Introduction: Tabour Door Units Fitted in to Alcoves
I was asked by a work colleague if I could make a couple of units to fit in to a couple of alcoves in her house. After a bit of brainstorming and coming up with various designs we arrived at the decision to have oak units with tambour doors.
Tambour doors are the ones made from a lot of slats, with some material backing, that run in a track to go round corners. I'd never made this type of door before and was up for the challenge. I'd also not made any built in furniture before so that was a first too.
I went round to measure up and did a couple of sketches with the general concept and the major dimensions. Both the alcoves had power points located in them which still needed to be accessible so that was also factored in to the design.
One of the units had an up and over door and the other a left to right door.
My main photos are from the up and over unit but the same principles applied to both.
Supplies
Oak timber. I used about 15m x 145mm x 20mm (45ft x 6in x 3/4in)
Plywood for shelves and a drawer
Glue
Heavy duty decorating canvas
Step 1: Make the Slats
I started by cutting some planks of oak to the required length and ripped them in to 20mm x 15mm wide slats. In the end for the up and over door I needed about 50. I also cut a 20mm x 40mm wide slat which would go at the bottom of the door so I could attach a handle to it.
Once they were all cut I added a chamfer to the long sides of the slats using a chamfer bit in my router table.
I then needed to cut a 'half tenon' to the edges. The sticky out bit would run in a groove and the other part would overhang the groove. This would ensure that the cut of the groove wouldn't be visible when the doors were shut.
Step 2: Create the Tambour Door
Now all the slats were cut I made a jig which would hold all the slats tightly together and perfectly square. I used a plywood base and screwed some more ply to hold each side of the door square.
Once I had lined up all the slats I put some masking tape along the very edges so the material didn't interfere with the running mechanism. I then used a roller to apply a lot of glue to the slats and placed the canvas on top. I then made sure that the material properly stuck to all the slats and was perfectly flat.
After leaving it for about an hour I removed it from the jig and rolled it up to make sure no glue was between each of the slats.
Step 3: Track Jig
As the tracks needed to be exactly the same an perfectly opposite I made a jig I could use as a template. I drew out the shape on some plywood and shaped the corners, sanding them smooth.
Step 4: Cutting the Track
Next I cut some oak to size and fixed it together with biscuit joints and glue, to create the side panels. Once these were dry I trimmed I was ready to cut the groove using a straight router bit with a guide bush. I positioned the jig on the first panel and cut the groove to a depth of around 10mm (3/8in). To make the next groove on the opposite panel I flipped the jig over before positioning it on the other panel. So the jig face that was side up on the first panel was now face down on the other. This would ensure that if there were an imperfections they would be reflected in the same position on the other.
Once they were cut I added an additional groove that lead out of the main track and out of the unit. This meant that I didn't have to glue to tambour door in to the final unit and would be removable.
Step 5: Build Internal Rear Panel
I added a back panel to the units which would be in front of the track. This would mean that anything that was put in the unit wouldn't be able to foul the door when it was opening. I started by re-sawing some of the oak in to two and putting it through a thicknesser (planer) so I would have lots of thinner timber I could house in a thicker frame. Once they were finished I cut a mortice in to what would be the inside of the frame. I then used pocket hole screws and glue to fix three sides of the panel together, slotted the thinner part in to the frame and secured it all with the final side.
Step 6: Joinery and Track Testing
With reference to the up and over unit, I made a top and bottom panel, cut some mortices in to the edges of them and cut tenons to the side panels. I also drilled some holes to the side panels before the glue up which would be used for the shelf pins.
Before committing to the glue up I tested the doors in the track to make sure everything was going to work.
Step 7: Construction
The unit was pretty easy to put together. The side panel tenons were glued in to the top and bottom mortices and the back panel was screwed in with pocket hole screws which kept the whole unit square during the gluing up process.
I then make a stop which would limit the travel of the door and a handle that I made out of oak and screwed in to the wider final slat.
Step 8: Secret Drawer
To install the unit I was going to place the unit on a wooden plinth that I could jimmy up and level on site. Taking that a little further I thought that there would be an opportunity to add a drawer to the bottom. I started by building the plinth with an open front and making a drawer from plywood which fit inside. To make the front fancier I cut some thin bits of oak and glued them in a nice pattern on some thin plywood. After adding some drawer runners I added a push to open mechanism so it didn't require a handle and didn't look like a drawer.
Step 9: Wire Management and Shelves
In order for wires etc. to be still used I cut a hole in the top of the left to right running unit which incorporated a groove so a round plug could be added to disguise the hole. I also added a few cut outs and grooves in discrete places to help with wire management.
I made some shelves with 18mm (3/4in) plywood which I painted black and added an oak strip to the front edge.
I also added a few oak blocks around the edge of the units which would eventually covered with thin panels during the installation.
Step 10: Sanding, Oiling and Installing
Now that all the parts were ready I sanded all the parts with 80, 120 and 180 grit and gave all parts a couple of coats of Danish oil.
The installation took quite a long time but looked really good in the end.
I started with the left to right unit in the living room which had carpet and skirting board. I cut and removed the carpet under the plinth and did the same to the skirting board with an oscillating multitool. I then added the plinth, levelled it up a and screwed it in to place.
I had built the unit so the bottom part was narrower that the alcove but would end up behind the cuts on the skirting board.
The top of the unit was cut oversized which I cut onsite with a panel saw. To get the correct size I used a thin bit ply with card to the edges to get the outline of the alcove. I then transferred this to the top of the unit and cut it to size.
This part could have worked better as I had to trim the top a few times before I finally got it to fit.
Once it was in the right place I cut the covering panels to size and glued them in to place to tidy it all up. I used a broken line of wood glue for strength and a few smaller lines of superglue (CA glue) to 'clamp' them in to place.
I then repeated for the up and over unit. The wire management was more complicated for this one and I used string to get from the hole in the top, along the inside edge, in to the plinth and out of the bottom. This could then be used to get wires etc. from top to bottom.
Step 11: Finished
After a full day I had installed both units and was very pleased with the final results as they looked great and added a lot of useful space to otherwise under-utilised alcoves.
If you enjoyed reading this Instructable and/or found it useful please consider voting for me in the woodwork contest.
Thanks!!!
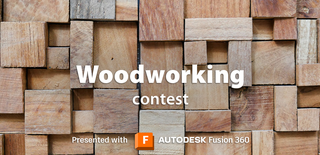
Participated in the
Woodworking Contest