Introduction: Ninja Turtle Onesie {Made It at TechShop}
It seems to me as the years slip away I find more and more reasons to help friends and family. The latest of my endeavors is one that I will cherish for many years to come because the Ninja Turtles hold a very special place in the memories of my childhood. Recently many of my immediate friends and family have all decided to add to the size of their families and they are all due around the same time. I decided that I was going to create special clothing that would replace the “cutest” item I could find at my local big box store.
Our friends Eric and Stephanie are up first in the onesie lineup and they decided to go with a Apple Green onesie and when we started throwing around ideas the Ninja Turtles came up pretty quickly! I, being the nerd I am, already had a similar t-shirt and decided just to take a picture of my tee and import it into Illustrator where I could then work my magic.
Step 1: Programs, Tools, and Materials
Everything used, featured, or pictured in this instructable is available at most Techshop locations
Programs used-
=Adobe Illustrator CS5 (Click here for CC)
=FlexiPrint MH software
Tools used-
=MH vinyl cutter
=Exacto knife
=Heat press (Set at 350F degrees)
Materials used-
=Apple Green Onesie
Step 2: Creating Your Artwork
About an hour later I had successfully traced out the design and separated the layers by color (Daddy Eric watched most of this process and it seemed to me that this must have been the dullest part of the entire project). After separating the White, Black, and Red I uploaded them to dropbox and packed up to head over to the vinyl cutting station (normally people would just use a USB stick but I like to work within dropbox so all of my files are always up to date and I never worry about losing ‘everything’)
This is when the real magic happens! On this separate workstation, I downloaded the file I needed and proceeded to copy+paste them into the proprietary vinyl cutting software and set up the cutter itself (20in/sec @ 180g). Since there was a lot of negative space within the design I decided to flip the mouth on the black layer as well as tuck the tongue closer to the red bandana to make the most of my raw materials. The White eyes were just cut on a corner of my bulk vinyl.
I had built my design so that the first layer was white, the second red, and the topmost layer would be black so it was imperative that I overlapped some of the vinyl slightly to achieve a seamless transition between colors. At the start of the project Eric didn’t quite see the method of my madness but at this point Eric understood how exactly we were going to build the design.
Step 3: Weeding and Starting the Layout
Once you have all your pieces cut you can begin the weeding process! This step is by far my least favorite pastime… If your settings were off by even 10g it can make this step VERY challenging to say the least. For those that don’t know what weeding is, it’s basically a separation process where you take everything you don’t want on your shirt off of the sticky clear transfer material and leave “your design” behind and in the correct location (think of removing the inner dot in the target logo and then trying to place it back in the exact center, not so easy!). I must say that the key to this step going off without a hitch is making sure that all your prep work is on point and the test (yes, ALWAYS run a test on your vinyl and make adjustments accordingly before trying to cut a finished product) square came out the way you wanted it. If all didn’t go so well, take your time, use a sharp x-acto blade and pull your waste material off SLOWLY so that if anything starts to lift, your blade will be in hand to help out.
Next we moved onto layout and the most important thing to note here is we had a reference image on our phone to help us place the eyes and tongue in the appropriate place. We fully “built” the design before sticking our Apple green onesie into the heat press to make sure that we understood how, logistically, the design had to be layered (the virtual layout helped, but its always worth the time to do a quick physical layout). We decided that we could put all three colors into the first press as long as they were not over the top of another color.
Step 4: Continuing to Build Your Design
Just continue to follow your master plan and take your time lining up subsequent layers because after all, you have come all this way, it would be a shame to ruin your garment because of ⅛” spacing.The first picture shows all of the plastic protection in place upon second pressing and the second shows the result (This vinyl required that I "hot peel" rather than letting everything cool down to room temp). Even after you’ve placed your design down, double check right before you close the press. Make no mistake about it, this is what they call the point of no return!
I like to use a saying my father always used when I was a kid.
~“If you didn’t have the time to do it right the first time, what makes you think your going to have time to do it a second time?”
Step 5: Realizing the Awesomeness of Your First Custom Onesie!
In this step its more layout and double checking and the final 30 second press. Daddy Eric had the honor of putting the icing on the cake, the final layer of black that brought the entire design to life. We snapped one last layout picture before I took it over to the heat press and that’s when the final countdown began. The DING & pop of the press had Eric and I smiling from ear to ear because it was finally done. The finished product was a result of a little over 2 hours of prep work, 10 minutes of layout, and only 1:50 seconds of total press time.
Want to design and produce your own custom shirts? Head over to techshop.ws and find a Techshop near you!
If you'd like any of the files I used here just let me know in the comment section below. Likewise if you have any questions, comments, or concerns let me know down below and I'll be sure to get back to you ASAP. Thank you and if you like this instructable favorite it and consider sharing with your friends!
May the Journey bring you Peace
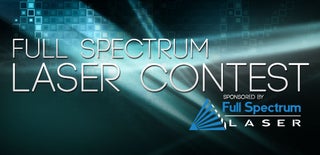
Participated in the
Full Spectrum Laser Contest