Introduction: Music Bag
The first bag I ever made was a replica of the PRIMULA Briefcase from ortus leather. That was 5 years ago and now I'm going to make another. My skills have increased since then so lets hope the result reflects that.
Step 1: The Leather
The leather used was normal vegetable tanned shoulder. The thickness of the main part was 1,4-1,6mm. The lining was 1,0-1,2mm. For the handle I used a small piece of 3mm shoulder.
After getting the leather the next step was to determinate where to place the pieces. As leather is never perfect you want to avoid any major defects and try to stay clear of any imperfections - but not at all costs. Sometimes the design of the piece you are making allows you to hide some of the imperfections and if that means that you are able to make better use of the remaining leather that is the option I choose.
After dyeing I put a sheet of MDF on top of it to prevent it from curling while drying. On top of the MDF I put the gusset and handle and another piece of wood.
After the leather had dried the color was lighter than what I aimed for. I therefore dyed it again but this time I applied the dye using a rack. The leather was still not dark enough so I choose to add a bit more dye to the mixture so instead of a 1:1 ratio I tried a 1,5:1 (dye:alcohol). I have had this problem every time I dye big pieces of leather. When I dye small samples the color is darker than when I dye big pieces with the same dye. The problem might be that the big piece does not get enough dye but that is kind of ruled out when you dip dye. Maybe the color actually is the same but it just appear lighter on a big piece.
I have later used this method to dye thicker pieces of leather with catastrophic results. It came out very uneven and very stiff. Exactly what went wrong I don't know but as a result I now only buy predyed leather.
Step 2: The Gusset
You can find pictures on Ortus's page showing pictures of the different parts of the bag. One interesting feature is how they chose to make the gusset. To help shape it they cut slits and sew it back together. I tried to mimic this method but using thicker leather than they did I had to change approach. Also I don't think the slits suits the otherwise clean look of the bag.I came up with a rather clever "origami" solution but wasn't really satisfied with the result. I knew from my first bag that it was possible to make the gusset without doing anything to it besides cutting it to shape but I did not like how flat it looked. Instead I wetformed it over a rounded piece of wood and got the result I wanted.
I first cut the gusset and then the lining. Its both made from the same piece of leather but one is dyed. The lining was cut 2-3mm oversize before the edges was skived. I did not skive the top edge as I want the edge to be as thick as possible to make it easier to burnish. Also the gusset was cut too long as I did not know the final length. I found that by loosely putting together the gusset and the main piece with clips. I could the Burnish the top edge and sew along the top.
Step 3: The Handle
The handle is pretty straight forward but has a rivet going through it which is new for me. I guess they did it to secure a metal strip to help keeping the shape of the bag. This is not necessary at all when using thick enough leather but it does look nice.In order to get the shape of the ends right I had to sew it together before shaping it. Also the rivets and washer had to be placed while the handle was wet to help press it into the leather.I used a bolt and a nut to push the washer into the handle while it was drying.
Finding the right size of cord to give the handle a round profile was not that easy. Most ropes I found was either too small or too big. I tried to order some leather cord on ebay but the was also too small. I then tried to make my own which actually worked out pretty good but I encountered another problem.The width of the leather used for the handle is 46mm. I got this by measuring a picture of the original. The diameter of the handle is 16-17 mm which is really hard to archive with a 46mm wide piece of leather so the "handle" part of the handle must be wider. I made mine 48mm wide tapering down to 46 mm at the end. Another thing that is difficult is getting the profile of the handle as circular as possible. With thin leather its not that hard but I use 3mm leather. What I came up with is something rather unsual but it seems to work. I stretch a piece of 10 mm elastic cord so that the diameter goes down to around 8 mm. After that it is much easier to sew the handle around it.
Step 4: The Pocket
Finding the right dimensions for the pocket was not that easy but I think I got it right in the end. To make it a bit easier to take the laptop out I cut out a piece of the top edge. I marked it using a wingdivider:
Very happy how clean it turned out. I cut it with the round knife using the "rocking" technique
Placing the pocket on the liner was also not that easy. I made a few wrong holes but nobody will ever notice unless somebody tells them.From my initial tests I knew the distance between the two vertical stitch lines and the distance from these to the horisontal stitch line.
I then gave the lining a treatment of leather conditioner I did not treat the pocket with conditioner at this point as it needed to be wet molded later
Sewing it on was a real pain in the ass. I started with the horisontal line which proved to be the worst one. If I could I would have attached a hook in the celling and use a string and clips to hold the leather upright. Unfortunately the celling is made of hard concrete and I don't have a rotary hammer which is needed. Instead I made this setup:
Step 5: The Lining
The lining leather is cut a bit oversize. I did this because I had to skive the edge of the lining and leaving a bit extra material helps you if you by accident skives too deep at the edge (as the edge will be trimmed off). Next time I will cut the lining to size and just take my time with the skiving to avoid mistakes.
When all the edges have been skived (the flap part of the lining should not be skived at its okay with a thicker edge here) The pocket was sewn on (see section about the pocket).
The stitch line really doesn't serve a purpose as the lining is glued in place. On the original bag the stitching goes through both layers of leather and I guess it helps keep the lining in place. I decided not to sew through the lining.
It will be glued on in 3 sections so that it follows the curves of the bag. If it was simply glued flat to the main part the lining would most likely wrinkle when bent. I used much more contact cement than I had thought and the smell in the workshop was not pleasant. Remember to open a window when working with contact cement! Or get a water based one.
Sometimes I wish I made wallets or other flat items. It would be much easier to sew. The top edge was difficult because I couldn't hold it in the clamp and the flap piece was always in the way. To make it a little easier I clamped a piece of wood to the table which helped alot.
Step 6: Sew Gusset
Sewing the gusset in place went without any issues. I started by gluing it in place with contact cement and the proceeded to make the holes with the awl. After that it was just a matter of sewing.
Step 7: Straps and Brass Bar
The straps are made from two pieces of the main leather 1,5mm glued together. At the end a piece of 3 mm leather is glued and cut to size.
After cutting the access of I used the belt sander to align the edges. The belt sander is a new addition to my tool collection and it is proving to be very useful. To get a smooth and consistent curve I press the piece against the rest while turning it.
It is much easier to sew then length of the strap before sewing it on the bag.
When it is sew on you make a loop at the end to hold the music bar. It would be easier to have sewn this loop before sewing it on the bag but that requires that you know the exact length of the entire strap which is difficult.
I have made a few brass bars for other types of music bags but I no longer have access to a lathe so I had to improvise. I will be using bigger balls and leave out the slot that helps keep the strap in place. I however still have to make a M6 thread on an 8mm rod so I'm really missing the lathe.Instead I will use a drill and a file and hope it works out.
Step 8: The Pattern and Tool
I will not go into details about what tools should be used. Basically this bag can be made with very basic leather working tool. For the brass bar you do need a die tap to cut the thread but that can be bought in most hardware stores very cheap. As you will be cutting brass you dont need good quality tools as brass is very soft and easy to cut. You dont even need oil.
The patters pretty much explains itself. Please double check all measurements before you go ahead and cut the leather.
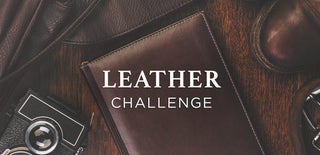
First Prize in the
Leather Challenge