Introduction: Marking Knife
Marking knives are a simple tool that can make a massive difference to your woodworking projects. Using the knife to score the wood creates a small channel that your saw will follow much better than a pencil line. This is particularly important if you use hand saws rather than power saws. The lines are also more precise than a pencil line due to their sharp design.
While you can use nearly any small knife a dedicated marking knife only has a bevel on one side that allows you to follow a ruler much better.
I have a pretty basic one and a decent marking knife has been on my wish list for some time now. The design I've made is suitable for both left and right-handed use.
I ended up making two marking knives, I wasn't happy with the first one's shape and I made a couple of mistakes (cracked the wood & drilled the holes off-centre). I've uploaded the templates for both designs so you can pick whatever one you like more.
Supplies
- Old saw blade or file
- Grinder
- Gas Torch
- Grinder
- Drill
- Sandpaper
- File
- Dremel
Step 1: Cut Out the Knife
Print out the template onto some paper, cut it out with scissors and then glue it onto a piece of saw blade.
Now cut the knife out using an angle grinder with a cutoff disc, then use a grinder to smooth and flatten all the surfaces of the knife.
There are a couple of ways to cut the semi-circle finger grove. For the first knife, I just cut the bulk out with the angle grinder and then used the smaller wheel of the sanding belt to smooth it out. For the second knife, I quickly softened the metal at this stage and then cut the bulk out with the grinder again and then used a half-round file and dremel sanding wheel to finish it off. I liked the second method more as I had more control over the size of the circle.
Step 2: Grind the Bevel
The exact angle of the bevel isn't too important, just try to make it the same on both edges. I just set the tool rest of the grinder and then carefully ground both edges. Only grind one side of the knife and leave the other flat, just like a chisel.
Once the bevel was done I used a Dremel sanding wheel to lightly round over the finger grove on the bevel side of the knife. Knocking off the hard corner just makes it feel much nicer. I've attached a photo of the two knives to show the difference.
Step 3: Make the Pins
I like to use small brass rods for my knife pins, & I've been using some brass tubing for the pin at the back end of the knife for a while now. I like the hollow pin as I can either tie a lanyard there or hang the knife up on a small nail, plus it gives it a different look.
Step 4: Drill the Holes
If you didn't soften the metal to file out the finger grove, you will need to do that now unless you like breaking drill bits. The mill saw blades are already hardened and standard drill bits won't be able to cut through it. It's very easy to soften (anneal) the steel, heat it up red hot with a gas torch or campfire and let it cool slowly, do not dip it in water!
Now centre punch where you want the holes and drill them to the same size as the brass pins. It helps to put a small amount of oil on the steel as you drill.
Step 5: Heat Treat the Blade
Now you need to harden the knife blade, only the end with the edge needs to be hardened. This is actually really easy, you just need to heat the blade up until it's 'cheery red' or a magnet no longer sticks to it. I used a gas torch and some firebricks but you can use charcoal and air blower as well.
Once the knife is hot enough plunge it into some oil and move it around. Once it's fully cooled down you can test if the hardening process worked by running a file over it, if the file skids over it without cutting it then it's hardened.
I recommend cleaning up the knife on some sandpaper to remove any burnt oil at this stage.
Now put the knife in an oven to temper it so it's not brittle, set the oven to about 200 degrees celsius and leave it in for an hour.
Step 6: Make the Handle
Select a piece of wood to use for the handle, either sand it flat or use a hand plane to flatten one side. Drill one hole through the wood, and drop in the pin to keep it aligned. Now drill the second hole and repeat the process on the second piece of wood. I marked around the outside of the knife and then trimmed it with a saw.
I normally use the pins to hold both pieces of wood together without the knife and sand the blade end of the handle as you can't easily sand that part once it's assembled.
Mix up some epoxy glue and coat the knife handle and pins, then assemble the knife and clamp it together until the glue dries.
Now sand or file the wood into the final shape you want, I find using a Dremel sanding wheel to shape the contours makes things a little easier.
If you have any glue spillage on the blade now's a good time to clean that off.
Step 7: Finish the Handle
I always like to finish knife handles by hand sanding the wood until it's smooth and fits your hand well. Lastly I gave everything a coat of linseed oil to protect and bring out the colours of the wood.
Step 8: Sharpen
I used some diamond plates to sharpen the blade, the first stage is to flatten the back of the knife and then sharpen both edges. Lastly, I used my strop to hone the edge.
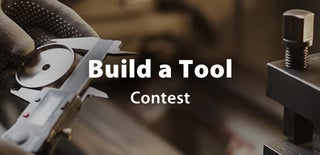
This is an entry in the
Build-A-Tool Contest