Introduction: Make Laptop Stand for CNC Router Using CNC Router Machine
i decided to make laptop stand for our lab Shopbot CNC machine, As it will help all CNC users in the lab to operate machine comfortably for this i started looking for some reference on Internet, i found some project which i took as a reference for designing my own design
1 Reference 1 from Refabstudio
2 Referance 2 from Pinterest images
i used this reference for making cnc laptop table , i want to do some modification in this as per my requirement
changes i want to do in this 1 this model have 7 degree of freedom as it is difficult to make it stable at perticular orientation by fixing 6 frictional joints 2 it have many linkages i want to make it simple by reducing linkages to 2-3 3 it have separate stand / table top for power control remote and laptop ,i want single stand for this
Steps for Designing the Model
the steps I took for designing CNC laptop stand
1 Designing cad model and do assembly check
2 Design mockup from cardboard
3 Make 2d drawinng for cnc
4 Making cuttiig tool path for cutting
5 Operating machine and do cnc cutting
Step 1: Cad Model of Prototype
This cad model is made in solid-works and i did this by making different parts and doing assembly of them this is i just made for visualization and checking dimensional relation
Attachments
Step 2: 2D Design for Laser Cutting
For testing mockup model of laptop, I made 2d cad file which I laser cut on 6mm cardboard sheet as shown
Attachments
Step 3: Making Mockup From Cardboard and Testing
This step i wrote you to make you understand designing and prototyping process you can skip this step of making mockup as you need final model
Step 4: Modification in Mockup and Designing Final File for Cnc
Changes done in Mock-up Designed
1 The height of model as earlier on testing mock i find arm length is short so i increased this
2 I removed one rotational joint along the hing ( the joint which give rotation about hing point ) as later i find there is no need of this joint in design also it may week hing point support for more see both video of mockup and final to compare model working
i am doing cnc on 19 mm plywood
Attachments
Step 5: Making Tool Path on Partsworks 2d for Cnc Router
follow this steps and see images stepwise to understand the process
Step 1 Open Partworks and click on create new file.
Step 2 Set the size of your sheet as my sheet is of 2400*900 so i put this dimension in that and set material z zero at at top and material thickness of 19mm
Step 3 Go to file option and click on import and import vector from here i.e dxf file which you made for cnc
Step 4 Now join all the open vector using join command in last row and first column of edit option so it make close boundary of your vectors.
Step 5 select inner profile of drawing and go to toolpath and select create profile toolpath on this the setting i keep for tool and cut depth to 19.3mm, i want to run my tool inside the boundary as Shown.
Step 6 once you select the tool and keep all parameters and click on calculate to make toolpath for the file it is showing you warning that cut depth is 19.3mm and material thickness is 19 mm, Now you can check the toolpath in 3d view on clicking on top to 3d view it shows you tool movement
Step 7 Create outer profile toolpath , once the toolpath is created now go to toolpath option and unclick the profile option and select the outer boundary profile and click on create toolpath option
Step 8 select the tool and add tabs in outer profile as tabs are joints which keep your cutting parts joint with your sheet so while cutting your tool will not move other parts ( here i select length of 10 mm and 4mm thickness)
Step 9 Now calculate the toolpath again and select both the toolpath it will show you total time it take for cutting as here it is showing here 55 minute for total cutting time and click on save toolpath option at right side,Now save toolpath to file it will save your file in .sbp format this file is gcode that is machine code for cnc cutting we load this in partworks for cutting
Attachments
Step 6: Machine Handling Using Shopbot Software
I have shopbot PRS alpha series 96*48*6 inch machine , so ii am writing steps in operationto this machine which may be diffrent frm your cnc
1 On machine switch and connect cables and set laptop and mount the tool on tool head
2 Set sheet on bed and mount the tool and and set the tool in the collet and fix the collat on the tool head
i am using shopbot for operating machine in i first need to open this software and move the machine head to origin point this is as per what you have given in tool path
1 the first step is to set the origin
2 second step is to run the spindle for atleat 5-8 minutes for spindle warmup
3 load part start the spindle and start cutting
Step 7: Operation on Shopbot
1 this is start window of shopbot after running spindle warm up (from c5 commond in setting ) you need to set origin ( for this go to move setting and set origin )and load file from cut Part
2 When you load file this window will pop up , now press entre and it will ask if spindle is on or not press start button on remote to on spindle and start cutting process
in you find some gaps in cutting actually they are tabs given for cnc to avoid lifting of your cutted part off sheet after cutting and wear ear muff and mask for your safety from sound and dust
Step 8: Doing Assembly of CNC Cutted Parts and Areas of Improvement
As i perfect sizes of pieces so they get fixed easily on table top on fixing everything i mount the table on side of cnc and it is fixed perfectely over side of cnc i take help of mr bhavani singh technician in our workshop in fitting this to shopbot
for locking it to certain position i buy locking threaded wheels with screw inside as shown in figure
Areas of Improvement
For anyone who wants to fabricate this design should consider the areas of improvement what i find in my design
1 In my design i have given side cuts for fixing boundary rib you can fix that for safty of your laptop
2 the bottom part which is fixed to cnc is not so strong along the bar you can increase its thickness, in my design this is of 40mm you can increase it to 60 mm as there is very little vibration due to this.
3 The rotating screw which i use inside the plywood for adjusting its movement is not holding the ribs so strongly or it may damage the internal surface on long use for avoiding this use
4 Al pipe in Centre of screw which will be in contact with wood and tight the knob in side for better holding. else i find everything good about what i made in terms of design , egromnomics and strength
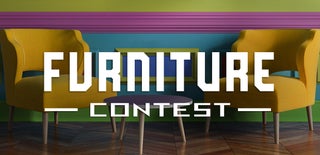
Participated in the
Furniture Contest 2018