Introduction: Moving White Phoenix With 3D Printed Parts
I've been working on making a mechanical bird model for a long time - complete with a wide range of fully controllable wing, tail, and head movements. I love how this project combines design skills, engineering skills, AND artistic skills into one magnificent bird!
In this Instructable, I will walk you through how to make your very own moving bird. I will present the mechanical & decoration details as an optional step: this way, you can customize the bird to your liking! Be creative!
Supplies
Structure Materials
- PLA filament
- M3 Nylon Screw Nut Assortment.
- Springs: Ten -Comp. 9/32”x1/2” Ext. 13/64” *13/16” for neck; four-Comp 3/8”x5/8”, Ext. 5/16”x1-1/8” for wings and tail. These do not have to be exact as long as the extended length fits. You can also consider using rubber bands, but springs worked better for me.
- String
- 4mm (outside) - 3mm (inside) plastic tubing
- Beads or similar spacers 5mm in height.
- Toothpick (1) or thin metal rod
- Transparent mini-rubber bands (here we used ones from an old Rainbow Loom set).
Decoration Materials (optional)
- (optional) White Iron-On Non-Woven Fusible Interfacing for feathers
- (optional) Velcro dots
- (optional) thread and needle
- (optional) Craft pipe cleaners for head feathers
- (optional) Black beads for eyes
- (optional) 28-gauge steel wire for feature structure
Tools
- Creality Ender-3 Pro 3d printer
- Sewing needle (optional, to help you thread strings)
Step 1: Wings
As you can see, we went through several iterations until we finalized the wing design. Lacking a proper mechanical engineering background, I probably took more wrong turns than needed, but it was still an exciting process with a lot of trial and error.
The design uses rotating wheels to move a system of interconnected beams (kind of like Lego Technic pieces, if you're familiar with those!), expanding and retracting the structure. All the holes in each piece are circular to allow the pieces to freely rotate around their joints. We started with a 2D design on paper, then fixed cardboard cutouts on a box using pins. We gradually adjusted the size and shape of each piece so that the wing could retract completely and extend to its maximum length efficiently and smoothly.
When making 3D models for printing, we had to make some additional adjustments. For example, some pieces needed to have an additional dent around their holes for a screw head to sink in, which would allow connecting pieces to move smoothly. This flaw was harder to detect with the cardboard model, as the cardboard would bend and compress easily. Additionally, we prefer not to use supports during printing (the 3D printer will automatically print out supports if a part of the 3D object is suspended above open air), so we occasionally still needed padding when putting things together. To allow us to easily attach decorations, we later added a grid of holes to all our 3D printed flat plates as well.
Print out the attached STL files. Arrange the beams in number order (not by order of length). Assemble pieces 1-7, 9 and 10 with screws as shown in the images. Add a spacer when connecting 5 to 9. We will mount the wings to the main body later with pieces 8 and 11. You should be able to fold/unfold the wing by turning piece 10 (the round widget).
Repeat for the other wing.
Add springs as shown to set up the unfolded wing position.
Step 2: Wings-Body Assembly
Print out the attached STL files.
Mount the wing structures you created last step to piece 12 using pieces 8 and 11. You might need to adjust the positions of the piece 11 of each wing (the gears) so they interlock properly. This way, the wings will move in sync when turning just one of the gear pieces (birds don't flap one wing at a time when flying!). Note that you might need to place a cardboard circle between pieces 11 and 12 as padding, depending on the height of your screw head.
Next, attach control strings. Attach strings to control the wings' folding movements (one attached to each piece 10) as shown. The wing should naturally be in the "down" position. Add strings as shown (one attached to each piece 11) and adjust as needed so that both the wings lift when you pull either one of the strings. You will eventually tie the strings together to minimize tangling.
Step 3: Body
Print out the body and secure the wing structure onto the body.
We initially printed out 3 more body frame pieces to add feathers later (see last image). However, we turned out not needing them at all! We have still attached the file here just in case. If you want to use them, they can be secured to the main body where the "+"'s are located. You can print out multiple copies of the file and attach them to the body if you wish.
Attachments
Step 4: Neck
Print out two copies of the neck file. Each file should print out two neck pieces, giving us 4 pieces (labeled 14, 15, 16, and 17) in total, along with a mounting neck piece (piece 13).
Stick the plastic tube through the holes on top of each neck piece, with beads placed in between as spacers as shown.
There are 8 bigger holes on the outside of the neck (see second image) labeled with odd numbers and 8 corresponding holes closer to the center labeled with even numbers.
We used springs to return the shape of the neck to its base state after moving it, as well as hold the neck in place when we're not controlling it. Use springs to connect hole 1 on piece 14 to hole 1 on piece 15, and repeat with the hole 9s of pieces 14 and 15. Similarly, connect the hole 5s of pieces 15 and 16 and the hole 13s of pieces 15 and 16. Use this alternating pattern to connect all neck pieces with springs and ensure maximum flexibility.
(Tip: if you decide to add feathers later, especially if they're relatively heavy, you might want to consider using stronger springs to hold up the extra weight on the neck. We used rubber bands initially, and they worked fine until we added feathers and the neck started to dip.)
Thread 4 strings through the neck pieces, one through each of the holes 3, 7, 11, and 15. These strings will be used to control the movement of the neck, allowing us to move it up, down, left and right.
Add the mounting neck piece (piece 13) by pulling the plastic tube through it and then connecting it to the rest of the neck pieces with springs. The 4 strings should also go through the corresponding holes on the mounting neck piece (piece 13) as well (see image).
Pull the strings and plastic tube through piece 13 into the body. Make sure to do this before attaching piece 13 to the body! Mount piece 13 to the body piece by securing the 4 corners of piece 13 to the body piece with screws (this piece will not move).
Attachments
Step 5: Tail
Assemble pieces 14, 15, and 16 (printed out in Step 2) into the tail structure as shown. Stick them through the tail hole at the back of the bird back. Add pieces 17, 18, 19, and 20 as shown to support the tail.
Use springs to connect the body piece to the inside end of the tail (at pieces 15 and 16) as shown. This should expand the tail. Thread a string through each of pieces 15 and 16 as shown. When you pull the string, the tail should contract.
Step 6: Head
To make the head of the bird, I remixed this design: https://www.thingiverse.com/thing:4856305
Print out the attached file and remove the supports.
Secure the upper and lower pieces by bringing A to B and A' to B' (see image). Push a toothpick or thin metal rod through the hole and trim off any excess.
Pull the plastic tube going through the neck pieces through hole 7 on the head. Fold the tube into a U shape and push it back into the hole next to it (hole 8) to secure it. Position the head and attach it to the neck pieces by threading a chain of rubber bands up through hole 5 and down through hole 6 in a U shape.
Use rubber bands to connect holes 1 and 4 and holes 2 and 3 so that the beak stays in closed position.
Attachments
Step 7: Feet
I tried to make mechanical claws that could open and close. However, the feet were too small to control reliably. An interesting next step could be making the feet out of metal wire instead of 3D printing them to allow us to control it.
To get the model for the feet, I remixed this design: https://www.thingiverse.com/mjprice/designs. Print it out and screw it onto the bottom of the bird’s body. The bird should be able to balance on its feet.
Attachments
Step 8: Feathers (optional)
Different kinds of birds have different body shapes and proportions. I didn't model any specific bird species in this design, so you have complete creative freedom with the feathers!
I decided to make a white phoenix. This Instructable is already pretty long, so I will just include a brief summary of the decoration process here. I can add a more detailed section to this Instructable if there's enough interest!
I used interfacing fabric, as its paperlike texture made it easy to cut and its cotton-like workability made it easy to shape using metal wires. It's also very lightweight!
- Tail: Cut long 2"-wide strips of varying lengths. Fold each strip lengthwise and cut out pieces to make the feathers look like feathers. Thread a thin wire through the middle of each strip and secure one end of the wire to the end of the tail.
- Wing: Cut metal wires into 90 lengths of 5 to 6 inches each. Cut out 2-3 small, round feathers and one long feather for each wire piece. (https://avianreport.com/bird-flight-tail-feathers/ might be helpful for a more realistic arrangement of wing feathers!)
- Neck: Cut out 5 circles of different diameters. Fold and cut out random triangles along the circumference (think "cartoon sun shape") to make a feather like effect. Cut a cross in the middle big enough for you to pull the head and neck through. Let each feather circle rest on a neck piece.
- Head: Weave pipe cleaners around the head to first form a frame and then create flexible decorative feathers on top of the head that are easier to shape. The downside of this method is that pipe cleaners are much heavier, and you may need to strengthen the springs controlling the neck.
- Body: Fit a sheet of interfacing fabric over the body. Pencil out the layout of the feathers on the fabric, then cut out and thread feathers onto it. Finally, secure the body feather piece with Velcro dots. We don't want to sew it in place permanently, as we may need to remove it to maintain the structure.
- Back: This part of the bird requires special attention because the strings and gears controlling the wings need to be able to move freely. Cut out a triangle of interfacing fabric, attach feathers, and position on the back with Velcro dots.
Step 9: Bird - Control & Beyond
We have introduced several control strings through the prior steps that can manipulate the bird's joints:
- 4 strings are used to move the neck up, down, left, and right. Trimming them to the same length and tying them all onto one 3D-printed plate allows you to smoothly control them with one hand.
- 2 strings are used to control wing expansion and contraction, one for each wing. We added beads of different colors at the end of each string to differentiate them.
- 1 string is used to control the flapping of the wings (remember, the gears ensure that both wings flap at the same time!).
- 1 string is used to control the tail's expansion and contraction.
If we were to make the bird again, we would make it bigger to allow us to control the beak and claw movements. The plastic tube was added mainly to help control the beak, but after we completed the head, we realized that there was almost no space to fit in any mechanisms to control the beak. A bigger bird may allow us to create claws that can actually grab objects as well.
As mentioned earlier, I would like to make the bird remotely controllable, but have not found the right motor yet. Most motors are either too weak to move the bird's joints or too big to fit into the bird without disrupting the decoration. The feathers, which add more weight and resistance, certainly aren't helping. Also, a constant, repeating movement would make the motion seem unrealistic, so I might need to fit an Arduino chip in there as well.
Another feature I want to add later is sound. If the bird can sing as well as open its mouth, that would enhance its realism greatly!
Thanks for sticking around to the end of this project, and I hope you enjoy it as much as I did! Feel free to comment with any suggestions!
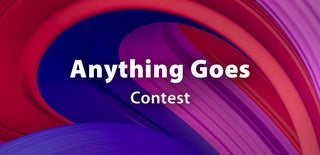
Runner Up in the
Anything Goes Contest