Introduction: Labware Chandelier
Hello Fellow Makers,
Today I will share with you how I made a chandelier from reclaimed laboratory glassware.
Step 1: Scavenge
There's shop here in Basel called offcut that sells surplus material from local shops/factories/museums. This place is full of surprises. I try to come here once a week just to see what kind of quirky objects show up. I found these glassware here after they received a donation from the local pharmaceutical museum. (I am actually very curious about what these were originally used for, if anyone knows please comment below.) I thought it had a very sculptural look to it and if combined in an interesting way they could make for an abstract collage-like assembly. They also happened to have a huge (2m x 4m) sheet of 4mm plexiglass for 5CHF!
Cost
The final assemblage costs about 30CHF.
~10CHF for the glassware
~15CHF for the LED light bulb
~5CHF worth of plexiglass
Step 2: "Scanning"
I wanted to scan the glassware in order to bring them into digital space and play around with the composition. I tried doing this with Structure Sensor for iPad and it failed to register the glass surface. I have read about photometric but I didn't want to risk spray painting the glassware since they are one of a kind and cannot be replaced. If anyone knows of any scanning technique that will work with glass please comment below.
In the end I had to 3d model them manually with a caliper and a bit of patience. It is a simplified version of the original but enough to work with for the next step.
Step 3: Composition
This step is highly subjective, I've tried many configurations and decided on one that I thought looked the best. There's not much science to this step. The idea is to start with one 'branch' at a random angle and revolve it around a vertical central axis. The symmetry of the overall composition is similar to a classical chandelier, and the individual branches resonates with the candle holders.
Step 4: Designing the Frame
Once the composition is set, it is time to figure out how to hold them together. The intention is to do it with the least amount of pieces possible while avoiding glue and fasteners. I chose to use plexiglass to make the frames. Their transparency worked well with the glassware and can be fabricated with precision on the laser cutter. Slots and hooks were introduced on the frames to work with the particular geometry of the glass pieces.
There's a constant back and forth between the drawing and the cutting (Step 5). I went through about ten rounds of trial and error before arriving at the final set of frames. The diagram above shows the process of evolution, many minor adjustments had to be made to get the frames and glass pieces to fit together perfectly.
Step 5: Lasercut
As I mentioned in the previous step this was a process of rapid prototyping. Many failed attempts were made to get the connections and overall composition to look right. Starting with getting the slots in the top ring and bottom ring to fit the geometry of the glass pieces.
In terms of the overall composition, it stayed relatively similar to what I had designed in digital space. The only parameter I played around with was the diameters of the two frames, which varied the angle of the branches and overall size of the assembly. I also tried different ways to integrate the second type of glassware. I realized during the process that having four branches was too crowded and made the overall assembly look static. You will notice that the final design had 3 branches instead of 4. Things like this was much easier to judge in real life.
In the end these are the final four frames used to hold the whole assemblage in place.
Step 6: Hang
I used fishing wires to hang the whole assembly into the metal part of the junction box. Notice in the previous steps I had little holes cut into the plexiglass frames, those were prepared for threading through the fishing wires. In terms of height, I like to hang chandeliers as low as possible. In my case the lowest part of the assembly is just a few centimeters above my head if I'm standing underneath it. If you happened to hang it above a table then I would recommend going lower.
Once the hanging was done, I purchased a simple white light socket and few different light bulbs to try out. If you're unfamiliar on how to hardwire a lighting fixture, you can refer to this tutorial.
In the end I went with the transparent LED light bulb that is a perfect sphere (125mm diameter). I think the simple geometry does not compete with the rest of the glassware. And the visible filaments resonated well with the glass tubing.
Step 7: Footnotes
I know this is one-of-a-kind object and you will not be able to duplicate the exact same thing, but the idea is to use found objects and re-contextualizing it in a way that changes our perception of its utility, its lifespan, or its status.
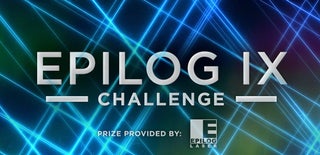
Participated in the
Epilog Challenge 9
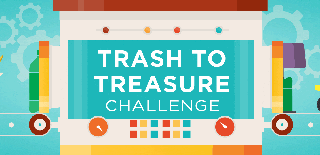
Participated in the
Trash to Treasure