Introduction: Phone Camera Jig
Today I'll show you how to make this phone camera jig using Fusion 360. I had ZERO experience with Fusion 360 CAM prior to this project. Made some mistakes throughout but learned a lot. Whether you're new to CNC/CAM or eager to begin, I hope this "beginners to beginners" guide helps you!
Skills required:
-Basic modeling in Fusion 360
-Operation of your CNC machine
-Basic woodworking
Supplies
Equipment:
-CNC Router (Next Wave CNC Shark HD 510)
-Table Saw, Miter Saw, or any tool required to cut your wood stock
Supplies:
-Wood, preferably pine
-Sandpaper (optional)
You should model everything before you gather supplies.
Step 1: Modeling (Sketching)
First, we sketch our jig in Fusion 360. My jig needed to be at least 22" inches in height and 24" inches in length. The jig will have 2 legs, 2 bases, and 1 board.
Here are the dimensions in inches (Length x Width x Height):
Bases: 6" x 2" x 0.75"
Legs: 24" x 5" x 0.75"
Board: 26" x 4.5" x 0.75"
Let's start sketching:
1) Create Sketch > Choose the ground plane
2) Sketch the board. 26" x 4.5" inches
3) Sketch the bases, left and right. 6" x 2" inches
4) Sketch a cutout in the bases to accommodate the legs. Since the legs are 5" inches in width and 3/4" inches in height, I will sketch a cutout with those dimensions.
5) Make sure everything is symmetrical and constrained!
Step 2: Modeling (Extruding)
Now that our "base" sketch is finished, we can extrude:
1) The bases will be extruded 3/4" inches as per the dimensions.
2) The legs will be extruded 24" inches as per the dimensions.
3) The board will be extruded 0.75" inches as per the dimensions. I added an offset of 22.25" inches above the ground.
Step 3: Modeling (sketching Cutouts)
Now we sketch the cutouts for both the camera hole and the slots for the board.
Dimensions for the cutouts in inches (L x W):
Camera cutout: 2.5" x 3.5"
Board slot cutouts: 0.75" x 4.5"
I put the camera cutout 1.25" inches away from the center. The board slots are spaced 0.25" inches apart. The highest slot is 1" inch from the top of the leg. Add as many board slots as you need.
1) Right-click on the plane you will be making cutout(s) > Create sketch
2) Sketch out cutouts
3) Extrude the cutouts, making sure to cut
Step 4: First Time CAM Setup
Personally, I found the CAM part very overwhelming for me. Take it slow. Refer to several tutorials on YouTube to get this set up. Here is one I recommend: https://www.youtube.com/watch?v=Do_C_NLH5sw
Our cutouts are modeled. It's time to use CAM to automate toolpaths for our CNC machines. Before we continue, we need to tell Fusion 360 what tools, machines, and posts we will use.
I recommend enabling your cloud library.
1) Click on your profile photo at the very top right of Fusion 360 > Preferences
2) General > Manufacture > Enable Cloud Libraries: Checked > Apply & OK
Now you will have the same tools, machines, and posts on every computer running Fusion 360 with your account.
Let's set up our tool.
1) Change Workspace > Manufacturing > Milling > Manage > Tool Library
2) Cloud > Right Click > New library > Name this library whatever you want, I named mine "Tools"
3) Click on your new library > Click the blue plus sign: New tool
At this point, you will have to determine what your tools are and its parameters. This is something you will have to find or make on your own. For this project, I will be using a flat-end mill.
4) When you are finished, click "Accept"
Now let's set up our machine.
1) Manage > Machine Library
2) My machines > Cloud
3) Click the grey plus sign: Create new
From here you will have to determine your machine's parameters. This is something you will have to find or make on your own.
4) Click "OK" when you're done
Now let's set up our post.
1) Manage > Post Library
2) My posts > Cloud
3) Import > Import your machine's post files. This is something you will have to find or make on your own.
Now that everything is set up, we can make our toolpaths.
Step 5: Setup
A setup is one operation. Each part will need to have its own setup.
1) Milling > Setup > New Setup
2) Stock > Mode > Change accordingly, I used "From solid" and clicked on the part I was setting up
3) Setup > Select your model, stock point, and orientation
The model is the part you're cutting. The stock point is the (0,0) you will set on your machine. The orientation: telling Fusion 360 what you want the X, Y, and Z axis to be according to your machine. For some setups, I needed to adjust the orientation.
4) Click "OK" when you're done
Repeat this for every part.
Step 6: Toolpaths
Now that our parts are set up, we can automate toolpaths for each setup. I used a 2D Contour for all my toolpaths.
1) 2D > 2D Contour
2) Set your tool
3) Click on the 2nd tab > Contour selection > Click the bottom of the cutout(s)
4) 3rd tab > Set your heights accordingly. You can leave most at default but I would change the "Bottom Height" > From "Selection" > Click the bottom face > Set offset at 0" or very slightly below 0"
5) 4th tab > Multiple Depths: Checked > Maximum Roughing Stepdown: the maximum depth your tool can cut for each pass. My tool is 1/4" so my maximum depth is 1/4" for each pass.
6) 5th tab > Ramp: checked (this can be left at default)
7) Click "OK" when you're done
Repeat for other setups. Remember that you can click on multiple cutouts for each setup.
Step 7: Post Process
Now that our toolpaths are generated, we can "export" them into code that our CNC machine can read.
1) Browser (where your parts and toolpaths are) > Right click on a 2D Contour > Post Process
2) Use machine configuration: Checked > Choose your machine
3) Choose your post
4) Name your program as you wish
5) Choose your output folder
6) If everything looks good, click "Post"
7) Repeat the steps for each setup
Triple-check each code to make sure everything looks good. Prepare the codes for machining (speeds and feeds). Remember to keep in mind the stock point and orientation for each setup before machining.
Step 8: Gather Materials
Now that the codes are ready, it's time to cut and gather our materials.
-Pine
Dimensions in inches (L x W x H):
Bases: 6" x 2" x 0.75"
Legs: 24" x 5" x 0.75"
Board: 26" x 4.5" x 0.75"
Note: exact dimensions will have very tight tolerances. I trimmed about 1/8" extra on some pieces after assembly.
Step 9: Cut Your Material
Now it's time to set up the material to cut! Each machine is different. Make sure you know how to operate your CNC machine. For my machine, I used clamps to hold down my material and set my (0,0) at my stock point. I also made sure that my orientation was correct. Once everything is set up, I put my code in and let the machine do its job.
Step 10: Assemble
Once everything is cut, assemble everything. If tolerances are too tight, you might need to sand/trim some material. I found that I needed to trim the legs and board so they could fit. I was also very tight on time and could not cut every single slot.
Now it's finished! Perfect birdseye view for a phone's camera. Hopefully you found this useful.
Backstory: My manufacturing teacher needed me to create a jig to hold his phone for table photos/videos. I said I would do it. Then I received my Finals assignment: make a CNC instructable. Figured I could kill two birds with one stone. Not the most practical solution, but definitely a learning experience for me as this was my first time using Fusion 360 for CNC!
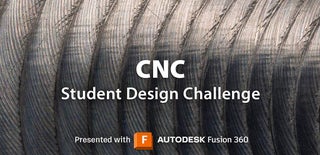
Participated in the
CNC Student Design Challenge