Introduction: Leather Hatchet/Ax Sheath
Leather work has intimidated me ever since I was a boy scout. The multiple steps, special tools, and attention to detail has always thrown me off. Now I'm older, wiser and able to focus on one thing for more than 5 minutes which makes leather work a lot more fun. The tools you need you can order with a few clicks online now (I didn't have amazon, or the internet, 30 years ago). I hope to show you that this hobby can be fun and even relaxing! I will say this now: "I am not a professional, I don't do this all of the time, and I certainly don't get paid to do it. My way is not the end all solution to many of these steps. I encourage you to search Instructables for other full lessons on each step! And as always, I certainly appreciate any feedback that will help me and future readers to make this easier to understand!" Also, please read or at least skim all the steps before you start gluing and stitching everything together. I made a really dumb and avoidable mistake in the order of operations. Just make sure you stitch the belt buckle (if you want one) before you assemble the rest. Lets get too it!
Step 1: Acquire Materials and Tools
Materials:
If you going to make something out of leather, you'll need to get some of you don't already have it. Most of my projects are pretty small so I usually get belly cuts of Veg-Tan leather because they are cheaper. I included a diagram of how the cut hide and what the cuts names are. You can also get also get different weights. I try and stick in the 6-9 oz range for projects like this. If you're a smart shopper you can find different cuts, weights and scraps on sale and not spend a lot on it.
Paper or cardboard to cut a pattern. Nothing fancy but thick enough to hold up with tracing it onto the leather. I used a extra little promotional poster I had sitting around.
Tape to hold said pattern while you're working.
A snap set if you want a metal snap to hold it closed
Tools: From left to right on the picture
You by no means need to run out and buy all of the stuff in this picture! There are many tools that do the same job 2 different ways. If you have a Tandy Leather or other local leather supply store and tell them what you're making they will usually be happy to come up with a decent set of tools that can get the job done. And if you are you are current or former military, fire or police, you get a significant discount at Tandy!
Stitching Grover - gives you a uniform grove along the line that you will stitch
Overstitch Spacing Kit - wheel that evenly spaces your stitches
Saddle Stitch Needles - for saddle stitching
Lacing Fid or Awl - Pokes the whole you need to sew the leather
Stitching Awl - it's your sewing tool "one option"
4 Prong Point Stitch Chisel - gives uniform wholes in which to stitch through
Super Skiver - thins the joining spot of leather "Easier to understand in action than by name"
Bees Wax - a good edge sealer
Honing Resin - helps with sharpening tools
Edge Beveler - Bevels the edge of the leather "#4 pictured"
scrap chunk of leather to sharpen you edgers, cut pound and practice on as you work
X-acto Knife - cuts stuff, have extra blade on hand, they can dull quickly cutting leather
Wood Slicker Burnishing tool - gives you that finished slick edge
Mallet - Wacks tools. not metal, preferably a "leather working" mallet
Hole Punch - Not Shown in picture
Button set - Also not shown
Up Top:
Leather glue, dye, and finish - your choice, I could write a book on just picking these three things and how to use them. Most popular glue is probably contact cement, leather die, whatever color you want, and I use an acrylic protective finish but there's lots of options.
Other picture: A Stitch Pony - if you are going to hand stitch a lot of leather this thing is a huge help!
Step 2: Design and Cutting the Pattern
Like anything you find on a "how too", there are many different ways to do it. I'll show you mine and if you come up with a better way, fantastic!
There's no real standard size of shape for an ax or hatchet head so I recommend making your pattern to fit what you got. I'm going to use the term ax in this Instructable because it's only 2 letters :) I'm going to also try to use all of the proper terminology, I added a diagram picture in case anyone needs it.
So I cleaned up my work space so I had lots of room to move and work and taped down the paper I was going to use as my pattern. I laid the ax down on one cheek and traced the entire head. I then rolled the ax onto its butt and traced it and then rolled the head onto its other cheek to complete the pattern. A learning note: If you follow the last step and do not give and additional space you will end up with an exact copy of you ax head, which your ax will not go into when it becomes a sheath. When you roll the ax onto the butt, slide it out a 1/4 to half inch, then when you lay it on it's other cheek, slide it another 1/4 inch.The addition I tell you in the upcoming step is not there for the same reason I'm telling you this.
You can then remove the ax from the paper and use and eraser and straight edge to clean things up a bit. Once you are happy with the shape, you'll want to add 1/2 to 3/4 inch of space from the toe to the heal and along the beard of the head. Don't erase your original lines of the bit, just add an additional line to the pattern as pictured. You'll need to draw in the flap that will buckle the sheath closed. I suggest you make this part of the pattern much larger than you think you might need it and then cut it down after it laying on the head.
OK, cut it out. Be slow and take your time, it'll pay out in the long run. Once cut, lay it on the ax head and make any minor adjustments you might have. Lay your flap over and cut it to fit a button placement. Also cut out a 2" x 4" rectangle if you want a belt loop on it.
Step 3: Cutting the Leather
If you use belly leather like I do, there tends to be some ugly spots on it that you might not want as the center-piece of your project. Move your pattern around until you find a good spot. I like to tape my pattern down with this weird vinyl tape I found somewhere in my garage. It doesn't leave any marks on the paper or the leather. I'll try and add that in later. Tape in lots of places. Take a piece off trace that spot, tape it back, working slowly around the piece.
Once you've traced the entire piece and removed the pattern, cut the toe to heal and beard pattern out of the pattern. It should look like a funky curved V type thing (see picture). This is going to add 2 extra layers to the bit and beard side of the sheath. Trace that small pattern 2 times (not 4 like you see me do in the pics) and trace out your belt loop.
Cut out the leather. A dull knife is the most dangerous tool in leather working. At any acute angle in your pattern, punch a whole before you start cutting. This will keep you from running past the angle with your knife! With a sharp knife, at a 90 degree angle to the leather cut your pattern. I use a "No Cry Cut Resistant" glove on my non dominate hand in order to keep all my fingers during this part. GO SLOW and cut on the line. don't worry if you don't cut all the way through the first time! take your time and retrace your cuts. Don't force
Step 4: Adding the Bevel and Color
The beveler takes the corner edges off the leather making it easier to burnish later. If you want a nice finished project look, investing in in one of these is a good investment.
So here's the part that can get confusing. We are eventually going to add those 2 weird V pieces to the pit part of the sheath with some glue and stitching so DON'T bevel these pieces. We're going to make a 4 Layer leather sandwich so don't bevel the non finished edge of the main pattern either. Once it get all set in place it'll make a little more sense but first we dye everything. Skip to the next step if this part is confusing you. Once you see it constructed it makes a bit more sense. Click on step 4 for a little more information before you start you beveling.
Staining. It was recommended to me that we stain here and buy enough that you can soak the leather in the stain for a little while (See Pictures) that way you don't get it stitched and find out you can't get your stain dauber all the way down in the nooks and crannies. I think I left mine in a few hours and laid it out on a flat surface to dry. I of course let it dry too long so I had to "re-hydrate it" in order to make it workable again. I then added the finish to it and let it dry again. And again, re-hydrated it and away we go. Pro Tip: Where gloves from the time you open the stain until you put the lid back on or you will some how always get stain on your hands!
Step 5: Adding the Belt Loop, Burnishing, and Construction
If you're smart, you'll add the belt loop here... I forgot, so you'll see me doing this much further down the line, If I was really smart I would have burnished all of the single layer locations, but I didn't, I skipped straight into construction. Go to step 7 for the belt loop and I highly advise you watch a quick video on gluing, stitching and burnishing. None of it's hard concepts to learn but we'll be here all day if I just keep typing. Pro-Tip: Stitching is not a substitute for gluing, you need both!
To Make It Easier On You... Stitch your belt look on there and burnish all the spots that aren't going to be glued before you proceed! You may have to skip a few steps forward to step 7 to see it but it's easier to do it here. Don't be a Chris!
OK so here's where the beveling becomes so important. Looking back on how I did it, I would probably glue the 2 funky V pieces together first and then glue them between the two cheeks, as shown in the picture. If you look at the first sheath I made, I did a process called wet molding and I ended up with clamp marks all over it. So this time you'll see my ruler and protractor in between the leather and clamps to avoid that. now you have all 4 layers glued together. The outside finished layer of each cheek should be beveled and none of the leather in the middle should have been beveled.
Once the glue drys, grab your favorite sanding method and smooth out the edges. if you sand it too much you may have to go back to the beveler and rub a layer of stain over some little spots. Make sure the ax goes in and out of what you currently have or it'll be kinda pointless to continue. If it doesn't, you may have to make some design adjustments :(
Step 6: Stitching and Another Round of Burnishing
Get out your stitch groover and your scrap piece of leather and practice using it once or twice to make sure it spaced and is working the way you expect it too, then take it too the project. You only need to stitch 2 lines. 1 from toe to heal and 1 along the beard. this should be the shape of the weird V you added earlier:) once you have your groove, take your overstich spacing wheel and role it through the grooves to give you a nice easy stitch spacing.
Once you're grooved and have your stitch pattern you're ready to get the stitch pony out and start poking holes. Poke your anvil through each spot that your stitch till go as straight as possible. Then watch a video on stitching and get to it. Stitching through 4 layers of leather can be hard, but is very possible. Take your time and if you notice yourself getting sloppy, put it down for a bit and come back to it later. It's important that it looks good!
Once you have those two edges glued sanded and stitched you can burnish this edge
Step 7: Adding the Belt Loop (a Little Late)
This should be done before the construction step but I missed it so I'm putting it here hopefully you have skipped to this step to do it in the right order. Your little rectangle is probably dry and stiff and you'll want to hydrate it to be able to manipulate it. You can put it on flat or in a Question Mark Shape or cut a belt tool into the sheath. I like the question mark shape the best, you do you :)
If you are going for the ? shape, you will want to grab your skiver and skiver the first 1/2 inch of the top of 1 end and then FLIP IT OVER skiver the bottom half inch of the other end. so one end skived on the top, one on the bottom. this will give it a cleaner more professional look. Yours skiver may not look like the one I have in the picture, but it's a good example of what the leather should look like.
Find your balance. If you put the belt loop too far forward, it'll hang funny, just the same as too far back. Try and find the middle and start the top of your belt loop there. Remember TO PUT THE BELT LOOP ON THE BACK OF THE SHEATH AND NOT THE FRONT! You'll need to glue the top piece on, then groove and overstich the pattern then sew it after the glue is good and dry. Then you'll do the same to the base of the loop, Adjusting it up or down to fit your needs.
Step 8: Molding and Buttoning the Flap
It's important to line up the snap and stud and allow yourself space so that you don't have to force it closed. I like to poke the hole centered on the flap where I'll want it to be. Fold the flap over like it will when it's closed and then slide the flap up, just a few millimeters so that it's not super tight when it snaps but snug. unless you have a bunch of buttons sitting around, you'll probably buy a snap set that comes with it's own little set and anvil tool.
It's probably best you find something on YouTube to see how to set the snap. It's not all that hard but I always find a way to mess mine up. see picture example and go learn from a pro... Believe me, I want what's best for you!
Step 9: Inspect and Rejoice
Give everything a look over, Find little imperfections and take note on how to learn form them. Burnish little spots that might not got their love the first go around. Be proud of your accomplishment! Go out in the woods with you ax strapped to your hip and conquer the forest.
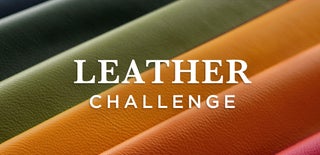
Runner Up in the
Leather Challenge