Introduction: Sonic Screwdriver Wand 2: the FDM Redux
Note:
You'll find the STL files at the end of this instructable.
Background:
'Twas the year 2014 when a friend of mine asked me to make her something similar to the Sonic Screwdriver Wand made by expert wandmaker Maranda Li aka Praeclarus Wands. The result of that inquiry was my own take on this, which I have documented in its own instructable. I even made a nice Tardis / Ollivander hybrid box for it to be kept in and again, made an instructable for that. Going further out of my way I designed a huge, A1 blueprint-like poster for the wand which you can grab for free and print for non-commercial purposes if you feel like it. Print it, slap it onto your wall, make your own T-Shirt with it, as long as you don't make any money off it and maybe, just maybe send me a picture of it I'm cool with it.
It was supposed to be a one-off project, yet time and time again I had been asked if there was a possibility to make another one. It seems access to woodworking lathes is rather limited, which in hindsight should come as no surprise. I mean if you don't have a lathe yourself, how do you even find someone who does? Plus, using one isn't that straightforward either. Nonetheless, citing some excuse or other I got away from getting roped into making another one. Until recently one determined lass managed to bribe, I mean convince me to bring this project back to life. Kind of felt like the situation of Fluffy getting booked for a show in Saudi Arabia (0:59 - 1:45 minutes). The catch this time is now that I have my very own 3D printer I'll be allowed to make the whole thing 3D printable, though mixed media or complete wood reconstruction is, of course, still possible for anyone who wants to do so. I think that access to 3D printers or 3D printing services ought to be far better than the woodworking lathe supply, so I might actually lay this to rest for good this time. Who knows? At the very least it'll be much simpler for me to make full or partial kits for all those bugging me. Just drop me a message here on instructables, on deviantart, thingiverse, flickr or youtube. I still don't want to redo the whole thing again, as it's a tremendous time sink which I'd rather invest into making something new. And I've learned to loathe sanding. It's so tedious but there is so. Much. Of. It.
In short:
Rejoice, you Whovian Potterheads, for it is time for Sonic Wand 2: The FDM Redux! And you can (somewhat) easily make it yourself this time.
I hope you've got your 3D printers set to preheat, because this'll be a hot one!
Goal(s):
- Redesign the Sonic Wand so it can be 3D-printed and / or made out of wood if someone wants to
- Add a few more details, because I can
- ???
- Profit! Or sweet, sweet quiet. Hopefully.
Safety Advice:
This instructable makes use of 3D printers, various power tools (optional) as well as super glue and epoxy resin. Super glue and epoxy resin are quite sticky and the fumes aren't good for your health, so take appropriate precautions. Work in well-ventilated areas and avoid skin contact in the latter case. Try not to glue your fingers to each other, don't be like me. Also, 3D printer hotends are quite hot, so please don't burn your fingers either.
Step 1: Tools and Materials
Tools (pure 3D print) / Materials:
- 3D printer / 3D printing service
- If you don't have a printer, you can use a 3D printing service, e.g.:
- 3dhubs
- Shapeways
- iMaterialise
- ...
- Slicing Software
- Exacto knife (optional, for cleanup)
- Sandpaper (optional, for cleanup, preferably wet & dry)
- Plastic of your choice for the printer
- Adhesive
- Super glue
- Epoxy
- ...
Metal core, additional Tools / Materials:
- Metal saw / Angle grinder with cutoff wheel / Bandsaw / ...
- Basically anything to cut aforementioned metal rod
- Power drill / screwdriver (optional)
- Metal file (optional)
- Rod of choice
- 8mm diameter, approx. 200 - 225mm long (optimum should be around 220mm)
- Stainless steel looks nice and has a good weight
Wood construction, additional Tools / Materials:
- Woodworking lathe
- Woodturning tools
- Pencil (optional, but helpful)
- Saw(s)
- Power drill
- Calipers
- Exacto knife
- File(s)
- Sandpaper (preferably wet & dry)
- Wood stain (optional)
- Varnish
- Wood
- For wand part, 14mm diameter and at least 180mm length
- For sonic part, 30mm diameter and at least 170.3mm length
- Various smaller pieces
- Various woodworking tools you may have which make this easier
Step 2: Design
Generally speaking, when recreating a prop or using it as an inspiration, getting as much high-quality reference material on it as possible is a tremendous help. As I am mostly copying myself / the previous iteration of this project (shameless link to it and its custom TARDIS box) and as I am a data hoarder I still have all the necessary material safely stored on a hard drive. Additionally I have procured some rather decent pictures from a production-used Sonic Screwdriver from Doctor Who episode “The Day of the Doctor” thanks to a tbt Props sale as well as from a high-quality replica by The Celestial Toystore.
Now it was never the intention to make a perfect replica, so my design is still not that accurate in respect to the original prop. I actually know for a fact that there are mistakes. It is, however, more detailed than my previous version with most differences being in the details. I've added some of the buttons and grooves found on the original. The general design can be seen in the sketches I have attached here. If you want to download them, I have attached a PDF of them a couple steps further down, specifically at the wooden wand part.
In cooperation with the commissioner I have also taken steps to have the wand and grip part seperate (as was done previously) and joined by a steel rod to give a higher weight to the Sonic Wand, making it feel higher-class than it actually is. As I realise not everyone will want to go down that route I have taken the liberty to design a couple different versions for various types of printing / manufacturing / joining.
Here is a list of the different designs whose STL files are denoted with the given prefix:
- A: One single, solid piece of the wand with grip
- B: Two solid pieces, wand and grip
- C: Four pieces, wand and grip, cut in half for easier printing
- D: Two solid pieces, wand and grip, but with a bore to allow for a 22cm, 8mm diameter rod to be used for connecting the pieces
- E: Four pieces, wand and grip cut in half for easier printing, all with a bore to allow for a 22cm, 8mm diameter rod to be used for connecting the pieces
- M: Moldmaking pieces. Slightly oversized gem / crystal with a 15mm long, 8mm diameter stem for sanding and moldmaking, as well as an endcap for testing the fit of the sanded gem
Note that the gem / crystal is always an extra piece and doesn't count here.
Step 3: Wooden Wand - Woodturning, Sanding, Drilling
3D Printing Alternatives:
While the sonic wand can be fully 3D printed and you could make the wand part out of a wood filament, painting plastic or wood filament to look like real wood is rather hard and frankly a skill I'm not particularly good at.
If you feel like going that route is preferable, you may be interested in TecRC's wood stripe STL modifyer (for wood filaments), texturing STL models with OpenSCAD or Blender, or other ways I am not aware of (recommendations appreciated!). I tried my hand at it but the results weren't great, most likely as my experience with this software is close to nonexistant and I didn't have the time to put into learning it to a sufficient level right now. If you're more well-versed and want to take a try, teach me a few tricks or so I'd really appreciate it. I'll gladly attach your altered STL files to this instructable (with attribution, of course), or better yet you make a remix on thingiverse and I'll link to that here.
For now I decided to go with a regular, turned, wooden wand which I'll stain and varnish. I have attached PDF plans for the whole wand to this step.
Cardboard Template:
I have attached a PDF printout with all the dimensions and one wand which can be used as a template. It's in A4 format, just scale it accordingly if you use US Letter or some other format for printing. Or tell me in the comments which format you prefer and I'll see what I can do. By the way, after printing, do check the horizontal and vertical dimensions of the parts to make sure you printed it at the right scale - for some reason my printer prints it just a bit too small even though I set it to "no scaling", so I have to compute the right scaling factor.
The formula goes like this:
Intended_length / Actual_Length * 100 = Scaling Factor in %
I got 180mm / 169mm *100 = 106.5%
To use the printout as a proper template I applied a bit of spray adhesive to some cardboard and glued the paper sketch printout on top of it, then proceeded to cut out the wand and more importantly, the outside shape of the wand. Basically what's usually used as a throwaway now becomes an excellent template for the woodturning. An exacto knife did the cutting part of the job just fine.
Woodturning and Sanding:
Same as the last time I'll be using my somewhat underpowered but cute modelmaking woodturning lathe made by Proxxon, the trusty little DB-250. As always when using power tools, wear appropriate protection - safety googles and a dust mask (not pictured) are highly recommended.
For starters I affixed some round stock beech in the lathe. It's 14mm in diameter, conveniently the same as the maximum diameter of the wand part. It's almost as if I scaled it like that to make my job a bit easier...anyway, once that was done I could affix the template to the lathe tool rest, spin the lathe up at the slowest speed and use a pencil to mark points at which there will be a step in the wood body.
By the way, the pencil I am using here is a Uni Kuru Toga Roulette (this is the place where I first heard about it, and a gem of a site full of cool tools - hence the site's name), a truly superb mechanical pencil which I highly recommend. There's different models at different prices, all with the auto-sharpening / pencil lead turning feature, but they're all reasonable and I like the aluminium body Roulette version the best. Uni's Kuru Toga pencil lead is fantastic, too.
Anyway, I used various lathe chisels to shape the wood, continuously using the template, plans and calipers to check if my measurements are all right. Of course as it's handmade they're not perfect, but they should be somewhat close.
Do note that I have the template facing in such a way that the thick end which I do not need to turn down is at the tailstock while the tip which needs a lot of turning is closer to the jaw chuck. This serves two purposes - for one the workpiece is more stable towards the chuck and thus turning is easier and safer, and secondly I get a centered divet at the back end thanks to the tail stock which I can then use for center drilling the wand.
After I was done with the woodturning I left the piece in the lathe and used 120 grit sandpaper for preliminary smoothing of the wand part while letting it spin at the slowest possible speed and keeping my hands well away from the chuck. Rapidly spinning stuff is scary, after all. Not to mention dangerous.
Cutting Plug and Tip Rounding:
I used a simple miniature hacksaw to carefully cut off the plug at the tip of the wand, roughly shaped it by twisting, turning and rubbing it on a fine file and gave it a round finish using 120 grit sandpaper.
Drilling Connection Rod Fitting
Now if you remember the design, one of the possible choices is to use an 8mm metal rod as a core to add some weight, some heft to the Sonic Wand. While it is certainly possible to limit oneself to the Sonic Screwdriver / grip part it is also possible to extend that rod into the wand part and use it as a connector. To that end it is necessary to drill out the wand part about 60-70mm deep and 8-9mm in diameter as centrically and straight as possible.
Now for good / proper ways to do that, please refer to the following example videos:
- TabLeft Workshop - "TIP: Drill down the center of bar stock"
- Embrace Racing - "How To End Drill Round Stock (Long Rods Without a Lathe!)"
- Dusty Guy - "Drill and Tap on a Lathe"
- Thomas Fox - "Drilling Round Stock Without a Lathe - Making a Microphone Thread Adapter."
And if you want to wing it, you can do it like me. Remember that I had a centered divet at the end of the wand thanks to the lathe's tailstock? I made use of that and started drilling a hole into the wand with a 4mm wood drill bit first, drilling as deep as I can with the drill bit. I left the wand on the drill bit and slowly spun it with the drill, checking if it wobbled or not. Noting that I switched to the next drill bit, 0.5mm larger and slowly started drilling into the previously drilled hole while pressing down on the drill bit from the wobble direction (basically if the wand previously tilted up, I now pressed that side down a bit while drilling). I repeated that process in 0.5mm increments until I ended up with a pretty well-centered 9mm hole, 1mm larger than I need it to so that any remaining non-centricity can be taken care of by two-part epoxy glue. Even though I pretty much winged it, it worked pretty well in the end I'd say. Just look at the chamfered testing steel rod I inserted. Beautiful I say.
Attachments
Step 4: Faux Inlay - Polymer Clay Trickery and Wood Finishing
If you choose to 3D print the wand part I hope you have some sort of multimaterial printing available to you, because the polymer clay faux inlay technique won't be working for you. Your prints will probably melt trying to use this process with them. Your only hope would be a colored 2-component-putty like Green Stuff, Milliput or something like that. I think Smooth-On's Free Form Sculpt with their Uvo or Ignite pigments might work for you, but haven't tried it so it's up to you.
Now then, the keen-eyed Whovians amongst you have probably noticed that I am technically using the wrong colors for the inlay. Romana's Sonic Screwdriver which is making up the wand part uses yellow and green highlights, as well as some black stripes. However I feel that mixing so many colors together would not look good, so I opted for TARDIS-ish blues which should fit nicely to the gem (or whatever that thing is) at the end of the 10th's Sonic Screwdriver which makes up the handle. You may say that the blues are off, too, as they are too light and you would be right in that. I do have better-fitting ones, but as I plan on staining the wood and make it darker, lighter blues will pose a nicer contrast and thus look better. At least that's the plan.
Polymer Clay Inlays:
Usually inlays are done by cutting grooves or even completely routing / milling out shapes or surfaces and then inlaying metal (e.g. Make: "Wire Inlay: Inspired to Make"), wood (e.g. The Wood Whisperer: "Router-Based Inlay") or other materials to sit flush with the surface. Proper inlaying is quite hard to do and requires a respectable amount of skill which I do not have acquired (yet) - so I'm going to cheat. This technique makes use of polymer clay, Fimo in this case, which is kneaded and pushed into the cut grooves generously before the wooden piece is put into the oven and baked according to the polymer clay's instructions. For Fimo that's about 110°C, which is totally safe for wood. Alternatively you can do a resin inlay as well, but that's a tad harder to do with a circumferential groove on a round object (e.g. Jonny Builds: "DIY Farmhouse Dining Table w/ Epoxy Inlays Using Reclaimed Barnwood", or doublereno: "Lichtenberg Wood Burning Blue Epoxy White Oak").
About five years ago I first experimented with this technique. Back then I also used round beech stock and used a v-shaped wood carving tool to cut grooves into the wood, then filled them with Fimo. In that case for testing purposes I used brown first, then expanded with copper, silver and gold Fimo. I had also experimented with undyed and dyed wood, sanding or not sanding (after dyeing) and a few other things. I'm just mentioning this to show you that experimenting is not a waste of time, even if you can't immediately use the results. The knowledge will definitely come in handy one day. Below are three examples of this experimentation. Even if they look drawn, I assure you those are Fimo inlays. After that is the current application on the wand.
Sanding:
Baked Fimo is fairly hard, and honestly quite a pain to sand. Curiously it is still soft enough so it can quite easily be cut with your average exacto knife. At least mine was, so I used aforementioned blade to cut away most of the excess Fimo and finally used 180 grit sandpaper to sand the Fimo down and presto, fake inlay done! The colors don't look that good yet, but that will fix itself after varnish is applied.
Staining:
As I've mentioned, I want to stain the wooden wand part to make it look a bit more interesting. For this I have chosen teak wood stain, mostly because this is what I have on hand right now. Unfortunately the polymer clay soaks up wood stain as well, so the usual application method of applying it all over generously and maybe wiping the excess isn't going to cut it. Instead I use a small brush to carefully apply it and try to avoid staining the polymer clay. While a foam brush is pictured, I didn't end up using it. Excess was carefully wiped with a paper towel. After the stain has dried well I used 120, 180 and 240 grit sandpaper to remove most of the surface staining and just leave the deeper penetrating stain intact, thus exposing and highlighting the wood grain. It's a bit shoddy, but it should end up alright. I hope.
Step 5: Gem Masters, Molding and Casting
For my first version of the wand I've used regular garden glass stones. The kind you can find at dollar stores or at the home / garden decoration department of a variety of stores. It worked, they had a nice color, but they're not ideal - from a whole package of a couple hundred of them, less than 10 were actually of a useable shape and size. Not only does it take time sifting through the literal pile to find good glass stones, even when I found one I had to shape the seating specifically to match one stone. Which might be fine for wood, but will get harder with plastic. Plus, it's somewhat time-intensive. And though I put quite a bit of time into finding a finished glass stone or plastic gem of the right size and shape which can easily be ordered my search was not successful. For an easy-to-replicate (mostly) 3D printed Sonic Screwdriver Wand these options are thus not viable.
Therefore I have decided to model the gem myself, prepare it accordingly, make a mold and then cast it.
The Design and Print:
In my design the seating allows for a 20mm gemstone, tops. As 3D prints rarely are exactly accurate I have added a 0.2mm offset, resulting in a 19.6mm gemstone of approximately 6.4mm height. That's the "ideal" size, if you will.
To make it easier to create a master for molding and to account for sanding I have resized the stone a bit to 20mm diameter, approximately 7.6mm height and added an 8mm diameter, 15mm long shaft at the bottom. You'll see why in a minute. Now the idea is of course to take that molding master, sand it down to approximately 19.6 - 19.8mm diameter, get it as smooth as possible (removing the layer lines of the print as best as possible), make a mold and then cast copies from resin. Now then, doing all that work for a single molding master isn't really worth it, it also makes getting new copies a very slow process given that most of the resins I use have a 24-48 hour demolding time. Plus mixing up small batches of resin is harder to do than mixing bigger ones, so I opted to make 10 at the same time.
To make my life easier I printed the molding master at 0.1mm with 5 shells to have something to sand down and to retain some stability while keeping the layer lines reasonably minimal. I don't remember if I used 20 or 25% infill, but that's not that critical anyway. I printed the parts upright like mushrooms and used supports for the "cap", that is the underside of the gem part. How good the bottom side looks is not that important though, so don't stress about it if it doesn't look amazing.
You can find the STL files for this molding master at the end of this instructable with the other STLs. I have also added a stand-in for the cap with a hole to check the seating of your sanded gem if you don't have calipers.
If you print the molding master with a translucent filament you might merely need to go through the sanding and not need to make a mold. You'll probably want to go for 100% infill, or use some sort of interesting infill pattern. I'm sure it is possible to do some amazing combinations there. If you go this route, do drop me a message because I'd very much like to know if and how well that turned out.
Shaping and Sanding:
Initially I thought I went about this the smart way. Remember the 15mm shaft I added at the bottom side of the molding masters? That's there to clamp the parts into a drill and have it spin the part, thus making the sanding much, much easier. No way I'm going to sand them all by hand, I'd definitely ruin the shape that way! Plus, it'd ruin my wrist for sure.
So for each master I chucked it into the drill, spun it up and then went to town with wet sanding. This is very, very important: PLA and other filaments have fairly low melting temperatures, and even lower temperatures at which they get soft and gunk up your sandpaper, or get an absolutely horrid finish from slightly melting during sanding. Wet sanding keeps the temperature of the part below 100°C as the water soaks up the heat and evaporates if it exceeds that temperature, making room for more water. Therefore when sanding 3D printed parts, use wet sanding whenever possible! Also remember to use proper safety equipment, safety goggles if you're using the drill method as parts may get sent flying and a dust mask for the sanding (even if wet sanding produces far less dust).
I started with 120 grit sandpaper and, where necessary, a fine metalworking file to get the initial diameter right. Checking with calipers every now and then I made sure the parts ended up at about 19.7 to 19.8mm diameter, and of course that the dome part was properly smoothed with the sandpaper. I continued with 180, 280 and 320 grit sandpaper, ending up somewhere around 19.6 to 19.7mm diameter. At that point I hit the parts with two light coats of spray-on varnish, giving it some time to dry between layers and more time to fully dry before moving on with sanding. 400, 600 and finally 1000 grit sandpaper completed the "regular" wet sanding part and were rounded off with two more light coats of spray-on varnish.
While the parts were definitely pretty smooth, it's at this point where the real fun started. I had gotten myself a set of MicroMesh, which is this amazing sanding stuff with absurdly fine grits. You can use these to bring varnish, resin and other stuff to a shine that's hard to believe. As recommended by the manufacturer I started with the 1500 one (which is actually somewhere between 600 and 800 grit regular sandpaper, on the Euro scale at least). From there I just went through all 8 remaining pads of the series, 1800, 2400, 3200, 3600, 4000, 6000, 8000 and 12000. Once that was done I used a small hacksaw to saw off the stem and sanded the bottom side somewhat flat on a file. It merely needs to be good enough for the glue to stick when making the mold after all. If you're printing with translucent filament and want to use the result directly, do put in a bit more effort into finishing the bottom side.
And I did that for all 10 molding masters. I mean, 1, 10, where's the difference anyway? Yeah... in hindsight the
difference was between being done in 2 or 3 hours, and being done in more like 12 to 14 hours and getting an aching back from being hunched over those molding masters, sanding them to absurd levels. My reasoning for all that hard work is that moldmaking silicone can have an insanely good resolution, down to the point of being able to pick up fingerprints on your parts. As I don't want to spend time sanding each and every cast gem copy, I figured I'd put in the work beforehand, making the masters as smooth as possible, to get a really smooth mold and in turn really smooth resin copies which don't need any finishing. Maybe a light hit on the polishing wheel with a smidgen polishing paste, tops. You can see the results in the following pictures. While they really don't do the sheer smoothness any justice, I hope you can see my efforts in them anyway. In the second and third image you can see the direct comparison between a finished one and one basically fresh of the printer with just the supports removed.
Moldmaking:
The moldmaking itself is actually pretty simple. I laid out the masters to take up a reasonably small amount of space and measured out the size I needed for them which turned out to be approximately 10 by 15cm. I used foamboard and a hot glue gun to quickly make a mold box with that as its internal measurements. As the height of the mold will not be that high, foamboard is plenty stable to hold out well.
As you can see in the second picture I used more hot glue to seal the inside seams of the mold box pretty well to prevent any leaks. The edges and corners of the mold won't be looking too good, but who cares? Once the box was constructed I marked out a grid pattern for the positioning of the masters, then tacked them down with some crazy glue. I didn't need a perfect seal around the bottom as I can simply remove any silicone that gets under it or even outright chamfer the silicone mold later due to the molding masters being taller than the actual gems I plan on casting (by not filling up the molds to the brim with resin).
As for the silicone itself, I basically followed the manufacturer's instructions for the ratio of silicone and hardener, mixed it up well, poured the silicone and then let it rest for twice the recommended time before demolding just in case. I am happy to say that the mold turned out quite well, as you can see under the casting section.
By the way, if you're new to molding and casting I can recommend the following sites and videos:
- Instructables' "Mold Making & Casting Class" by Paige Russell
- Punished Props Academy's "Molding & Casting 101" playlist
- A bunch of videos on Tested, such as "How To Make Resin Copies of 3D-Printed Figures", "How to Mold and Cast a Lightsaber!", "How To Mold and Cast Foam Props!" and "How To Make a Silicone Brush-Up Mold!" (and more)
- I Like to Make Stuff - "Mold and cast an action figure ( or anything ) // How-To" and "How to 3d Print & Cast a Neon Sign"
- Also, don't scrape the containers when pouring the silicone or resin - the stuff on the walls is mostly badly mixed and won't cure properly, potentially messing up your molds / casts!
- Molding and casting stuff has a shelf life which may be surprisingly short - keep that in mind! You'll see why when you read on.
- Stir well and thoroughly. I mean it.
Casting and Finishing Touches:
Now this here is a sad story indeed. It really didn't get off to a good start at all. Those who know me personally know that I'm a bit of a tool and maybe material hoarder. I buy such stuff all the time, and it tends to sit on my proverbial (and literal) shelves until actually needed. In the case of casting resins I have, over time, bought a couple different ones and used them for a project or two, but by far not all of it. While the mold was curing I wanted to perform some quick-ish tests to determine how much dye I need to add for a nice and proper gem look.
So I prepared a simple grid mold with foamboard and hot glue, set up all my mixing stuff, grab the first can of resin, pop it open, try to pout it and ... nothing. But the can is heavy, so what's the problem? Yeah, so, remember the bit about shelf life? It completely cured. 30 bucks of resin, a solid block now. Damn. I peeled the can around it to extract it as a single piece and maybe, just maybe be able to use it for some project or other in the future. Or just to use it as a fairly expensive paperweight.
No matter, get the next can of a different resin, open it up, try to pour it and ... dammit. Not again. Some poking and can peeling later I'm effectively another 30 bucks or so poorer and one paperweight richer. Somehow I'm beginning to think I should call it a day and return to it after a good night's sleep. At the very least I really should stop buying more resin than I need for a given project and perhaps extend that to other stuff with a shelf life date on it. For your entertainment I've added a picture of the two offending blocks of resin, by the way. As us German folks say, "Schadenfreude ist die schönste Freude", so do enjoy the image. Hit up google translate if you don't get it.
But no, I'm not calling it quits yet! Third time's the charm, after all! So going for my third and last (!) can of resin I shake it and hear the glorious sound of slushing liquid. A good sign, I say! My calculations determined that to completely fill the gem mold I'm going to need approximately 15-25ml of resin. Account for some stuck on the walls of the mixing cup which will be wasted, I mixed up a test batch of 40ml. Once I get the right figure for the dye, I'll just halve the amount, mix up 20ml and I should be golden. Next, I added a mere three tiny drops of the only blue resin dye my local material supply shop carries, "signal blue". I thought it prudent to slowly work my way towards the right gem color. My intention was to start lightly, pour one sample, add another drop of dye, stir, pour and repeat. I even thought long and hard about the scheme to calculate back the dye concentration at each step to be able to determine the number of drops needed with a full 40ml batch of resin to get similar results! Anyway, I stir the three drops up aaaaand its basically an opaque, crappy blue. Totally overdosed on the dye. Damn. Alright, finish mixing it, pour the stuff into the test mold, mix up another batch, this time putting a drop of dye onto a paper towel and using the stir stick to take up only a small bit of it, mixing the next batch up. It's a little too light, so I repeat the process to get to a decent strength, pour it and from the looks of it, the dye is absolutely and 100% unuseable for my purposes as the color / look isn't even remotely close to what I want it to be. I can't get that gem look I want if my life depended on it, the color just isn't right even with an acceptable translucency. It is possible that the dye is simple meant to be opaque instead of the desired translucent, but the package just doesn't say. Damn. More Schadenfreude for you, I guess, see the picture of my failure. At least the test mold box' crappy looks fit the results of the dye tests.
You know what they say about getting your hopes up ... so screw it, I'm getting some pre-dyed resin and be done with it for now. So next day I went to my supply store and got this pre-dyed version of the same clear resin I've been using for my coloring experiments. According to the package, it's meant to look like lapis lazuli which, should it be translucent, would be a pretty good color.
Back to the mold - after about twice the recommended demolding time I took the mold box apart and the silicone has cured well. Despite not using any mold release for fear of lowering the quality of my surface finish, all masters demolded easily. It's a good thing silicone sticks to almost nothing but itself. Now as I have expected, the edges of the mold look downright horrible due to the hot glue used for sealing the inside of the mold box. There was also quite a bit of silicone leakage under the masters, or flashing if you will. I removed that with a razor blade, cutting all around each of the individual gem domes. This left a pretty jagged and ugly edge as well, so all in all my mold won't win any beauty contests - but on the inside, oh, on the inside it's beautiful. Perfectly smooth surfaces, and not a single air pocket in sight. At this point I'm itching to try it out and disregard the manufacturer's instruction to let it sit for a couple days after demolding for reasons I forgot. Also, the deadline for a contest I'm handing this instructable into is approaching and I can't afford to waste much more time.
In order to try it out I've mixed up a batch of 15ml of the pre-dyed resin according to the manufacturer's instructions and as it turns out, that's pretty much the perfect amount. The uncured color looks good, too. From that previous cured-resin and poor-dye-color fiasco I'm still a bit wary, but I think I'm tentatively hopeful that this will work out. If it does it'll also be super easy to make more of the gems as the resin is pre-mixed anyway, so no way to screw the color up. I do feel obliged to mention that I have not used any mold seperation agent here either - no petroleum jelly, no talcum powder, no liquid or spray-on separation agent. I fear this might ruin my finish, so I have not applied any and accept that the longievity of the mold will suffer. On the other hand, I'm not expecting to make hundreds of these gems anyway and if the mold degrades too much I can still make another one as I will keep the masters anyway. This might screw me over, so fingers crossed!
First, the good news: The castings came our amazingly well, both in terms of color and in terms of finish. I'll have very little work left to do on them, just flattening the bottom side and going over with some acrylic polishing compound with a polishing wheel ought to be enough.
The bad news is that I have already noticed some minimal tearout in some parts of the mold. I did expect shortened mold lifetime from not using a mold release, but this feels exceptionally quick (good silicone molds last for 50-100+ castings). Maybe the super-smooth surface is especially good at grabbing to the resin? In any case, should I have to recast for some reasons I will use a mold release to minimize further damages to the mold. A liquid or spray-on one should do the trick.
As the deadline for the contes I'm handing this instructable in to is approaching frighteningly fast I have opted to skip over finishing every single casting, especially since I technically only need one for now. For illustration purposes I have finished up three to compare those against unpolished castings. The bottom side was mostly sanded flat using a fine metalworking file, then with wet sanding on 120, 180, 280 and 320 grit sandpaper and both sides recieved some quality time with a polishing wheel and acrylic polishing compound. What's left is to attach some self-adhesive aluminium (also known as aluminium tape) to the back of the crystal gem so it reflects a bit more light and looks nicer and I am finally done with this part of the build. Below are some examples; the bottom row is as cast, the top row has recieved the finishing touches described above. Funnily enough the 'polished' ones are a bit less shiny, but don't have any surface blemishes anymore. I'd say the tradeoff is worth it and it's good enough for the given purpose.
Step 6: 3D Printing, Glueing, Sanding
As I have already made the wand part (Romana's Sonic Screwdriver) from wood and the gem / crystal is cast from resin, the next missing parts would be the grip in the form of 10th Doctor's Sonic Screwdriver and the metal rod. Beginning with the Sonic Screwdriver, to make life a bit easier for me I decided to go for the version where it's split in half and has a bore to accomodate for the steel rod. If you go back to the Design part of this instructable you'll know that I have chosen file type "E: Four pieces, wand and grip cut in half for easier printing, all with a bore to allow for a 22cm, 8mm diameter rod to be used for connecting the pieces" which you can find at the end of this instructable.
Printing the Pieces:
Generally to minimize cleanup as much as possible I print with 0.1mm layer height, which is important as I am printing with PLA and there's few convenient ways of finishing prints (such as acetone vapor smoothing for ABS). To have a bit of material for sanding while maintaining part stability I typically go for 5 shells (and top / bottom layers). In this case as some of the walls may be a bit thin I went for an infill of 30% instead of my usual 20-25%. This ougth to be sufficient, I think.
For the Sonic Screwdriver / Grip part and the moldmaking gem / crystal I have additionally enabled supports and a 5mm brim. The supports are of course for overhanging structures which are hard to avoid and the brim is due to the split Sonic Screwdriver being fairly large and flat. The brim tends to keep parts from lifting up from the print bed.
Most other parts should not necessarily require the usage of supports or a brim. In all cases it won't use much filament at all, so it should be fine.
Below you can see the E-Series Sonic Screwdriver grip halves basically fresh off the printer, I have merely removed the brim and supports roughly. The parts still need a good cleanup before being glued together. As they are right now they don't quite fit together and when they're pressed together the metal rod can't be inserted as remains of the supports are still sticking out in the bore channel.
Cleanup:
I have printed the parts in PLA, so there's no good way around finishing them except putting some spit and backbone into it, which means more sanding. No vapor smoothing for me, oh no. Just manual labor. I'm beginning to think this instructable should've been titled "Sanding: The Instructable!" as I feel that's all I'm doing. Time-wise it might actually exceed 30% of the project time and feel at least like 50%. But I still have some tricks up my sleeve to at least make it bearable, so I'm going to share them with you in due time. Hint: We're going to cheat. We're partners in crime now, no way out of it.
The general concept is to finish the inside and hard-to-reach areas of the halves, then glue them together, take care of the seams, then sand it all flush to be ready for primer painting.
Thinking about it in order, the first thing that needs to be taken care of is the remains of the support in the inside channel / bore for the steel rod. I use rounded carving chisels / knives (straight gouge chisel) to get rid of most of it, but a round file will do as well. Wrapping the steel rod with sandpaper and using the steel rod kind of like a file or form-fitting sanding block works quite well, too. For the blunt end in the cap you can press the sandpaper-wrapped steel rod in and just twist and turn it. Remember to change the sandpaper quite often as it gets clogged up. Also, wet sanding to prevent overheating the PLA, though it's not so important for the interior parts.
The supported / bridged underside of the four bars connecting the body to the cap with the gem were sanded flush with a metal file and an exacto blade was used to take care of the resulting burr.
Moving on, remains of the brim and other artifacts along the perimeter of the flat side (which includes the edge to the bore for the steel rod) need to be removed. For this I mostly used a dedicated deburring tool as well as an exacto knife. This may result in a small chamfer, but that will get filled in later when taking care of the separation seam.
With the hard-to-reach areas mostly done the flat sides can be prepared for glueing by sanding them with something like 120 grit sandpaper on a flat surface to make sure they're really flat as well as for giving the glue something to grab on to. After this dry-fit the parts and insert the steel rod, making sure it fits easily. If not, go back and sand the offending parts down until they're no longer a problem.
As for cutting the rod, you can probably use a hacksaw, cutoff wheel, bandsaw or any number of utensils to do it. If you're This Old Tony, Bruce Lee or Chuck Norris a simple hand chop will be sufficient. Jokes aside, I trust that you can do it. I used a chop saw with a cutoff wheel for a nice 90° angle. Which isn't important, but I like it. Furthermore I fixed the rod into a drill and turned it while using a metal file to add a chamfer to it, but that's not really necessary as no one's going to see either end anyway. Except you of course, looking at the pictures here.
By the way, if you use the solid parts with a bore and the rod doesn't fit, you likely don't have drill bits long enough to drill it out / widen the bore. You can probably use a trick by Matthias Wandel to get the rod in though. Just check his video "Making wood thread taps". It's super simple and should work well with plastic. The end that's being used to attach the wand part won't be visible anyway so you can cut grooves into that one. It'll also give the glue more surface area to grab on to, so it's a win-win.
Glueing:
At this point the two halves can be joined together. My glue of choice for this is 2-part epoxy, preferably a quick-setting one. It dries quickly, can be filed and sanded and it's super strong. This is also where we're taking the most important steps to make our lives easier down the line (read: where we're setting up the cheating part). The Sonic Screwdriver is a mostly round object with, in this design, a central bore axis where the steel rod gets inserted. That rod conventiently extends past the tip of the screwdriver, which we'll be making use of later.
As I have repeatedly stated like a broken record I am using a steel rod and want to preserve the color of the exposed part near the back end, so when dry-fitting the parts I prepared a fairly exact bit of masking tape to cover that section up so glue and paint won't mess it up. With these preparations done I put down some plastic wrap to prevent any dripping of glue onto my work surface as well as two overlapping strips of packing tape which will serve as my temporary glue mixing surface. It's a neat trick for mixing up 2-part epoxy and such. As for the mixing itself, a popsicle stick with an angled, flat-cut side as well as a similarily prepared toothpick is used. Besides mixing these handy tools are also used to smear the inside bore of both halves as well as the flat parts with glue before carefully inserting the steel rod, sandwiching it in and then using clamps to hold everything in position while the epoxy cures. I made sure all the parts line up well and let it sit for two or three times the recommended amount of time. Surplus epoxy is used along with the squeezeout to build up a layer of epoxy around the seam, thus masking it off for now. After it cured I turned the Sonic Screwdriver around, mixed up a bit more epoxy and treated the other seam similarily.
More Sanding:
With everything dried / cured / hardened an old exacto blade (broken tip, but not dull) is used to get rid of most of the excess epoxy glue around the seams. If you take off too much, just apply some once more or use any combination of crazy glue and zip kicker, baking soda or baby / talcum powder (last one takes some time to set, but it's a nice, solid texture depending on the mixture, see Tested: "Shop Tips: Mixing Superglue and Baby Powder"). A small metalworking file may also be used to remove most of the excess glue, but be sure to clean it regularly with a wire brush and / or an old exacto blade or something similar to keep the cutting teeth clean and in working order. A gunked-up file is next to useless.
Next we can use the cheat I have hinted at multiple times - using the exposed steel rod to chuck the Sonic Screwdriver into a drill, spin it up and easily sand most of the areas. Again, this is only possible because the Sonic Screwdriver is mostly round without many parts sticking out and we have our steel rod as a central axis, otherwise it'd be a lot more manual labor. The part is then wet sanded as much as possible while spinning and unreachable areas are then sanded manually (wet, if possible). The smoother the part gets, the better, but it doesn't have to go anywhere near the ridiculous levels of the gems / crystal. With the approaching deadline I've settled for 120 grit sandpaper which should be good enough for the primer. While layer lines can still be seen, they can't be felt anymore, so it ought to be fine. If it isn't, I'll go back in with more and / or finer sandpaper. Hindsight note: ~240-320 grit would've been a bit better.
To make your sanding life a bit easier, here's a few of the tools I've been using (which you can also see a couple pictures above):
- Wet sandpaper, various grits
- (Small) Metalworking / modelmaking files
- Foam- or wood-backed nail files. You can get these at most drugstores and they're pretty neat as they're easy to handle and come in a couple different grits
- Nail file sticks. Again, same aisle at the drugstore. With these you can get into the tiny corners you can't reach with regular sanding implements
- Popsicle stick with glued-on sandpaper. Easy to make and adapt to your needs.
- Custom sandpaper holders. I've printed this 1cm-wide version designed by workshopbob on thingiverse. There's a whole bunch of different designs to choose from on thingiverse, so take a look around.
- Exacto blades. Less for sanding, but can be used to quickly remove or scrape off excess material.
- Deburring tool
- Various carving knives / chisels. I think these are meant for linoleum, but they're sharp and work with PLA just fine.
Step 7: Painting (with a Bit of Sanding)
Painting:
Before I start let me remind you to use proper protective gear, especially a decent respirator / filter mask, as well as to work in a well-ventilated area. And if you're using a respirator mask and don't remember when you last changed your filters, this is your reminder to do it now.
With the rod acting as a painting handle I quickly made a stand out of cardboard and some tape to hold it in place for the paint to dry. Talking about the painting, my concept is masking the steel rod, then go for grey primer, black basecoat for the non-marble parts (masking the marble parts), silver for the metal-ish parts (keeping the marble parts masked, additionally masking the black front cap), finally a white basecoat for the marble part, all in that order. The rest will be done with acrylic paints. Let's see how it works out. At this point in time your guess is as good as mine.
For starters after two fairly heavy layers of grey primer the layer lines are still pretty apparent, so it's time for sanding. Again. After letting the paint dry (accelerated with a hair dryer) 180 grit sandpaper is used to sand the Sonic Wand once more. Two more heavy-ish layers of primer, some touch-up sanding with 320 grit sandpaper to follow. Finally about 3 or 4 more light layers of primer as a finish. It's not perfect, some of the layer lines and parts of the separation line can still be seen but as my time is running out I can't be too picky now. 'Good enough' will need to suffice. At this point I let the paint sit for an hour to fully dry / harden (and ventilate the premises properly) before applying masking tape and moving on to the next step: black basecoating.
There's nothing much to say at this time except for maybe to carefully apply the masking tape to get clean lines. Maybe using high-quality masking tape instead of the cheap stuff I've got at a discounter a couple of years ago. Oh, and whoever first thought to use a hair dryer to get paint to dry quicker was a bloody genious. I learned the trick from Adam Savage's videos on tested (website / youtube, very much worth a visit, especially the One Day Builds and Shop Tips). You can apply multiple paint layers so quickly with this method! No wonder modelmakers all around the world use this technique. To think I've spent so much time pretty much literally watching paint dry. No more!
Just be a bit careful with the hair dryer and PLA, don't dwell too long in one spot or get too close as you might either damage the paint or the print itself.
Anyway, layer and separation lines still show through, but with each layer of paint it gets better and most of it can be passed off as 'texture' by now. Hooray for me! I mean, just as planned! Next up is letting the paint fully dry for another hour, then super-carefully masking off the black cap part before moving on to silver paint for the metal parts.
The silver paint went pretty uneventful as well. More masking, more spraying, more drying. Not as shiny as it could be, but I didn't have any high-quality chrome paint at hand and learning from the solidified resin fiasco I kind of want to use up what I have first. Plus, for a really shiny chrome finish you need an expertly prepared surface as well, meaning it has to be suuuper smooth (which mine isn't) with good basecoats. If you're interested, Bill Doran from Punished Props has an article of chroming parts with Allclad Lacquer on Tested, which is apparently industry-leading or something. Adam Savage on the other hand swears on Molotow Liquid Chrome, which he also uses in his video on Tested: "Adam Savage's One Day Builds: Mortal Engines Hand Cannon!" where he finishes a 3D-printed prop firearm.
Next one's going to be interesting as I'll have to peel off the current masking and apply new ones.
The peeling went pretty well, only minor chipout and paint creep under the masking tape. Nothing that can't be touched up later with acrylic paints. New tape was applied to mask off the non-marble-parts and white base paint was used to create a base for the marbling, which I already dread as my painting skills are quite underdeveloped and marbling is fairly ambitious for me. By the way, in the picture below it looks grey-ish, but that's because the paint isn't quite dry yet. It really is white as you'll see a bit later.
That went unexpectedly well. All the masking tape peeled off without any problems, and the layers upon layers of paint are thick enough to almost completely mask any remaining layer lines of the 3D print as well as the separation line of the halves. I specifically focused on the separation line in the picture below, and there's only a few places where you can see it. If you don't exactly know what to look for, it's not noticeable. In order to protect the sprayed paint before moving on to acrylics I gave the whole Sonic Screwdriver two or three light layers of spray-on varnish. It also helps when wiping off excess acrylic paint either wet or dry without damaging the spray-painted paint layers. Now it's time to do the marbling, the detailing and maybe some very light weathering. We'll see.
Damn, I only noticed the reflection of my lighting umbrella on the acrylic painting palette in editing. Oh well, now you know how I get soft lighting on my pictures: Shoot-through umbrellas. Not quite as good as softboxes, but a heck of a lot cheaper and typically quicker to set up, too. At the same time I noticed that I had flipped my cutting mat to the black side instead of my usual green - what a blunder. Either it's getting too late (I'm writing this at 1am to make the deadline) or the paint fumes had gotten to me. Oh and you don't need this many brushes, in fact I only used two of them - a very fine-tipped one for details, and a rather fine flathead one. I don't quite remember if it was the left or the middle one of the trio you can see here. But they are decent-quality synthetic brushes, which makes things a lot easier.
First of all I removed the masking tape of the exposed steel rod part. Then I moved on with some touch-ups on the silver and black parts that were either scratched up or not colored properly. The zig-zag channel of the extendable part (of the real Sonic Screwdriver, mine doesn't move) was filled in with some black paint using a very fine brush, as was the channel for the push-button-thingy at the side. The other side channel was colored light blue, similar to the original prop. Finally it came down to marbling. I used Snobs Interiors: "Grey Marble Effect" as a reference, as well as some images, but in the end I just added black lines of various widths with a fine brush and after a varying amount of fairly short drying time I dabbed or wiped over it with a dry or slightly damp piece of kitchen paper. This process was repeated until I ended up with something which from a distance and while squinting and being almost blind just might resemble marble. Being pretty much done with the detailing I'm fairly satisfied (rad: I've passed the 'Good enough!' threshold) so I think I'll be skipping any weathering and move on to the assembly.
Step 8: Final Assembly & Varnish
This almost doesn't deserve to be a step in and of itself as it's pretty easy and short compared to previous ones.
First of all the gem / crystal is backed with some self-adhesive aluminium tape. Two-part epoxy is then used to glue the gem to the back of the Sonic Screwdriver and the wand part (Romana's Sonic Screwdriver) to the grip (10th Doctor's Sonic Screwdriver). Simple, isn't it? Except my wand is a bit crooked as I apparently messed up with the drilling. That's what I get for hand-drilling. Maybe I should've gone for a drilling jig? Oh well, 'good enough' and all.
Finally, with the wand assembled varnish can be applied to make the wood pop and to protect the whole Sonic Wand as well as making it super smooth to the touch. I applied it in thin layers making sure to sand the wand between layers to get an pretty smooth finish. Though the sanding was limited to the wooden part as the printed grip was already super smooth after the layers upon layers of paint and a bunch of sanding.
After the first layer of varnish I sanded with 180 grit, one more layer of varnish, sanding with 320 grit sandpaper and the last layer of varnish.
Finally done! Now if only someone could get me a piece of clothing so I'll be free from this project in the future I'd be quite grateful.
Step 9: Glory Shots
Here's some pictures of the finished Sonic Screwdriver Wand for your viewing pleasure.
Unlike my regular instructable documentation pictures I've added these in a higher resolution so you can go around pixel-peeping and spotting all the small and big mistakes I made.
Have fun and enjoy!
Step 10: Remarks, Potential Improvements & STL Files
Remarks / Potential Improvements:
First of all I am happy to say that I have fullfilled all my general goals. The wand is definitely 3D-printable and can look quite good if some effort is being put into finishing it. And though few details were added compared to the previous iteration, I think they're good ones and the serve to improve the general looks of the Sonic Wand. Adding the steel rod is a success as well I'd say - the completed wand weight something around 160g, which is about your average 5-ish-inch-smartphone weigth. It balances pretty nicely, too, with the balancing point being somewhere around the flat marbled part towards the front of the Sonic Wand.
The design itself might be improved a bit to resemble the real Sonic Screwdriver more and there might be some improvements to get better printability. Maybe making the connectors / braces / whatever connecting the body of the Sonic Screwdriver to the emitter part seperately printable parts which would pretty much remove the need for supports.
If I had printed the wand part, painting it like wood would have been hard, especially as there is no real texture there. I'll have to look into texturing the STL file to look like wood, though then the removal of seam lines and the general sanding will become much harder. I think pretty much the only good way for smoothing would then be sandblasting, but access to that is rather limited. So unless a lot of effort is put into cleanup, printing the wand smooth and learning how to paint wood-like pattern seems like the better choice. Plus, I currently don't have the spare time to look into texturing STL files / models.
Hand-drilling the wooden wand part led to it ending up crooked. That's virtually impossible with a 3D printed part. Maybe I should have printed it completely after all, but then again, the Fimo accents look really nice and aren't possible with PLA parts. A larger drill press or proper lathe might help, or designing and 3D-printing a drill guide.
The gems / crystals do come out quite well, but still need some finishing after demolding. I guess I could make something like a drill adapter to glue them on to with some hot glue for much easier and quicker finishing. Hot glue is, thankfully, easily removeable with some IPA / rubbing alcohol / denatured alcohol after all and should not leave any residue.
The painting went surprisingly well and I think the finished wand looks pretty neat. The marbling might need some improvement, maybe a few different grey-ish or even red-ish / brown-ish stains to break up the monotonous white surface. Perhaps a subtler pattern might have been better, too. And though I like how everything came together I do wonder how a properly weathered one would look like.
And with this I should be free from requests to remake this wand as anyone can print it themselves, or get it done for a very reasonable price, e.g. at 3dhubs. I wouldn't mind making full or partial kits though as that doesn't take away too much from my free time which I'd like to invest into other projects if at all possible.
STL Files:
Now as promised, here are the STL files of all the different versions of the Sonic Screwdriver Wand V2: Back with a FDMgeance (my initial working title which didn't make the cut).
You can download them here, or head over to my thingiverse account, where you'll find them under the following link:
https://www.thingiverse.com/thing:3238594
That's just if you prefer to download things on thingiverse rather than instructables, for whatever reason. Keep in mind that I have added a prefix to the files grouping them together. You just need to print the files with the same prefix, and pick whichever version you like the most.
Different STL file series, based on prefix:
- A: One single, solid piece of a wand with grip
- B: Two solid pieces, wand and grip
- C: Four solid pieces, wand and grip, cut in half for easier printing
- D: Two solid pieces, wand and grip, but with a bore to allow for a 22cm, 8mm diameter rod to be used for connecting the pieces
- E: Four pieces, wand and grip cut in half for easier printing, all with a bore to allow for a 22cm, 8mm diameter rod to be used for connecting the pieces
- M: Moldmaking pieces. Slightly oversized gem / crystal with a 15mm long, 8mm diameter stem for sanding and moldmaking, as well as an endcap for testing the fit of the sanded gem
Note that the gem is always and extra piece and doesn't count here.
Final Remark:
In any case, have fun using them and as always I welcome any kind of criticism, remarks or ideas for improvements and such. If you think you have a nifty design change proposal, do tell me and I'll see if I can put it into practice. I'll also be very happy if I get to see pictures of your very own copies of this wand.
Attachments
A_SonicWand_WandWithScrewdriver.stl
B_SonicWand_Screwdriver_Body.stl
B_SonicWand_Wand.stl
C_SonicWand_Screwdriver_Body_Half1.stl
C_SonicWand_Screwdriver_Body_Half2.stl
C_SonicWand_Wand_Half1.stl
C_SonicWand_Wand_Half2.stl
D_SonicWand_Screwdriver_Body.stl
D_SonicWand_Wand.stl
E_SonicWand_Screwdriver_Body_Half1.stl
E_SonicWand_Screwdriver_Body_Half2.stl
E_SonicWand_Wand_Half1.stl
E_SonicWand_Wand_Half2.stl
M_Moldmaking_Crystal.stl
M_Moldmaking_Testing_Cap.stl
SonicWand_Screwdriver_Crystal.stl
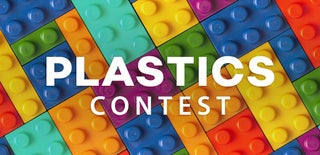
Runner Up in the
Plastics Contest