Introduction: Multifunction Sanding Bench
This Instructable describes the evolution and construction of a portable, multi-functional shop bench for my garage/woodshop. When I'm not using it, my shop takes up half the garage while my wife's car takes the other half. With the exception of my main workbench, each of my shop tools and appliances is on rollers. When I'm not using them, they are tightly packed into my half of the garage, jigsaw style. There's not a lot of room left, so that was the first constraint I had to deal with--I wanted to make something that would do as many different tasks as possible and still fit in the available space.
The second thing I wanted to accomplish was to use as many of the old materials I had laying around as possible, and minimize buying new materials. I had lots of off-cuts of plywood, two by fours, two by sixes, and four by fours. One of my bad habits is cruising estate sales, where I can often pick up wood and hardware quite reasonably. One piece of hardware I definitely wanted to incorporate was a huge Craftsman woodworking vise that I bought a few years ago for about twenty bucks at an estate sale.
The third thing I wanted to accomplish was to make the table serve as a on-feed or off-feed table for my tablesaw, as needed.
The final thing I wanted to accomplish (and my primary motive) was improve my dust collection, particularly when sanding. My whole-shop dust collection consists of a shop-vac and a Rockler Dust-Right vortex separator that I move from tool to tool as needed. Using my orbital sander, the only dust collection I had was the cloth filter bag that came with the tool. These measures probably catch 95% of the dust produced, but it's that last 5% that's a problem. Dust settles everywhere.
To that end, I had been thinking about making a down-draft sanding table for a while, and one day I was at Lowe's and whaddaya know, there was a great pre-Christmas bargain on a 12 gallon Shop-Vac. I bought it and--if you know me you guessed it--here it sat for about a year, still in its box, just one more piece to move around in the garage.
Earlier this year I decided to get serious. I started scouring Instructables, YouTube, and various corners of the internet, and found posts with a number of valuable ideas. Some of those posts are listed below:
https://www.instructables.com/id/Build-a-Down-Draf...
https://www.instructables.com/id/Rolling-Workbench...
https://www.instructables.com/id/Downdraft-Table/
https://www.instructables.com/id/Workshop-Air-Filt...
The project grew from there. Unlike most of my projects, there was no fixed plan--I simply elected to adapt & overcome as I went. That approach resulted in a few retrenchments and one major about face, but I'm happy with the end product.
Supplies
TOOLS
table saw with standard blade and dado set
drill driver with various bits
hand-held router with various bits
sabre saw
block plane
pocket hole jig
hole saw set
clamps (always)
MATERIALS
4 x 4 pine lumber 2 10-ft lengths
2 x 6 pine lumber about 13 linear feet
2 x 4 framing lumber about 30 ft
1 5 x 5 ft sheet of 3/4" Baltic birch ply
various off-cuts of 3/4 inch, 1/2 inch, 1/4 inch, 1/8 inch ply, and 1/8 in melamine hardboard
various pieces of oak, pecan, and cherry hardwood used for edging, etc.
1/2 sheet styrofoam hardboard insulation (the blue stuff
various wood screws and bolts
1 20-in box fan
2 16 x 25 furnace filters
1 plastic storage box with moisture seal and clip-on lid.
1 Chinese-made dust vortex assembly
vacuum hose and various 2" PVC fittings
3 electrical boxes (one double) with covers, two double outlets, and one double switch.
15 ft 14 gauge 3 wire romex cable, wire nuts, wire stripper, etc.
one generic grounded power tool replacement cord
1 set 22" full extension drawer slides
1 set of heavy-duty (600 lb rated) workbench step-down casters.
2 16 in x 16 in metal pegboards (not ultimately used)
2 return air grill covers from the Habitat for Humanity ReStore
miscellaneous hinges, magnetic closures, and similar hardwate
wood glue
silicone caulk
sandpaper
Step 1: Design Considerations
This project involved a classic case of scope creep. The original idea was a down-draft table.
The first addition was an air cleaner. I knew that the dust settling everywhere around my shop was dropping out of the air, and the woodworking magazines I got were full of ads for these boxy air cleaners that hang from the ceiling and cost several hundred bucks. One of the ideas I saw several times during my research was a homemade version of an air cleaner using a fan and furnace filters. I knew that every three months or so we would dispose of two filters from our in-house HVAC, and they always looked like they had more life in them to me. To test it out, I bought a cheap box fan and just duct-taped a filter to it while I was using the shop, then left it running for a few hours afterwards. I was working with some cherry at the time, and the filters pretty quickly turned a reddish brown, which was all the evidence I needed. The bench was getting an air cleaner, too.
The third addition was the vise. That was kind of a "duh" moment, as it had been laying in the corner gathering spiders since I bought it four or five years ago.
Step 2: Framing the Bench Out
The first thing I had to decide was the size of the bench. One side of the interior would house the vacuum, and the other side would house the air cleaner assembly. The vacuum was in a shipping box 17 in square and about 29 in tall. The box fan was a little over 20 inches wide, 22 inches high with handle & control knob, and 5 or so inches thick. There had to be enough room overhead for the vise, and I didn't want the table taller than my table saw.
Because I planned to use the bench for some significant assembly work, I made the risers out of 4 x 4s, the top stretchers out of 2 x 6s, and the bottom frame out of 2 x 4s. That also took some room in the layout. In the end, I made the side stretchers 48 inches, and the end stretcher 26 inches. I only used a 1 x 6 on one end, and a piece of horizontal half inch ply set into dadoes on the other to accommodate the vise. The length of the legs was 34 inches, so that when the 1.5 inch top was fitted the table would be 35 1/2 inches, just a hair shorter than my table saw. To support the weight and the forces that the bench top was likely to see, I joined the three 2 x 6 stretchers to the legs using lap joints. Rather than locking casters mounted to the bottom of the legs, I used step-down casters, which mount on the side of each leg and allowed the table to rest directly on its 4 x 4 legs when retracted.
Step 3: The Air Cleaner Box and Vacuum Caddy
Once the outer framework was done, I installed the floor for the air cleaner assembly and built a slot sub-assembly to hold two filters, one behind the other, and a box from 1/4 inch plywood to direct all the air pulled in by the fan through the filters. I also built a base for the vacuum on some heavy duty full extension drawer pulls so that I could pull the vacuum canister outside the bench to empty it, and I routed a circular groove in the drawer so the canister would sit securely on the shelf and not slide around as the bench was moved and the shelf pulled out. I wanted all these interior parts to be strong, but because all this work would be covered, I didn't worry at all about whether it would be pretty (and it definitely wasn't).
Step 4: Downdraft Table: False Steps
Next, I turned to the downdraft assembly. My original idea was to make a shallow, 16 x 32 x 4 in downdraft table and inset it into the tabletop from below, where it would be tucked up inside the 2 x 6 stretchers. The size was determined by the size of the two 16 inch-square metal pegboards I planned to use as a top.They were sturdy and seemingly perfect for it.
I framed the downdraft assembly with trimmed 2 x 4s and build a shallow series of ramps out of melamine hardboard that funneled down to an opening at one side. I reinforced the back side with triangular struts to keep the thin hardboard stable under vacuum, and I epoxied one of the vacuum attachments in at the outlet to collect the sanding dust.
It came out pretty much as I intended. Thank goodness I decided to try it before I cut the hole in the bench top, though, because when I tried it, it didn't work. At all. The vacuum simply didn't pull enough air to draw down the dust across the span of the table. Not even close.
My first impulse was to try to salvage my assembly. I blocked the initial air intake off, drilled a 2 1/2 inch port in the wall above it, and tried it again with my larger shop vac. It wasn't any better. Not only was there not enough air, but the melamine that I used to minimize friction seemed to develop a static charge that actually held onto the sanding dust. Nothing to do but hit the internet again--should I make the table 16 x 16, and use only one of the metal grids? That's when I found this resource:
https://billpentz.com/woodworking/cyclone/downdraf...
He explained what my problem was. Put simply, there was no way that piddly shop vac was going to do what I was asking it to do. I would need something moving a lot more air at a higher velocity, and I didn't have it.
Back to the drawing board...
Step 5: Plan B
Rather than abandon this part of the project, or build something that didn't really work, I decided to re-envision it. I would make a table with a much smaller and deeper trap, and use a removable open grid to support projects during sanding. That way, I could simply vacuum it out whenever I needed to.
I built a trapezoidal box about a foot deep and 9 x 13 inches at the top, designed to avoid other components inside the cabinet. I ran a length of PVC into the box to provide an interior vacuum source. I didn't think it would be particularly effective, but hoped it might pull in some of the finer dust. In the revised plan, I would split the vacuum line, attaching the other half to the orbital sander itself. Several sources I looked at touted this as the most effective way to catch dust while sanding with an orbital sander, anyway.
For a sanding surface I built an open framework grid of cherry laths, 1/4 inch wide by an inch or so deep. The grid was on 1 in centers, so roughly 56% (9/16th) of the grid was open space that would allow shavings and dust to fall through, while still being sturdy enough to support quite a bit of weight. I tried a grid with eighth inch laths first, but it didn't seem robust enough.
I wired the bench at this stage, too. The power came into the box so that it first arrived at an unswitched duplex outlet, then traveled on two hot wires to the duplex switch, and then to a second outlet. By removing the jumpers on the switch and second outlet, I made it so each plug jack was controlled by a separate switch. Therefore, all I had to do was plug in the shop vacuum and the box fan, and each could be independently controlled with its own switch.
Step 6: Adding the Top
Now that I had the grid located, I cut the 5 x 5 ft piece of 3/4 inch plywood I would be using for the top in half, marked the location of the sanding grid on the half that would serve as the benchtop, and cut the hole for it out with a sabre saw. Because the sabre saw did not really produce a clean edge, I cut it a little small and used a router with a straight-edge guide and an edging bit to clean up the margin until the grid fit.
I then used that as a template to cut a slightly smaller hole in the second half of the plywood sheet, then glued the two tops together to make a top 1.5 inches thick.
The next day, I cut dados around the edge of the grid so it would sit flush with the tabletop, and made a second, solid insert using the piece I had cut out previously and a little hardwood edging. Both inserts simply drop into the hole, so swapping them out is easy.
To complete the top, I trimmed the edge with the router and edging bit, attached the vise, drilled two rows of dog holes with a 3/4 inch forstner bit, affixed hardwood edging, and attached it to the bench using countersunk screws covered with plugs. I'm not really worried about wood movement because the top is plywood, but there is a devil sitting on my shoulder yelling that the frame isn't plywood, and I'm going to be sorry. I hope I don't regret that decision.
The top is slightly larger than 30 x 60 in (with the edging) and I attached it so the end with the vice sits flush with the cabinet. That means it overhangs the other end of the bench by nearly a foot. It's not over empty space, though, because that's where the vortex unit is mounted.
Step 7: Vortex Unit
A vortex separator is a device that sits between the vacuum inlet (the end of the hose) and the dust container in the vacuum body. It diverts flow in such a way that most of the material sucked up by the vacuum swirls around for a while (in a vortex, duh), then drops into an underlying bin. That way, most dust is removed from the air stream before it reaches the vacuum unit, where it can clog the filter and shorten the life of the motor. Large dust control units usually have a vortex built in, but in the shop-vac world it's an accessory that you buy separately. My primary shop-vac has a vortex bin that does wonders for cutting down on shop vac filter drama, so I wasn't about to make this bench without one. However, I was also feeling cheap, so I ordered a Chinese version off of Amazon instead of springing for an American one like the Oneida Dust Deputy, which costs roughly three times as much. The thing I got works fine, but the fittings are all an odd size and it required a lot of machinations to get everything hooked up right. If I had to do it over, I'd go with an American unit.
Instead of using a plastic bucket and lid for a dust receptacle, I got a clear plastic storage bin with secure clips and a foam seal from a big box store, and mounted the vortex on it. That way, I can see when it starts to fill up. I built a braced shelving unit out of 2 x 4s to hold the whole thing, and attached it to the bench with pocket screws and glue. The bin simply sits in a pocket on the shelf, and is quite secure.
Step 8: Finishing Up
With that done, all that was left was putting a skin around it and finishing it up.
In the area beneath the vise, I used some 3/4 inch walnut veneer plywood to make a door and a fixed panel. The panel is affixed with screws but no glue; if I ever need to replace the box fan, that will be my route in. I used the same material to craft double doors over the vacuum access. The rest of the body was Frankenstein'd together with 1/8 inch and 1/4 inch plywood pieces from a variety of sources. I then lined the walls around the vacuum with some styrofoam hardboard insulation to cut down the vacuum noise a bit. There was a hollow next to the vice, so I made an inset holder for bench dogs, and I attached oak jaws to the vice and drilled some dog holes in that.
Step 9: The Completed Unit
After a quick sanding, I finished the sides with some Danish Oil I had (mahogany, which looked great on the walnut ply, but made the pine pink), then attached the return air vents and hooked up the vortex unit. I attached the doors and some hardware to wrap the cord around, treated the top with a couple of coats of wiping poly, and it was done. Ready for the next project!
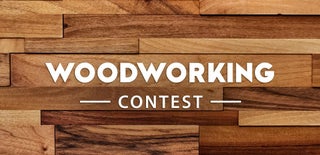
Participated in the
Woodworking Contest