Introduction: Stained Glass Flying Turtle Lamp - Low Poly Model to Stained Glass
There were three main sources of inspiration for this project.
- A stunning, multi-color sea turtle mural in Halifax which I visited back in 2018.
- The fascinating Flying Sea Turtle model by amaochan on Thingiverse.
- My mom who's getting back into the hobby of stained glass. She offered to make me a window for Christmas, but instead we decided to collaborate on a more challenging 3D glass structure.
- The Chetywnd Public Library. Big thanks for the use of your Taz 6 3D Printer.
My intent for this instructable is to document a process for converting any "Low Poly" 3D model into stained glass. The technique worked really well for turtle shell, so I believe it could be applied to almost any low poly model. Don't be scared to try. Straight lines and convex shapes are the easiest thing to cut out of glass, and low poly models basically guarantee that those conditions are met. As long as you can extract the 3D printed form after the glass has been soldered together, the sky is the limit.
Personally, I learn the best from watching videos so I've included links to videos for the generic stained glass steps (2-4). The other stained glass instructables are also good resources to look at if you need a bit more clarity.
Supplies
Safety
- Cut proof gloves
- Sharps container
- Shoes*
- Nitrite gloves*
- Safety glasses
- Newspaper
- Brush
Environment
- Warm
- Good ventilation
- Desk with comfortable working height
Design
- A low poly 3D printed template. The facets on the model should be at least 1”x1” in area for a visually appealing end result
- Masking tape
- 1” and 2” wide
- Pencil
- Sharpie
- 8.5x11 paper
- Crayons or pencil crayons that match glass colors
- Ruler, 6” cork backed if possible
- Utility knife or razor
Glass Cutting
- Art glass
- Hard flat cutting surface (cutting board)
- Glass cutter w/oil
- Glass breaking pliers (grozing pliers)
- Diamond stone or glass grinder*
- Dish soap*
- Paper towel
Copper Foiling
- Copper foil (13/64” with black adhesive)
- Lathekin (fid) or stick
- Scissors
Soldering
- Soldering iron
- 60/40 solder
- Flux
- Acid brush for Flux
- Patina
- Cotton swabs
- Carnauba wax (must be Turtle brand for maximum effectiveness ;)
Accessories
- 14-gauge copper wire
- Steel wool
* not included in picture
Step 1: Creating the Template
- Use a pencil to highlight the edged on the 3D printed model. Depending on the model you’ve selected, this step might not be necessary, however for the turtle shell model, there are a few very subtle transitions between facets (flat regions) so it’s important to highlight them.
- The facets on the turtle shell model were a bit too large for an ecstatically pleasing stained glass lamp, so we decided to subdivide several of the larger facets using a pencil.
- I decided to cheat on pieces 5 and 8 on the template. Technically speaking, these pieces should be split into two to match the facets on the model, but I thought they looked better as a single piece, so I took the risk.
- I also decided that pieces 13 and 21 weren't necessary, so I deleted them.
- Number each facet on the 3D printed form using a sharpie.
- Stick pieces of masking tape to cover each facet. When applying the tape, align the straight edge of the tape to a straight edge on the model to reduce the chance for error when trimming the tape to size.
- Use a utility knife or razor to trim the edges of the tape to match the model edges highlighted in pencil. A corked back ruler is an excellent straight edge to guide the razor because it prevents the ruler from sliding around.
- You can overlap 2 pieces of adjacent tape and cut them both at once to ensure that the seams match perfectly. After the cut has been made, carefully remove the excess tape from either side.
- Trim the masking tape edges so the corners of each piece of tape are aligned
- Copy the facet numbers from the 3d printed model to the masking tape template using a sharpie. I highlighted the tape edges to highlight them for this tutorial, it’s not necessary to do this in practice.
- Place the 3d printed form on a piece of white paper and trace the outline using a pencil.
- Sketch out the facet edges on the paper template and transfer the facet numbers to the paper template also.
- Use crayons/pencil crayons to color in the facets on the paper template. We iterated through this process several times before we landed on a final solution. I would recommend doing the same as you’ll only have one chance to cut the glass.
Step 2: Cutting the Glass
- Watch this video (https://youtu.be/C6jyP0_nEoM)
- Identify which surface of the glass you want exposed in the final product, generally the textured side. We’ll call this the working surface. Place a piece of masking tape in the middle of the glass to help you remember which side of each pane is the working surface.
- Carefully remove the correct (color matched) pieces of masking tape from the 3d printed template and stick it to the working surface of the glass. Make sure you align one straight edge from the masking tape template to a straight edge on the art glass to keep the number of cuts to a minimum.
- If you’re cutting multiple pieces of glass of the same color, transfer all the masking tape templates to the glass and cut them all out at the same time. Once all the template pieces have been transferred, score and cut a bigger chunk of glass for further subdivision.
- Put on your safety glasses, gloves, shoes and prepare the container for glass shards. Don’t let them escape and find their way into someone’s eye, foot or other body part.
- Flip the glass so the flat surface is up (the masking tape template is on the bottom) and use the glass cutter and a straight edge to score the glass. You must have a continuous score across the glass, from edge to edge. The little carbide wheel is the part scores the glass.
- If you’re having trouble seeing the template edge through the darker glass, put a piece of white paper under the glass, or use a light box, to highlight the edge.
- I prefer to push the glass cutter away from myself while scoring, but I’ve seen it done the other way also, so use which ever method that feels right for you.
- Only score the glass once and get it right the first time. Double scoring only makes the break line more unpredictable.
- Tap the underside of the glass using the glass cutter several times along the score line to weaken the score line. If you’re tapping correctly, you should be able to see the fracture moving through the glass.
- Use your hands or a pair of grozing pliers to break the glass along the score line by applying pressure to the opposite side of the glass.
- If the broken edge of the glass is uneven, or if the piece of glass is oversized, use a diamond stone to grind the glass to exactly match the masking tape template.
- The diamond stone that we described in the materials section will do the job, but we had access to an electric glass grinder, so we cheated.
- After every piece of glass has been cut/ground to the final dimension, test fit them on the 3d printed model. Use rolled up pieces of masking tape, stick side out, to hold each piece of glass in place. This will give your enough wiggle room to squeeze all the pieces in.
- If the pieces don’t fit nicely, continue grinding them until they fit perfectly. I had to touch up several of the pieces (21-28) to make them fit properly.
- 1mm-3mm gaps between pieces won’t be a problem to solder, but you should probably re-cut or re-adjust the pieces if the gaps are greater than 3mm.
- After you’re happy with the test fit of the glass, peel the masking tape template off of each piece and transfer the piece number to the glass surface using a sharpie.
- I stuck all the masking tape templates to a piece of overhead transparency (clear plastic) so that I could re-use them in the future.
- Use the diamond stone to break the sharp edges of all the glass pieces. This will make the copper foiling process much easier
Step 3: Copper Foiling
- Watch this video first (https://youtu.be/wsyEmIyTzSU)
- Clean each piece of glass using warm water and dish soap, and dry using paper towel.
- Peel back a small portion of the copper foil backing and stick the copper foil to the edge of the glass first.
- Start the tape in the middle of an edge (not on a corner)
- If the piece of glass is along the edge of the finished piece (pieces 1-12), make sure you start the foil tape on an internal edge of the glass.
- Make sure the copper foil tape is centered on the edge of the glass, so that the excess foil tape exposed on either side of the glass is equal. This was impossible to capture in a picture so you’ll have to take my word for it.
- Remove more of the foil backing and work your way around the edge of each piece of glass, working on one edge at a time. Keep the copper foil tape centered and avoid folding the edges down until the entire piece is finished.
- Make sure you use one continuous piece of each piece of glass.
- If you make a mistake, peel the copper tape off and start again.
- After all edges of the glass have been taped, use scissors to trim the foil tape to the final length. You should target between ¼” and ½” of overlap.
- Use a fid (fancy name for a stick) to firmly press the copper foil onto the edge of the piece. Work around all edges of each piece.
- Use your fingers and the fid to fold and press the copper foil tape around all edges of the glass, adhering it to the flat surfaces of the glass.
- Leave the corners alone until all the edges have been addressed.
- Use the fid to neatly fold the copper tape at the corners, similar to how you neatly fold the edges of wrapping paper when wrapping gifts. Tidy copper foiling results in good looking and strong solder joints. Practice a few times 😊
- Firmly press the copper tape onto each glass surface using the fid. Don’t take any short cuts on this step. Proper foil adhesion is vital for strength.
Step 4: Final Assembly and Soldering
- Watch this video (https://youtu.be/5RHDGAU0lx8)
- Lead solder, flux and flux fumes are all bad for human consumption. Work in a well-ventilated area, don’t snack while soldering and wash your hands thoroughly and often. Sweep up any solder blobs that might spatter around before you’re finished.
- Use rolled up pieces of masking tape, stick side out, to stick the foiled glass pieces onto the 3d printed template.
- This is your last opportunity to fix any pieces that don’t fit properly. Considering the time you’ve invested in this project so far, don’t settle for less than perfection here. The cost of re-cutting, re-grinding and re-foiling a 1 piece of glass is minimal in comparison to a final product that doesn’t look good. That being said, stained glass is an art form because it takes experience to make a beautiful finished product. Often failure is the best way to get experience, but in this case, just take my advice 😊
- If your copper tape is showing signs of tarnish, use some steel wool to buff the copper tape to a bright shiny polish.
- Prop up the 3d printed form with the glass attached, so that the top surface is level. If you try to solder the joints on a slope, the solder will run and pool at one end, which doesn’t make for a strong or attractive joint.
- Apply flux to the corners of the pieces on the level surface using an acid brush. Apply flux to 1-3 corners at a time and solder them as you go. I used paste flux so it didn’t flow all over the place, but liquid flux should also work.
- I decided to solder all the outside pieces together 1-12 then 14-19 before moving to the middle pieces 21-28.
- Use the soldering iron to melt the 60/40 solder onto these fluxed areas. I suggest keeping the soldering iron close to the joint and feeding the solder into the soldering iron to melt it directly onto the coper. This is an old habit from electronics soldering, which uses flux core solder, but it works well for stained glass too. If you absolutely have to, you can melt a blob of solder to the end of the iron and transfer it to the copper that way. Using this technique won’t work later in the process.
- The goal with this first step is to lock all the pieces into their final position. If you need to adjust the positioning of a piece, it’s much easier to re-melt the solder in the corners only, instead of re-melting the solder along all 4 edges of the piece simultaneously.
- Continue steps 2-4 until all the corners of each piece are tacked together, making sure to adjust the work piece so you’re only applying solder to level joints.
- After you’re happy with the fit, apply flux to the edges of the glass, and the pre-soldered corners, only a few seams at a time.
- Melt the solder into the joint and once a bead of molten solder forms in front of the iron, start moving the iron along the seam. The solder will flow and fill the joint and cover all the copper tape.
- Re-melt all the pre-soldered corners during this process. The end product will look better
- Make sure all the copper tape has been covered in solder before you’re finished with this step.
- If you need to re-work any seams, allow time for the glass/solder to cool before proceeding. Thermal expansion isn’t a huge problem for small pieces of glass, but you don’t want to risk cracking a piece in this final stage.
- Repeat steps 8-9 for all the seams.
- Remove the glass from the frame. I was able to pry the glass away by hand, but if you’re worried that you might over stress the solder joints, slide a razor between the 3d printed form and the glass and cut any pieces of masking tape that you can.
- Flip the piece over, apply flux and solder to the backside of each seam.
- Work quickly when soldering the back side of the glass. If you hold the soldering iron for too long in one location, you risk melting all of the solder which will cause it to flow out of the joint.
- Finally, run a bead of solder around the outer edge of the work piece. All the copper tape needs to be covered in solder, both for strength and beauty.
- Cut and bend 3 “L” shaped pieces of 14 gauge copper wire
- Re-flux to the underside of the glass seams where you intend to attach the copper wire. Hold the copper wire using pliers and then solder the wired to the stained glass. I used the blob of solder on the iron tip technique because I ran out of hands. The wire will be used to attach the glass to the 3d printed lamp base.
- I didn’t stress about the location of these wires. Instead, I just manually drilled the holes into the lamp base after the fact.
Step 5: Patina and Final Polishing
- Use warm water, dish soap and paper towels to clean the flux off the soldered work piece. Make sure you clean both surfaces of the glass and repeat this process several times until the glass and the solder is clean and dry.
- Flux is nasty stuff, so you’re cleaning for health reasons here, not just for beauty.
- I like to give my pieces a few hours to dry in a warm place before proceeding just in case there’s water hiding somewhere. This is a good opportunity to go for a walk… also for health reasons 😊
- Wear eye protection, gloves and shoes. Patina is also bad for human consumption. Wash your hands thoroughly and often.
- Before applying patina, use some steel wool to buff and clean all the exposed solder.
- Pour a little patina (1-3 ml) into a bottle cap. A little dab will do you, so don’t go overboard.
- Never pour excess patina back into the original bottle. If any solder gets transferred back into this bottle, unintended chemical reactions will occur, and your patina won’t work properly any more. Avoid cross contamination at all costs.
- Start on the underside of the glass and use a cotton swab to absorb some of the patina and rub it over the clean solder joints.
- The cotton swab will discolor as you apply the patina. I rub until I the patina runs out of gusto, then I use a fresh cotton swab to absorb some more patina and apply it.
- Avoid re-using a contaminated cotton swab for several application, to avoid cross contamination. I used 5+ cotton swabs to apply the patina.
- The reaction between the solder and the patina only happens once, so there shouldn’t be a need to re-apply patina more than once.
- If it doesn’t look right after one application, it’s possible that the solder wasn’t clean to start. Buff it back down to clean solder using steel wool and try again if you must.
- After all the solder joints are the correct color, wash the glass using dish soap and warm water, then dry with paper towel
- Use paper towel, or a soft cloth to apply carnauba (Turtle) wax to the finished piece.
- Allow it to dry for a second then buff it to your hearts content.
- Clean up, wash your hands and give yourself a pat on the back. You’re finished.
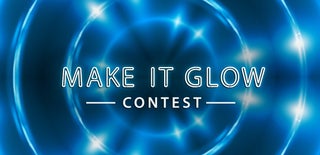
Participated in the
Make it Glow Contest