Introduction: Make Professional Looking Front Panels for Your Next DIY Project
Making professional looking front panels for DIY projects neither has to be hard or expensive. With some FREE software, office supplies and a little time you can make professional looking front panels at home to spruce up your next project.
Supplies
Regular A4 printing paper (or white inkjet/laser labels depending on your printer type)
Clear inkjet/laser labels (doesn't matter which) - Available from Office supply stores
Double sided tape or spray contact glue
Sharp craft knife
Step 1: Get the Software and Design Your Masterpiece
There's a lot of free software out there. Just do a google search for free panel design software.
The one I used for this project was Front Panel Express. The software is free, easy to use and lets you design front panels (ultimately to be professionally made). However you can print it as a layout (with drill holes) and/or a finished looking design. I'm not planning on showing you exactly how the software works. This is more a guide on what you can do with the software and how to get finished front panels for cheap.
To start off with, draw on paper an outline of your panel. Then do a rough layout of your design so you know where you want everything. Adding in dimensions will help when inputting into the software.
Once you've downloaded and installed the software, start it up and select a new project. It will ask you dimensions so measure your front panels you're planning to make and put those dimensions in. While this particular software is limited (colours, fonts etc), it's more than enough to make something cool looking.
Start by assigning a reference point for all your measurements. This is where all of your measurements will be from. I've selected the bottom left corner (as you can see by the bullseye) That way either you can use absolute measurements to start with (which is what I did) and then move them around if need be. You can zoom in and out of the panel which makes it easy to manually align elements.
In the pictures above, there's several stages of me designing the front panel. I started with hole points and cut outs (like the front LED panel). Then I added in group surrounds (which you can change the shape and line size) using the software's various rectangular forms. From there, I added in text for the controls.
Once you're happy with your design, save it.
Step 2: Print Your Design
Now print two copies - one as you see it (the final version) onto your medium (paper, inkjet paper). As this will be what you will see, use high quality print (under your printers options). Also print (any quality) a layout version onto plain paper (with hole references you'll use to drill and cut out). These option is under the print menu.
Step 3: Attach Your Template, Drill and Shape the Front Panel
Cut the printed template design around it's edges so it will fit on the front panel. Now attach it with some sticky tape to the edges. Be careful to align it correctly and that the paper is stretched so it is flat.
For the holes, either scribe or hole punch the centre of the holes. Drill pilot holes with a small drill bit (2-3mm) to help keep the larger drills from wandering. Once that's done, use a larger bit to get the final holes. I can only go up to 8mm as my larger drill bits grab too much in plastic and tend to break the plastic than drill holes! You could use a step drill bit, but on plastic it's just as easy to use a hole reamer to get the final hole sizes when I need larger holes.
I've drilled some holes for the LCD cut out, large enough for the jigsaw blade to fit in so I can cut it out. It doesn't have to be exact, as you can use a file later to clean it up.
Once everything's cut and drilled, remove the template and clean the cutouts up with a file to the final size. Burrs can be taken off the sides with a file. Use a large drill bit by hand to remove any burr on the holes.
Finally, give it all a clean with some spirits (grease and wax remover, methylated spirits etc) to remove any contaminants.
Step 4: Attach Your Front Panel Design
There's a few ways of doing this. I only had on hand clear labels so I decided to print the design on plain paper. To attach it, I was out of contact spray so I used double sided tape to attach it.
Before starting, use a tack cloth (available from car paint stockists - a cloth with thinners will do something similar) to remove any foreign objects.
Put a few strips of doubled sides tape on the front panel. Roughly cut your front panel design except for one edge. This should be cut exactly on the line so you can align it correctly. If you're using double sided tape, you only get one shot to attach it. Otherwise you'll have to reprint it and use more doubled sided tape. However, that's the one good thing about using double sided tape - if you stuff it up, it's easy to remove and start again. If you use contact spray, you generally don't have that luxury.
Once the design is stuck on, again use your tack cloth to give it a wipe over. Then put a 1/2 sheet of clear printer paper over the top to protect it. It can be any type of paper (inkjet or laser) - it doesn't matter as it's only to protect the design.
Step 5: Trim and Cut Out Using a Craft Knife
Using a craft knife is easier as they're generally sharp. Use it to trim the excess around the edges of the panel and cut outs. For the holes, cut a cross (+) in the middle of the hole. This will help trimming around the small holes.
Step 6: Final Assembly
Now all that needs to be done is to assemble your hardware onto the panel and you're done.
Step 7: Final Thoughts
While this method works well, it's probably easier (not necessarily cheaper) to use one sheet of white inkjet/laser printer paper to print the design on and then cover it with a clear film. Also, standard paper is a little rough and you can see that the clear film doesn't bond flat with it. For the next project, I would probably use white gloss paper for the front panel design as I think this would look a lot better. Although, I was pretty impressed with the results using just what I had on hand here at home.
I'd probably also wrap the clear protective film around the edges onto the back when I do it next time. The edges seem to catch on the lip of the case when inserting the front panel down the top and bottom. However, I was a little worried doing this as I thought with the doubled sided tape, paper and two layers of film would not allow the panel to slip into the slot easily. But I think it would be okay, it would just depend on your project box.
One nice feature of using a front panel design is you can cut it to overlap, which is what I noticed when I put some transparent red acrylic in for the LED panel. If I had of made the cutout bigger, I could have cut the front template to the exact size I wanted and put a larger piece of acrylic flush with the overlay instead of wedging it in between the LCD and front panel. But it still looks fine.
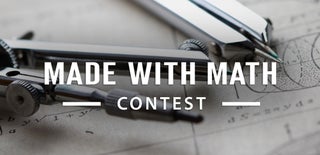
Participated in the
Made with Math Contest