Introduction: Silent Omni-Directional Desk Fan
Hello fellow makers,
This is one of those projects that started of as one thing and ended up being something completely different.
I started wanting to make a small spiral wind turbine that would charge up a supercapacitor and after a lot of failed prints trying to print an Archimedes screw, I designed this easy to print rotor.
Unfortunately these didn't work nearly as well as the Archimedes screw but I was still interested in seeing how well balanced it would be so I pushed it onto a motor shaft and hooked it up to a battery...and well I immediately decided it was going to become a desk fan!
Not only is it whisper quiet but it gives a gentle omni-directional breeze.
Join me to see how you can make your own...
Step 1: What You Will Need:
To make your own you will need the following:
- Access to a 3D printer
I used PETG and SBS filament in my build
- Casting concrete mix
- 5v DC Motor
- 6mm I.D. 686 bearing
- 6mm stainless steel rod
- An old USB cable
- Adhesive
- Material for a mold
I used an old tea box for this project
*As an Amazon Associate I receive a small percentage from sales made through provided links at no cost to you, this helps fund future projects.
Step 2: Design and Print:
After many MANY failed attempts I designed this rotor using Fusion 360.
It is made to fit a motor with a 2mm shaft and fits a 6mm rod on the bearing side, scaling the rotor will require you to adjust the hole sizes.
Any printer with a build volume of 140mmX140mmX140mm will be able to print this as there are no crazy overhangs and can be printed with any filament you prefer.
I printed the rotor with PETG for its stiffness and the support arm is printed with SBS which has a very slight rubberiness to it that helps with any vibration.
My print settings are as follows:
Material: PETG and SBS
Speed: 40mm/s
Temp: 250 degC (220 for SBS) Nozzle and 85 degC Bed
Nozzle: 0.8mm but smaller will also work
Step 3: Assembling the Rotor:
Assembling the rotor is really easy.
We start with a 6mm stainless steel rod roughly 100mm in length that I gently tap into the bearing side of the rotor, you want about 8mm left sticking out. The rod should be held in place quite snug but if your printer oversized the hole you can add some adhesive to keep the rod in place.
Next I pressed the 686 bearing into place, again if it is slightly loose you can add some adhesive to hold it in place. I use flanged bearings as they work well for me with these type of projects but you can use the regular 686 as they are less expensive and readily available.
Step 4: The Concrete Mold:
We are going to need a heavy sturdy base for our fan and as always concrete suits this job perfectly PLUS it looks stylish!
I usually print a simple mold for my concrete castings but in this case an empty tea box was absolutely perfect for the base and its free!
I simply reinforced the outside of the box using some packaging tape as I feared it might tear when it got wet, also tape the flaps of the box as shown in the picture as it will keep the sides of the box stiff.
Next I printed out a sleeve that is that fits around the motor, this will give us a neat slot in the concrete to mount our motor.
Simply glue the sleeve into place using some hot melt glue.
Step 5: Casting the Concrete:
Time to cast the concrete.
Following the instructions of the manufacturer mix up a batch of concrete, I like to use old ice cream containers for this.
With your mold placed on a flat level surface start start scooping the concrete into the mold, tapping out the air bubbles as you go. Continue until you reach the top of the sleeve.
Leave the casting to cure according to the manufacturers instructions.
Step 6: Refine the Concrete Base:
The next day my casting was set but still workable....and fragile so be careful.
I removed it from the mold, which simply tore away and then just by hand smoothed the edges and sides.
At the bottom I made a small slot using a skewer just for the wire to pass through underneath the block when it's on a table.
You can now leave it to cure completely.
Step 7: Wiring the Motor:
For this step you can use a new DIY USB plug but as I have lots of old mini USB cables laying around that no longer gets used, I like to repurpose them in projects like this.
I simply snip off the mini USB side then strip off the outer casing to expose the wires.
We won't be using the green and white wires as these are the data wires so I also cut those off, I kept the shielding wire and soldered it to the body of the motor to give some support for the thin power wires.
Strip the ends of the of the black and red wires and connect them to the motor so that it spins anti-clockwise.
Step 8: Assemble the Base:
With the concrete base fully cured it's time to start assembly.
Start by feeding the USB cable through the motor sleeve in the concrete base, next I use B-6000 glue which is a fantastic clear drying glue that's very strong yet it stays rubbery when dry so it will also help dampen any vibration from the motor and rotor.
Smear some glue onto the inside wall of the sleeve and slide the motor into place, you want the motor face to be flush with the concrete base.
Leave the glue to set then you can push the rotor onto the motor shaft, If the rotor doesn't go onto the shaft snug add some adhesive to hold it in place just make sure it doesn't run down the shaft and seize the motor.
Step 9: The Finishing Touch:
The final step is to attach the support arm of the rotor.
I use a 2 part CA glue as it seeps into the concrete slightly and creates a really strong bond.
Smear some CA glue onto the bottom of the arm, slide push the rod of the rotor into the bearing and then position the arm onto the base.
Because this is a 2 part glue it gives me time to adjust the positioning of the arm to make sure it is straight and the rotor spins freely without wobbling.
Once you are happy with the position of the arm you can spray some activator onto the joint to set up the glue.
Now you can go ahead and plug in your fan and test it out!
Step 10: Enjoy!
Because of the gentle omni-directional airflow created by the fan it is a great addition to a buffet table to keep any pests away.
I hope you guys enjoyed this Instructable and if you have any questions please feel free to leave me a comment bellow.
Please share your own creations with us by clicking the "I Made It" button below.
Happy making!
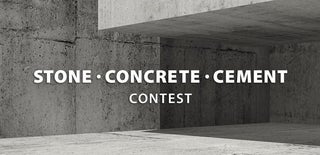
Runner Up in the
Stone Concrete Cement Contest