Introduction: Stained Glass Blue Suncatcher
Just as a dreamcatcher traps all the bad dreams, this suncatcher traps sunlight to brighten your day. If you follow my step by step Instructable, even a beginner can create this eye catching work of art.
Step 1: Materials & Tools
Materials -
- Blue glass
- Clear glass
- Solder
- Copper foil
- Copper wire
- Decorative steel wire
Tools -
- Pattern & scissors
- Sharpie
- Straight edge (ruler)
- Glass cutter oil & applicator sponge
- Glass scorer/cutter
- Grozer-breaker (glass pliers)
- Fid (foil burnisher)
- Grinder coolant
- Glass grinder
- Safety glasses
- Manila file folders
- Paper towels
- Cardboard
- Push pins
- Safety flux
- Paint brush
- Glass cleaner
Step 2: Pattern
When coming up with a pattern, I wanted something that would show off these beautiful pieces of glass I had that, when held up to the light, just dazzled. This started the suncatcher idea. I wanted to use a hexagon pattern like a dreamcatcher, but also wanted more realistic feathers than glass suncatchers usually provide. I made these by drawing what I wanted, scanning my drawings into the computer, and then using the smart line function in Microsoft Word to trace out my pattern. Pro tip: clipart works as great stained glass patterns. As long you can cut out the paper pieces, you can likely make it out of glass.
The feather patterns are about 5-1/2" tall and the dreamcatcher is 9" in diameter (both provided above). It is helpful to print out two copies of your pattern, label the pieces identically on both copies, and then cut out the pieces on one of the copies. This way you can check an individual piece's dimensions and see how it fits into the project at large.
Attachments
Step 3: Color Selection
While this suncatcher would be gorgeous if it used all the colors of the rainbow, I really wanted to evoke the feeling of a bright, summer day, so blue was the natural color to choose. I used a variety of blues to create a patchwork border around the suncatcher, showing how versatile one color can be in your artwork. (Other frame possibilities are wood grain glass, the rainbow, or a pure white border.) I also wanted to accurately depict the "threads" of a dreamcatcher, so I used clear glass with straight line striations that run through it for center. In the last step I add a black patina on the threads, which helps the center pop. I kept the silver of the solder throughout the rest of the piece to accentuate the blue and to help differentiate the black “threads”.
Step 4: Cut Glass
Cutting the glass, for me, is one of the most rewarding steps. Layout your pieces carefully and thoughtfully. I try to accomplish two goals at once: 1, I actively conserve my glass, cutting only what I need. 2, I consider how the grain or pattern of the glass will affect my final image. As you see with the above picture you can get some crazy cuts to help conserve glass. Start by laying out your cut pattern pieces on the glass and draw around the final shape of the pieces. Then, mark out the cuts you will make to separate the pieces. I like to leave a little extra space around my piece and then grind to my final shape, as this lets me perfect the parts and insure they fit tightly. With only a glass cutter and patience you can cut out some complex, tight curves. The trick is to use a glass cutter that is not dull, oil your cutter regularly, and tap the crack along your score to release your shape. Make your cut firmly, but not so hard you can see chips popping off. Surprisingly little pressure can achieve great results as long as it is consistent. Then tap the ball on the end of your glass cutter on the opposite side of your score line. Begin on one side and then move to the other and repeat. Insure the glass is only a few inches off the work surface because, as you tap, a crack will appear out of your score line and then your cut piece will break free soon after. The amount of control you get with this method is incredible, and I did not break a single piece of glass with this score and tap method. It is incredibly satisfying to not have to re-cut a particularly complex part! I like to cut all my pieces out and do a quick clean of my area before moving on to the next step. Be sure to keep all of your pieces organized and labeled, especially those identical hexagons. Something to keep in mind for the hexagons is that most have 5 straight sides and a curved side; I used an arrow to mark the curved side so it would be easily noticeable when I went to grind.
Step 5: Grind
Now comes the zen part of stained glass artwork: grinding. Like I said in the last step, I like to leave a little extra on my glass so I can grind to my final shape. However, too much grinding can be exhausting so be sure to trim extra with the glass cutter if you left more than a 1/4" of glass around your lines. Be sure to fill your reservoir with plenty of water. I also pull the sponge out and pour a little grinder wheel coolant on it. After replacing your sponge, turn on the grinder and let it run until the head is completely dampened before you start to grind. While you wait, set up your manila folders (or other guard) around the glass cutter; this will help with glass spraying everywhere.
Put on your safety glasses now! Hold your glass down securely with the finger tips of both hands and apply even firm pressure to the grinding head. Take off small layers at a time or grind to your final shape by slowly carving out the piece, whichever works best for you. I find myself switching between both methods. Either way, don't use too much pressure; if you're bogging down your grinder you are using way too much pressure and are liable to break your glass or your machine. Grind all pieces, checking the shape with the cut pattern pieces as you go along. You will likely need to reapply the sharpie as it gets washed off from the grinding coolant/water mixture. Silver sharpie, while easier to see, needs to dry for a long time or the smallest amount of water will remove it. Some people rubber cement the pattern piece to the glass insuring the pattern is always there, but I do not enjoy the cleanup, and I also like to save and reuse my pattern pieces. After each individual piece is ground, place it on the overall pattern, and insure it fits next to its brothers and sisters. The tighter you can make things fit now, the less gaps you have to fill when you begin to solder.
Step 6: Copper Foil Wrap
We will be constructing our vibrant blue suncatcher via the copper foil method. To do this, we must first clean our pieces thoroughly with glass cleaner, as we want the greatest amount of adhesion as possible. Keep track and label the pieces you spent so much time grinding to perfection.
I used two different copper foil tapes in this project. One is black backed and was used on the transparent pieces to give the illusion that the "threads" go all the way through the glass. The other was copper lined, which I used for the rest of the piece.
First guestimate how much foil tape you will need. Then peel back just an inch or so of foil. Apply the foil to the edge of the glass trying to split the difference so both sides of glass have an even amount of foil when they are pressed down. Start your foil on an inner edge (a side that touches another piece) to insure your suncatcher foil and solder don't unravel later on. Next pinch the sides down leaving the corners sticking up. Then, fold over the corners, again trying to insure a smooth continuous edge of foil encircling the glass. Pick up the fid and use it to burnish, or smooth, all the edges of the piece you foiled. Cut away anything that doesn't overlap correctly or overhangs too far on one side. If you don't like a piece simply remove the foil and start over. Proceed to wrap all of your pieces.
Step 7: Solder
Soldering is another one of those fun parts. I like to lay out my pattern on a cardboard box and use push pins to hold everything together. The cardboard will burn if you leave your soldering iron on it to long, but will only singe if the solder drips on it. I find that using cardboard is an excellent way to preserve my plastic glass-working table.
Start by applying a generous layer of flux to the copper foil using a brush. Flux helps your solder stick by removing any oxides or dirt that forms on the copper as it is exposed to air. If you ever find a piece is not soldering correctly add more flux and nine times out of ten you will fix your problem. Start by tacking all the intersections together. I have a rheostat switch on my soldering iron, and I leave it set just under 5 for most of the soldering process. I like to start on the inside and move out, reapplying flux as needed. After you've tacked everything together, its time to tin your piece. Using the solder that is left from tacking, spread it all over your copper foil until everything is gleaming silver. Again, flux well and flux often. If you like the tinned look, stop here and move on to tinning the back. If you'd like a thicker bead of solder, load your iron with more solder and pull this extra solder across your piece. Try pulling smoothly and consistently. As you pull your iron across adding solder along the way, you'll get a raised bead of solder that leaves the project strong and beautiful. Make sure you flip and solder both sides of your piece, being careful not to melt the solder on the other side.
Step 8: Wire
For the large hanging loop and feather loops, I made mine out of copper wire. Simply wrap a few inches around a pencil or other dowel and then cut out your loops. For the main hanger I made sure i had a few loops of copper wire. The suncatcher to feather connectors only needed one loop, and the loop on the actual feathers were the smallest. After the loops were made I fluxed the wire. While holding the loop with pliers - or your grozer-breakers - tin your loops with solder. This step is not necessary, but it does make the loop stronger and blends it all together. Next flux and solder your loops in your desired location; I chose three intersections on the border patchwork to get my feather spacing right. Feel free to test fit your steel wire in and get a preview of the finished piece, but don't attach them permanently yet unless you are skipping the patina step. Also be careful as the steel wire is more rigid than the copper and you can bend your loops easily if you're not careful.
Step 9: Patina
Almost done! This last step really makes this piece pop! By using a controlled patina to blacken the "threads," you really bring your dreamcatcher to life.
Start by removing the feathers if you temporarily attached them. Being careful not to get it on you or on any of the border pieces, apply the patina to the center "threads" using a paper towel. Patina is a special acid that oxidizes the solder in a way get a desired color. Usually, by applying more patina you get a darker color. Since patina is an acid, be sure to wash your hands if you get any on you. After you patina, take a damp paper towel and wet all the patina-ed areas. This neutralizes the acid an keeps your other pieces from oxidizing as you clean off your work. Finally wash and windex everything until it shines like the sun it caught!
Step 10: Catch Some Sun
Attach all your feathers securely and add a wire to the top to hang your new brilliant suncatcher. If you chose translucent glass, your artwork will positively glow in the sunlight! I find it best to hang indoors in a window that gets plenty of sun. However, in keeping with the dreamcatcher theme, it is perfectly acceptable to hang in your bedroom window to filter out all the bad dreams and stream in the light! I hope you enjoyed this project. Let me know if you make one too or have made something similar!
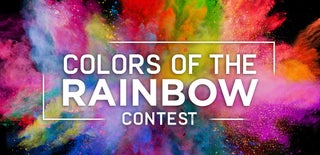
Fifth Prize in the
Colors of the Rainbow Contest