Introduction: Scaffolding Ladder Bookshelf With Tambour Door Cupboard Designed in Fusion 360
I had a corner in my living room which was being underutilised and was next to some existing scaffolding shelving I had made before. I also wanted some general storage so decided that I'd make a ladder shelving using scaffolding tubes and fixings for the frame, scaffolding board for the shelves and a hardwood tambour door cupboard.
Supplies
Materials
Scaffolding tube (26.9mm) - 2 x 2100mm, 2 x 245mm and 3 x 500mm
Scaffolding fixings (26.9mm) - 6 x short tee, 6 swivel locating flanges, 2 x single swivel, 6 x double lugged bracket, 6 x single lugged bracket and 3 x hooks
A single scaffolding plank - 225mm x 38mm x 2400mm
Hardwood for the cupboard - 195mm x 20mm x 4000mm
Decorating cotton dust sheet
Old pine panel for the shelf
Step 1: Fusion 360
After coming up with an idea I thought I'd draw up my idea in Fusion 360. My Fusion 360 skills are fairly limited and I work much faster in CAD so started with a 2D drawing and imported the DXF in to Fusion. I then extruded elements and joined them together with move and copy. I also created the scaffolding fixings from scratch in Fusion which did take a while but seemed to work out!
I have added the Fusion file here if anyone is interested.
Attachments
Step 2: Make Cupboard Shell
I had already made a tambour door coffee table in my front room made from Sapele and had a plank left, so it was a no brainer to make the cupboard from the same material to cut costs and for matching purposes.
I started by cutting the plank in to the sizes I required and glued together using butt joints to make four panels.
I then routed grooves in to the ends of two panels and cut half tenons in to the other two panels using a table router and dry test fitted the panels together.
Step 3: Add Tambour Door Channel
Having made a tambour door before I already had a jig for routing a groove for the door. I did need to adapt the jig however as it wasn't quite wide enough. The jig is used in combination with a handheld router with a template bushing and an 8mm spiral router bit. The track runs along the entire front along the edge and about half way along the back. When closed the door will end about 1/3 in to the edge and when closed the handle end will end up by the corner.
Once the track groove was cut I added an additional groove at the back so the door can be put in and taken out when the rest of the cupboard was complete.
Step 4: Make Tambour Door
A tambour door is made from a series of long strips glued on to a piece of material.
I started by ripping about 30 strips of 20mm x 10mm of sapele wood from my offcuts and added a chamfer to both edges on a router table.
I then used a couple of saw tracks as straight edges to make a jig to hold all the door slats tightly in placed. I clamped the first track down and used a single slat to set the position of the second track at the front and the back, so I knew the tracks were parallel. I then installed a piece of wood to the front running at 90 degrees to the tracks, added all the slats between the tracks and finished by screwing another bit of wood at the back while pulling the strips tightly together to minimise any gaps. I followed this by added some masking tape along each edge as I only wanted the material in the middle of the door.
I then spread wood glue to the entire door and added a piece of cut to size decorators cotton dust sheet,pressing and pushing down making it straight and as tight as possible. After an hour the glue was set enough to remove the door from the jig and go along the door separating all the slats and cleaning up any glue squeeze through.
To finish the door I placed it face up and cut a rebate in to the edges of the slats. This means that when the door is closed the overhang of the rebate will go over the channel so you end up not seeing the channel and everything looks nice and neat.
Step 5: Finish Joinery, Glue and Clamp
I needed to add a couple of internal panels to the left hand side and the back so anything in the cupboard wouldn't foul the mechanism. As they weren't structural panels I just used some 4mm thick plywood. I used a series of grooves to the rear of the top and bottom cupboard panels and one to the right hand side panel, along with a couple of pieces of wood to the left hand side, with grooves, so I could add a floating panel to the side and rear. Unfortunately it seems like I didn't take any photos of this stage...sorry!
Now I had all the parts of the cupboard I put it all together with glue and clamps.
Step 6: Add Door and Shelves
To get the tambour door to slide in easily I sanded the top and bottom of the door and added some paste wax to the track and wood. This helped to get it in initially and then sliding the door backwards and forwards a few time to distribute the wax.
I cut a single shelf from a panel of pine I had once salvaged from some old furniture and added a couple of recess to the corners for some support pins. I added some wenge wood stain to darken the oak to match in better
I then sanded the whole thing using 80, 120 and 180 grit sand paper.
Step 7: Add Handle and Oil
Lastly I added a shaped piece of wood that screwed on the last door slat for a handle.
I then added a few coats of hardwax oil to the whole cabinet to finish it off.
Step 8: Build Scaffolding Frame
The frame was build from 26.9mm scaffolding tube and fixings. There is a good local shop I used called The Metal Store which also cuts to size and delivers for no extra cost, handily they also stock scaffolding boards so it was a one stop shop for all I needed.
I started by confirming all the scaffolding I had ordered was the right length, which it was, so I didn't need to do any cutting myself. I then put together the first side support with an allen key using two tubes, three swivel locating flanges, one single swivel, three short Tees and three single lugged brackets. Once the first one was put together I used that for reference for the second so everything was in the same place.
I leaned one of the sides against a wall and marked out where the brackets attached the cupboard. I then drilled out some holes, countersunk and put in some 6mm insert nuts.
With the brackets loose I used some machine bolts to attach the cupboard to the scaffolding using some nuts for spacers. Once both sides were fixed I added the scaffolding tubes for the selves and tightened everything up.
Lastly I fixed the top of the frame to the wall and the bottom to the floor.
Step 9: Add Scaffolding Board Shelves
I had ordered a single 2.4m (8ft) board which I cross cut down to size and ripped a couple of sections as the bottom and middle shelf were wider than the board. After gluing those two shelves together with wood glue and leaving to dry, I sanded the shelves roughly with 80 and 120 grit.
I then oiled the shelves with a dark oil so the boards matched in with the cupboard a bit better.
I added a couple of hooks to the bottom shelf support for music leads etc. so needed to drill a couple of holes to the underside of the lower shelf to accommodate them.
Finally I simply screwed the shelves to the double lugged brackets and levelled them with a spirit level.
I think these shelves ended up really nice and added more storage I could use for some music equipment and books in a corner that before was look quite messy and underutilised. So overall very happy!
If you have enjoyed reading this Instructable please think about voting for me in the book and bookshelf contest. Thanks for reading!
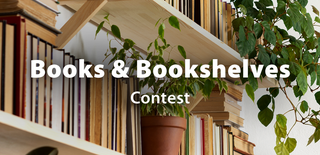
This is an entry in the
Books and Bookshelves Contest