Introduction: Screen Printing
Screen printing, or skill screening, is a relatively easy process that allows you to replicate an image onto a variety of surfaces including fabric and paper. Printing on fabric allows you to design and print your own graphic T-shirts
Step 1: Cut the Stencil
Materials:
silk screen (silk screens usually have rectangular frame made out of wood or metal, with silk fabric stretched across the frame)
something to make a stencil
I would recommend:
acetate paper (clear paper, basically the same as what you would use to write on on an overhead projector)
contact paper (you can buy this at ACE hardware, it can be colored or cloudy/transparent and it is sticky on one side)
screen printing ink (silk screen ink)
squeegy
masking tape
newspaper
The easiest and cheapest screen printing method uses stencils to make the print. To make these stencils, place a sheet of acetate over the sketch and traced over the lines with a sharpie. I find that acetate is easier to use than contact paper because it is transparent, can be easily cleaned, and can also be used as a stencil for spray paint.
silk screen (silk screens usually have rectangular frame made out of wood or metal, with silk fabric stretched across the frame)
something to make a stencil
I would recommend:
acetate paper (clear paper, basically the same as what you would use to write on on an overhead projector)
contact paper (you can buy this at ACE hardware, it can be colored or cloudy/transparent and it is sticky on one side)
screen printing ink (silk screen ink)
squeegy
masking tape
newspaper
The easiest and cheapest screen printing method uses stencils to make the print. To make these stencils, place a sheet of acetate over the sketch and traced over the lines with a sharpie. I find that acetate is easier to use than contact paper because it is transparent, can be easily cleaned, and can also be used as a stencil for spray paint.
Step 2: Tape the Stencil to the Screen
Once you have your stencil, place it on the front of the screen. A screen is made up of a wooden frame with silk stretched over one side like a canvas. The front is the side of the screen that you'd paint on if it were a canvas. The front of the screen is the part that will be face down, touching the material to be printed on.
Make sure that when you place the stencil that the image facing you is the mirror image of what you want to be printed; if you are printing words, the words should appear backwards when you put the stencil on the screen.
Next tape down the stencil. I use masking tape, because it is more water resistant than scotch tape but still peels off of the screen without damaging it. Also cover all of the other areas of the exposed screen. All of the negative space, or open areas of the screen will allow ink to be pushed through. I usually use spare rectangles of contact paper, or folded newspaper to cover the open areas of the screen.
Make sure that when you place the stencil that the image facing you is the mirror image of what you want to be printed; if you are printing words, the words should appear backwards when you put the stencil on the screen.
Next tape down the stencil. I use masking tape, because it is more water resistant than scotch tape but still peels off of the screen without damaging it. Also cover all of the other areas of the exposed screen. All of the negative space, or open areas of the screen will allow ink to be pushed through. I usually use spare rectangles of contact paper, or folded newspaper to cover the open areas of the screen.
Step 3: Print
Once the stencil is securely on the screen, place the screen, face down on top of the material you want to print on. Make sure that the location of the design is lined up with where you want to print it. When the screen is face down, your stencil, should be flat, directly on the material you are printing on, with the silk screen over it. In looking down at the screen, you should be able to see the image, exactly how you want to print it, through the fabric of the screen. If this is not true, and the image is flipped, you should re-tape the stencil.
After the stencil and screen are lined up, place a line of ink at the top of your stencil and spread it around, making sure to cover the majority of your stencil (I find that spoons work very well for this). Next use the squeegy to evenly spread the ink over the whole deign (taking care to make sure that all the parts of the screen that are not blocked by the stencil are covered with ink). This is called flooding the screen, which ensures that there is ink in all of the open areas of the stencil. Do this by placing one, or both hands on the squeegy and pulling toward your body at about a 45 degree angle. Make sure that when you are doing this, the screen remains stationary (you can do this by either having a friend hold the screen in place, or working on the ground and placing your knees on the frame of the screen to keep it steady).
Once the screen is flooded (there will be excess ink at the base of the screen) repeat the same motion with the squeegy while applying more pressure. This should make a scrapping sound, similar to the sound your finger nail would make if you scratched the screen. Repeat this 2 or 3 times to make sure that the ink has been pushed through the screen onto the material below.
I would recommend practicing this technique first to get a better idea of how much ink is needed to flood the screen and how much pressure is needed to push the ink through the screen.
Next, lift off the screen from the material that was printed on (keep in mind that the material, especially if it is fabric, may stick a little to the screen). Wash off the screen while you let the ink dry. It is important to wash of the screen as soon as possible so that the ink does not dry in the screen (dry ink will block future ink from being pushed through the screen, and will therefore change the design).
Once the first layer is dry you can print on top of the first layer with a different color using the same process if you would like a multicolored print.
After the stencil and screen are lined up, place a line of ink at the top of your stencil and spread it around, making sure to cover the majority of your stencil (I find that spoons work very well for this). Next use the squeegy to evenly spread the ink over the whole deign (taking care to make sure that all the parts of the screen that are not blocked by the stencil are covered with ink). This is called flooding the screen, which ensures that there is ink in all of the open areas of the stencil. Do this by placing one, or both hands on the squeegy and pulling toward your body at about a 45 degree angle. Make sure that when you are doing this, the screen remains stationary (you can do this by either having a friend hold the screen in place, or working on the ground and placing your knees on the frame of the screen to keep it steady).
Once the screen is flooded (there will be excess ink at the base of the screen) repeat the same motion with the squeegy while applying more pressure. This should make a scrapping sound, similar to the sound your finger nail would make if you scratched the screen. Repeat this 2 or 3 times to make sure that the ink has been pushed through the screen onto the material below.
I would recommend practicing this technique first to get a better idea of how much ink is needed to flood the screen and how much pressure is needed to push the ink through the screen.
Next, lift off the screen from the material that was printed on (keep in mind that the material, especially if it is fabric, may stick a little to the screen). Wash off the screen while you let the ink dry. It is important to wash of the screen as soon as possible so that the ink does not dry in the screen (dry ink will block future ink from being pushed through the screen, and will therefore change the design).
Once the first layer is dry you can print on top of the first layer with a different color using the same process if you would like a multicolored print.
Step 4: Done!
In making multicolored prints, you can either paint on the color in blobs before you flood the screen, or you can create a stencil for each color. When you make multiple stencils, keep in mind which colors are lighter, and should therefore be printed first, and the alignment of the stencils when you are making them and while you are printing. This method, while more complicated than painting on the color in blobs, allows you to contain the color and create defined lines between different colors.
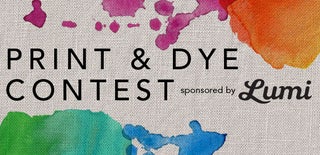
Participated in the
Print & Dye Contest