Introduction: Simple Rotor Balancing Machine
Hello everyone.
This machine was made to help my friend with rotor balancing process. The principle that used in this machine is that we reading misbalance/vibration from the accelerometer only from one axis, Y axis on the accelerometer in this case, this gives us a sine wave. We're getting this sine signal and firing the LED strobe only on the wave peaks, that is how we detect the heaviest point on the right and left plane. By numbering the sectors on the rotor, we can understand which one requires balancing. Oscilloscope, that added to this machine, helps to understand information about rotor under the test, maybe it's ok and doesn't require balancing at all.
Note: Oscilloscope was made by Peter Balch in his very nice Instructable, so I'll not be doing lots of copy/pastes from his article.
Supplies
• 2 x 500mm SBR12 linear rails, like these with bearing blocks on Amazon
• 4 x SBR12UU Bearing Blocks
• 690mm of 20x20 aluminum profile (cut on pieces 230+230+230)
• 14 x M4 T-nuts for 2020 profile series, better to have a set of such with different sizes
• 8 x M5 T-nuts for 2020 profile series
• 8 x M3x20 screw with cylinder head
• 40 x M3 locking nuts
* 10 x M3 nuts
• 4 x M2x20 screws
• 12 x M2x8 screws
• 8 x M3x20 screws with a conehead
• 12 x M4x10 screws
• 8 x M5x10 bolts
• 8 x M5 T-nuts
• 8 x M5x15 bolts
• 6 x M5x20 bolts
• 2 x M6x20 bolts
• 2 x M6 nuts
• 4 x MR148 bearings
• 16 x MR63ZZ bearings
• 50cm of 8mm linear rod
• 2 x LM8UU bearings
• 140mm TR8 8mm lead screw
• 1 x TR8 Nut for the lead screw
• few GT2 timing belts with 572, 800, 848, 900 teeth
• 1 x 2GT-20 teeth timing pulley for the motor with bore 5mm
• 2 x 2GT-20 teeth pulley with 5mm bore
• 4 x 2GT no teeth pulley with 5mm bore
• 3D printer with engineering plastic, like ABS
Electronics:
• 2 x GY-61 analog accelerometer based on ADXL335
• 2 x switches with On-On mode
• 3 x Double Sided Prototype PCB 4*6 cm
• 1 x 775 motor
• 1 x 12Vx5A power supply
• 1 x DC motor RPM regulator, like this one from Aliexpress
• soldering iron, soldering supplies, and related stuff
• oscilloscope that mentioned above
Step 1: Models to Print
This step has attached STL files that needs to be printed. All details, except listed below, have to be printed in 1 copy. I've printed all parts with EngineeringABS plastic, which has
You'll need to print multiple copies for:
2 x BrakeInsert.STL
2 x BrakeHandle.STL
4 x Leg.STL
2 x RockerHolder.STL
4 x Rocker.STL
2 x RockingBase.STL
Attachments
DisplayHolder.STL
Bearing_MR148_right.STL
Bearing_MR148_left.STL
RockingBase.STL
Rocker.STL
RockerHolder.STL
Motor_holder_ver2.STL
BeltTensioner2pulleys.STL
HeightLockerHandle.STL
BrakeHandle.STL
Roller holder.STL
RightSideBracketMovingPart.STL
RightSideBracketTop.STL
AdjustingWheel.STL
RightSideBracketBottom.STL
BrakeInsert.STL
LeftSideBracket.STL
RegulatorHoudingCover.STL
RegulatorHouding_bottom.STL
HosingStrobe_rev2_Bottom.STL
RegulatorHouding_bottom.STL
HosingStrobe_rev2_top.STL
RegulatorHoudingCover.STL
Leg_v2.STL
Step 2: Wiring Diagram With Strobe and Oscilloscope
This simplified version off the machine schematics gives an understanding how the signal switched between accelerometers and output sources (strobe or oscilloscope)
Step 3: Electronics…
Because accelerometers doesn't provide the enough power to flash the LED, we have to amplify the signal to flash the LED. This operational amplifier built on LM358 chip and has adjusting resistors to tune the sensitivity of the signal reading which comes from the accelerometer and flash the LED on the exact "sine top".
There are lots of schematics for the operational amplifiers on the web, this amplifier using the SMD components, to save some place and it is much easier to create PCB.
Wires between accelerometers and switches are shielded, I used old USB charging wires from the old electronics.
DC motor power regulator does'n require much words, it comes already assembled and requires to connect only power source and motor.
Step 4: Installing the Brakes
On this step we have to take a couple of bearing blocks and replace bearing with printed inserts, which will be taking a role of the lockers for the bracket on the rails. Place the bearing blocks to the bottom of the brackets and tighten with M5 bolts.
Step 5: Handles
There is not much to say about handles and cranks. Just print them, insert bolts/screws and lock them with nuts. And it's done!
Step 6: Assembling the Right Bracket
This step contains detailed set of images to assemble the right side bracket.
This bracket has different construction, because not all rotors has similar diameters of the axels on each side, so it have to be adjustable to compensate this.
so…
First of all we have to push the nuts into the adjustable top. Then snap the LM8UU bearings to their places. Then thread through the bearing the linear rods and check that part is mowing smoothly with no jams. After this a nut for the lead screw with M4 bolts have to be inserted to the top. After this bottom and top part have to be connected tightened with bolts. Do not for get to check that parts are still moving smoothly. Insert the lead screw and lock it with M3 screw in the adjustable/moving top part. Done.
Left bracket assembly doesn't requires such steps, it has more simple construction.
Step 7: Assembling the Suspension
This step is very important and from success of this step depends the sensitivity of the whole system.
All strings from the plastic details, have to be removed. Places for the bearings have to be clean.
There is an extra lip on the outside side of the bearing places, to avoid bearing from falling out, so bearings have to be inserted inside out. After bearing inserted it have to be locked with the M3 locking nut.
NOTE: Locking nut have to be used with locking ring closer to the bearing. This will help to lock the screw without any friction between plastic detail and nut. After assembly all parts have to perform rocking movements freely with almost no friction/resistance.
See series of photos for reference.
Step 8: Belt and Pulleys
This step shows the belt schematics with pulleys and tensioner mounted on the aluminium extrusion.
Step 9: Frame
Assembling the frame doesn't require much time, but rails on it have to be parallel. I've used SBR12 rails that has predrilled holes. to squaring the frame much easier. All that needs to be done, take a rail, and one piece of the 2020 profile and tighten with bolts perpendicularly to the SBR12 rail. repeat the same on the second side. After this put the second rail on the profile and do not tighten the screws. Put the both brackets on the rails with some gap, as shown on the image, and tighten the screws. Check that brackets can move across the rails with no jams. There have to be reasonable resistance, because of the brakes inserts.
Step 10: Test Run and How to Operate
Once you get assembled all parts together, it's nice to check how it works. On the picture, attached to this step I've took the magnet and sticked it to the one side to cause misbalance. Adjusted the RPMs and… as you can see, we're getting the sine wave on the oscilloscope screen. It means that we're doing everything correct.
This step contains a video of the test run with short demo. It has no timing belt used yet and ran on a simple rubber band. On video it runs in 0.1V and 10ms frame, so only half of the wave is visible.
Step 11: Cable Management
Here are some models to help with cable management and LED holder.
Attachments
Step 12: Cable Management and Final Result
After organising wires, device looks much nicer with no wires hanging around.
Thank you for reading!
Step 13: Improvements and Upgrades After Use
After some time to being used in fields, my friend requested some changes, that significantly improved the work of this machine. All models to achieve changes are attached to this step.
#1 We've replaced the metal bearings with V shaped Nylon parts. That improved the sensitivity of the whole machine and "noise from the metal bearings" on the sine wave has disappeared at all.
#2 Changed the construction of the top rocker to allow balancing for the rotors that has cooling impeller installed close to the axel end, like on the attached photo. So now it's possible to balance any rotor.
#3 Replaced timing belt with elastic drive and using the flat stationery rubber loops. As result the new motor pulley was made and attached to this step.
#4 Redesigned LED reflector/holder, now it gives more focused light spot.
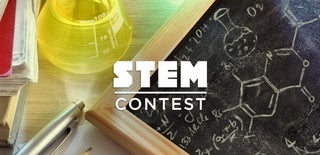
Participated in the
STEM Contest