Introduction: Make a 3D Printed Weaving Loom and Use It
I have always been inspired by weaving. The seemingly simple process of it makes me feel as if everything could be broken down into simple parts. When I was in Peru I would see people weaving gorgeous items, I wanted to try. I first started with a cardboard loom, which made me think that there must be an easier way to do this. Exited to use the new 3D printer I decided that it would the perfect excuse to print something. But for the new design I needed three things:
- Pegs instead of slots so I can remove project without cutting it
- A longer needle because I found using tapestry needles very difficult
- More space under the warp for the needle
- A comb of the proper size
- It must the prefect size for costers (approx. 10x10cm)
Step 1: Supplies
Equipment:
- 3D printer (I used an Ender 3 Pro) *optional*
Materials:
- About ten meters of printer filament
- Yarn that is medium or bulky
- Scissors (the ones on swiss army knives work amazingly)
- Small crochet hook (mine is a 3.25mm)
Step 2: Print It
I used an Ender 3 Pro and Cura, my settings were as follows:
- Infill: 10%
- Supports: None
- Wall Thickness: 1.2mm
- Scale 100%
- Bed Adhesion: Skirt
Make sure to print all three components, the loom, the needle and the comb. All of these were printed on a 22x22mm plate at the same time. BE VERY CAREFUL WHEN TAKING THE NEEDLE OFF OF THE PLATE AS IT IS VERY FRAGILE. All parts should be at the same scale so that they work well together.
.
Step 3: Print It (Without a Printer)
For those of you who don't have a 3D printer, you can order it online (crazy right?). For this example, I used Shapeways which seemed to be a suitable service for one-time prints. They also can print in a variety of materials which allows for some interesting uses for one's designs.
To start you will need to go to www.shapeways.com and make an account. Then you can click the upload button, you will only be able to upload one file so I recommend uploading the one below so that it all prints together. At the time of writing the cheapest way to print this was to use Versatile Plastic as the material and white as the colour. This came to CAD 43.72 or USD 33.06.
Attachments
Step 4: Weaving Time!
Before you start to get worried, don't...
Weaving is super easy!
For this section, you will not need a 3D printer, however, you will need your yarn, scissors and a small crochet hook. I recommend that once you get the hang of weaving, putting on some music or a tv show for some entertainment while you work.
Step 5: Warping
Warping is the process of creating the warp which is what you will use to weave through. Start by taping the end of the yarn to the bottom of the loom. Then, wrap it once around the first peg. Next, wrap your yarn around the loom like in the picture with the arrows on it. Once you are done, cut the yarn and tape it onto the other side of the loom. That's it! You have just warped your loom!
Step 6: Weaving the Weft
The weft is what you are going to be weaving through your warp. To begin, cut a length of yarn from your left shoulder to your right hand or vice versa. Take one end and tie it to the needle, as shown in one of the pictures above. Now, you are ready to weave. With the tip of your needle go under the first warp thread, then over, then under, repeatedly, until you get to the end of the loom, next pull the yarn through until you have 5cm (2in) extra at the end. With the comb push the yarn into a line about 1.5cm (0.5in) from the edge of the loom. Now from the other side of the loom take your needle and do the reverse, going over first then under and repeat. Comb this line so that it touches the line from before. Repeat this until you run out of yarn, when that happens, make a new strip and keep on going through. Once you are about to 1.5cm (0.5in) the end of your loom, you will want to stop there. if you have extra yarn cut it 5cm (2in) from the warp.
Step 7: Cleaning Up the Edges
Looking at your woven masterpiece one may notice that many loose ends are hanging from your piece. What on earth will you do with those? Unless you want to keep them, you will want to follow these steps:
- Cut the loose end to 2.5cm (1in) from the warp
- Take out your crochet hook and pull them through the loops on the side that you are working on until you get to the end of your piece of yarn
- Repeat for all loose ends
NOTE: I always do this while my project is still on the loom, this makes it so much easier.
Step 8: Taking Your Project of the Loom
Now for the moment, you have all been waiting for! Your masterpiece will finally be separated from your loom.
Let's get started:
- Remove the tape from the sides of your loom (If you can't remove the tape, you can cut it, but next time try to use painters tape)
- Take all of the warp loops of as shown in the picture above
- If you have done everything right you should be able to pick up the project and take it straight off of the loom
Step 9: Tying Off
You may see weaving instructions that tell you to cut your warp when finishing your weave. I find it easier to just leave it uncut, especially for beginners like myself. But you still need to do something about the warp ends (hint: the pictures might help):
- Get your crochet hook and poke it through the weft
- Grab the warp end and pull it halfway through, making another loop
- Pull the warp end through this loop, pulling until tight
- Snip the excess
You're done! I hope that was fun! If not, practice makes perfect!
Step 10: The Design Process
This project was designed in Fusion 360. My design process went a bit like this:
- Started with a sketch that included the body and a one peg
- Then I extruded the peg and sketched a lip to hold the warp on
- Extruded the loom body
- Went to the simulation workspace and ran some tests
- Repeated steps 1 to 4 until I was happy (At this point my design is the red loom)
- Added fillets and a needle
- Printed it
- Realized that the body got in the way of the warp and that I needed a comb
- Did everything again to get to what you have now
I have included the current .f3d file for those who would like to tinker with it. If you do post your new design, please link back to this instructable and put a link in the comments so that I can see. I would like to thank seamster for inspiring me to write this section.
Attachments
Step 11: Next Steps & Conclusion
I hope that this can be an ongoing project, but the only way that can happen is if there are improvements. If you have any suggestions I would be happy to collaborate with you. Here are some of my initial ideas:
- Making it more accessible for schools and homeschools
- Speeding up the manufacturing process
- Creating laser-cut and CNC versions
- Making different shapes and sizes
If you are a weaver and see some design flaws, please tell me so that I can make any changes necessary. I am new to this weaving thing and would eagerly accept any advice.
Thank you so much for reading this. I have put a lot of time and effort into creating this and I am glad that I can share this with an awesome community.
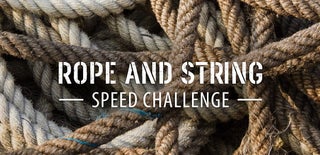
Second Prize in the
Rope & String Speed Challenge