Introduction: Metal Micromachining at Home on the Cheap!
Hello fellow makers!
Lately I've been working on items that require parts much too small and delicate for my not so accurate home built CNC. As always I started searching the web for some inspiration, I fell down the rabbit hole of wire machining but ultimately realised it would cost a lot and the DIY versions out there are just way too complicated.
Next I stumbled across electrochemical machining which looked a lot more viable but having to build a new rig for it and then having to make conductive dies for every part was just too much of a hassle if you're doing a single part.
Then by accident one day I saw a video suggestion of photochemical machining, the description was exactly what I was looking for plus because I make PCBs regularly I already had everything I needed on hand!
In this Instructable I'm going to show you how you too can create some tiny parts with incredible detail for unbelievably cheap.
Let's get going!..
Step 1: What You Will Need:
To do some micro machining you will need the following:
- Photosensitive film
Amazon - Photosensitive Dry Film
- Aluminium sheet
For a cheap source of thin aluminium you can use aluminium cans (make sure to remove the plastic coating) or disposable "heat and eat" dishes.
Amazon - 0.048" Aluminium sheet
OR
- Brass sheet
- Hydrochloric acid
Amazon - Hydrochloric acid 37%
- Hydrogen peroxide
- Sodium carbonate (washing soda)
- Acetone
- Cleaning cloth
- Safety equipment eg. eye protection, chemical safe gloves, mask.
Optional:
- 500mw Laser module
OR
- Desktop laser engraver
- Transparency sheet
Amazon - Laser transparency OR Inkjet transparency
*As an Amazon Associate I receive a small percentage from sales made through provided links at no cost to you, this helps fund future projects.
Step 2: What Is Photochemical Machining (PCM)?
Photochemical machining (PCM), also known as photochemical milling or photo etching, is a chemical milling process used to fabricate sheet metal components using a photoresist and etchants to corrosively machine away selected areas. This process emerged in the 1960s as an offshoot of the printed circuit board industry. Photo etching can produce highly complex parts with very fine detail accurately and economically.
This process can offer economical alternatives to stamping, punching, laser or water jet cutting, or wire electrical discharge machining (EDM) for thin gauge precision parts. The tooling is inexpensive and quickly produced. This makes the process useful for prototyping and allows for easy changes in mass production. It maintains dimensional tolerances and does not create burrs or sharp edges. It can make a part in hours after receiving the drawing.
PCM can be used on virtually any commercially available metal or alloy, of any hardness. It is limited to materials with a thickness of 0.0005 to 0.080 in (0.013 to 2.032 mm). Metals include aluminium, brass, copper, inconel, manganese, nickel, silver, steel, stainless steel, zinc and titanium.
Source: Wikipedia
Step 3: Design Your Part:
To design your part you will only need a black and white positive image and that's it.
I use Adobe illustrator to design my parts as it has some great features to make drawing easy and accurate but you're not limited to it and can use any software you chose as the only requirement is a black and white image. Heck you can even use Microsoft Paint!
I made these three design to show off some of the capabilities of the photochemical machining process.
They are a Instructables name tag measuring 23x7mm, a 14mm micro sieve with 0.3mm holes and an incredibly delicate spiral 17mm in diameter with 1mm traces.
Remember when design and exporting the black areas will be left behind and the white areas will be etched away.
Step 4: Applying the Photosensitive Mask:
Now we get to the most important part of the process.
In this Instructable I will exclusively be using aluminium but the process is the same for most non ferrous metals.
We need to apply the photosensitive film onto the aluminium, if the aluminium is not prepped and film not applied correctly your design might start peeling away when etching ruining the entire part.
I start by sanding the aluminium sheet with some 400 grit sandpaper and then move on to a finer 1200 grit to give a smooth shiny finish.
Do not prep your aluminium ahead of time as aluminium naturally builds up a protective oxidation layer that will cause problems while etching so only sand as you use.
- Remember to wear the appropriate safety equipment when handling chemicals -
With the aluminium sanded we can wipe them down with a clean cloth and some acetone to get rid of any oily residue.
Next in a dimly lit area away from natural light you can cut off a piece of the photosensitive film that is large enough to cover the front as well as the back of the aluminium sheet.
The photosensitive film has a protective film on the front and back of it, to remove simply take two pieces of painters tape and stick them on the corner of the film both sides. Then peel the tape off and the back protective film should come off with it.
Keep the front protective film on.
Now apply the film onto the front of the sheet first making sure to push out any air bubbles then wrap it around and do the back as well. I always do the front face first as the back does not need to be as perfect.
You will notice that the film doesn't really stick that well to the surface, for it to adhere we will need some heat. Simply heat it with a hairdryer or a heat gun and rub down the film well once hot.
Now I like to pre-expose the back face of the sheet, to do this I simply tape over the front face to protect it from light (black electrical tape works best but as I will use this sheet straight away I simply covered it in painters tape) then place the back face in the sun for about 30 seconds to expose it. You will notice the film goes from a light blue to a dark blue when exposed.
Your aluminium sheet is now sensitised and ready for photochemical machining, with black electrical tape completely covering the front you can also store your sensitised plates like this.
Step 5: Expose Your Design:
There are a few ways this step can be done, we will be looking at the two ways I usually do it.
Exposing the photosensitive film using a laser engraver:
All the examples in this Instructable was done using this method as it it the simplest, quickest and most cost effective for one off parts.
Using a very inexpensive 405nm diode laser engraver module from Amazon usually used for engraving on wood we will "engraving" with it at about 1% of it's power onto the sensitised aluminium sheet.
The 405nm UV light emitted by the cheap laser modules are exactly what is needed to expose our film.
Using LaserGRBL as my preferred laser engraving software I set the output power at 8 (it goes from 0-1000) and my engraving speed is set to 1000mm/m using line to line tracing and 15 lines per mm resolution.
These settings give me a light exposure with no bleeding of the light onto areas that shouldn't be exposed and it also develops quick and crisp.
Exposing the photosensitive film using a printed negative:
With this method is perfect when you will be making multiple duplicates of the same part and also results in amazing detail.
You will start by printing out an inverted copy of your design onto a transparency sheet, I recommend using a laser printer and priting using the high quality/photo setting as it gives a better negative mask.
Place the printed negative transparency onto the sensitised aluminium sheet (remember to work in a dimly lit area away from natural light when handling the sensitised aluminium) and sandwich it between two glass planes.
You can then move the sandwiched plate into the sun for about 30 seconds to a minute depending on the UV exposure.
Bring the glass back into your dimly lit room before uncovering.
Your positive should now be ready to be developed.
Step 6: Develop the Negative:
To remove the unexposed film we need to submerge the piece in a development solution:
Add 1 teaspoon of washing soda to about 200ml of water, you want about a 3% solution. Adjust this according to your specific brand of photoresist film. It's best to first try with a spare piece of film, you want it to take about 3 minutes to dissolve. If your mixture is too strong you'll also dissolve the developed film.
Now remove the top protective film and submerge your aluminium sheet with the film into the solution.
You will see the undeveloped film starts to get opaque and dissolve into the water. Using a soft bristle brush you can gentle brush away the dissolving film until you are just left with the dark blue developed resist.
If there are small areas that did not develop correctly or wiped away you can use a PCB touch up marker to correct it. If large areas lifted while developing I will recommend repeating the steps above as your film might have not adhered correctly.
Rinse well with clean water.
Step 7: Photochemical Machining:
- WEAR ALL NECESSARY SAFETY EQUIPMENT BEFORE CONTINUING! -
In a well ventilated room or outside mix two parts hydrogen peroxide and one part of hydrochloric acid together in a separate container. Ferric Chloride can also be used as an alternative to this solution if you have some available but is much slower and is a nastier chemical. (this is your etching solution so handle with care)
Tip: The hydrogen peroxide + hydrochloric acid is a safer alternative to Ferric Chloride and is much easier to use.
Carefully submerge the aluminium into the etching solution, the aluminium that needs to be etched away has to be completely submerged and facing upwards.
Agitate the mixture regularly.
Leave it in the solution until it has dissolved all of the exposed aluminium leaving behind only the aluminium under the resist.
Remove the part as soon as it has etched through as leaving it longer will result in under cut and there is also a risk of the film lifting.
When done rinse thoroughly in clean water.
After the etching is complete your part will still be covered in the photosensitive film, to remove this simply submerge the part in a little acetone and it will peel off by itself.
Step 8: The Results:
Here are the results I got from this process.
The photochemical machining was done on 0.13mm thick aluminium which my CNC would have destroy at first touch with regular machining
Under a microscope you can see that the 0.3mm holes in the sieve are pretty well defined and accurate throughout and much smaller holes are also possible with a printed transparency negative as there is less light bleeding.
Overall I'm super happy with the results I get from this process and it opens up loads of new possibilities being able to manufacture parts on this scale.
Step 9: Troubleshooting:
Here are some of the problems I faced when starting out with photochemical machining:
Metal not prepped properly:
Halfway through etching this piece the resist started coming loose and eventually completely separated, this was due to not sanding the surface with 400 grit sandpaper first and also I simply washed it and did not wipe it down with acetone before applying the photosensitive film.
Overexposure and light bleeding:
With this piece I was testing out the power settings of my laser.
You can see by looking at this picture of the developed film that the one on the left was overexposed and caused the light to bleed and expose the areas next to the design.
By looking at this picture after it was exposed but before development you can see that the design should be just barely visible like the top and not a dark blue like the bottom.
Step 10: Enjoy!
I hope you guys find this Instructable useful and if you have any questions please feel free to leave me a message or comment bellow.
If you found this Instructable helpful and would like to support my future projects you can Buy Me A Coffee.
Thank you for taking the time to read through my project and as always..
Happy making!
---
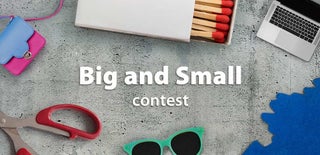
Participated in the
Big and Small Contest