Introduction: Solar Concrete Gothic Window Lamp (Remix)
Hello everyone,
Last year during the concrete contest I came across Yueshi's Concrete Cathedral Night Light on one of the newsletters and instantly fell in love with it.
The only problem was they were too beautiful to just make one!
I wanted an easier way to make several to scatter throughout the house and to give as gifts (p.s. If you know me you're probably getting one for Christmas)
So off I went using Yueshi's Instructable as inspiration I decided to 3D print a mold that was then cast in silicone to produce a long lasting easy to use method to cast multiple concrete "bricks".
With electricity being such a scarce resource in my country I also decided to make mine solar powered using supercapacitors as the energy storing device instead of a regular battery, but I will also show you how to make it USB powered.
Let's get started...
Step 1: What You Will Need:
To make this Instructable you will need the following:
I have included amazon links for reference to similar products.
- Concrete mix
- 5v LED USB Strip
- Access to a 3D
- Sanding paper
- High fill primer
- Glue eg. hot melt, CA, epoxy
- Formwork material eg. cardboard, poly carbonate, foam board
- Modelling clay
Optional:
- Silicone
Amazon - Platinum cure silicone
Solar:
- Solar cell
- Supercapacitor
Amazon - 10F 5.5V Supercapacitor
- Transistor
- Resistor
Step 2: Initial Build:
The first one I made I used just a 3D printed mold and I got a really nice result from this, unfortunately I was a little impatient and had to destroy the mold in order to release the "brick".
As I didn't want to have to regularly reprint the molds I decided to spend a little more and make myself a silicone mold and so far I made 3 and it has worked flawlessly.
I will include the file for a 3D printed mold if you don't want to go through the extra hassle to make a silicone one.
Step 3: Design and Print:
Everything was designed in fusion 360 and I have included the F3D files so that you can change the design to your liking.
I have made the window pane a separate file as this makes it easier for you to create a few different designs or even create some interchangeable ones!
I've printed mine in PLA but if you use the 3D printed mold instead of the silicone mold I would suggest printing in something a little more durable like PETG.
Print settings:
Mold outer + inner ( 3 parts )
Nozzle: 0.6mm
Material: I used eSun PLA+
Temp: 220 deg C
Speed: 50mm/s
No support needed
Window pane
Nozzle: 0.4mm
Material: I used eSun PLA+
Temp: 220 deg C
Speed: 30mm/s
No support needed
Back cover
Nozzle: 0.4mm
Material: eSun TPU
Temp: 215 deg C
Speed: 30mm/s
No support needed
You can print this with other filaments too I just prefer using TPU as it allows you to just pop the back into place.
Attachments
Step 4: Prepare Your Mold:
When you're done printing the 3 parts needed to make the mold we need to assemble them and get rid of those pesky layer lines.
First you need to glue the "main frame" to the "mold outer".
I used 2 part Cyanoacrylate glue ( Super glue ) to glue them together, just make sure they are properly aligned on the inside.
Next I sanded both parts with some 220 grit sanding paper to get rid of most of the layer lines and to give the primer a coarse surface to adhere to.
Now remove sanding dust and give both parts a nice thick coat of high filler primer.
When your primer is thoroughly dry sand away any imperfections with 400 grit or finer sanding paper.
When you are happy with the look of your mold you can move onto the next step.
Step 5: Casting the Silicone Mold:
Now with our mold prepped we can get ready to cast the silicone in it.
First I take a clean pane of glass, then I roll out some modelling clay onto the glass that's just bigger than the mold inner and about 5mm thick.
Now press the mold inner into the clay and remove the excess clay around the inner.
This will hold the inner in place and prevent the silicone from filling it up.
Next position the outer mold over the inner and centre it.
I used hot melt glue all around the outer to keep it in place and seal it to prevent silicone from seeping out.
Silicone:
In this instructable I'm using 25 shore A 2 part RTV silicone mixed in a 100:3 ratio.
It is very important that you follow the manufacturers instructions EXACTLY, if this is your first time using silicone I would highly recommend rather using platinum cure silicone as oppose to RTV silicone it's a little more expensive but much more forgiving. Also I find the 25 shore A silicone a little too flimsy and would suggest something like a 30-40 shore A.
Now with your very VERY well mixed silicone (trust me there is nothing more disappointing than coming back a day later to uncured silicone) pour a thin stream from up high into the mold and fill it up slowly.
After it is poured leave your mold to cure (usually 24 hours but will depend on the type of silicone you used) and then demold.
I would suggest leaving your mold now for another 24 hours before starting to cast the concrete.
Step 6: The Electronics: (Solar)
Now for what makes it shine...literally.
So unfortunately due to the civil unrest in my country while I was making this Instructable I was unable to order any new parts so I had to use some old parts I had lying around in my project drawer, please bear with me here.
First I sprayed the inside of the back cover with some chrome spray to reflect more light.
Now with some CA glue I glued the solar cell to the back of the cover and fed through the wires to the inside. ( In future builds I will might use a slightly larger solar cell but I will definitely use larger super capacitors as I only get about 2-3 hours of light out of these)
The provided schematic will give you a light that will automatically switch on when there is no longer sun shining on the solar cell.
I had to connect several smaller supercapacitors together as I could not order a larger one like linked in the beginning of the Instructable.
In this one I used a piece of LED "fairy lights" with 3 LED's as they are very efficient and gave the effect of a light hanging inside of the window when bunched together.
Step 7: The Electronics: (USB)
Making the light USB powered is a much simpler approach.
The pictures attached shows how I made mine with a simple day/night switch (depending on your transistor PNP or NPN, PNP turns on when dark whereas NPN turns on when light)
In my design is a boost converter as I only had a 12V LED strip available so you will not need it when using a 5V LED strip.
You can also omit the light sensing circuit completely and use a pre-wired USB LED strip. Just feed through the wires and stick the LED's on the inside of the cover.
Step 8: Casting the Concrete:
Time to cast the concrete!
Now you need to make a formwork around your mold the size you want your lamp to be. This can be done with anything from corrugated cardboard, foam board, poly carbonate etc.
I made mine from some leftover poly carbonate sheets glued together with CA glue and its approximately 110mm X 200mm.
I then glued the formwork to a glass pane using hot melt glue on the outside and sprayed the inside with some cooking spray (PAM)
Place your silicone (or 3D printed) mold in the centre.
Now mix mix your concrete according to the manufacturers instructions and slowly pour/scoop it into your mold until it's full, then tap around the edges to make any trapped air bubbles float to the top and set aside on a level surface to set for about 3 days... yes I know the wait is torture!
After the concrete has fully set you can gently remove it from the mold.
If you are having trouble with the concrete breaking I recommend getting a fibre reinforced concrete mix or buying some chopped fibre glass mat and mix some into your concrete.
Step 9: The Window Pane:
This is where you can get creative...
For my first lamp I used some white wax paper for the window and it worked quite well.
You can also cut a piece of thin poly carbonate to the shape of the window and sand it with some coarse grit sanding paper to give you a frosted effect.
If you want to be really creative you can even use some thin acrylic paints and paint on the back of the poly carbonate to give a stained glass look.
On this build I wanted to try something completely different.
I started by painting the back of a piece of hardboard with some PVA release agent, then 3D printed a frame of the window that I placed onto the sealed hardboard with some clay to seal the sides.
I then mixed some epoxy resin with amber tint and poured at into the cavity and let it cure.
This gave me a great textured window pane that looked antique.
I will definitely do this again in future builds!
Now the get the front decorative piece of the window to match the rest of the concrete I took some white and black acrylic paint and mixed until I got a grey that matched the concrete closely.
Remember it will darken when dry.
Paint the decorative frame and leave it to dry.
Step 10: Assembly:
Now all that's left to do is to assemble your lamp.
First slide in the decorative frame into the front and secure it with epoxy or CA glue.
Now your window pane goes in behind it and is also secured with some glue.
If you'd like to add some more character to your lamp you can take some thin wax paper and draw some interior features on it with a black marker like a chandelier, benches etc. that will cast a shadow on the window pane and place it behind the pane.
Now just push on the back cover and you're done.
With my current solar cell and supercapacitors it charges in about two minutes with direct sunlight.
Step 11: Enjoy!
There you go.
Now place your new creation in a sunny spot and marvel at it's beautiful glow when the sun goes down.
Feel free to leave a comment if you have any questions and please share your creations with us.
Happy making!
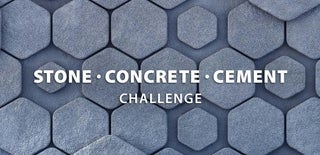
Second Prize in the
Stone, Concrete, Cement Challenge