Introduction: Leather Shield and Decoration
Once upon a time in my life :
One evening, at home, I found myself thinking: “I’m bored, LARP (live action role-playing game) events are not very often, and I would like to keep my mind and hands busy while remembering past games and preparing future costumes.”
And so I started working on leather, and as I was starting from scratch, I practiced, discovered, and .. used what I had under my hand (or could find easily without too much investment)
And so after a long work on a hon kozane do (when you want to do something, do it hard, so you’ll learn … or stop on the way… and for the non japanese-speaking people here, that’s the most complex form of Japanese scale armor), I tried other things.
And finished by creating my own easy way to decorate leather elements.
Please note : if I started with a crazy project, imagine I continued with… crazy projects or strange methods…
I’m quite proud of my leather shield, and I’ll use it as a reference here, but I will show other examples of my “technique”.
It is not a perfect technique, it is not ideal, it is not even “classic” (yes, I know what embossing is and yes, I practiced that too and I can prove it, but it’s not what I want to explain, thank you for the question).
Supplies
You need:
To make a leather shield:
- a piece of leather (please see part 1, it’s really important),
- wooden boards (seriously, the ones you find, if you want to go cheap, or make some research to be historically correct (hints: linden, pine, …). I used pine planks from a wood pallet),
- wood glue,
- contact glue (neoprene),
- a hacksaw,
- decorative nails (tapestry nails),
- solid nails,
- a hammer (for those who don’t put nails with their bare hands),
- sand paper,
- varnish,
- a knife (and here, I mean, a real sharp one, maybe even a scalpel),
- a pencil,
- ruler,
- compass (to draw a circle, you know ...).
For leather decoration:
- your leather,
- dyes of dark color (I prefer alcohol based dyes than water based dyes personally),
- acrylic paint (for leather preferably), white or any other color that would contrast with the dye,
- thin brush, size 0,
- water,
- sponge,
- clean fabric,
- sample drawing,
- A ball pen,
- and … well… something long enough to be held like a ball pen, with a round tip like a ball pen, that you can use to make drawings like a ball pen. But not a ball pen. I mean, it has to be solid and strong, and NOT LEAVE INK or marks. I used a 15 cm long sail needle, reverse (I used the socket side, not the needle side)
Step 1: Choosing Material
part 1 : choosing leather
One can’t make nice products with poor resources.
Leather being a noble material, and as you want to work with it properly, you must buy proper leather.
So here is a short lesson on leather.
Leather comes from animal skin. Mostly cow, but it can also be goat, lamb, pig, ostrich, or even crocodile (or other crazy origins… fish, banana, mushroom, …). I won’t speak of the last 2, seriously, I never used them. Lamb, pig and goat leather are very similar : super flexible, very thin. They are nice to use, but for decorating and making solid stuff, it’s not ideal
So cow we use (or buffalo if you are on a Japanese trip …).
There are several methods to transform a cow hide into cow leather. I’ll spare you the details, but the most critical part is : tanning.
For that, 2 schools, 2 results : chrome tanning, or vegetal tanning.
Chrome tanning uses … chrome (1 point if you guessed). It makes flexible leather, water resistant, strong, and CHEAP. Cool, no ? No. Because embossing, shaping or decorating leather implies using water. Plus, it’s bad for health to wear chrome leather with sweat and so on.
Vegetable tanning uses … oak ! (yes, it’s a vegetal, I checked). Oak releases tannins when boiled, and those tannins transform the hide into leather. Flexible, not water resistant but more expensive. Too bad.
So You need VEGETABLE TANNED LEATHER.
ONLY.
NOTHING ELSE.
At the time I was buying them, they were at around 100$ for a little more than 1m².
Seriously, it hurts, but you can’t imagine the sensual pleasures of working with leather (sensual… related to senses…. Eyes, touch, smell, earing … no, I didn’t try tasting it, but thanks for asking).
I always used non dyed, vegetal tanned cow leather, 3 to 5 mm thick (so corresponding to 5-7 oz for those who use those measurements).
Now you see why I found the trick of the large needle … I was broke after buying my leather.
part 2 : about wood
Lots of people can access wood planks easily. Lots of people even use wood pallets as a cheap source for it.
I will always recommend to check the information burned on your pallet : the wood is usually treated to make it resistant to some eventual situations in their wood pallet life (humidity, mushrooms, mosses, insects, …)
Pallets are made of low quality wood, but it’s not really a problem.
When you find (or buy) a pallet, check the sign burned on one of the sides. There should be a code defined with letters somewhere.
Those letters define the country of origin, and the treatments the wood received.
Some of these treatments are all fine, some others are seriously bad for health.
Here is a list of the treatments of a wood pallet :
- DB : debarked. Ok, just the bark that was removed. Not a bad sign. Carry on.
- HT: Heat treated : good, they heat it to kill what is inside and make it harder. Go go go
- KD : Kiln Dried : well, it’s dried, that’s not bad ! go go go
- EPAL : European pallet. They follow strick treatment protocols (heat treated). Go go go
- EUR : old European norm. remember : old timers used coal and asbestos. What was OK by then is not always OK now. So … avoid
- MB : Methyl Bromide. Want to have some really bad chemicals getting inside your body ? then don’t use those, seriously
And if the palette is colored, run away fast. You think they color them for decoration ?
So, pine wood pallet, uncolored, DB-HT. That’s a safe source.
Step 2: Planning, Choosing a Pattern and Color
You need some planning before really starting the nice part of the job: you have to find a nice drawing as a reference, and some nice colors to fit with.
Internet is a good source of references, but be careful with ownership properties. Don’t steal the work of others. If you know the author, ask for authorization to use one of their drawings, especially if you plan to sell your work. They’d have the right to sue you if you sold something protected by author’s rights, it’d be quite annoying for you.
In the following examples, internet helped me: 2 drawings are generic and were inspired by images found online (the griffin and the celtic dragon) while the other 2 (Atalante and Pyros) were made with the special authorization from the artist Crisse (and as gifts for one of his friends).
The shield decoration is also a public and very classic japanese dragon.
Once you have the drawing, you then have to choose the dye(s) and eventually paint(s).
Choose them so they have a good contrast:
white on a black or dark brown background,
black on a light background,
natural leather, being light tan, can even be left without paint on a dark background if you want.
The following examples are (see photos):
- a LARP sword scabbar, griffin decoration, black dye, silver paint;
- an armband, celtic dragon decoration, dark brown dye, no paint;
- a frame, Atalante decoration, light brown, red or black dyes, white or silver paints;
- a book protection, Pyros and Atalante, light brown dye, no paint;
- and the shield, japanese dragon decoration, dark brown dye, white paint.
The drawings are always made at the last step, just before making the color. I don’t make the drawings before because shaping the leather might stretch it, deforming the drawing.
If you want to see this step about drawings, jump directly to step 6.
Step 3: Making the Wooden Base for the Shield
This shield will have a round shape. Therefore, you need to make a round
wooden base. Lay the boards on a flat surface, pressing them together. Using a compass, draw a circle on them. 60 cm is a large shield, heavy. 50 cm will be lighter but smaller. It really depends on your preferences.
Glue the boards in the shape of the circle and glue and nail 2 additional supports you can screw them if you prefer for more solidity.
Saw off all the unnecessary parts with your jigsaw
Using glue and nails or screws allow you to avoid protubing bolts, which would be a problem for security (LARP, remember?).
Sand, coat with stain and varnish this round wooden base.
Step 4: Making the Leather Part of the Shield
Here we are…
We start with maths… bad news.
You need to cut a large leather disc from your beautiful freshly bought skin. For that, you need to calculate the diameter of that disk.
I hope you didn’t buy your leather skin before….
Ok.
Your shield is 60 cm in diameter and the planks are 1 cm thick. A nice strong shield.
So you need: 60 cm + 2 times the thickness of the planks + 2 times the internal fold (as you will nail the leather on the inner part of the shield) and add 2 cm “just in case”.
Ok. Not “just in case”. Leather is thick and doesn’t fold like paper. You MUST take into account that thickness. 5 mm thick, 2 folds on each side, that’s 1 cm on each side.
So my leather disk is 60 + 2*1 + 2*2 + 2*1 … total … 68 cm in diameter, 0.4 m², 50$. Ouch.
Once the disc is cut, we start the first drawing session. geometry. Starting from the center, we trace the spokes of your disc at regular intervals. I took approximately 4 cm between each radius. It is calculated, it is peripheral to the circle divided by the number of tabs you want. The more tabs the easier to fold...
Then you draw the cuts. The first part will be laying flat on the cylindric surface of the shield side. Then the external part will be folded inside, and so it needs a different calculation.
Or you just do like me, cutting a V to be sure everything will remain properly spaced and not too complex to calculate and cut.
Step 5: Assembling
You can put your cutter down and grab your glue, hammer and beautiful nails.
Leather works very fine with neoprene glue, so don’t fear using it.
spread on your leather underside (the one with the fibres) and on the wood shield, then wait it doesn’t stick anymore and place the shield on the leather (by the way, if you want to be historical, forget the neoprene, use fish glue or bone glue, or even wet raw hide…. But you’re not making an historical shield here, so … deal with neoprene)
flatten your leather on your shield, press well, so it’s all flat and clean.
Wet the flaps well, fold, and nail them on the side of the shield. 2 nails for each flap.
Then wet again, fold and nail on the internal side of the shield. 2 nails for each flap.
Step 6: Decoration
Here be dragons.
Japanese, for the culture. How to know? Count the number of fingers. 3? Japan. 4? Ancient China (non imperial family). 5? Ancient China (imperial family)
Print your drawing on a paper (or 2, or 3…), assemble if necessary and attach them together with scotch tape. Mark the center of the drawing and the vertical and horizontal lines. Seriously, it’s easier to position the drawing like that.
Center the drawing using the vertical and horizontal lines of your shield. And then …. You must not move it anymore. Once you start, you must finish the first step, or you might lose everything. Repositioning a large drawing is a real pain.
Then, using your ball pen, outline ALL the lines of your drawing while pressing on the paper
that celtic dragon earlier was easy. Atalante a little harder, but Crisse makes “simple” drawings.
and you know what? The Japanese dragon was a real pain. Lots of details, scales, etc.
Normally, your drawing should have transferred onto the leather as a very light marking. But at least, it’s present there now and you can go to the next operation.
Get your needle or any other round tipped, easy to handle accessory and a bowl of water.
Water a small surface of leather, then using the eye side of your needle, push on the leather and outline again the whole drawing.
It’s long, seriously, but the result of using a round shaped tool is that you don’t break or cut the leather. It remains soft.
Once done, you can go to the next step… dye.
It can be a tricky one. Don’t start with your masterpiece. Practice before (you had a large hide, you cut a circle from it, so you certainly have leftovers for small tests, don’t you?).
Get your dye in a small pot (that can be thrown away, those dyes are really tough), refill your cup with water, get a sponge and a clean fabric (and a plastic glove eventually if you like your fingers with their natural color).
Wet the sponge, and use it on the leather. the leather will get dark, and water will be absorbed.
Once the whole shield is wet, you can put some dye on your clean fabric and use it as a brush to dye the leather, making light strokes.
The trick here is to keep your fabric wet but not soaking, so when you go across your embossed lines, the dye doesn’t get inside the lines, leaving them with their natural color.
Why did you wet the leather before ? Because there can be surface treatments, tanning process cleaning that were left longer on some places, and internal tensions. The water will soften the leather, allow the dye to get deeper inside and will uniformize the result.
Once done, and if you want the drawing to pop, get your brush and acrylic paint and … well… paint the inner lines (dilute your paint a little when doing so).
Here, you can see repainted lines and natural color dots (in the middle of each scale).
You can then add decorative nails around the shield.
Step 7: Final Details
It’s a shield… so attach 1 or 2 straps of leather
to a wooden base so that the shield is comfortable to hold. You can find references on those straps positions online, it depends on your preferences.
Hammer a row of decorative nails around the edge.
Et voila, your leather round shield is ready. Enjoy the work done.
And if you didn’t want it to be a shield, and just a wall decoration, then, it’s ready to be used!
Step 8: Some Other Examples
Here is another example, with Atalanta:
outline, press on wet leather, dye (light brown here) by strokes and not brush.
As you can see, the strokes were made with a quite dry fabric, so the different textures of the leather appeared and you can see the natural folds it had before.
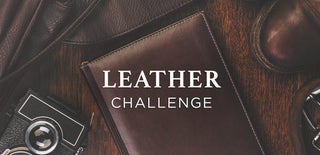
Participated in the
Leather Challenge