Introduction: Puppeteered Human Scale Spider Arms
This Instructable documents the journey to creation of a wearable rig that gives a performer human scale spider legs that they can control via puppeteering.
Every year a local non-profit group stages an elaborate Halloween production. I volunteer my services to craft props and set pieces for the show. This year they asked if I could help them realize a character that starts out looking human, but sprouts spider legs as it taunts its victims.
Challenge Accepted.
The Character was completed and currently part of this years Halloween shows.
This is the tale of how the creature came to be.
Shown here is a photo of the spider legs backpack after a quick base coat of black paint, and later as part of the performer's costume. Kudos to Sam, the performer pictured, for putting up with the design process, and the inevitable changes driven by scene changes and the laws of physics.
Supplies
Plywood - 1/2" for baseplate
More Plywood - 1/4" for arm segments
Lauan (very thin plywood) - Optional in place of some of the arm segments to reduce weight
2x4 - For mounting arms to baseplate
1/4x20 Bolts - Long for bolting arms to 2x4s. Short for connecting arm segments
Wingnuts and Locking Nuts - Wingnuts for prototype tuning. Locknuts for operating consistency.
Wood Screws - For attaching 2x4s and bookbag to baseplate
Parachute Cord - for puppeteering tendons
Bungee Cord - For spring loading limb tips
Screw Eyes - For Cord Routing
Bookbag - For wearing the rig
Paint - Personal Preference
Step 1: Initial Design and Prototyping
I envisioned an organic blend of Doc Oct, Iron Spider, and The Thing's morphing alien.
Early on I decided on a backpack device that would deploy four articulated limbs. One limb on each side of the performer's head, and one on each side between the waist and chest. A quick Lego Technics and Action Figure proof of concept was assembled (pictured). The show's directors gave the design idea a Green Light, and work began to scale up the concept.
One twist to this year's Halloween Nightmare Production, thanks to the pandemic, is that it would be performed as live action over video conference, featuring first person video footage as a character works their way through the storyline. This afforded some benefits of character design with respect to predictable viewing angles, and convenient off-camera reset and donning of the device.
The initial idea was for a group of four slowly self-deploying limbs, with additional tendon puppeteering after deployment. Cardboard and roughcut plywood prototypes of a single limb were constructed. Simplicity and silent operation are key to live performances. Configuring three spring loaded, folded limb segments so that each limb could be slowly deployed without striking the performer in the head or shoulders proved a tall order. Layering additional tendon articulation on top of that spring loaded design exceeded the design time available.
The design shifted to a less compactly folded version using 4-bar linkages to smoothly execute a coordinated deploy of the first two segments of each limb. Additional cardboard prototypes were created to gauge the scale of required pieces (pictured). The cardboard prototype pieces were then used as templates to cut out four sets of arm segments. Note that curved shapes help relay an organic rather than engineered feel.
The limbs protrude further behind the performer than the original design, but the mechanics of a 90 degree rotation deployment are much more manageable. The interlocked linkages provide precise control of the moving limbs to keep them clear of the performer's body. The increased side profile of the stowed legs is not a significant concern for the specific intended use. Camera angles can keep the mechanism out of view behind the performer's body.
Four pieces of 2x4 are screwed to the plywood backplate. Prototyping was done with a single screw for each block, to allow adjustment of arm angles during design refinement. The two linkage bars that make up the first segment of each arm are bolted to the 2x4s. Robust 1/4x20 carriage bolts were used to mount the linkage bars to the 2x4s. Wingnuts were used during design refinement to experiment with the proper amount of bolt tension for smooth deployment action. (pictured)
Step 2: Deployment, Puppeteering, and Making It Wearable
With the 4-bar linkage deployment mechanism in place, work turned toward a method for the desired cinematic slow reveal of the the limbs. A trigger release of bungee loaded guillotine speed scimitars was to be avoided. It would be too quick, too noisy, and too hazardous for the performer.
A plan for deploying the limbs as the performer rose from a chair was devised. Parachute cord affixed to a bar linkage of each leg would pass through guide eyelets and attach to the performers feet. As their own legs extended, the cord would actuate the linkages and cause the spider legs to extend.
It worked, after a fashion, but the design of the scene changed, as they often do. The performer would be required to walk around the scene wearing the spider legs. The foot tethered deployment became a liability, and a change was made to hand operated tendons that perform the same task.
The 3rd leg segments were added at this point, and additional cord tendons routed to provide the performer with control of the leg tip motion after deployment. The tips were bungee loaded so that their resting position was tucked in, and would only extend when the tendons were shortened. This keeps them out of the way during deployment.
Along the way one of the design changes was to make the lower legs protrude more forward and outward than the upper arms. This was done to increase their visibility and avoid entanglement in the performer's wardrobe. This design change was accomplished easily by lengthening the second segment of the lower legs, and by adjusting the angle that the bar linkages were attached to the 2x4s. Two new boards. Two new holes. Done. The new arm segments were fashioned out of a double layer of Lauan to reduce the weight of the rig.
The backplate with the attached legs is mounted onto the straps half of a sturdy bookbag. Screws with fender washers are driven through the bookbag and backplate and into the 2x4s. The backpack straps easily support the weight of the rig, and provide comfort for the performer. No poky bits provide for hours of relative comfort.
Step 3: Final Design Changes
Design tuning was done using wingnuts to tighten all the joints. This provides an easy means to adjust joint stiffness while searching for that sweet spot.Too loose, and the legs flop about and bind. Too tight, and the legs are too hard to deploy and the rig becomes poseable rather than puppet-ed.
Variations in bolt tension and wood on wood friction are a source of inconsistent stiffness for the 20 joints. I fashioned HDPE washers from a milk jug and installed them between wooden components at each of the 20 pivot points. (pictured) These washers provide more consistent stiffness at all pivot points. The wingnuts would loosen over time as the joints flexed. Once the design for smoothness of movement was tuned, all wingnuts were replaced by nuts with nylon insert that lock them in place. These locking nuts hold the joint stiffness constant across many deployments. Another option may be to use a hardware retention material such as LocTite. Note that joint stiffness will change over time with materials wear. It's best to keep some adjustabililty in the joint tensioning method used.
Step 4: Finishing Up
The entire mechanism received a coat of flat black paint to reduce its visual presence in the camera feed.
Camera tests confirmed the entire rig disappears into the dark background of the dimly lit Nightmare scene.
Contrasting color highlights were added to the edges of the spider legs, and as periodic stripes around the legs, to draw the eye to the desired parts of the design.
The paracord tendons were trimmed to the preferred lengths of the specific performer.
In the particular scene, the performer starts in a chair, without the leg rig. The rig is hidden behind the chair. The camera is on them as they deliver some lines. When the camera turns to the hapless victim, the spider character quietly stands and dons the leg rig before the camera returns to them.
A tug on a double cord deploys the legs for that side. Another double cord deploys the other side.The bottoms legs auto-deploy their leg tips. Two additional single cords, each equipped with a black disk for easy grasping by the performer, are used to control the flexing of the tips on the upper spider legs during the scene.
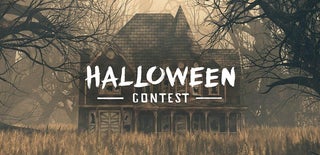
Participated in the
Halloween Contest