Introduction: Rocks to Art! DIY Lapidary Machine.
I needed a way to turn Geode rocks into uniform, polished art to use in my stained glass work. Perhaps you want to work with rocks, and like me, don't have thousands of dollars to spend on Lapidary equipment.
No big deal, with a few discarded parts, some basic hardware, and a lot of...grit..., you will build a machine with countless possibilities.
You can buy a couple cheap components to make things easier, or you can build them from scratch if you have the tools - I'll show you how to do both.
So let's go! Release that inner child that just wants to go find interesting rocks.
DISCLAIMER! Do not proceed unless you are confident in your building ability. Electricity will follow the shortest path to ground- sometimes through you (Shocking!) Machinery with moving parts does not care about your loose hair or extremities that get in the way (pinching, crushing, pulling, ripping.) Work safe, ask for help if needed, and always wear Personal Protective Equipment.
Supplies
See step 1 below.
Step 1: Gather Your Tools and Materials
For best results, read this instructable in it's entirety and gather the tools and materials required before you begin building. Critical decisions can only be made with the proper parts in front of you. Most of what I used was scavenged scrap material. You could do the same or make life easier and purchase a couple key components.
Tool List:
- Tools for Measuring and Marking
- Drill
- Drill bits. 3.a- Hole saw (not required but will make things easier)
- Allen wrenches
- X-Acto knife
- Pliers and Screwdrivers
- Saw (if you make your motor base from wood)
- Sander (or you could hand sand...)
- Angle Grinder (only required if you make your own backer plate instead of buying one)
- Not pictured: Screws (12), nuts and bolts (4 each) and spray glue (I like 3M 77)
Materials List:
- Kitchen stand mixer motor (I found mine discarded)
- Motor Shaft Adapter
- PVC flange (top half pictured)
- Motor base Material (I used leftover plywood)
- Bucket, Tube and fittings (supply lines meant for water/ice dispenser on fridge would work well)
- Flat lapping plate/Backer plate (I used and old saw-blade and acrylic)
- Basin to catch water/rock slurry ( I used a Medium Mortar Mixing tub)
- Waterproof Sandpaper (I used grits from 150 - 2000
- Waterproof motor housing (I used a Plastic Storage Container)
Step 2: Build a Base for Your Motor.
First things first. In case you didn't know, the intent of this machine is to take rough rocks and smooth them to a glass smooth, polished surface. This is achieved by abrading the rock with progressively finer diamond plates or sandpaper. To prolong the life of the cutting plate/sandpaper, water is used to flush away the rock slurry.
To achieve this, there are some KEY things you need: A motor, discs to grind the rocks on, and a way to keep the water and rock slurry OUT of your machine (most machines don't appreciate getting dirty and wet).
This is why I chose to use the motor from a kitchen stand mixer. Most have 5-6 speeds, the slowest being about as slow as a microwave turn table, and the fastest being...fast...but not so fast you fear you will fling rocks across the room or lose a finger.
The motor is the heart of this machine, and deserves a nice house. Based on the size of my motor, I built a plywood housing in the form of a "U" shape. This "U" shaped housing needs to be able to fit inside the waterproof container you have chosen (I used a plastic storage container turned upside down). This, in turn, sits on a plywood base.
Drill a hole to allow the motor shaft to extend through the top. I used a hole saw for this step. I also attached the PVC flange (mine was about 3" in diameter) I used a hole saw to recess the fitting into the wood, as I wanted it to be as flat as possible. This PVC flange was scrap I had, but you could buy something similar at a hardware store for less than $3. Look for a "coupling housing" or "flange" in the PVC or electrical section. I glued mine in place.
As you build the base, I highly suggest you screw them together, but don't glue them- as you may want to take it apart a couple times to ensure everything fits perfectly.
Step 3: Attach Motor Shaft Adapter, Mount Motor to Base and Cover.
Next, secure the motor shaft adapter to the motor. I used an Allen wrench for this.
KEY INFORMATION!: The decision you make here is very important, and highlights the benefit of having all your parts before you build. You MUST choose the correct adapter here. Carefully measure the shaft, and purchase an adapter that will:
First: Fit the size shaft of your motor.
Second: Convert that size to a threaded arbor that will fit the grinding attachments you purchase or make. The most common sizes are 1/2" threaded arbor or 5/8" threaded arbor. The adapter you choose will dictate the size and type of tools you can use. If you are feeling ambitious, just buy one of each- they are only about $10 to purchase online. Search for any of the following: Motor Arbor Adapter/ Motor Extension/ Motor Coupling/ Motor Shaft Adapter.
Secure the motor to the base so the shaft and adapter extend through the top.
Place the waterproof cover on top of the motor and base assembly. Even though all the water will be collected in the basin installed on top of this, the cover provides extra insurance against water, dirt, and protects the electrical components of the motor.
I installed this by drilling a hole that is a friction fit with the PVC flange. I then used a X-Acto knife to cut a slot where the on/off switch is located.
Step 4: Install Catch Basin and Water Coolant "system"
We are almost there! Install the basin to catch the water and rock slurry by cutting a hole inside the Mortar mixing tub. As with the waterproof cover, make sure this hole is a friction fit with the PVC flange. Place the basin over the PVC flange and install the threaded top ring. Tightening this ring will ensure a waterproof seal.
Instead of purchasing a submersible pump and feeding the water into the machine, I opted for a simple gravity fed bucket with tubing attached. I use a bolt to regulate how fast the water comes out. The bucket is placed above the machine, and the water drains onto the surfacing plate and into the basin.
Step 5: Install (or Make) Your Backing Plate and Flat Lapping Discs
At this point, you have a fully functioning machine. Now we need the surfacing plates to grind the rocks flat. This is made up of a backing plate, and flat lap discs of varying grit.
You could purchase these online, they are not too expensive- however I opted to build my own. If you want to purchase them online, search for the following: Aluminum Master Lap Grinding Pad or Aluminum Master Base Plate (This is what the discs will reference against.) You also need Flat Lap Discs- search for: Electroplated Diamond Lapidary Faceting Flat Lap Disc or Flat Lap Disc Grinding Polishing Wheel.
If you want to make your own- this is what I came up with: A used saw blade and acrylic discs with sandpaper adhered.
Table saw blades are balanced and hardened. The problem with them is they are flat until you reach the teeth, where each tooth is "set" at an angle to aid in cutting. We need a surface that is completely flat, so to achieve this you need to cut or grind the teeth off. I used a plywood blade, because the teeth are very small and easy to grind off.
I then used scrap acrylic to cut the circular discs. After the saw blade and acrylic pieces were cut, I sanded them lightly. Sanding the acrylic will ensure there is more "bite" when I glue on the sandpaper.
I used 3M 77 (an aerosol contact cement) to glue the sandpaper to the acrylic discs. I had wet/dry sandpaper from 150 grit all the way to 2000 grit. I put sandpaper on both sides of the acrylic.
Step 6: Machine Set Up: How to Use and Enjoy Your Machine!
To use the machine, put the backing plate on the arbor with the acrylic disc on top. Make sure the nut is tight on the arbor and that the PVC flange connection from the basin to the base is secure. This produces a very flat/stable surface to grind your rocks to a polished shine! Place your water coolant on a surface higher than the machine, and let the water slowly flow onto the disc. I use a flexible lamp that allows me to see what I'm doing AND hold the hose in place.
Now you just need to find an interesting rock! Geodes and other semi-precious stones are often broken or cut open. Start at the lower grits and work your way up to the highest grit you have. Give it a final polish with a buffing wheel and diamond paste.
Thank you for following along! Stay tuned for my next installment where I will show you how to use this same machine to cut rocks into even slabs for jewelry, art, or in my case- pieces in a stained glass window!
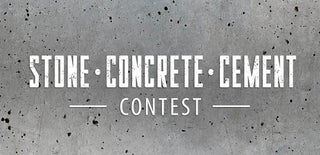
Participated in the
Stone Concrete and Cement Contest