 speakers (the 2nd speaker being connected to the first by wire), bad if you want a single (mono) speaker as you cannot pool output signals from both amplifier channels. The separate BT board allows for pooling the line out signal before feeding it into the amplifier.
- The amplifier is a TPA3116 D2 Dual Channel 50Wx2 Amplifier Module (approx. $ 3.5) (the same on Amazon)- this one is stereo (which seems like a waste, however, stereo amplifiers are nowadays easier to find than mono and considering the cost of 3.5 $... and may come handy in case you want to connect 2 speakers). For mono you will need to bridge L and R channels coming from the BT board (see the wiring section).
- Pretty much any 12V/1A+ (the more the better) power supply (approx. $ 1.7) (the same once again on Amazon) will do. E.g. an old 12V laptop power adapter would be great. I use a small 10x15 mm rocker switch as power switch (which is optional as the amplifier has a switch built into the volume control - which, however only switches the amplifier).
- A small LM1117 Step Down converter (approx. $ 0.2) (the same on Amazon). This will convert the 12V from the power adapter to 5V needed for the BT board.
- The driver I use is a Visaton FRS 8 M - 8 Ohm 8 cm (3.3") full-range speaker (around $ 10). The exact same driver may be difficult to find in the US but here a few options on Amazon.
However, basically any combination will do (as long as the driver is 3.3" or smaller so it fits the enclosure - if you use a different driver you may have to slightly adapt the mounting holes). I have made an adapter for 2.5" drivers but would really recommend to use a bigger 3 or 3.3" driver.
Step 2: 3D Printing
The enclosure itself is 100% printable. All .stls are attached. All you need is a few M3 screws to mount the driver, the back plate, and feet plus some glue to attach the side panels. For the side panels you have two options. Either printing or cutting them from 6-8 mm (ply)wood. I have included a 1:2 plan (.pdf) for cutting the side panels (and of course .stls for printing). Basically they are simple 20 x 15 cm boards with 10 mm fillets on 3 corners and a 3 mm fillet on the 4th.
Printing itself should be pretty straightforward. You will notice that the body has a 1 mm cover on one side. This is to give it more stability and make it easier to print and remove from the printer. No support or attachments needed.
Slice in your favorite slicing software (I use Cura). Print in PLA (or ABS, PETG... what ever your favorite material is) at 0.28 mm resolution and (around) 15% infill. You will glue the side panels to the body (after mounting the driver and electronics) and the front and speaker will be attached with M3 screws and the back panel that covers the electronic compartment as well. The feet (I print these in TPU) are optional.
Start by printing
- the body (1 piece). The body is a single print, in itself needs no screws or gluing, has a 1 mm cover over much of the lower side (which very much adds to stability), at 15% infill uses up about 350 g of filament, and takes around 20 hours to print. Speaker_Body_V2.stl
- followed by the side panels (if you are not cutting them from wood - print 1 piece each, right and left, respectively). Speaker_Side_002_PartA.stl AND Speaker_Side_002_PartB.stl OR Speaker_Side_Pannels_Drawing.pdf
- the small back cover for the electronics chamber (1 piece), which has openings for the volume control, the rocker switch, and the 12 V power cable. Speaker_Back_V2.stl
- the front speaker ring (1 piece), Speaker_Front_V2.stl
- optional: the feet (4 pieces), ideally printed in TPU, but PLA will also be fine. Speaker_Feet.stl
- optional: volume knob (1 piece), which simply slides over the volume control of the amplifier - Speaker_Knob_V2.stl
Attachments
Step 3: Wiring
If you re going for the Bluetooth option you will need basic electronic and soldering skills. However, there is always the option of using them as passive speakers (i.e. you simply connect the driver with the output from an external amplifier).
Make sure to wire and test all your electronic components before mounting them in the enclosure (except for the 12V power cable and rocker switch, which goe through a hole in the back cover), this makes troubleshooting so much easier.
This is for the list of supplies above and may be different if you use different components. Connect the output from the 12V power adapter (this one goes through the small hole in the back panel!) to the POWER IN (marked VCC and GND) on the amplifier board PLUS to the little LM1117 board (VIN and GND) - The 5V output (VOUT and GND) from the LM1117 board is connected to the power in on the BT board.If (like I do) you use this as a single MONO speaker, bridge the L and R output coming from the BT board (this is important, it will give you a mono signal, instead of half stereo!). Now you connect the bridged L/R and GND from the BT board to line in (IN-L OR IN-R and GND) of the amplifier (if you are using a stereo amplifier, connect to either the left OR right channel). Finally connect the output from the amplifier (L+ and L- OR R+ and R-) to the + and - on the speaker.
The rocker switch is optional (for the 12V power). However, there is an opening in the back cover, so it is easy to mount (but needs to be inserted into the back cover before soldering).
Try all this before mounting everything in the enclosure (this really helps with troubleshooting).
Step 4: Assembling
You should now have all printed parts and the wired (and tested) electronic components ready for assemblage. Only the rocker switch and power cable need to be in place before soldering.
- Mount the speaker ring to the outside and the driver to the inside of the enclosure with four M3 screws (12 mm) and nuts. Insert the cable in the little channel on the back side of the speaker chamber.
- Mount the amplifier to the back cover (which has a hole for the volume control) - the nut of the volume control will hold it in place.
- Mount the Bluetooth board inside the electronics chamber (use a little glue to make sure it stays in place)
- Mount the back cover with two M3 screws.
- Glue the two side panels to the main body. You may want to sand the contact areas with course sand paper before gluing.
- Attach the feet with a drop of glue and/or short M3 screws.
- Slide the volume knob over the potentiometer shaft of the amplifier.
Step 5: Enjoy!
Turn it on, connect your phone to the Bluetooth receiver, enjoy the music...
HOPE YOU LIKE IT, AND IF YOU LIKE IT, PLEASE LIKE IT!
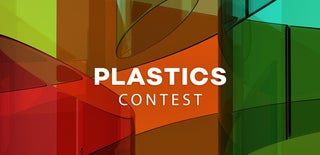
Participated in the
Plastic Contest