Introduction: Skyrim Town Guard Shield
Welcome everyone, to my first ever Instructable! My name is George, and I manage the NYDesigns FabLab in Long Island City, NY. It’s a 5000+ square foot space loaded with all the equipment you might need for even the most ambitious DIY projects, and we are always looking for new members to join our community.
For this first instructable, I had the chance to do something that I’ve wanted to do for a long, long time: Making props. I’ve always loved Skyrim, and Whiterun/Riften feel like second homes for all of the time I spent there, so I figured why not remake the shield of our favorite protector of sweet rolls?
Step 1: Materials
While this instructable isn’t meant solely for members of our FabLab, it does require access to both a laser cutter and cnc. Ours are huge (51” x 51” and 4’ x 8’ respectively) so I did everything in one piece, but there’s nothing to stop you from breaking up the project into smaller pieces.
So with that aside, for this project you will need:
A 30” x 30” x ¾” plywood sheet:
This will be the main “body” of the shield, providing structural support and encircling the “face” of the shield with a rim that will be finished to look like metal. It doesn’t particularly have to be plywood, all the outwardly visible parts of this piece will be painted to specifically not look like wood, but plywood is strong, cheap and not particularly heavy. For reference the final weight for my shield was 3.5 pounds.
One or Two 30” x 30” x ⅛” plywood sheet:
This will be the front “face” of the shield. Whereas the other sheet will be made to look like a metal rim, this sheet will be the outward facing central planks you see in the image of the shield from the game. This is done not to make your life harder, but because we need a prominent wood grain to be facing forward that can be made to create the illusion of multiple distinct planks.
Ten #8 x ½ wood screws
These screws are used to affix the 3d printed handle and optional leather arm strap. You need 4 for the former and 6 for the latter. These are just barely short enough that they won't poke through the surface of the shield face once everything is together.
Access to a 3D printer
I had my own handle done with solid infill from our Stratasys ABS printer. After a lot of testing and swinging the shield around, I’m confident it will hold up to years of use. Prints from a home 3D printer should be the same, although I’d suggest using PETG at 50% infill or more if your machine can handle it. Alternatively, feel free to get creative and make a more authentic handle out of wood, metal or some combination thereof.
Can of Rust-Oleum 2-in-1 Filler & Sandable Primer Spray (Color Doesn’t Matter)
This stuff is really just the best. Much like Franks Red Hots, I put that $#!t on everything. I discovered this stuff while trying to find a way to get rid of the lines of a 3d printed part, but in this case we are using it to hide the wood grain and flaws in the ¾” plywood.
Can of Rust-Oleum Forged Hammered Metallic Spray Paint/Primer (Antique Pewter)
So technically I actually used Rust-Oleum Flat Iron Metallic for the yellow (Whiterun) shield on the left. It was the first of the two shields I made and I didn't have the Forged Hammer spray at the time. My biggest critique of that build is that the rim looks too new compared to the rest of it and I think that this textured paint would go a long way towards making it look like something a Skyrim blacksmiths could mass produce.
The second shield (Riften) on the right had the rim painted with the forged hammer spray-paint and came out with the look I was hoping for, but please feel free to pick whichever you like better.
Can of Rust-Oleum Canary Yellow Gloss Spray paint/primer
Now, I know what you’re thinking… Canary yellow, and gloss no less, does not sound remotely like something from Skyrim… but it worked out well as the primary color for the Whiterun shield, and the secondary color for the Riften shield.
Can of Krylon Fusion Satin Lavender
I know, another not-very Skyrim color, but that’s what it looks like/the wiki calls for. This is the primary paint color for the Riften Shield.
Can of Rust-Oleum 2X Ultra Cover Matte Clear
The matte finish helps subdue the gloss of the yellow, and protects all the painstakingly added artificial scuffs, dings & weathering from real world scuffs, dings & weathering!
Can of Minwax Wood Finish Aerosol spray, Red Mahogany color
This is used to stain the ⅛” plywood, and we do it for two reasons. The first is that the veneer on the top surface of most plywoods has a very subtle grain pattern to it, and with this stain you can really get the grain to pop out; and the second reason is that we want the plywood to look like it is actually a much more sturdy variety of hardwood. I liked the mahogany red because it reminds me of the old growth redwoods near where I grew up, they were so huge and just seemed to personify strength and durability. What better choice could there be for something that’s supposed to protect you from taking another arrow to the knee?
Miscellaneous Supplies
- Wood Glue
- Blue Painters Tape (the wider, the better)
- Assortment of Sand Paper
- Clamps
Step 2: Pick Your Hold!
For my first attempt I did Whiterun (Center) but for the majority of this Instructable I will be working on a Riften (Left) shield, but regardless of whichever Hold (Except Hjaalmarch, that one won’t work with this project) you want emblazoned on your shield, this page on the skyrim wiki is a great place to start. Get the full sized image and download it to your computer.
Step 3: Getting Your Emblem
The intent of this step is to get your emblem isolated from everything else, make it pure black and then clean it up (optional).
What you need to do is open up your saved shield image from the last step and open it in Illustrator. With the shield selected you want to go into Options > Live Trace > Tracing Options. Settings will vary depending on the shield, but you want to do your best to get your emblem as complete and isolated as possible. My settings for the Riften Shield are in the screenshot above.
From there, I took the result to Photoshop, inverted the colors (in this case) and cleaned it up. As mentioned before, beyond a minimal amount of cleaning it isn’t necessary to do what I did, essentially reconstructive surgery, because I wanted a much crisper look.
Note: For the Whiterun shield, I upload the image into Autodesk Fusion 360 as a canvas to be traced using the sketch feature; Sketches can be saved as a DXF file which you can open in illustrator as a vector. This is not how I will be continuing with the tutorial, but for those interested, you can find a general tutorial about inserting/scaling canvases here, and this will also work for the next step.
Step 4: Outlining Your Shield Face
The shield face consists of the ⅛” plywood, which we are going to use a laser to cut into 5 segments that jointly make up a circle. To do this, we continue from where we left off with the photoshop file.
The emblem should be on one layer by itself, and you want to create 3 additional layers. One will be for the circular rim of the face, another to break up the circle into individual planks and the last one is for a copy of the original image you first created.
Start off by opening your original shield image (unedited) as a separate file, and drag it into your existing file, making sure that you have one of your empty layers active. I made this my first layer, turning the opacity to 25% and scaled/positioned it so that it was centered on my edited emblem.
In the next layer, I used the elliptical marquee tool, while holding shift to make sure that you get a perfect circle, create one that roughly traces the inner rim. Don’t worry that it isn’t spot-on, we will be sizing it later. Once you have it centered around the emblem, right click inside your circle and select “make work path.” Use the pen tool to stroke the path with a pixel width of 10 to 20, making sure the color turns out a solid black.
In the final new layer you are going to trace each edge between the wooden planks using the pen tool. Make sure that both the beginning and end of the line are outside the circle; it’s important to do this or the laser won’t cut properly. Obviously you can’t see everything, so just do your best and make it straight, but flawed; I only used the planks in the picture for a reference and decided to center them a bit more. Stroke all paths when you finish, making sure they are together in one layer apart from everything else.
Step 5: Bringing the Shield Face Together
At this point, the shields face is done, but it needs to be made ready for a laser cutter. Save your file in photoshop as a photoshop document, and then open it up in Illustrator. It’ll give you some options, just make sure that layers are saved as objects. You now need to select each layer/object individually except for the low opacity copy later and (the circle, the emblem, the plank edges) go through the process of live tracing them. This time, though, make sure to select to ignore white spaces for all of them, as well as have the “stroke” option selected for the plank edges. The latter is needed because the lines look all jagged and unnatural otherwise.
Now it’s time to scale our shield face to the final dimension. Delete or hide the layer with the original image (It’s just for reference now) and select everything. And after selecting everything you should see something like the image above.
We now have to decide how big our shield will be. I want a 24” shield with a 2” rim so I should set the Width and Height to be 22,” but as you can see I made them 22.01. I did this because as tiny as a laser is, it still has some width to it, and a 22” circle on a computer would end up very slightly undersized in the real world. 22.01” works out as a nice snug fit with some sanding to final dimensions.
So at this point the file is the right size, but what about colors? This will vary if you are not working with the 51” x 51” Trotec laser in our FabLab, but for our machine we generally want to use pure RGB colors to separate tasks for the machine. So I’m arbitrarily deciding RGB Red (255, 0, 0) will indicate cutting and RGB Black will indicate engraving. Have the circle and the plank edges set to red for cutting, and the emblem set to black for engraving.
We’re close to done now, the final step before taking this to the laser! All we have to do is change the stroke weight of the circle and plank edge objects to be .001. This makes them into what the machine will recognize as a vector. And that’s it, you’re done! Go ahead and save that as an illustrator file to a USB stick and take it to your laser, but don’t go just yet, read the rest of the guide first!
If you’re making this at home, there may still be some work to be done, such as dividing the file into smaller pieces that your laser can manage, or working with line width or coloration to satisfy the software your laser cutter uses.
Step 6: Cutting Your Shield Face
We don’t want to engrave yet, just cut out the circle and the planks. This won’t mean much to anyone outside of our fablab, but I cut at 100% Power, 1.5 speed and 1000 PPI.
One thing to note is that, despite the plank cuts separating the shield face into 5 segments the grain still makes it look like it is all from the same piece. To get around this, i did two sets and switched out the 2nd & 4th sections. If you can’t afford a second sheet of this plywood, try breaking the file down into individual planks and cutting the wood from different angles for each plank.
The edged are going to be charred black, but don’t worry about it, this actually helps with what you need to do next. Take each piece and use some sand paper or a blade to bevel the top edge along the length of every plank cut; that’s a total of 8 edges. You should aim so that the bottom half remains blackened and the top half has been fairly aggressively sanded. This will further help each wood “plank” look like it’s from different trees.
It is very useful at this point to glue all the pieces back together. We will be breaking them apart again, so just use wood glue. I used the tip of a pen to run along the cracks to keep any glue from showing between the beveled edges.
Step 7: Staining
Now gather your shield face and your bottle of spray on wood finish. Make sure you have the side with the beveled edges facing up and follow all safety instructions. In regards to application, I spray it on fairly thick in one go, and then take a cloth rag and wipe off as much as I can after letting it sit for a few minutes; I found this helps keep the wood grain really stand out and become more visible.
This takes a long time to dry properly, so make sure to have it set up somewhere that it's ok to sit for a while.
Step 8: Primary Paint Job
Once the finish dries, it is time to apply the primary paint job. It’s important to remember that you are not going for full coverage of the entire shield face, maybe 90% at most. I applied the spray paint in multiple, thin layers and with each layer I went closer to the edge until I was at a distance I was happy with. After that, because it looked like it was spray painted on, I used a brush while the last coat of paint was still wet to texture everything. Between doing this, and moderately sanding the edges of the paint in a bit you can get a very nice look.
Step 9: Masking With Painters Tape
After waiting until the paint was completely dry, I carefully covered the entire face with blue painters tape, being careful to align the edges of each piece of tape so that there was no overlap. Even so, I was concerned about paint getting through small gaps as I had seen in test pieces, so I added a second layer of transfer tape. This tape isn't very adhesive and was terrible to work with. In hindsight I think it was excessive and do not suggest it, and if you insist on a second layer, use the painters tape again.
With that set, it’s time to go back to the laser and etch our emblem. The idea here is that we will be essentially burning the tape away, spray painting over the exposed parts and then removing all the tape.
I started by spreading a large sheet of paper over the laser bed, and cutting out a circle using the same shield face file from before. We don’t need to cut the plank edged again, so hide that layer, and print the file to the laser using the same coloration as before. Set the laser to ignore black (the emblem) and proceed to cover the laser bed with a large sheet of paper. Cut the outline in the paper and use it to accurately place your shield face on the laser.
Now etch your emblem. For this Riften emblem it took just over an hour to complete. The settings I used were 30 power, 50 speed and 1000 PPI.
Between etching the emblem and spray painting over it, make sure to apply pressure to the tape around where it was burnt away. Failure to do so will allow paint to seep under the tape. Spray as many layers as you want to match your taste and after the last layer let the paint dry for 1-2 hours before using some tweezers to start removing all the tape.
Once completed, use a blade to run between the plank edges and then gently apply pressure to each plank edge and separate it into the original five pieces. Very lightly sand the plank edges and store the pieces away until final assembly.
Step 10: Modeling Your Shield Body
The face is done, now we need a body. Open your 3D modeling software of choice and create a sketch. Draw one circle that is the diameter of your Shield Face (Remember, the .01 we added was to plan for the laser kerf), so in my case it was 22 inches. I then made a second concentric circle that would be the full size of the shield, 24 inches.
While you’re at it, plan out your handle placement. I have a 3D printed handle towards one end of the shield affixed by 4 and 4 holes around the center of the shield for an arm strap made of scrap leather. However you want to do it is up to you, but make sure to create a pocket for your screw heads so that it won’t get in the way when we do the final assembly.
Extrude your inner circle to .23” and the outer rim to .625” and chamfer/filet the rim to get a rounded point. Alternatively you can also shape the rim by hand afterwards if you don’t want to go through the trouble of programming the CNC for curves. I used Fusion 360 for both the CAD & CAM aspects of this project.
Step 11: Making the Shield Body
Once you’ve machined the body, work on sanding the rims as smoothly as possible, as well as filling in any splinters or gaps with glue or wood fill. After everything is dry and smoothed, I applied three coats of Rust-Oleum 2-in-1 Filler & Sandable Primer, lightly sanding in between sprays. By this point the rims shouldn’t look overtly like wood any more and you are good to apply paint. Don’t worry about getting any in the center and just focus on getting the rims well covered.
Step 12: Handle & Armband
By now, we’ve completed the body and the face for our shield, the last thing we need to do is make our handle and we can assemble everything.
I started by going back to my Fusion 360 file and built a basic handle around hole layout I created, make sure to model the holes too or else the print will crack as you install it. I printed it on the FabLab’s Stratasys U-Print with solid infill out of ABS plastic.
It is remarkably sturdy. I would have no doubts that it would stand up to the days of constant use at a convention. All the same, it didn’t feel quite right without the arm strap; The final product weighs 3.5 pounds so it’s a bit much for my wrist to support on its own.
I ultimately did not spent much time finishing the backside of this shield. I was worried that any paint finish would end up on my hand or arm and it’s not like the majority of people will see this side of it anyways.
Step 13: Final Assembly
Now, finally, it’s time for final assembly. Install your handle first, but not the arm band (if you have one). Due to the nature of the design, the handle can only be installed before the shield face is, or otherwise I'd install that afterwards as well. The #8 x ½ wood screws listed in materials were perfect for this.
With the handle installed, lay the shield body with the rim facing up on a table with the handle hanging over the edge. Take the shield face pieces and do a dry test installation. Most likely you will need to do a fair bit of sanding. I sanded mine until I got a nice snug fit, and then began to glue my face pieces one by one to the body while making sure that none of the pieces warped. For some I very lightly used clamps, but if you didn’t oversand on the test fit, the friction of the rim held most of the pieces in place after the first corner piece.
Take care to align the shield face relative to your handle. It isn’t something very apparent at this stage, but you can very easily install this upside down or at a weird angle. I suggest holding the handle in your arm and then mark the top with a piece of blue painters tape on the rim.
To finish up, generous apply a few layers of protective matte clear coat, install your armband, and you’re done!
Step 14: You're Done!
Thank you for taking the time to look over my Instructable! I hope you enjoyed it, and I welcome any feedback about how I can do my next one better.
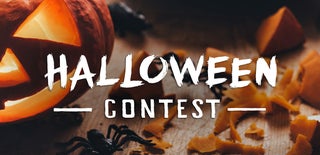
Participated in the
Halloween Contest 2019