Introduction: Monkey Candle Sculpture
Intro-
In this, I will be taking you, step by step, through the process of how I turn sculptures into delightfully smelling candles. I will: show you my sculpting process, how to mould the sculpture and finally how to make this in to a candle. I will try and add in cheaper/more readily available materials where possible, as I know that some of these materials can be quite expensive; especially if you're just starting out. I hope you enjoy this tutorial, you find it helpful and informative and it gives you some inspiration with moulding and candle-making!
Supplies
-Oil based clay
-Water based clay
-Basic sculpting tools
-Newspaper
-Parcel tape
-Marbles (as eyes)
-White spirit
-Release spray/petroleum jelly
-Moulding silicone
-Thixo
-Plaster
-String
-Wick
-Soy wax
-Essential oil (optional)
-Disposable gloves, cups & mixing sticks
-Double boiler
Step 1: Armature
To start with, when sculpting anything you must think about the armature. The armature of your sculpture is essentially the skeleton, it acts as a base & support to your clay. Armatures come in a variety of materials and shapes, however when I am sculpting heads or busts I tend to use newspaper & tape. To create such armature, all you need to do is: tear off a piece of paper, scrunch it into a ball, keep adding pieces round it until you have the desired size and secure this with a form of tape, here I have used parcel tape.
Step 2: Sculpture
Once you have your armature, you can start sculpting. I mostly use oil based clay for small-medium sized sculptures, like this one, but if you prefer an alternative clay then feel free to use this. The clay I am sculpting with is ‘Chavant Plastaline’; this is a great clay to use because it is soft, easy to work with and doesn’t need warming in an oven.
I always use reference pictures as a guide to help when sculpting; having images of the subject from different angles and with different expressions will help immensely.
To begin this piece, I took small pieces of clay to build up the basic structure of the monkey’s face. I roughly added clay to the armature, using the reference pictures as a guideline. i used marbles in place of eyes for this sculpture as they were the perfect size and are nice & smooth, this helps create that glossy finish eyes naturally have when casting.
Step 3: Refining Your Sculpture
Once I had the general shapes mapped out, I began using my tools to refine these shapes and give the face more definition.
Tip - I find it helpful leaving your sculpture for a while and then returning with fresh eyes, so that you can see more clearly the areas that need changing or building up.
Once I was happy with the shape and expression, I started adding texture; I have a couple of tools that are extremely helpful when texturing human or animal skin. The first is this ball point tool, this tool is great for creating pore textures such as this.
Using this tool directly onto your clay will result in quite harsh indents. To soften the texture, so that it appears more realistic, you can use a piece of plastic as a barrier between your clay and tool. Using this technique will ensure your pore textures are much more refined.
Another tool I like to use for skin textures is this rake tool, which is great for creating fine wrinkles in the skin. I adopt the same tip with the plastic to avoid harsh lines.
Once I was happy with my textures, I took a small, soft brush, dipped in white spirit, and brushed over the whole of the sculpture. The white spirit breaks down the clay and smoothes, tying everything together. A different method to smooth clay is by warming it with a heat gun, melting the clay slightly. Be sure not to hold the heat gun over the clay for too long, because you only want to melt the top layer and not morph the shape of your sculpture.
Step 4: Prep for Moulding
To begin my moulding process, I built a wall using water-based clay separating the two halves of the sculpture. As I knew I was moulding this to create a candle I had to be very precise as to where the two parts of the mould slot together, because this would be where my wick would sit. The clay wall went through the centre of the head and down the highest points of the ears; this is so that I would not encounter any undercuts when de-moulding.
I then coated my sculpture in release spray; this is imperative as some materials can stick to the silicone if not released and damage the mould. Here I used ultra 4 parfilm but a cheaper, more available alternative would be to melt petroleum jelly onto your sculpt. If you do use this; be aware that if the petroleum isn’t melted properly it may be too thick, resulting in some of the detail being lost. I gave this sculpture 2 coats of release spray and waited 10 minutes in-between sprays to ensure the release was set.
as you can see in the image i have used a large ball point tool to create circular indents in the wall, these dents when filled with silicone will act as 'keys' resulting in the 2 halves of your mould slotting perfectly together.
Step 5: Moulding
Next, I began adding my silicone layer by layer. The silicone i am using is called 'Ps 28' this is a condensation cure silicone, it is a great one to use becauce of its flexiblity and its quick cure time. The first layer of silicone needs to be runny to catch all of the details in your sculpture. The next layer can be thicker and should be applied to the sculpture when the first layer of silicone is starting to set (still a bit tacky) so that it creates a strong bond. To thicken silicone, I used a product called ‘Thixo'; a few drops of this will enable you to apply a bulk layer of silicone, without worrying about it dripping off of the sculpture.
Step 6: Cleaning Up Your Mould
After my silicone had completely cured, I made a strong plaster jacket for the mould. A plaster layer is needed because the silicone itself is extremely flexible and would not hold the shape without some kind of support. I mixed the plaster with water until it was the consistency of clotted cream, then I smoothed this over the silicone. I repeated this on the opposite side (using release spray on the silicone so it did not bond to itself) and waited for it to cure.
Prior to casting my wax, I de-moulded my original sculpt and cleaned up the little pieces of clay that were trapped in my mould. I placed my wick in between the two parts of the mould and secured the mould shut with bungee cords. To keep the wick secure I used a piece of string to tie around the base and then taped this to the mould.
Step 7: Making Your Candle
To cast in wax, I heated 500g soy wax in a double boiler until it reached a temperature of 180°F, i then added my fragrance to the melted wax and poured this into the mould. the fragrance is optional but if you want your candle to smell lovely then i would reccomend!
Any essential oils will work for this, all you need to do is mix in 10% oils - wax. For example, my monkey is 500g wax so i mixed in 50g oil.
The final stage of the process is to de-mould your beautiful candle and clean up any seamlines that may have formed. this size candle will take on average about 4 hours to fully cure before you can de-mould it, do not take the candle out of the mould prematurely as the wax will be too soft and you may damaged it. I hope you have enjoyed this step by step & i would love to see the candles you produce!
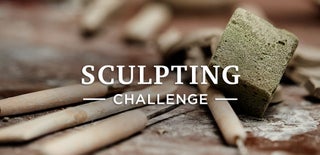
Runner Up in the
Sculpting Challenge