Introduction: Shade Sails , Howto Alter,make and Install
Hi , I needed an alternative to umbrellas with a heavy concrete base , that kept falling over in a high wind .
I live on the windy island of Crete, in Greece , I had already constructed my swimming pool and needed cover from the hot sun . I found these shade sails at a good price from the UK , a company called Primrose .The sails are called breathable knitted Koookaburra 10 year gtee.
Alas the pool dimensions did not fit the metric sizes of the shade sail, so my only option was to alter the sails , by unpicking one side on a triangle shade and re-machining it . The material is called HDPE 340 gram/per sq metre weight , and I found you can sew it on a domestic sewing machine with a no. 110 needle or a denim needle , the thread most suitable was the invisi thread , transparent nylon.The sails are all metric measurements , and it is necessary to add about 33centimetres for the tensioners, (called turnbuckles ) for your fixing points spacing .If you dont tension the sails in all dimensions they will flap and ultimately fail , the can rattle the turnbuckles and undo them , and then cause havoc by flapping around everywhere .the next step will show you materials needed and some dimensions for the tensioners.I say you can machine these up on a domestic machine , that is 3 layers of HDPE and a re-enforcing tape , but where the two come together at the "D" ring you are looking at around 10 thicknesses of material , thats best done by hand with a sailmakers needle , but does not take long .
Every one of these sails has been restitched to fit snugly
Step 1: Materials and Tools Required Step 1
1 a good domestic sewing machine , some invisi thread, or coloured nylon suitable for sewing machines, or tough bonded nylon in different colours from Ebay
2 some open weave strong tape about 4 centimetres wide for the re-enforcement in the hem
3 the HDPE knitted material ...or a ready made oversize sail
4 Fixing tensioners , a variety shown here in the photo
5 if you want to make your own sails you will need inox ( s/steel) D rings for the corners from Ebay
6 childs washable marker pens
7 Stout wooden uprights , or steel uprights , or a handy house wall , or trees to support the sail(s)
I have included the sail manufacturers guide re sizes etc .
Remember these sails are called tension sails , and boy do they need a fair bit of tension to stop them flapping around in a high wind. You can see the shape of the sail on the ground , its oblong , and at the corners it comes to a point at the D ring , this is so no unwanted bellies occur in the fabric.I have made cardboard templates with a 2cm grid, so you could scale them up and use the on your sails
Step 2: Setting Out the Sail Step 2
OK , maybe you bought off the peg sails like I did and they are slack , because they dont fit to the post correctly , all is not lost . put the spacing of your poles or housewall etc down on graph paper and see if you can juggle the sail to make an adjustment to one length only , thats the quick fix.
If you have purchased some HDPE knitted material the lay it out flat on a surface and with the childs marker , mark out the position of the 3 D rings for a triangular sail or 4 D rings f aor a square or oblong .
You will also notice the D rings are set at the corners and tapered away , I have taken templates of the commercial sails and just go ahead and scale them up, dont forget the pole or fixing position should be half the angle, as explained in manufactures page
The sails will stretch by about 2 centimeters in both directions , allow for this or use smaller turnbuckles than you allowed for .
Using the childs marker pen , pencil in the position of the D rings and the curve coming away from the D ring , and then straight edge to join the ends of the curve up. Next step get onto the sewing machine , and with a loose top tension ,trace rounds the whole shape .I used a contrast white thread that could be unpicked.You can sponge off the marker line now if you wish , it tends to come off on your hands, the work gets grubby.
Step 3: Running the Re-enforcing Tape in the Selvage
OK you now need to run the tape along the seam to re-enforce it and hold the D rings , look at the photos , the tape is continuous all along the perimeter .The pocket or selvage on the commercial sails were 4 centimetres , and I made a cardboard checker to keep an eye on this turnover .You can either machine the tape on the fold line , or machine its outside edge ,and tuck the tape in as you go , the only thing to be careful is the D ring at one corner, in the photo you will see the tape , and about an extra 30 centimeters piece snuck next to the tape , so there are now 2 thicknesses of tape but only at the corners . This is where you may have problems closing the joint , an industrial machine can do the job , but you can too with a sailmakers needle and suitable thread.
I used the 2 poles high , 2 poles low configuration to give a 3D hyperbole effect to the sails , so they look like a ray or bat in flight , they have substance , and the longest run is 6 metres, and this I found could be a problem flapping around , even when they were tensioned up , so I made a halfway tab and anchored it down to a pole , which quietened it completely, see the sand coloured sail in the last photo
Step 4: Useful Kit to Help Install the Sails
Dont forget , even with the knitted sails there will be an immense pressure from the wind on the sail, and if they are not taught , there will be trouble ahead ! . The maximum length of sail on my two triangular sails was 6 metres ex 6m x4.2 m x4.2 m right angled sail . One sail , even though there was ample tension on it , would always want to snap up and down in a high wind , so I pegged it to a support midway along its length , that quietened it down completely .
This picture is of fittings to bolt to a wall or fascia board ,carbiners, rings , and guy wire and cleats for the wire, and closeups of the poles and tensioners
Step 5: Installation of the Sails
here I have scanned the manufactures data sheet to help you decide howto anchor the sails .
Mine , I cut my railings round the pool and inserted 10 cm tubes welded in place, and inside those, 8 cm thick wall galvanised tubes that I could slide up and down to get the effect I wanted bending the sails , but every tube that was taking tension , I needed to guy with a thin steel hawser to counter the pull from the sails .House walls and trees dont move , but unless your supports are very hunky they will bend out of line , mine did , hence the guy cables .
If you have any queries message me here and I will do my best to help
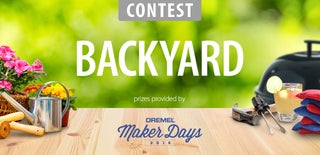
Participated in the
Backyard Contest 2016