Introduction: Steampunk Gentleman's Cane
Any steampunk gentleman's wardrobe is not complete without a sturdy and fashionable cane. I've always wanted to make a cane, and I love steampunk so it seemed natural to put the two together. That being said, I made this cane about a year ago and I'm just now getting around to making the instructable so there might be a few details missing. If that is the case, please, post questions and I'll add the missing bits to the main post. Thanks in advance and let's get building!
Step 1: Materials and Tools
Materials:
1 x 3 foot by 3/4" oak dowel
Various gauges of copper wire
A small length of 3/4" copper tubing (~2" would be plenty)
Assorted brass gas line fittings (I'm not sure what the specific names of the fittings are, I just experimented with a few extras that I had
to figure out how they went together to make a good cane head)
5-minute epoxy
Solder
1 x ~1 1/2" screw
A few small (~1/4") screws
1 x castor-tack-thing, I'm not sure exactly what it's called, but basically it's a large tack with an oversized head (~1/2"). Although, a scrap of thick rubber wight work better for the purpose.
White vinegar
0000 steel wool
Black tea
Spar varnish
Paper towels
A couple dixie cups
Tools:
Hacksaw
A few files
Soldering torch
Wire clippers
Drill
Vise grips
A Dremel (not necessary, but it sure makes things easier)
Small hammer
Gloves
Bench grinder or disk sander (not necessary, but again, it makes things easier)
1 x 3 foot by 3/4" oak dowel
Various gauges of copper wire
A small length of 3/4" copper tubing (~2" would be plenty)
Assorted brass gas line fittings (I'm not sure what the specific names of the fittings are, I just experimented with a few extras that I had
to figure out how they went together to make a good cane head)
5-minute epoxy
Solder
1 x ~1 1/2" screw
A few small (~1/4") screws
1 x castor-tack-thing, I'm not sure exactly what it's called, but basically it's a large tack with an oversized head (~1/2"). Although, a scrap of thick rubber wight work better for the purpose.
White vinegar
0000 steel wool
Black tea
Spar varnish
Paper towels
A couple dixie cups
Tools:
Hacksaw
A few files
Soldering torch
Wire clippers
Drill
Vise grips
A Dremel (not necessary, but it sure makes things easier)
Small hammer
Gloves
Bench grinder or disk sander (not necessary, but again, it makes things easier)
Step 2: Assembling the Head
This will probably be the least helpful step because I don't know the names of the specific gas line fittings I used to make the head. However, that being said, unless you just want to reproduce this design, you shouldn't need the names. What makes gas line fittings and really and metal pipe fittings so great for this is that they come in so many shapes, sizes, and configurations. My advice is to find a bucket of old scraps or a store that has different fittings out, and just start mixing and matching until you find a design you like. Also, don't be afraid to modify stock pieces by soldering things on or cutting things off. As you can see in the pictures, I kept my design pretty simple with just a little added wire coiling.
Step 3: Shaping the Shaft
The only significant shaping I did on the shaft was to reduce the size of the top end enough so that it would screw inside the pipe reducer fitting that served as the connection between the head and he shaft. As you can see in the pictures, the inside of the fitting was tapered after the threads, so I used a disk sander to taper the end of the shaft to match. The shoulder was also necessary to get the shaft as far inside the fitting as possible for maximum strength. Once the taper was correct, I used emery cloth to reduce the diameter of the end of the shaft just enough of where I could start threading the fitting on. To finish threading the adapter on, I soked the shaft end in water for a few minutes to soften the wood. (I am aware that this also causes the wood to swell, all I can say is that it worked for me, whether that was luck or not I don't know) After finally getting the adapter threaded on, I left it on the shaft while allowing the wood to dry. When the wood was completely dry, I removed he fitting and drilled a hole in the very end of the shaft to accept a retaining screw. This is kind of optional because you could just epoxy the fitting on, but I wanted to be able to remove it if I wanted to so I opted for the retaining screw. If you do use the screw, you will want to use a screw with fairly coarse threads, ~1.5" long, and a head smaller than the outer diameter of the adapter's small end yet larger than the inside diameter of the small end's hole. Hopefully that all makes sense.
Step 4: The Ferrule
I kept the ferrule very simple in style, but with this design, you can get fancy if you like by cutting designs into the copper. Anyway, I started with a length of 3/4" copper tubing that was about 1 1/2 to 1 3/4" long (arbitrary). Using some emery cloth, I sanded the end of the cane down until the tubing fit snugly over it. Above the ferrule, I tapered the shaft back up to full thickness; other than that, the shaft is completely straight. The last thing I did to the shaft was to round the edges over to match the rounding of the copper ferrule which I will describe next. Once the tubing was rough fitted, I took a piece of bar stock that fit inside of the tubing and ground a rounded profile on one end to use as a form for the ferrule. With the bar stock clamped in a vise, I place the tubing over it. With a propane torch I heated the copper and, working my way around edge, rounded the end over by tapping it with a small ball peen hammer. After the copper had cooled, I filed out the end hole on the ferrule to match the diameter of the castor tack. To attach the ferrule, I drilled small screw holes at 120 degree increments around the copper tube, I also pre-drilled the holed into the wood once I had the ferule positioned where I wanted it. The castor tack was driven into a pre-drilled (undersized) hole in the end of the cane. I should mention that the reason I filed out the hole in the copper ferrule to match the castor tack was so that if the copper sleeve were ever damaged or I just wanted to change it, I would not have to pull the castor tack as well. The one downside of the castor tack is that it does not grip very well on slick surfaces, so you may just want to use a thick piece of rubber epoxied or tacked in its place.
Step 5: Ebonizing
At this point, you can use any finish you would like, but I opted for ebonizing. Ebonizing is a chemical reaction between iron acetate and the natural tannin in the oak wood, it will work with other woods, but not quite to the same degree. While not as simple as staining, this process is actually really easy and results in a beautiful coal black finish without resorting to paint.
The process requires a little prep time for ingredients, so plan accordingly. First to make the iron acetate, all you need to do is put a wad of 0000 steel wool in a jar of white vinegar and let it completely dissolve, this will probably take a day or more. Note: Make sure to leave the lid of the jar loose so the gases from the reaction can escape. The result is a dark rust colored liquid. This is really the only ingredient you need to ebonize the wood, however to make the finish darker you will want an extremely strong brew of black tea. The tea will be used as a wash to increase the amount of tannin in the wood's surface layers.
To prep the wood for the finish, raise the grain by slightly dampening the wood and allowing it to dry; this will make the surface feel a bit rough. Take some fine sandpaper and gently remove the roughness; you don't want to scrub very hard, just enough to smooth the surface back out.
Pour a little of each component into separate dixie cups. You want to be careful not to mix them or contaminate the main jars because you only want the reaction to take place on/ in the wood. Sponge brushes would work, but I just used folded up paper towels to apply the liquids.
First step: Wipe on two liberal coats of the tea and allow to dry until the wood is just damp to the touch.
Second step: Wipe on the iron acetate solution until the wood doesn't seem to be getting any darker and allow to dry until damp.
At this point, the finish may look a bit chalky, don't worry, it gets better.
Third step: "Wash" the wood by wiping it down with a couple passes of the black tea and allow to dry completely.
After it has dried, it might be a good idea to gently wipe the surface down with a soft cloth (a little black will come off). And that's all there is to ebonizing. Now you're probably looking at your piece of oak thinking "It's black, so what. I could have done that with spray paint in half the time." Well, all I can say is have patience my friend, the character of this finish will blow you away once the clear coat is on.
The process requires a little prep time for ingredients, so plan accordingly. First to make the iron acetate, all you need to do is put a wad of 0000 steel wool in a jar of white vinegar and let it completely dissolve, this will probably take a day or more. Note: Make sure to leave the lid of the jar loose so the gases from the reaction can escape. The result is a dark rust colored liquid. This is really the only ingredient you need to ebonize the wood, however to make the finish darker you will want an extremely strong brew of black tea. The tea will be used as a wash to increase the amount of tannin in the wood's surface layers.
To prep the wood for the finish, raise the grain by slightly dampening the wood and allowing it to dry; this will make the surface feel a bit rough. Take some fine sandpaper and gently remove the roughness; you don't want to scrub very hard, just enough to smooth the surface back out.
Pour a little of each component into separate dixie cups. You want to be careful not to mix them or contaminate the main jars because you only want the reaction to take place on/ in the wood. Sponge brushes would work, but I just used folded up paper towels to apply the liquids.
First step: Wipe on two liberal coats of the tea and allow to dry until the wood is just damp to the touch.
Second step: Wipe on the iron acetate solution until the wood doesn't seem to be getting any darker and allow to dry until damp.
At this point, the finish may look a bit chalky, don't worry, it gets better.
Third step: "Wash" the wood by wiping it down with a couple passes of the black tea and allow to dry completely.
After it has dried, it might be a good idea to gently wipe the surface down with a soft cloth (a little black will come off). And that's all there is to ebonizing. Now you're probably looking at your piece of oak thinking "It's black, so what. I could have done that with spray paint in half the time." Well, all I can say is have patience my friend, the character of this finish will blow you away once the clear coat is on.
Step 6: Wrapping the Wire Collar
To wrap the wire collar, I drilled a shallow hole in the side of the cane just below the bottom edge of the pipe fitting when it was screwed on. I bent the very end of the wire I was going to use into an "L" shape and epoxied the short part of the L into the hole I had drilled. Once the epoxy had set, I would begin wrapping the wire. Working quickly, I smeared a thin coat of epoxy onto the shaft down to the line I wanted to wrap to and began coiling the wire around the shaft. When I got to the end mark, I used a pair of vise grips to wold the wire from uncoiling while the epoxy set. After the epoxy set, I cut off the excess wire and used my dremel to grind the edges off the end of the wire coil. As with any of the metal parts on the cane, polishing is optional depending on the look you are going for.
Step 7: Finishing
There's not much to say about finishing other than I used three coats of gloss Helmsman spar urethane as prescribed by the directions on the can. Oil and wax finishes will work as well, but the spar urethane is the most durable. Also, remember to tape off the wire collar; I don't think urethane adheres to metal very well.
Step 8: Finished Product
Once the finish cures, you can assemble all the pieces and admire the steaminess of your handiwork. And there you have it, a sleek and stylish cane to show off your steampunk side for an evening on the town or to complement your best costume. I hope you enjoyed this instructable and feel free to post question, I'll answer them as soon as classes allow.
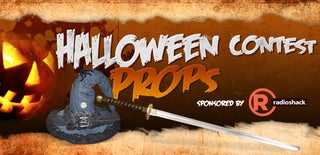
Participated in the
Halloween Props Contest