Introduction: Mini Boat
Have you ever wanted to build a boat?
How about a really (really) small one?
If so, you may be interested in building this 6-foot mini boat.
Here are the highlights:
- Super darn cute and a joy to ride.
- 100% electric propulsion from an outboard trolling motor.
- Made from precision laser cut components.
- Interlocking assembly means no jigs required.
- Simple and quick cable-tie and epoxy construction.
- Interior bulkhead design keeps it floating even when flooded.
- Steers with a beefy plexiglass steering wheel.
- Low and comfortable seating position.
- Surprisingly stable flat-bottom hull design.
- Reliable and accurate steering geometry.
- Convenient cubby storage (above dash).
- Additional behind-seat storage.
- Designed to fit a 6'2" tall rider 200lbs or less.
I was inspired to build my own mini boat after seeing a few others, most notably Paul Elkin's 8-foot "Little Miss Sally". Be sure to check it out.
I wanted mine to be a 6-foot boat so that I could say:
Neener-neener Paul, my boat is smaller!
;-)
For more fancy product-shots, videos, and info on my mini boat, please visit my website:
https://rapidwhale.com/mini-boat.php
Thanks, and enjoy.
-Josh!
Step 1: Design (or Purchase) Your Boat Parts.
You can design your own boat referencing this workflow,
or you can buy a DIY Kit or Plans from my website.
As with most of my projects, I spent more time designing than actually building. Here's what my design workflow looked like for this project:
- Sketch a desired shape.
My concept sketch started on a sticky-note (don't they all?). That sticky-note sat in front of my desk for a few months as motivation to actually start such a daunting project. The sketches that followed were drawn with more realistic proportions in order to actually fit myself into the boat.
- Model it in CAD.
I imported my favorite profile sketch into Solidworks and designed around it. I simulated the material and water-displacement in order to determine my vessel's center of gravity and center of buoyancy. The relationship between center of gravity, center of buoyancy, and hull shape is critical for determining (or estimating in my case) boat stability. I wasn't keen on designing an unstable boat, so I began tweaking my design as I went in order to make it more stable.
- Build and test a scale model.
I laser cut a 1:2.2 scale model to test in my friends hot tub (hot tub jets make for an awesome choppy-water simulation by the way). I loaded up the scale model with weights to match. The scale model floated, but it wasn't quite as stable as I was hoping for.
- Adjust the CAD model.
I took what I learned from the scale model and adjusted my CAD model accordingly. I needed to move the center of gravity forward, and I needed to slightly modify the hull-shape. Sounds simple, but that meant 40+ more hours of design edits. Ouch.
- Cut / Print the Full Scale Boat Parts!
To build the full-scale parts meant a lot of laser-cutting and 3D printing. I actually cut / printed enough DIY Kits for 3 boats. My Dad and a friend of mine also wanted to build their own.
Step 2: Gather Your Supplies
In addition to the custom components that you created (or purchased as a DIY Kit) you will need to purchase a variety of off-the-shelf components. This will cost you an additional $500 - $1,100 depending on how crafty or fancy you are.
Here is a link to the complete Bill of Materials.
And here is a part list overview:
- Trolling Motor
- Motor Connector Plug
- 12V Battery
- Battery Straps
- Rope
- Quick-Cleats
- Pulleys
- Seat
- Epoxy
- Stir Sticks
- Stir Cups
- Wood Flour
- Icing Bags
- Gloves
- Brushes
- Chemical Foam
- Cable Ties
- Varnish
- 12V Light
- PFD (life vest)
- Emergency Paddle
- Dean's Connector
- Dead Mans Cable
- Charger
- Switch
- Volt Meter
- Paint
- Stain
- Fillet Tools
- Fiberglass Tape
- Fiberglass
- SS Hardware
- PVC Pipe
- Wire
- Vinyl Tubing
- Hook and Loop
- Carpet
Step 3: Build Sub-Assemblies
Seat Base:
- Glue the top and bottom of the seat base together and let dry under weights.
- File any excess dried glue out of the pockets.
- Glue in the rest of the seat base assembly.
- Clean up the glue before it dries.
Steering Wheel:
- Glue the center of the steering wheel assembly together. Take note of which side is routered. You can use Acrylic Cement, CA Glue (Super Glue), or Epoxy.
- Glue on the front and rear pieces of the steering assembly. Take note of which side is routered.
- Sand it to a nice uniform matte finish. This helps hide any unsightly gluing jobs.
Steering Drum:
- Glue the matching sets of the sub-assembly together.
- Let them dry under clamps and weights. Binder-clips work best!
- Sand any excess glue off the surfaces.
- Stack and glue the drum sets and let dry under weights.
- Scrape off any excess glue.
- Cut the motor shaft to length such that the total exposed shaft length is exactly 22.35". Use a metal conduit rod (as pictured) to ensure you do not cut (or drill) through the wires. You can also use that small motor-shaft sleeve as a guide for cutting. Rest a hack-saw blade on it, as we will not be using this sleeve in the final assembly. Remove the sleeve and leave only the motor mount on the shaft after you are done cutting.
- Use the 3D printed hub as a guide for drilling the holes. Obviously don't drill through the metal conduit that is protecting your wires. That means you will need to drill 4 total holes. Align the hub before your start drilling to ensure your steering drum will be facing the correct direction when mounted. Look at the propeller mounting location when determining alignment.
- Remove the protective metal sleeve that was protecting the wires.
- Ensure the only loose item on the motor shaft is the motor-mount itself. No other loose items should remain on the motor shaft. That sleeve should not remain.
- Epoxy the steering drum hub to the wooden spokes. You will want to dry-fit the spokes first to ensure they seat properly before applying epoxy.
- Quickly epoxy the Hub/Spoke assembly into the drum assembly. You may want to use a little hammer-force to ensure it all goes together smoothly.
- Drill an access hole (likely 1/2") into the assembly so that you can fit the bottom bolt. Grab one of the 2.5" long 1/4-20 bolts and test-fit to ensure you drilled out enough.
- Press-fit the delrin thrust bearing into the 3D printed steering drum hub. I have already inserted in in some kits, in which case just make sure it is there.
- Attach the steering drum to the motor shaft. It's very tricky to feed the hardware through the motor shaft without pinching the internal wires. You will want to use a smooth, rod (perhaps one with a cone-tip) to feed through first, in front of the hardware to more easily separate the internal wires, then drive the bolt in right behind it. Alternatively, one customer decided to thread in QTY: 4 smaller bolts from all sides that do not pass all the way through the wire area of the shaft. That customer used QTY: 4 of 3/4" length bolts instead of QTY: 2 of the 2.5" bolts.
Step 4: Prep for Assembly
Epoxy the Puzzle Joints:
For the sake of shipping (and manufacturing) some of the larger plywood pieces are split into multiple pieces. You must therefore epoxy together all of the puzzle joints in order to create the larger pieces of the boat. These puzzle joints end up being just as strong, if not stronger, than the rest of the plywood. So fear not, your puzzle joints are rock-solid.
- Run a small amount of 5-minute epoxy (or marine epoxy) along both edges of the puzzle joint.
- Use a flat board as a press. Wax paper can be used to keep the epoxy off the flat board.
- Stomp on the board to ensure a flush press-fit of the puzzle joint.
- The press fit should be tight enough that you do not need to use any serious clamps. Just use binder clips on the corners as pictured.
- Repeat for all puzzle joints.
- CRITICAL: When gluing the nose pieces (of the hull-sides), triple check that they will be glued such that the bottom of the boat is FLAT (not curved). This is a FLAT-BOTTOM boat. It is easy to make this mistake.
Glue Motor Mount to Transom:
This is where the removable trolling motor will tighten-down onto your boat. So it will need to be re-enforced as follows.
- Apply liberal amounts of wood glue and stack the pieces accordingly. Be sure the cable-tie slots are all aligned. You may want to avoid excess glue in these areas or you will need to scrap it out to fit the cable-ties through later.
- The piece with the two holes (pictured) is the top-most piece to be stacked. Put it on last.
- Be sure they are all perfectly aligned and let them dry under weights. Your battery makes a very good weight.
Sand Puzzle Joints Flush:
- Sand the puzzle joints after the epoxy has cured. Don't go too crazy with the sanding, you are just trying to remove the excess epoxy from the visible surface. You don't need to do much sanding at all to the non-visible side.
Trace and Cut Fiberglass:
- Use the newly formed pieces to trace and cut the fiberglass accordingly. Cut the fiberglass right on the line because you will not want this fiberglass to wrap around any edges (that's what the 3" fiberglass tape is for).
- You will be fiberglassing: The entire hull (including the transom), the deck (optional), and the floor of the cabin (where you sit). The floor of the cabin is not able to be traced since the shape is not obvious, you can cut that piece after assembly of the plywood or you can try to guess as to the shape by tracing and cutting a second bottom-hull piece and trimming off where the inner bulkheads will go.
Step 5: Assemble the Boat
Begin Cable Tie Assembly:
- Knock out the large circle in the bulkheads. You will be using this opening to fit an arm into the bulkhead in order to apply the necessary epoxy fillets.
- Attach the bulkhead plywood to the base of the hull first. Ensure the cable ties are oriented such that the heads are visible after assembly.
- Attach the sides of the hull, and the transom next. Leave the cable ties loose for now, such that adjustments can still be made.
- Carefully form the hull shape by bending the plywood and attaching cable ties accordingly. If you bend too quickly, or unevenly, then you may crack the plywood near the kerf-cuts. You can repair any cracks with epoxy later. To ease bending, consider a poor-man's steaming technique utilized by applying water and running a clothes-iron to force steam into the wood.
- Attach the dashboard. You will also want to glue the two small pieces to the dashboard, and possibly cut the profile of the dead-man's Dean's Connector before assembly. Reference the pictures.
- Attach the piece (that is similar in shape to the dashboard) to the bottom of the deck.
- Attach the deck.
- Attach the small pulley block pieces connecting the dashboard to the similar shaped piece.
- Begin cinching down all of the cable ties. The wood pieced inter-lock, and you are left with an edge as pictured if you are doing it right.
- Snip the dangly-bits off most of the cable ties. So that they don't get in the way as you begin the next step. At this point your entire boat should be assembled, minus the plywood windshield piece which will go on later.
Epoxy Fillet Hard to Reach Corners:
- Mix epoxy and Wood Flour until you get a peanut-butter consistency. It takes a good deal of Wood Flour, and it's better to error on the side of too stiff than too runny.
- Use the Icing Bags to apply the newly mixed peanut-butter-like epoxy. Cable-tie the back so that there is no chance of a leak from the wrong end.
- Channel your inner contortionist as you try desperately to fillet all of the corners INSIDE the bulkhead. This is by far the most challenging part of the construction. You will have to apply the fillets blind because unfortunately there isn't enough room to get a head AND arm into the bulkheads. Use a phone to take a picture of what your progress looks like, and repair the fillets accordingly. Use the wooden fillet tools if that is helpful.
- Apply fillets to the inside of the transom. (back of boat) Run a wooden fillet tool over the fillets to make the them perfect. Do that for as many fillets as you can.
- Apply fillets to the inside of the nose. (front of boat)
- Apply fillets up under the inside of the deck. At this point nearly every cable-tie and corner on the inside of the boat should be covered in an epoxy fillet. The only exception being the base of the floor of the cabin (where you sit). That spot will have its cable-ties trimmed and fillets applied after pouring foam.
Fill Bulkheads with Foam:
The bulkheads should be air-tight once construction is completed. The foam is just there to ensure that even with a leak, the bulkheads will still displace water. The purpose of the bulkheads is to provide flotation to a flooded boat. You can pack the bulkheads with pool noodles or just leave them empty if you don't want the redundency and professionalism that two-part foam offers.
- 5-Minute Epoxy the small wooden tabs into the back of the bulkhead hole. You will use these tabs to...
- 5-Minute Epoxy the large wooden knock-out panel back into the bulkhead. Align the grain if you want to be fancy, and ensure the small hole is punched out beforehand.
- Ensure you epoxy all around the knock-out panel. Otherwise the foam may push it out as it starts to expand.
- Quickly mix the foam.
- CRITICAL: Only mix as much foam as you need. (Assuming 2 lb density: You need 1/4 gallon of A + 1/4 gallon of B mixed well and then poured into each bulkhead).Follow the directions on the label. Confirm volumes. Do not pour too much or you risk injury, death, and blowing up your boat. I'm not exaggerating: Pour-foam can create a LOT of pressure.
- Pour the foam. It will quickly start to expand, so rock the boat such that the still-liquid foam gets evenly distributed throughout the bulkhead. That way as it expands, it fills the entire cavity evenly. The foam gives off a good amount of heat and creates a good amount of pressure. If you do everything right, most of the bulkhead plywood should be warm, and the foam should exit out the small hole opening. Wait for the foam to cure.
- Seal the bulkhead by carving out excess foam and gluing in the small plywood circle. Align the grain if you want to be fancy.
Continue Assembly:
- Snip the cable-tie heads off the floor of the cabin (where you sit). The now-cured epoxy fillet that you laid along the inside of the bulkhead will hold this piece in place.You are snipping these cable-tie heads off so that you can more easily run a fillet bead.
- Apply a fillet along the base of the floor of the cabin (where you just cut the cable-tie heads). As usual, clean it up with a fillet tool. At this point every single corner inside the boat should be covered in a nice looking epoxy fillet.
- Cable-tie the plywood windshield together. Keep them fairly loose for now and ensure the cable ties are oriented such that the heads are visible (outside) after assembly.
- Attach the windshield to the deck w/ cable-ties. It is easiest if these cable ties are already fed through the slots in the deck before placing the windshield (as pictured previously).
- Cinch down all the cable-ties. It helps to use needle-nose pliers.
- Epoxy fillet all inside corners of the windshield area, even those inside corners where the windshield meets the deck. This ensures a permanent bond to the rest of the boat. Let the epoxy cure.
Step 6: Admire Your Work Thus Far.
Awesome:
You just turned a pile of wood into a shape that resembles a boat! Yeah, we built three of them.
Step 7: Waterproof the Boat
Prep the Interior:
- Sand off any excess epoxy and ensure the wood is clean and even.
- Vacuum the entire interior.
Waterproof the Interior:
- Cut and layout a sheet of fiberglass all along the floor.
- Wet-out the fiberglass with epoxy. It doesn't have to be pretty since it's just the floor, which will eventually be covered with carpet, but try and keep air-bubbles to a minimum.
- Epoxy coat the entire interior, starting with the harder to reach spots like the nose, transom, and inside the windshield piece. I would suggest putting the epoxy on heavy in the hard to reach areas since no one will be seeing those areas. Let the epoxy cure overnight.
- Pro Tip: If you wash the recently cured epoxy with soapy water, you can remove a residue layer that clogs sandpaper. Otherwise your sand paper gets immediately clogged whenever you sand fresh epoxy layers.
- Lightly sand all of the visible epoxy and re-coat the interior with another coat of epoxy.
- Epoxy coat the seat base and the steering drum while you are finishing up. No need to have multiple layers of epoxy on these parts.
Prep the Exterior:
- Snip all of the cable-ties flush with the plywood.
- Epoxy fillet all of the exterior corners. Reminder: Fillets should be created with epoxy that is made to be a peanut-butter consistency with wood flour. Be sure to get enough epoxy in those corners such that you can later sand them into a round-over.
- Jam that same thickened epoxy into all of the kerf-cuts on the nose of the boat.
- Jam that same thickened epoxy into all of the small gaps/voids all around the exterior. If you can fit a fingernail in it, fill it. This is to ensure you don't get air bubbles when you lay out and wet your fiberglass.
- Sand all of the epoxy corners to make them rounded.
- Sand the nose and the rest of the exterior to remove excess epoxy.
- Fill-in any nooks or bubbles that didn't get filled with epoxy the first time. Sand flush after curing.
- Vacuum the entire exterior and then rub it down with Denatured Alcohol to ensure it is as clean as possible and ready for waterproofing.
Waterproof the Exterior:
- Cut, layout, and wet-out strips of fiberglass tape all along the corners of the hull. Try and keep air-bubbles to a minimum and wet the entire thing out from edge to edge. It tends to stay put once wet, but keep an eye on it to make sure it doesn't wonder. be sure to cover all of the edges of the hull, and then let cure.
- Lightly sand all of the edges to get them somewhat flush with the hull panels. Don't sand the rounded corners at all, as it's too easy to accidentally sand through the fiberglass at this point. Hit them with a handheld sanding pad if need be. Just light sanding is all that is required, knocking down any obvious problem areas.
- Layout and wet-out the pre-cut sheets of fiberglass for each hull section one by one. Repeat until the entire hull is covered in glass and epoxy is cured. If you did it right, there will be no air-bubbles and look like shiny wood.
- Lightly sand the entire hull. Avoid sanding the rounded edges, just focus on the surfaces for now.
- Clean the hull w/ a vacuum and Denatured Alcohol.
- Coat the entire hull in epoxy, lightly sand / clean / and repeat.
- Ultimately you should have 1 layer of wet-out glass, and 2-3 coats of epoxy on top of that.
Now we are going to do those same steps to the top of the boat:
- Flip the boat over and begin working on the deck. I stained my deck, but I wouldn't advise putting a dark stain like mine under a layer of fiberglass/epoxy because as you can see it showed all sorts of epoxy errors. I'll later go on to paint over this deck, so it didn't end up mattering in the end. I'm still glad I stained my wooden windshield piece though.
- Layout and wet-out the pre-cut deck sheet of fiberglass. If you decide not to glass the deck, then skip this step.
- Cut, layout, and wet-out strips of fiberglass tape along all of the corners of the deck. You can also do this when you are working on the corners of the hull, the order is not critical.
- Coat the wooden windshield piece in epoxy while you are at it. This piece does not need fiberglass.
- Lightly sand the entire top side of the boat. Avoid sanding the rounded edges, just focus on the surfaces for now.
- Drill and clean up any areas in the fiberglass that are meant to be openings.
- Clean and wipe down the boat.
- Coat again in epoxy, lightly sand, clean, and repeat.
- Ultimately you should have 1 (optional) layer of wet-out glass on the deck, and 2-3 coats of epoxy on top of that. At this point your entire boat is waterproof and every square inch is covered in epoxy.
Step 8: Paint (optional)
Prep for Paint:
- Ensure the surface is smooth. Sand with 220 grit sandpaper to knock down any imperfections. It doesn't have to be absolutely perfect since marine paint calls for at least 3 coats.
- Wipe the surface clean. Denatured alcohol is your friend.
- Tape the area to be painted. I'm not a fan of blue painters tape, so I tend to use thin green automotive tape anywhere paint will touch tape. I use the blue stuff to block off large areas.
Paint:
- Follow the directions on your paint can.
- Paint on your first base-coat. Move fairly quickly and in an orderly fashion to ensure newly applied paint always hits wet paint.
- Sand, clean, and re-paint as many times as desired. Typically marine paint will call for 3 coats minimum. I did 3 coats.
- Peel off the tape!
Step 9: Varnish
Varnish is a necessity evil in order to protect your exposed epoxy from harmful UV rays.
- Prep the surface for varnish by cleaning it and wiping with denatured alcohol. If you painted part of your boat already like I did, you are going to want to tape off the paint to protect it from the varnish. You only want the varnish going over epoxy, not paint. And you don't want paint going over varnish, so if you plan on painting your boat tape off that paint area.
- Follow the directions on your varnish can! It is absolutely critical that you stir the varnish thoroughly before and during use. If you don't, then you run the risk of applying varnish that will never cure (ask me how I know). And not all varnishes are created equal. I tested two and put the better one in the bill of materials.
- Apply your varnish with a brush to all surfaces that will be exposed to the sun. I found that using the cheap disposable brushes was fine if your application technique is adequate. I would avoid applying it to any surface that is not exposed to the sun. I had issues with it not curing fully when I put it where the sun don't shine.
- Most varnishes will require you to sand w/ 220 grit after waiting at least 24 hours between coats for a minimum of 3 coats. I did 3 coats. The varnish I link to in the bill of materials allows for a wicked-fast application process than allows you to knock-out all varnish coats in a single day.
- Varnish your steering drum while you are finishing up.
Step 10: Final Assembly and Wiring
Begin Assembly:
- Bolt on the rear pulleys. The 3D printed spacers keep the pulleys level when mounted on the curved deck, and the smaller spacer goes under the deck (not visible) to keep the nuts level. The cover is held on with the one inner-most bolt, so tighten that bolt up last, after you place the cover. There are mirrored pieces for port and starboard sides, so no two pieces are identical. Pay attention to how your are assembling them and don't mix up the covers.
- Bolt on the front pulleys. Bolt them on staggered. Meaning: If you bolt one closer to you (as pictured) bolt the other one (on the other side) further from you. You need the pulleys to be staggered so that the rope runs through them and around the steering shaft smoothly. Use the fender washers on all spots where washers touch wood.
- Bolt on the Quick-Cleats to the steering drum.
- Bolt on the Delrin steering shaft bearings. Float the steering shaft in them as you tighten down. That way you can rest assured the two shaft bearings are concentric to the shaft after tightening.
- Drill holes in your steering shaft according to the note.
- Bolt the 3D printed steering hub onto the shaft and bolt the steering wheel onto the hub.
- Install the steering shaft into the boat and bolt on the final 3D printed steering shaft piece to hold it all in.
- Press-fit the motor controller. It goes in from behind the dash, and you may need to spend some time filing excess epoxy to get it to fit perfectly.
- Press-fit the 3D printed motor controller knob onto the motor controller shaft. That holds the motor controller in place.
- Attach the straps, seat, and hook-n-loop strips to the seat base. Be sure to thoroughly clean the seat base where you plan on attaching the peel-n-stick adhesive.
Wiring:
- Review the schematic.
- Wire the motor. Its never a good idea to use smaller wire than stock, and this motor comes with 10 AWG wire, so I would suggest sticking with that, and even transitioning to 8 AWG wire for the wire harness inside the boat.
- Run the motor wires through tubing (1/2" ID, 5/8" OD was the ideal size).
- Connect the motor wires to the trailer hitch connector. I didn't need to solder directly to this connector, I was able to tin the wires then file 'em down to fit inside the holes. If you strip a bolt, or can't get the wires to fit, then I wouldn't hesitate to just solder direct.
- Create your Dead Man's Switch. Use a proper Dean's Connector, which is rated for something like 60 amps, which is fine for the trolling motor which calls for peak current of 40 amps.
- Begin creating the wiring harness. You will want to measure, perhaps with a string, and cut your wires accordingly.
- Drill your own volt-meter and light-switch holes in the dash if you plan on having those features. I would suggest clamping on a sacrificial piece of wood to reduce the change of splintering the back side.
- Install the light. Use a gasket.
- Install the main wiring harness you created. I ran the wires through a large diameter tube and hot-glued the ends in an attempt to waterproof them. It's not necessary though, you could just run cable-ties every 6 inches.
- Wire in the fuse. It should be as close to the battery terminal connection as possible. I mounted mine up under the deck where the trailer connector is located (see pic).
- Connect the wires to the in-dash motor controller (reference wiring diagram).
- Cable-tie the wiring harness out of the way. Alternatively, you could drill a hole in the further wooden piece to run the wires through that. Try and coat the edges of any hole you drill with epoxy (5-minute epoxy is fine) in an attempt to maintain waterproofing of the wood. The wiring harness should look clean and tidy if you did a good job with cable-management.
Continued Assembly:
- Install the seat. Make sure to clean the floor of the boat to ensure the peel-n-stick adhesive on the hook-and-loop tape will stick. I would suggest doing a test-fit before adhering to the boat. I installed my seat such that in the fully open position, it was just barely touching the wood behind it. I had read that these seats do not like a lot of weight reclining on them, so I think it is a good idea to have it butt up against the wood support as I did. Mark the perfect location so that you can place it there again with adhesive. You will not get a second shot at this, and the industrial grade hook-and-loop is pretty much a permanent mounting solution.
- Run the rope. It is critical that you run the rope as pictured. If you deviate from this, then you will either limit your steering ability, or have backwards steering.
Step 11: Document and Enjoy.
Be sure to check out the other info, pictures, and videos on my website:
https://rapidwhale.com/mini-boat.php
Thanks.
-Josh!
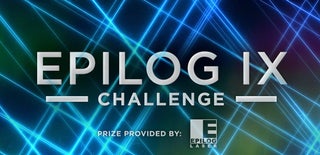
Runner Up in the
Epilog Challenge 9