Introduction: School of Fish Sculpture
This method can be used to make a single fish, or school-of-fish sculpture of any species type. In most cases, I let the silvery color of the weldable sheet steel shine through, but they can just as easily be painted if you wish to do a colorful, tropical type of fish.
Step 1: Tools and Materials You Will Need
MIG welder- I use a 110 volt portable system to connect the fish and attach the hangers.
Oxyacetylene torch- for annealing and to attach the pectoral fin.
1/16" RG-45 copper coated welding rod- filler rod for attaching the pectoral fin.
Torch tips-#4 for annealing, #1 for welding on the pectoral fins.
Ball peen hammers- large and small
Center punch
Photocopier and paper
Rubber cement
4-1/2" grinder with a 1/16" thick cut off disk, grinding disk, and 120 grit (or smoother) flap style sanding disk.
Weldable sheet steel- I use 1/16" (.063") for the larger fish and 20-22 gauge for the smaller fish and pectoral fins.
Vise
Magic Marker, and welder paint pen for steel
drill bits of various sizes depending on the intended size of the eyeballs.
Dremel tool with cutoff discs
acetone - to clean the metal of oil and soften the rubber cement.
Step 2: Select Your Fish
Search for a good quality, clear profile image of the type of fish, or school of fish you wish to make. In this case of the feature photo, I chose to use a Coho salmon. It can be from a drawing, sketch, or painting.
Step 3: Draw the Fish Outline
Draw an outline of the fish by laying the fish picture on top of a piece of paper with a sheet of carbon paper in between. Darken the line with a sharp ink pen with permanent ink.
A profile image is 2 dimensional. You can create a 3-dimensional effect by fattening the outline to allow for the curvature of the fish. After the fish is hammered out, it should appear the same size as the original drawing.
Step 4: How Many Fish Do I Want?
You can make a single fish or a school of 30 fish or more if you wish. It's up to you to decide, but the fish should be scaled to the size of sculpture desired in the end result. You can even make a welded steel frame to encase your fish (steelhead trout) or an open school of fish (herring) as shown in the photos.
Step 5: The Layout
What's important in the layout is that some of the fish in the school appear to be farther away. This is accomplished simply by using a photocopier. Vary the size of the printed copy and print as many different size copies as will be the number of fish you want in your sculpture. The sculpture is basically the same fish drawing printed over and over again in different sizes.
There are two types of relief sculptures:
- Low relief (a.k.a. Bas relief- pronounced BAH) This is similar to the image on a coin.
- Alto or high relief- Parts of this sculpture are well raised above the surface.
Alto reliefs look a bit more realistic. With most of the school of fish sculptures I've done, depending on size, the largest fish ends up being about 2 to 2-1/2 inches off the wall surface.
By reason of size and placement, the smaller drawings will naturally appear to be farther away. Positioning the smaller fish under the next larger fish will enhance the image of distance.
Although the arrangements are endless using paper cutouts, it is imperative that the fish are all laid out so that they can be connected by one, two, and sometimes three concealed welds. The larger, thicker fish support the smaller fish in the layout.
Mark the percentage size of the blowup on each fish drawing.
Step 6: Cutouts
Clean a sheet of steel using acetone to remove any factory oil.
Cut out the paper fish drawings just outside of the lines and paste them to the sheet steel using the rubber cement. This holds everything in place for you as you cut around the lines.
There are a number of ways to cut out the drawings. These include shears, sheet metal cutters, tin snips, nibblers, 4-1/2" grinder with a cutoff wheels, plasma cutter, etc. Whatever you use, cut up close to but not past the printed line.
After each fish is cut out, refine the edges by grinding exactly up to the line without going over a line. This usually involves a bench grinder to start, a grinding disc on a 4-1/2" grinder, on down to a Dremel with cutoff disks to get into the tight spots.
After the fish is cut out, transfer the notation of that size fish onto the backside with the metal paint marker. The mark does not disappear, even though the metal is heated to red hot. You can get these at some hardware stores and places that sell welding equipment, or online.
Center punch the center of the eye deeply on a block of wood, and shallower in two places at the leading edge to identify the location and angle of placement of the pectoral fin.
Using a Dremel tool and cutoff disk, inscribe the gill slits by cutting through the paper just enough to identify the location and line of the gill slits after the paper is removed. The gill slits are enhanced later by tapering a slightly deepening grind up to the inscribed lines by again using the Dremel with the cutoff discs.
Once finished cutting out, punching and inscribing lines, remove the paper and Rubber cement by soaking the paper with acetone. Clean up any excess glue in preparation for annealing.
Step 7: Anneal and Shape
After the paper is removed along with any excess rubber cement, anneal the metal.
The annealing process is simply heating all of the metal cutouts to red hot using an oxyacetylene torch with a large torch nozzle. I use a #4 tip because is covers more area quicker. The entire fish does not have to be red hot at the same time. You can start at one end and work your way to the other end. The fish may warp a bit, but it's nothing to be concerned about since it will be cleaned up in the hammering and forming process.
What the annealing process does is expand the molecules of the steel. This softens the metal making it easier to hammer into shape.
Lock a peen ball or a ball peen hammer in the vise so you can use the peen part of the hammer as a back stop to round the edges of the fish to create fullness to the fish using another hammer. This is why you fatten the fish in the original drawing.
On the larger fish with thicker metal (1/16", .063"), I find it easier to heat a couple inches along the outer edge to red hot. It will form much easier when hammered against the ball shape. Thin metal cools quickly, so the torch needs to be as close as safely possible to the hammering location.
Annealing metal, especially the thinner gauges, requires concentration. One distracted moment and you can accidentally blow a hole in a lot of prep work. There is a fine line between red hot and the melting point. I suggest practicing first with a representative example of the metal you plan to use and see how far you can take it before it melts a hole. Usually, when you see teeny tiny sparks happening on a red hot surface, it's getting close.
Step 8: The Eyes
Using a wire brush on a bench grinder, remove all the dark scale created by the annealing process. This should restore the look to that of the original metal.
This video will show you how to make a realistic looking fish eye in sheet steel and demonstrate some of the other steps that I've explained up to this point.
Step 9: Make the Connections
You want the school of fish sculpture to look realistic, so it is important to lay them out in such a way that you can make all the welded connections without being able to see them from the front. This video shows what goes on behind the scenes.
A MIG welder works best for this part. Again, practice on a representative example first. Get your settings right because it's easy to accidentally blow a hole in a whole lot of work.
Attaching the pectoral fins is the most challenging part in that it requires the most care, patience, and welding dexterity. It's tricky to weld thinner metal to thicker sheet metal. Here's how I do it.
Line up the leading end of the pectoral fin with the corresponding center punch marks. Adjust for angle, and shoot two tiny tack welds with the MIG on the outer corners of the fin's leading edge. This will act like a third hand.
With your 1/16" feeder rod in one hand, torch in the other, heat a spot just in front of the fin until it will accept the feeder rod. Control the melt and flow up to when it just touches the fin. It's best to have the torch set for slow but steady progress. "Haste makes waste."
Step 10: Coloration
Coloration can be applied by a number of methods. You might try alcohol inks or tints like the rainbow trout in the photo above. These usually require follow up with a protective clear coating that doesn't affect the base material. Acrylic paints are another choice and work well for highly colorful tropical fish with intense markings. Acrylics are more UV tolerant if you want your sculpture to be displayed outdoors.
I choose to use the torch for coloration. It's like icing on the cake, and the most fun part. This is accomplished by first buffing the steel to a high luster and then applying heat from the torch. How close, how hot, and how long you hold the torch to the metal are the determining factors for how the metal changes in color.
Done carefully, torch tinting can produce some pretty interesting results like tiny spots followed up with different coloration across the same area. The more you buff the metal first, the more control you have as you progress through the color change, and the more distinct can be the line of coloration.
Although not on the list of tools, spots on the backs of some fish species are easiest to make with a mini torch like the one's jewelers use. I use them fairly often. They are pretty handy to have around if you ever want to do small welding in steel. They are available online for under fifty bucks.
To make a spot on the back of a fish, make a vertical quick dip to the metal surface with the mini torch (they usually come with an assortment of tips), hold the hottest part of the flame to the metal, and pull away the instant a visual change starts to happen, or, go by a prepared time established by practice relative to the thickness of the metal and size of torch tip.
Torch tinting requires a little practice to control. The temperature of the metal can produce light yellowish colors on to reds to deep blues just by how long and how close the tip is to the metal. The size and intensity of the flame is another factor.
I recommend practicing by playing around first with a buffed up sheet of metal. When you get the results you want, then apply that method to your sculpture. In any case, you can erase any failed attempt with regular metal polish like MAAS, or Simichrome polish and try again and again. Buff away the polish residue first.
Raw steel will rust in a short period of time. For this reason, I employ a non yellowing protective coating on the metal like a clear acrylic lacquer.
Step 11: In Conclusion
I sell fish sculptures like these for up to $750. You can too. It just takes a little practice. Best of luck and good fishing!
Step 12:
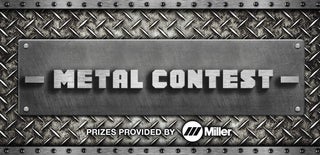
Second Prize in the
Metal Contest 2017