Introduction: Laser Engraved Cigar Boxes With Wood Inlay
This week we're pulling all the stops and making this mesmerizing laser engraved cigar box or humidor.
We simply engrave the top of our cigar case and inlay our LaserPaper Wood, as well as some synthetic mother-of-pearl.
We also use the Mutoh 426UF UV printer to print our cigar rings out of our LaserPaper Synthetic material, along with registration marks. We then put it in our Trotec laser cutter, where our camera system reads the reg marks and cuts accordingly.
We also have a bonus round, read the final step to see what it is!
Step 1: Engrave the Box
We first place our cigar box that we purchased at Michael's (or any arts/craft store), into our Speedy 400 100w laser engraving machine and engrave the RGB Black fill in the artwork file attached.
We go slower than normal because we need the engraving deep for the inlay.
Engrave setting: 100 power, 80 speed
Step 2: Laser Cutting Wood Paper
We then place our wood paper into the laser machine and cut based on the RGB red and blue cut lines in the artwork file. There are 2 colours for 2 different wood papers - maple veneer and cherry veneer.
Cut setting: 35 power, 2 speed
Step 3: Laser Cutting Synthetic Mother-of-pearl
We then put in our synthetic mother-of-pearl into the laser and cut our patterns based on the RGB turquoise colour in the artwork file (you can mix and match the design and colours of your choosing).
Cut setting: 35 power, 2 speed
Step 4: Putting the Inlay Together
We then take off our cover on the 3M adhesive backing for the paper wood and synthetic mother-of-pearl and place them in the engrave spot accordingly.
Step 5: Putting on Shellac
We then put on Bulls Eye Shellac Traditional Finish and Sealer to enhance the natural beauty of the wood, and let it dry for a few hours.
Step 6: Sanding & Sealing
We sanded down any air bubbles and then sealed it with our Varathane Triple Thick One Coat Clear Finish, and let it dry for a few hours.
Step 7: We're Done Our Inlay!
...check out next steps for what's inside the box!
Step 8: Photo-engraving the Inside Lid
We then open our box and place it in the laser machine where we engrave the lid with a photograph for each of the four boxes including: John F. Kennedy, Winston Churchill, Sigmund Freud and Arnold Schwarzenegger who are all famous cigar smokers.
Please see artwork file in step 1.
Engrave settings: 100 power, 100 speed
Step 9: Printing the Cigar Rings
We then make our own cigar rings by placing our LaserPaper Synthetic white paper into our Mutoh ValueJet 426UF UV printer. The synthetic paper has a glossy finish and is almost impossible to rip apart, it has that professional cigar ring finish.
We set the UV printer to CMYK (no white since it's already on a white surface) and print "colour-on-white".
Artwork files attached.
Step 10: Laser Cutting the Paper
We then place our synthetic paper into our laser machine.
The camera system then reads the reg marks and knows exactly where to cut around the rings.
Based on the RGB red hairline outline in artwork file.
The reg marks have to be 0.25" in diameter with a RGB black fill and hairline outline.
Step 11: Putting the Ring on the Cigar
We use our double-sided engraver's tape on one side of the cigar ring and then simply place and glue it together around the cigar.
In this demo they are No.1 cigar sizes.
Step 12: Creating Our Paper Insert
We then take our LaserPaper Colour (Dark Blue) laserable paper and put it in our laser machine. We engrave our logo and kiss-cut the fold-lines.
We then fold the paper insert it in our box and put in the cigars.
Step 13: ***BONUS ROUND*** - Engraving the Cigar
For the bonus round we engraved our logo directly on the cigar!
Engrave settings: 30 power, 100 speed
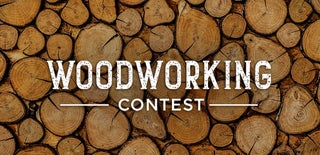
Participated in the
Woodworking Contest