Introduction: Pneumatic Air Graver From Bolt
This instructable is about making an air graver. In the past, I made the same tool but the working principle is completely different. That graver uses suction and compression while the one I am telling in this Instructables only uses compression, which means that the regular air compressor works without any hassle. Now one thing that is similar in both cases is that I am using a 20 mm bolt for the build. I do a lot of stainless steel work and I have a few of these bolts available from one of the repairs I didn't do a few years ago. This build requires quite a lot of precision and doing this without a lathe is a bit more difficult task to do but if you ask me it's definitely doable and the only thing you need is patience. To be honest the tools I have are not the best in their line and need to be replaced. But if you have a lathe then definitely this build is much easier to do without any issue. Although in a few areas you definitely need to improvise to achieve a certain level of precision. This particular tool is mostly made out of bolts but there are a few elements for which I need to use the punch which is made out of HSS. If you have some suggestions for me then definitely leave them down in the description section.
Attachments
Supplies
Material Used
- M20 stainless steel bolt
- M8 Allen head bolt
- M10 brass rod
- M10 Punching Die
- Grub screw M4X6 mm.
Tools Used
- Angle Grinder
- Drill Press
- Drill Machine
- 11.7 mm Drill bit
- Sanding Pad
- 20 mm core drill
- 4,5 mm thread Tap with.5 mm pitch
- 1/2" unf thread tap male and female die
- Tap Handle
Although to ease the work you can easily do the entire work with lathe and surely its hardly one day work, so how fast you can make this totally depends upon what resources you have.
Step 1: Drilling Hole to Construct Barrel.
The first thing to do in this is to drill the hole. There are two different hole diameters required for this tool. For the main barrel, the hole required is 10 mm and for the adjustment nut, the hole required is 11.7 mm for ½" UNF thread. To get a good start I first made both the ends flat so that the drill has a good start. Since we need to grind down the barrel from outside that's why a little bit of wobbling can be done easily. After that, I mark the center point and then center punch for the drilling operations. Started the drill with a 5mm drill and then reached up to 10 mm. Stainless is a work-hardened material and the one I have seems to be a bit harder that's why I decided to anneal it and along with this I also annealed the HSS blank because later on, I am going to make a piston with this piece and also the graver holder. To slowly cools down the material I wrap this inside the glass wool and it really worked. After 4 hrs later the bolt is ready to process. Once this is done I drill down the hole and prepare it to cut.
Step 2: Cutting to Required Length
After drilling work is completed it's time to cut down the piece to the required section. The first cut I made is for the adjustment nut and this will help to adjust the stroke length between the graver holder and the piston. If the striking distance is more the impact will be High and this will generally be used for the stainless steel engravings. The final required length for the nut is 14 mm. The next cut piece is used for making the graver holder. If I had a bigger chuck in my drill press then I definitely prefer to turn the entire piece from a single piece. The length required is 8mm. The last piece cut out is 47 mm. And then the bolt head which is left in the end which is going to be used for making the butt cap.
Step 3: Setting Up the Drill and Start Reducing the Size
Once I cut the piece to the required dimensions I started turning them closest to 16 mm and I first clamped them in the bolt and then clamped the bolt in the drill chuck. Once I started rotating the drill you can see the wobbling. Now I start the grinding process with various tools like an angle grinder, die grinder, and file. This is an extremely time-consuming process and once you remove the wobbliness then you need to constantly measure the size otherwise it's going to look ugly. I decided to use a fresh file so that I get the result a bit faster. During this process make sure that drill is rotating anticlockwise direction. Even after taking too much care, I am off with .1mm but I think it's good with such a Setup.
Step 4: Preparing for ½" UNF Thread
Once the final size of the barrel is achieved I started the work on the threads which is an extremely crucial process in this build. First of all, I apply the layout fluid and then spread it evenly onto the barrel then I marked the thread length which is 14mm on one side and 8 mm on the backside. I use the carbide scriber to just poke it into the barrel to get a deep scribe line which later on I can follow. Again with the help of an angle grinder, the die grinder and file achieve the final result. The diameter required for the ½ thread is 12.7 mm but I do not succeed in starting the initial thread cut that's why later on I need to reduce the dia to 12.4 mm. The same thing has been done for the backside also where 8mm threads are required. Once the size is ready I use a drill chuck to hold the job securely to its place and then tap the threads to both the ends. To prevent the material from squishing inward I used a copper tube having a diameter of 10mm and that's the only way to prevent the squishing of the material. Once it's done then I tap the nut portion also. For the female threads, I need to use all of the pairs because tapping stainless is a pretty hard job.
Step 5: Constructing the Recess Area
Once the threads have been done to close the nut assembly completely I need to remove some material where I am not able to cut the threads. This work is done with the help of a needle file. I kept on grinding until the nut covered all the threads completely. Then to make the surface look even I file down the entire surface. I also trim down the nut to the final length which is 13 mm.
Step 6: Drilling Breathing Hole and Air Inlet Hole
Once the final size of the barrel is achieved I mark a distance of 12mm from the front end where I need to mark the hole location for the breathing holes. There are a total of six holes that need to be drilled out and for that, I used nut sides to mark the location for the hole. From the front side, I marked a hole location having a distance of 21 mm and this needs to be tapped with M5 thread. For the tap, I used .5mm pitch threads so that they make a tight seal and also have more grip on the barrel.
Step 7: Stoper
Inside the barrel, there is a stopper piece needed to be fitted. The length of this piece is 5.7mm and the putter diameter is 10 mm. The inside hole has two different diameters one is 8mm and the other is 6mm. I use a piece of bolt held for this. I first trim it to the exact size which is 10 mm and then drill down 6mm through-hole and from thereafter drill 8 mm hole up to a depth of 3mm. Since I need a flat base to achieve that I use an end mill to construct a flat base. Once I separate it from the main portion I bring it to the final dimension which is 5.8mm. At first, I use heat to expand the barrel and then insert this spacer piece but later on it loses its position so I need to tig weld it.
Step 8: Constructing the Piston
For the piston, I chose a punching die and the die I used was 10 mm. First I mark the length required for the piston which is 29mm and this needs to be divided into two sections in which one stays 10 mm having a length of 12mm and the other one is 17mm having a dia 6mm. I already soften this blank so now it's easy to refine this. Again I used a die grinder and file to reduce it to the final dimension and then polish the surface with 320 sandpaper. Into this piston, there are two holes that need to be drilled and they are perpendicular to each other having diameter of 2.5 mm.
Step 9: Making the Elbow Fitting.
For the elbow fitting, I use the remaining portion of the bolt and turn it down to the required dimension and tap MY thread onto it. Then I drill a thorough hole inside it. Unfortunately, during this, I broke my tap. There is a connection piece that needs to be made and for that, I use this brass rod having 10 mm dia and drill down two holes one for the M5 thread and the other for the M4 thread. This piece O was able to make in the third attempt because the hole I drilled wasn't straight and also I am not happy with the position of the holes either.
Step 10: Graver Holder
Graver holder is a two-part construction. One portion is obtained from the M20 bolt and the other from the punching die. And both press-fitted in each other and turn them to the required length onto my drill. At the back of the holder, I made 2 groves for the O-ring to avoid air leakage, and at the front drilled a 3mm hole. To hold the graver to its place I use an M4 grub screw. On the back side, I need to make a flat spot onto which the piston is going to make strike. And also there is a locking pin that needs to installed which is going to prevent the turning of the graver holder during the work. During this process, I made a slot in the main barrel as well to see the alignment of the holder with the barrel. After making a cut with a grinder with a few strokes of file it's a perfect fit inside the barrel.
Step 11: Heat Treatment
Since the piston and holder are going to strike that's why I need to harden these pieces and they are already made with die so it's a doable process. After heating them red hot they are quenched in oil and after tempering they are ready for use
Step 12: Back Cap for the Graver
Once the barrel, graver holder, and adjustable nut are done it's time to do the work onto the back cap. For this, I use the bolt head. There are two of them and for one portion I drill drown hole with a hole saw and then use the core. I weld the core with the second head. Since there are few operations need to be done so I didn't cut all the way and after drilling and tapping the hole I finish the final cut and welded it with the other bolt head. Then I hold it into the tap because that's the only thing that is going to give me the right fit. With the help of a die grinder, angle grinder, and file I bring it to the final dimensions.
Step 13: Polishing
Once everything is prepared I polished all the pieces one by one. I didn't go with the mirror finish because I want some roughness so that tool didn't get a slip in the hands. On the adjustable nut, I made groves with file and diamond blade and finish it with a Scotch-Brite pad.
Step 14: Finally
After assembling all the components the tool is ready for use. There are few areas where I need to use glue to make a tight seal and also use thread tape to avoid air leakage. I am very happy with how this tool came out and pleased with the result. If you have some tips to improve it then definitely let me know in the comment section down below.
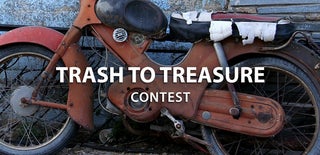
Participated in the
Trash to Treasure Contest