Introduction: Restoring a Wood & Canvas Canoe
Wood and canvas canoes were popular before plastic and composite boats became mainstream. There's something about being in a wood boat that I completely enjoy, they are quiet, smooth and at home in their natural surroundings.
Popular to common belief wood canoes are incredibly strong and easy to repair. They generally weigh about the same as fiberglass canoes and if stored properly can be kept in mint condition longer than other construction methods as they are more easily refurbished.
In the past few years I have built boats from skin-on-frame, plywood, strip-plank and composite techniques but never found the opportunity to do restoration work on any of the old classics. About a year ago I decided to jump into working on these pieces of Americana purchasing a wood and canvas 1958 Old Town Trapper Canoe in need of repair.
The following details the build process and shares some lessons learned. I thoroughly enjoyed completing this project and expect it will stay in my family for generations to come!
Step 1: Buy a Boat!
Do some research on which manufacturer or style of canoe you are looking for, there were a few main manufacturers and boats are going to be more available in areas around the northeast and Canada Prices vary from free to a touch over $1000. Realize that if a particular model or brand of canoe peaks your interest you should delay in order to find one or pay the extra cost someone may post for that model as the time you spend on the boat will certainly outweigh any savings in project start or money by buying something other than what you wanted.
In this case I purchased a 17ft 1958 Old Town Trapper Canoe. Many times the boat may look to be in one piece and possibly even float however during the buying process one must be aware of hidden areas of rot that cause entire sections of woodwork to be removed (Found this one out the hard way!). These are commonly underneath rails, or at the stems of the boat. Also boats may be stored upside down on the tips of their decks, necessitating rework of decks, stems, rails and the tops of ribs, so a pretty extensive workload.
Now bring it home and show off your boat that won't float!!
Step 2: Set Up the Shop
One thing that I love about boat building is that it doesn't require too many expensive woodworking tools outside of your general hand tools. For this restoration I used:
1) An army of clamps
2) Set of chisels
3) Dovetail Saw
4) Various hand planes
5) Jigsaw
6) Tablesaw
7) Router
8) Sandpaper
9) House painting supplies
You need to build some stands from 2x4s before you can start working on the boat. My stands have the ability to hold the boat in a sling fashion when sitting right side up or on a removable cross-bar when upside down on the rails. Saw horses might work as well but they tend to put you at the wrong working height and don't allow you to roll the boat about the long axis like you can when its in the sling.
Step 3: Demolition
Look over your boat and figure out what might be reusable and which parts you might want to upgrade. Look for those pesky hidden areas of rot and start removing bad planking, rails etc.
In my case after removing the small canoe decks I found that the joint between the deck, stem and rails had some serious rot. I likely could have scarfed in new pieces to the rails and deck, just replacing the top of the stem, however I was going for something more aesthetically pleasing so I decided to remake the rails and deck from scratch. This actually let me put some really neat customized details so I am glad it happened.
The seats and thwarts were completely reusable in my boat however I wanted to upgrade them to mahogany and cherry respectively.
Step 4: Clean & Sand the Hull
Now that all of the rotted wood is removed the boat needs old varnish removed followed by a thorough cleaning. Varnish removers are very harsh and I hate working with them but there is little way around this. Just follow the directions and WEAR AN ORGANIC VAPOR RESPIRATOR.
Luckily on this build the previous owner had removed the varnish many years back so it was only cleaning and lightening the wood that needed to occur. Using a two part teak cleaner followed by soap and water will remove the mildew, dirt and likely leave the wood with a slightly more blonde color which I find appealing.
Many times boats will have taken on a very dark oxidized color. Using a two part teak cleaner will help this much more than a one part. Also sanding the inside of the hull after washing will cut into the oxidized layer and bring out a lovely honey color. It should be noted that when varnish is applied the color will be slightly darker so always wipe with water to see what the final color will be.
Step 5: Enjoy Lumber Yard Smells & Order Parts
Compile a list of parts that you need to rebuild and what type of wood you will mill them from. Head to a reputable lumber supplier and take your time selecting your lumber. Look for wood free of knots and with correct moisture content. The supplies I picked up from the lumber yard:
1) Rails: Light Mahogany 1 x (17ft x 1.5in x 8in)
2) Seats: Dark Mahogany 1 x (6ft x 3in x 6in)
3) Planking: Cedar 4 x (12ft x 4in x 0.5in)
4) Ribs: Cedar 1 x (6ft x 4in x 0.5in)
4) Thwarts: Cherry 1 x (12ft x 4in x 1in)
5) Decks: Zebra wood, Hard Maple, Walnut
Rebuilding canoes does require some specialty parts. Special tacks are used to clench planks to the ribs and all large fasteners are normally brass. Depending on your build quality and brand of boat historically accurate bolts/hardware may be desirable.
1) Canoe tacks (2lbs) https://www.wooden-canoes.com/
2) Stem tacks (0.5lbs) https://www.wooden-canoes.com/
3) Brass screws #8, 1.5in (125) Lowes
4) Diamond Head Bolts (12) *Specific to Old Town canoes https://www.wooden-canoes.com/
5) Duck Canvas (21ft x 72in) https://www.bigduckcanvas.com/
Step 6: Mill Planks, Rails, Ribs and Misc Parts
Find someone who has a table-saw and mill out the rough dimensions of all your parts. Everything can be fine tuned later using hand planes or sanders.
Make sure to use appropriate safety equipment, work with another person and use correct jigs and clamps to insure a safe milling process.
Do spend extra time getting the dimensions of your planks close to the thickness you want. While a touch too much thickness is a good precaution (You cannot install overly thin planks and maintain a smooth hull) realize that if you don't have a power planar you will make a lot of shavings using a hand plane!
Step 7: Fix Broken Ribs
Rib damage can fall into one of two major categories:
1) Cracked or Broken ribs cause the structure of the boat to be weakened and can also causes bulges on the hull of an otherwise smooth boat.
2) Rotted Ribs do not support the rails well and can cause twisting or major failures in a boat when the deck or rail separates from one another.
Cracked ribs are normally recut and bent to appropriate curvature using a jig (shown above) for the Cant Ribs in the very front of the boat, or bent around the hull for any of the main ribs in the middle.
Rotted ribs are normally damaged only at the tops, which can be replaced by cutting below the rot at a sharp angle and scarfing in a fresh piece of appropriately shaped material.
Ribs also commonly have chips taken out of their tops which can be replaced by adding small pieces of wood.
Step 8: Install Planks
After getting the planks to the correct thickness install them into the boat using the canoe tacks ordered in an earlier step.
The tacks are a special nail driven from the outside of the boat inwards and turned back over on itself using a heavy metal object known as a clenching iron. The circle shape that the clenched tack follows makes it so that no sharp tips are seen in the boat and the flat outside head and clenched inside part of the nail act like a rivet but for wood.
The great thing is that this type of construction is very strong and not brittle like composite boats. Also if a paddler ever damages there boat it is a fairly straightforward process of remaking the part and replacing it. This can allow a boat to be maintained indefinitely which can be contrasted to other styles of construction that once de-laminated(strip-plank) or cracked(plastics) are very hard to repair.
Step 9: Blend New to Match Old
Its very rewarding to replace old rotted sections of your boat with new material that will last. Unfortunately the historic patina the wood takes after being exposed to the air is not present and can produce an undesirable contrast. While some of this will be covered by varnish a bit of stain can help the wood match.
I use a very light stain as a base and then add darker shades of brown and red to get the correct color practicing on a similarly sanded piece of excess material. You won't be able to get it perfect but it will certainly be less noticeable.
Step 10: Install Inner Rails
The inner rails are in many ways the backbone of a cedar canoe. They hold the curved shape of the boat's sides and form the foundation which decks, seats and thwarts are attached to. The inner rail is simple in construction with a rectangular shape and simple taper at the bow and stern so it can sit snugly between the deck and planks.
The inner rails are installed by driving two nails through every other rib in the canoe. The rails on some boats have enough vertical curvature that they must be steam bent and dried on a jig to prevent breakout when installing.
When putting the rails on the army of clamps is called into service. A tight match between the stem and the rail tips is required so using a long sanding stick or the kerf of a saw can help reduce the gap.
Step 11: Make & Install the Decks
The tips of my decks were rotted out so I decided to replace them. Most decks are made using a board bent over a jig and then shaped into a triangle. In my case I wanted to have some woodworking details run throughout various pieces of the boat so I incorporated hard maple(white pin-stripe), walnut(center black stripe), and zebra-wood in the decks, outer rails and seats.
The previously roughed blanks were laminated together and cut using a jigsaw. A hardmaple butterfly key was added across the back of the laminated decks and then a chisel used to carve the decks to the appropriate curvatures. Finishing was done by stepping through sandpaper on and orbital snader from cutting grit to finishing grit.
This is were I would encourage people to slow down and think of how long this process takes and how long they plan to use their canoe. It may be troublesome to put these personalized details in but well worth it!
Step 12: Make Seats and Thwarts
The seats were made from dark mahogany to contrast with the light cane they would be woven with. They were built using a keyed mortise and tenon structure and rounded over using a router. Once I finished the routing I was very impressed with the grain that showed through! Holes were drilled for the cane to be woven through.
The thwarts were made from cherry. Its a bit lighter in weight and color than mahogany and I like the color in the boat as sometimes too much dark wood can clutter up a build. The old thwarts were used to pull a pattern which I routed to and then used a smaller rounding bit and sander to finish off the thwarts. The unvarnished product is in the last picture on the left compared to the oak thwarts on the right.
Step 13: Christmas Gifts
Use leftover canoe materials to build Christmas Gifts!
Step 14: Make Laminated Outer Stems
The outer stem is the part of the boat that cuts through the water and covers the bow and stern tips of the boat. Most canoe builders favor placing a brass band as the outer stem but I had enough left over material that I decided to create a custom jig and laminate wooden outer stems.
The jig is created from plywood and has large holes drilled in it so that clamps can be placed every few inches. Strips of 1/4in mahogany are placed in a tube and steamed for 45min. They are bent around the jig with an aluminium band running behind them to prevent backside breakout.
After drying they retain their shape and are laminated using West Systems Epoxy.
*The jig I built was taken off the stern and the stem produced did not fit as well on the bow. Make sure you make two jigs one for the bow and another for the stern.
Step 15: Varnish......Forever
I applied six coats of Epifanes varnish to the inside of the boat and two on the outside. In between each coat the entire varnished surface must be sanded with fine grit sandpaper or a Brilo pad. This takes a very, very long time but the result is spectacular!
Step 16: Canvas the Boat
Skinning a canvas canoe could make a great Instructable all on its own! The canvas is folded in two and placed between a set of two-by-fours at each end so that it can be pulled taught using a set of come-alongs.
In my case I found a tree and my truck worked pretty well as anchors. The boat is placed into the pocket and weights placed inside of the boat to further stretch the canvas. It is then tacked around the upper edge with these tacks eventually being covered by the outside rail.
Once the tacking is completed the excess material is cut away and your boat is skinned!
Step 17: Apply Filler & Fair the Hull
Canoe filler is a mixture of house paint, dryers, and talc powder. When applying it has the consistency of chalkboard paint and is intended to dry to that type of hardness. Due to the different mixture of products the filler does not fully cure for almost 5 weeks!
The filler is applied just like regular paint usually requiring two or three coats. There are formulas available online but I just purchased from a canoe supplier.
After the filler has cured the optional step of fairing the hull can be completed, I used a low density filler and a long-board sander to reduce bumps and smooth the hull. This helps produce a better finish if using a high gloss paint.
Step 18: Make Laminated Outer Rails
The outer rails of a canoe are more complex then their inner counterparts. The outer rails' profile has a lip the size of the planking which stops an inch below the top of the gunwale. This lip can be cut on the table saw or using a router.
The outer rail is also slightly thicker than the inner and more prone to breaking because of such. In order to avoid this I created laminated "Fish Tail" tips for my outer rails composed of mahogany, walnut and hard maple with an inset zebra-wood diamond. The total laminated tip was 9 pieces of wood.
The "Fish Tail" was made of two laminated curves, made using the small jig above, backed up against one another and then transitioned by the inset diamond to the longer part of the tip.
Step 19: Cane the Seats
Canoe seats are typically cane though sometimes webbing, leather, or other materials are used. Cane can be prewoven and pressed into a routed notch on the edge of the seat or hand woven through holes drilled on the seat edge. I choose to hand weave the cane and use a daisy & button pattern rather than the standard six weave.
3mm natural cane was used for the main pattern with a larger width for the border. The cane comes in 6ft long sections and is soaked for a few minutes before being woven. Make sure not to over soak your cane as it will turn gray and not return to the natural tan.
After all the hard work in the shop caning is a pretty fun weekend project and great for the hot months of the year.
Step 20: Paint the Boat
After fairing the hull three coats of Epifanes Marine Enamel, Color #23, were applied using the rolling and tipping method.
In rolling and tipping a paint roller is used to spread paint to a consistent thickness on the surface and then a paintbrush used to remove the bumpy pattern of the roller. High quality rollers and paintbrushes should be used to avoid leaving hairs or fuzz in the paint job. In between fairing, which creates lots of dust, and painting, I thoroughly clean the shop. Epifanes products are very thick and I always have to add brush thinner. This is a good thing as the quality is high and thinner is cheap! While a high quality marine paint does incur a greater expense it is worth it as common house paints won't produce nearly as bright and deep of a shine, don't have UV stabilizers and won't last as long.
This is actually one of the fastest parts of the project and high temperatures can cause you to have a tough time keeping up with the wet edge of your paint job.
*I did not use a high enough quality roller on my first coat, and it started to leave fuzzy bits of the roller in the paint job. When I noticed this I stopped using the roller, just applying paint with the brush. This doesn't allow for even distribution of the paint and caused some sags as seen above. These have to be sanded out and another coat applied. After switching to a better roller for the next two coats I got a nearly perfect finish!
Step 21: Final Assembly
With the paint dry its time to put together all the pieces, So cool to see your handy-work together for the first time!
At the time of writing this instructable I just finished the build and have yet to go out for a maiden paddle. I will upload some better pictures and video of the final product out on the water soon!
Thanks for taking the time to check out the build, happy paddling!
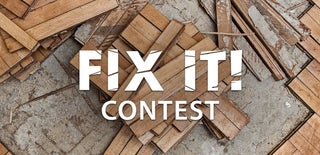
Grand Prize in the
Fix It! Contest