Introduction: Layered Topographic Coasters
Lasercutting is a fantastic way to create versatile, personalized gifts while still having plenty of flexibility to prototype and revise along the way. But what do you do when all of your friends are tired of intricate papercraft, engraved wood, and model x-wing fighters?
Easy. You trick them into making it look like something else. Outlined below is a great gift for any of your outdoors-oriented friends that's sure to get front and center on their coffee tables, or at the very least make them say "wow, you should really get a CNC."
Supplies
What you'll need for the layered portion:
- Posterboard (size varies) — I ended up settling with metallic gold, as it made for a visually interesting surface and offered nice reflective contrast between the lasercut edges (brown). I went through a 24" x 36" sheet while testing these, but the final layout that I made fits a full coaster on a 12" x 12".
- Superglue
- Sewing pins
- Project cork (12x12", 1/16" thickness)
- Contact Cement
What you'll need for the cast portion:
- Clear casting resin (approx 12 oz).The exact type/brand doesn't particularly matter; mine was a polyester-based one.
- Mold — ideally any roundish plastic container will do; I used leftover mixing cups from a different casting project, but tupperware, yogurt cups, or even a custom 3D printed mold will all work. You'll want this as smooth as possible to minimize your work later.
- Gloves
- Mixing cup/mixing stick
- Scale
- Optional: sandpaper (various grits), buffing wheel
Note that I lasercut these, but you could easily do these on a Cricut/similar, or, if you're feeling very brave, hand-cut. Let's get started!
Step 1: Creating the File (Map to STL)
Originally I'd planned on obtaining topographic data from an online repository such as this one and manually tracing over the area I wanted in CAD. Luckily there's a much easier way to procedurally generate topographic maps, beginning with the terrain map for a given area.
The first step is to isolate the desired area. There's a really nifty online software called Terrain2STL that generates STL files of a given rectangular area in Google Maps. For this project, I decided to make a map based off of a particular area in Death Valley where my friends and I had camped—this coaster set was a gift to one of the people in that group, and I planned on using pins to mark our campsites throughout the valley.
To select your desired area, move around the map as you normally would and center around the area you'd like. You can adjust the size and rotation in the "Model Settings" window. You can also adjust the vertical scaling (this will affect what "resolution" the resulting coasters will be at, or how much elevation change each layer represents) and can add a base, although we'll be doing those at a later step.
This project actually ends up going through a lot of scope changes: I'd initially planned on doing the entirety of Death Valley, but there's so much definition (particularly because it's multiple valleys) that the resulting topography would've been too cluttered to fit on a single coaster. That, and even though I restricted myself to an area of a couple square miles, my coasters still ended up being ~200 pieces total. Don't be afraid to experiment! I initially prototyped in cheaper cardstock before using my posterboard.
Once you've finished selecting your area in Terrain2STL, hit the "Generate Model" button.
Step 2: Creating the Map (Modifying the STL)
Terrain2STL will output a high-quality rectangular STL file. However, we'll want to scale it down, trim it into a round shape for optimal coaster-ness, and, depending on your computer specs, lower the resolution so that the slicing software in the next step doesn't have a conniption.
I used NetFabb, which is a great STL editor for this application because it has a built-in circular split function, and it won't try to edit the entire mesh, which would be difficult with a file of this size. However, any slicer will do the trick.
To scale in Netfabb, right click the part and select the scale option. You don't need to be very precise here; we're just scaling it to fit into the workspace here and we'll be doing more size adjustments at a later step.
To trim to a round shape, select the cut icon from the top toolbar and navigate to polygon cut. Center and adjust the size of your trim area, select the "Cut" button, and then export the rounded part as an STL. Note that if you're running on a slower computer, you should choose to decrease the export quality to help out with the next step.
Step 3: Creating the Map (Slicing the STL)
The final step in the file creation is done via the Autodesk Fusion360 Slicer plugin, which will convert our STL file into a flat PDF that we can then cut out. Effectively, this auto-generates topography lines for us. Adjustments in the software allow us to set the height between each contour line that the layers on our topographic coasters will represent.
In this step, we'll scale the file so that it's the right height and diameter. After importing into 360 slicer, select the "Stacked Slices" option. Depending on how your planar presets are set up, the default slice orientation may create slices perpendicular to your ground plane rather than parallel to it. If that's the case, you should rotate the slice direction 90 degrees using the "Slice Direction" feature.
This is also the time that we'll want to scale the model down to our coaster size. I used 3.25" as my diameter to match the size of my mold. Leave the uniform scale option selected and change your height/length (this may be width/length if you didn't need to rotate your model) to the desired diameter.
It will be quite likely that the resulting model will only have 2 or 3 slices, and will not be very well defined. That's okay! You can either adjust your material thickness in the Manufacturing Settings, or you can uncheck the uniform scale model and only scale your "width" (which in this case means height). Decreasing material thickness or increasing unscaled "width" will result in more contour lines, but be careful—this also means more pieces!
You should also keep your real material thickness in mind. (Material thickness) x (Number of Layers) = (Total Coaster Height), and if you have too many layers your coasters will be too tall. The posterboard I used was approximately 0.017" thick, but you don't have to match it directly in the Slicer. For example, I wanted more layers so I could show more contours, so I used a slightly smaller material thickness.
Once you've found a balance that you're okay with, export this file to a PDF and start cutting!
Note on Thickness: I found a strange bug where the files would fail to generate if the "width" (again, this refers to the height of the coaster) is an even multiple of the material thickness. For example, using a width of 0.5" and a material thickness of 0.1" would result in an error. This can easily be avoided by adjusting the width to 0.501" or similar.
Note on Dowels: Slicer does have a built-in dowel function that helps with alignment for larger projects; however, for the scale that we're working with, most dowel holes will be noticeable and therefore unideal.
Step 4: Cutting the Map
Now that we have the flat pattern, we can begin cutting! Depending on what tools you have on hand, your steps here might be different, and most lasercutters are also going to have different procedures, so we'll speed through this section.
With the PDF flat pattern, we can adjust these files to make them more easily digestible for our cutting implement of choice. The output from Slicer is meant for wooden projects and as such has artifacts such as engrave lines (red) and numbers. For posterboard, this isn't particularly necessary and you may burn through your material, so I would remove these. Additionally, I removed any piece smaller than 1/8" x 1/8", as they wouldn't lasercut very well and they would add extra height that I didn't want.
For the first cuts, I used cheaper cardstock so I could get a feel for how tall things would be and estimate how long assembly would take. I then adjusted the design in Slicer a few times to lower the definition. My final file was 51 parts for one coaster and fits on a 12 x 12" bed (for my K40), but your mileage may vary.
Once I roughed out the design in cardstock, it was time to switch to my shiny posterboard! A note for lasercutting non-metal objects that have a metallic finish: cut these shiny-side down. This is good practice so that the char is on the bottom of your part, and also lets your laser focus properly instead of reflecting.
Attachments
Step 5: Assembling the Coasters
Now that you've got all the pieces, it's time to bring it all together. I found that it was useful to have the Slicer file on-hand in case I wasn't sure where a specific piece was supposed to go.
I initially played with alternating black and gold cardstock, but settled with the pure gold instead. This is the last time that you can really mess with the design before things are set in stone (resin), so swap colors, adjust your Slicer file, and so forth here!
As far as assembly, I found that stacking all of the pieces up in their correct positions without gluing anything together, and then flipping the entire assembly upside-down and pulling each piece to glue one-by-one from the bottom piece up was the easiest approach that led to the fewest missed pieces. Because we'll be casting these, you don't need too much glue between each layer; I used superglue because of the relatively short cure time (which will add up as your part count increases). Be sure to press down well as you're gluing to remove as much air as possible, as these air pockets will come out as bubbles in the casting process.
Step 6: Casting the Coasters, and Some Bloopers
Unfortunately I don't have many in-progress pictures of the casting process because wearing gloves, gloopy materials, and cameras don't mix, but luckily this step is relatively straightforward compared to previous ones.
Clear casting resin is easily obtainable from art supply stores. The exact material and surface quality will depend on your budget, and each coaster ends up being around 3 fluid ounces, so feel free to plan accordingly (accounting for a few outtakes).
Always wear proper equipment when handling uncured epoxies. Polyester mixes like what I have here aren't particularly harmful, but if you happen to be casting with a clear urethane, you will want to be in a well-ventilated area and wearing gloves and a face mask. Read the back of your specific label to see what protective equipment you'll be needing.
Most casting resins come in a two-part form: a base and a hardener. Depending on your specific type of resin, the exact ratio between the two parts will vary, so measure according to the back of your packaging. Outside of the mixing ratio, there are two key numbers when casting: your pot life (how long you have until the resin becomes too viscous to pour or work) and your cure time (how long the resin takes to fully harden). Best practice is to not touch the cast between after the pot life is passed and before the cure time is reached. Make sure you've gathered all of your materials in an easily accessible place prior to mixing.
The mold I selected has flexible walls, which makes demolding easy. However, if you're using a rigid-walled material, be sure to spray it with mold release so that your part will come out of your mold later. Also, depending on your resin, your posterboard glue-up may be less dense than your resin. In this case, you will want to glue the poasterboard assembly to the bottom of the mold, as resin will likely fill under the bottom of your posterboard assembly and cause it to float. This will result in a coaster that is not level. I used hot glue here, but I found that the resultant heat from the resin curing loosened the hot glue significantly; in a future revision I would recommend superglue or tape.
I also put the pin (X marks the spot) in at this step, although it's optional/purely aesthetic.
Once you've measured, mix your resin in a disposable container. You will not get this container back. Mix the two parts together thoroughly and pour the resulting mixture into your mold. Bubbles will start to emerge from where they are trapped between your layers of posterboard; use a needle or a pin to pop these as they emerge to keep your coasters clear.
SOME BLOOPERS
Mistakes happen! Here's a few things that I did that you might want to avoid:
I read online that you can make molds out of packaging tape to form the walls/bottom. This may work for different parts, but for a round part where the edges weren't well-defined, the resulting cast part was very lumpy. I would recommend using a rigid container if you have the chance. Again, any tupperware, yogurt container, etc will work just fine here! Don't worry if the bottom isn't what you want; we'll be covering that up.
I've seen a few techniques where a torch is used to heat the resin to force the air bubbles to rise to the top, resulting in more clear parts. Check the flashpoint of your resin before trying this; I lit mine on fire and ruined the part. I found that a sewing needle is much more effective at removing bubbles and significantly reduces the risk of fire.
Secure your part to the bottom of the mold. If the part rises up a little bit during casting and makes things crooked, it's not the end of the world—you can actually cast another layer of resin once the first layer has cured to even things out, but it's better to avoid this if possible.
Step 7: Post-Processing
Once the resin is fully-cured, you have an important decision to make: good enough?
Depending on your mold's smoothness and shape, you might be good to go. If however you want crisp, optical clarity, you've already made it this far.
I also took this opportunity to sand a fillet onto the edge of the coasters. This made the edges magnify the interior, and overall made an effect I was really pleased with. You can speed up that portion by using a chamfer bit and a drill press/router, or freehanding on a belt sander.
Do not post-process until your part is fully cured. Otherwise, your part will still be soft.
I cleaned up my surfaces using sandpaper of increasing grit (a lower grit number means more coarse; higher grit is softer). Take off large areas using a belt sander or low grit sand paper, and then smooth out with progressively higher grit until the surface is buttery smooth or your hands are gone. It's tempting to want to skip up to higher more quickly, but you'll want to keep sanding with a given grit until the entire surface is uniform, and then repeat with the next highest grit. I started wet sanding at around 2000 grit; this helps give a more clear finish. Finally, a shop rag or paper towel with a dab of toothpaste provides a very high grit abrasive for the penultimate pass.
For the last pass, I ran the coaster under a buffing wheel, although if one isn't available to you, the sanding trick should get you pretty close.
Finally, I cut out some cork circles for the base to give it grip—I also engraved them with names/dates as part of the gift, so they aren't shown here, but cork lasercuts fantastically. A quick application of contact cement ensured that they stayed on snugly.
Step 8: Closing Thoughts
If you've made it this far, congratulations! Time to repeat steps 4-7 over again, hopefully with some more knowledge under your belt.
I definitely tweaked this process a lot as I went through it, and I've tried to note specific troubleshooting tips that I came up with throughout my prototyping process. Some things you'll want to keep in mind:
- Minimizing the number of pieces will really help with your sanity as you start trying to make multiple sets. The number I settled on was around 50 pieces per coaster, which was fine for resolution and was just enough for me to keep track of all the pieces.
- Keeping the map area (the size of the map you're trying to make topography for) helps a lot with the above. It's okay not to get the entire area in one go, and most people aren't actually going to recognize the topography of a given area without prompting anyway.
- The reflective posterboard really lends a lot of depth to the final result. I initially tried with matte cardstock but preferred the metallic elements more.
- This is a custom project, hopefully one you're okay sinking several hours into. Don't be afraid to mess around and mess up; your materials are relatively low-cost and mistakes are easy to fix! Poke around, have fun, map your own course, etc etc.
Thanks for reading!
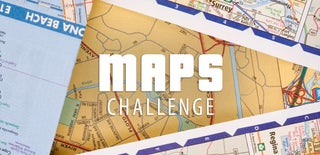
Runner Up in the
Maps Challenge