Introduction: Small Garden Table - Automotive Theme
A small garden table constructed from some old alloy Wheels and an old table leg.
My original Idea was to create a JDM (Japanese Domestic Market) styled table, from that point of view it came out great.
it's a simple project, but I found it very messing making as it requires a lot of careful angle grinder work.
Definitely need a mask, goggles and hearing protection.
If you have all the parts the project can be completed in a morning, I had to wait for the fixings, this gave me chance to get most of the work done before they arrived.
Feel free to ask any questions, I've tried to include as many useful comments as possible.
Step 1: Major Parts
Up-cycled Items
This table is built 99% from old previously used parts that have been brought together.
The items I used in the build for this table were:
- Two old two piece alloy wheels.
- An old corporate acrylic advertising sign.
- Chromed table leg from a kitchen table. (some form of pole, old exhaust etc).
- Feet from a desk.
Two piece alloys are good because they can be unbolted and turned around and cut to make narrow table sections.
Some form of top I used an old corporate sign that had to have the logo peeled off with a heat gun, if you have the skills a bonded glass top could be used or even wood or aluminium.
The chromed table leg was something I found from a long gone table, an old exhaust pipe could also be used as could a piece of wood.
Feet from an old office desk, these could be new.
Bought Items
I also had to buy a few items to put it together and I chose stainless steel fixings as I intend to leave the table outside.
- Counter sunk M8 x 40mm stainless steel bolts
- Button head M8 x 40mm stainless steel bolts
- Stainless M8 Nyloc nuts
- 4 Connector nuts.
- Rivnuts
- Double sided foam tape
Optional
- Pipe clamps and bottle opener. :)
Step 2: Build Plan and Tools
Build plan:
Function – I wanted the table to be useful, this meant it had to be a good height and be level and the correct kind of size.
Form - I wanted it to be pleasing to the eye, and themed.
Durable – Be able to withstand at least some of the elements when left out in the garden.
Build – Be able to fabricate with tools available.
Function
I started by deciding how I wanted the table to function, I sat on a chair that I planned to use with the table and created an approximate measurement with a tape for the height, this was about 600 – 700mm
Using the alloy wheels and the old metal table leg I arranged these in-line on the floor and confirmed 700mm height was possible.
Form
The items I had choosen were ideal, I wanted this to be a JDM or Japanese Domestic Market occasional table, that meant the wheels I had selected were JDM wheels, I also wanted to to be a bit jaunty so included the corona bottle opener...
Durable
I selected all stainless steel fixings and all of the components were commonly found exposed to the elements or a harsh environment apart from the table leg itself (hopefully this will stand the test of time as it's chromed). So I was confident It would last.
Now I was confident the table was obtainable from the collected materials and would have the desired look and be long lasting I started work on the build.
Tools used in the build:
- Cordless drill
- 8mm Drill bit (Long)
- Counter sink bit
- Centre punch
- Hammer
- Lathe (Not necessary)
- Sanding wheel
- Angle grinder (with thin 1mm cutting disks)
- Allen Keys
The tools used in the build are general hand tools, and depending on your project may change.
I did use a lathe to cut some slots in two M6 cap heads for mounting the cap catcher, but this could have been held on in many ways so that is definitely optional.
Step 3: Build
Build
I first started on the base, I was planning to build up from the ground, so I wanted to build the base first.
I started by turning the wheel centre around in it's rim so the wheel centre part of the wheel was effectively pointing to the deep side of the wheel rim, basically the wrong way around if it was to be fitted to a vehicle, this gave a nice skirt for the base of the table, but left a tall basin / dish, as I was happy with this skirt I cut the dish of the wheel from the rim using an angle grinder and cutting disk.
I cut around the bolt lip of the wheel, you can see where the bolts are in the picture.
After cutting the wheel
I could bolt the bottom part of the wheel together to form a base.
This took quite a while as the wheel has quite a few fixings.
I also chose the button head fixing for the base.
Base
When I was creating the base I wanted it to be slightly clear of the floor as I thought the aluminium could make quite a mess of my slabs so I used some M8 connector nuts and screwed the old office furniture feet into them.
This gives enough clearance and stops heavy scratching and marking of the slabs.
Step 4: Build 2
Build 2
Now the base was finished I needed to install the table leg, the leg was a little big for the wheel centre so I used a sanding wheel to open up the bore of the wheel.
This was pretty straight forward but made the drill very hot!
Once I got the pole into the wheel I drilled a hole diagonally through the wheel and tube and put a bolt in to hold the base and leg in position, I did consider using epoxy, but thought it would struggle to bond on the chrome.
Building the top
This required cutting another wheel rim in half, as I wasn't sure how I wanted the top I left a little lip on the wheel when I cut it. After trying a few arrangements I decided I liked the lip and left it as part of the top.
After cutting the wheel in half I used the wheel to mark out where I needed to cut the Acrylic, I cut the Acrylic using the angle grinder, this was really messy if you have access to a bandsaw that would be a better way of cutting it.
The Acrylic also needed quite a bit of finessing to fit well I did this using a bit of sand paper.
The double sided foam tape was then placed as a gasket between the metal of the rim and the acrylic top this stuck them together (permanently) and I used this so the Acrylic wouldn't crack as I tightened the fixings in the top (later).
This may be better without sticking it completely as I couldn't then remove the Acrylic, this wasn't a huge problem but would have been easier if I could have removed the top.
Next drill the holes using the wheels existing bolt holes as a guide so the fixings can pass through the Acrylic.
After doing this the inner part of the second wheel was offered up to the pole (this would form the support for the top of the table and the sanding wheel was used again, this time after the wheel was a good fit I drilled the pole both sides and inserted nutserts, this was because this arrangement might be visible through the top of the table and I wanted it to look as good as possible.
After installing the wheels centre part I then finished of the wheel rim / Acrylic top by countersinking the holes in the alloy rim to accept the M8 countersunk fixings.
This would be easier to do if I could have removed the top.
Step 5: Final Flourish
Final Flourish
Now the top was installed, the table was essentially finished.
As a final flourish I decided to install a bottle opener that was laying around in the garage, so I used some mechanical hose clamps the type that use an allen bolt and installed the opener using some long bolts and spacers, I also had to make a mount for the cap catcher, I used my lathe to cut some slots in some M6 stainless capheads as a mount.
This mount could have been achieved in all sorts of ways, I just used the tools I have.
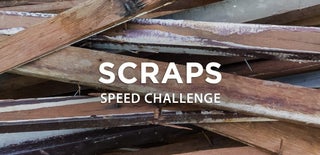
Participated in the
Scraps Speed Challenge