Introduction: Steel Viking Helmet
In this Instructable we will be looking at how to fabricate a Viking style helmet out of steel. Looks great for a costume or for LARPing. Please note that this will not cover the specifics of dishing planishing or welding, but the overall technique of how to go about constructing the helmet.
Materials:
*Mild Plate steel 18 or 20 gauge
*Butcher paper or card stock
*pencil and ruler
*Scissors
*Rivets, dome head
*Belt Leather
Tools:
*Metal Bandsaw OR Nibbler OR Beverly Shear
*Dishing stump
*Dishing Hammer
*Planishing hammer or English Wheel
*MIG welder
*Grinding wheel (rough grinding disks and flap wheels)
*Random orbital sander with 120 grit sandpaper
*Polishing Wheel
*Buffing wheel
Attachments
Step 1: Pattern Layout
The first step is to layout your pattern on cardstock. It is very important and helpful in metalwork to get your pattern right before you start working on your actual project. It will save you a lot of grief and time later on. For this project, I based my helmet off of an image I found online. A basic spangenhelm is comprised of 8 pieces. This particular piece also has a face mask and ear cops, which comprise an additional 5 pieces. I began with patterning out the spangenhelm, which is the most complicated part.
I do not have too many photos of the patterning stage. Please refer to the photos to get a better sense of the instructions. The outer shell of the spangenhelm is comprised of four pieces. I measured the circumference of my head, added 1/2 inch extra ( to account for padding that will be added later on), and then divided by 4. This is the width of the four outer shell pieces. I then measured from about halfway down my forehead to the opposite point on the back of my head, and divided by two. This is the approximate height of my outer shell pieces, once they are dished. I shaved off a couple inches so that when the outer shell is dished and welded together, it will leave a void at the very top of the helmet for a pair of vice grips to fit through. We will cover why later.
I freehanded the INNER curve on my outer shell pattern based on the research image. It is very important that your pattern be symmetrical, so when you are patterning your outer shell piece make sure to mark your centerline, fold your pattern in half and THEN cut it.
For the Inner ovals, I found it was easier to wait until my outer shell was welded, and then I took a tracing in cardstock (NOTE: BE SURE TO ADD ABOUT 1/8 INCH ALL THE WAY AROUND YOUR OVAL PATTERN BEFORE YOU CUT IT OUT OF METAL, OTHERWISE IT WILL FALL THROUGH!). it also helps to wait for the two inch wide band which wraps around the helmet, so you can get an accurate measurement of the outer helmet circumference.
After you have cut out your pattern, it might not be a bad idea for you to tape it together in cardstock just to get a sense that all your shapes are correct. I was pretty confident I had done everything correctly, so I decided to skip this step and go for it.
Attachments
Step 2: Cutting Out Your Shapes
It is now time to cut your shapes out of steel. I utilized a metal bandsaw for this step, but you can also use a nibbler, or a Beverly Shear. 18 gauge steel is not really thin enough to cut by hand, and even 20 gauge might cause some difficulties. If you have one, a metal bandsaw is probably the best way to go here. It is very important that all your pieces are cut carefully so the finished products are identical to each other.
Once your shapes are cut out, there will probably be some burrs from the cutting. You should either grind these away or hit them with a bastard file so you dont get cut moving forward.
Step 3: Dishing and Planishing
Now its time to dish and planish your pieces. Start with your outer shell pieces. We will come to the teardrop (re:oval) shapes later. The outer shell pieces are going to get pretty heavily dished. Focus on trying to dish them all evenly. When you move on to planishing be sure to be thorough--the better planished the easier your life will be when polishing.
Step 4: Welding
Once they are dished and planished, go on ahead and start welding your outer shell pieces. Keep in mind that a human head is really more of an oval shape than a circular shape. It might not be a bad idea to weld in two halves and then hand bend as needed to modify your shape. Once you are happy with the overall shape, go on ahead and weld it all together.
Step 5: Tear Drop Shapes
If you recall, during the patterning phase, we took a measurement of our heads and then divided by two. But we shaved a couple inches off this measurement. The reason for this is so that we can have a hole in the top of the helmet. This is going to come in handy for welding in the tear drop shapes. Now the first thing we should do is to do a general dish and planish of the tear drop shapes. We want to get them close to the general curvature of the outer shell of the helmet. Once that is done, we can use some vice grips and grip the tear drop shape on the inside of the helmet to the outer shell of the helmet. Now sneak your helmet (with the tear drop shape vice gripped in) over the planishing stake, and hammer it out until it matches the curvature of the helmet.
You want to be very attentive here--you dont want to misshape the work you've already done on the shaping of the helmet. Once your first tear drop shape is shaped and you are happy with it, move on to the other three. Keep careful track of which tear drop shape goes where. Once they are all shaped to your satisfaction, go on ahead and weld those puppies in.
Step 6: The Band
Now its time to attach the band. I over dished my outer shell pieces just a little bit, so I had to straighten the bottoms out a little bit to give me a clean surface to weld to. I just used the vice, planishing hammer, and anvil for this. I vice gripped the band to the center back of the helmet, and carefully bent it along the circumference, tack welding along the inside as I went. Make sure you are welding it on nice and level! You want your helmet to sit nicely on a table once your band is welded on. Also make sure you cut the band to the appropriate length before you weld it on. You want to be able to wrap around the entirety of the helmet, butt it back onto itself, and then weld it along the seam on the outside.
Attachments
Step 7: Top of the Helmet
Now its time to cover up the exposed hole on top of the helmet. To do this, cut out a circle (i made mine about 3 inches). Dish it, planish it, and weld it in, from the inside of the helmet.
Step 8: General Polishing
Mild steel is shipped from the manufacturer impregnated with oil to help prevent rust. If you want your helmet to have a polished finish, you are going to need to polish this away. I utilized a 3 horsepower Baldor Grinder for this purpose. I had a flap wheel on one side and a buffing wheel on the other. Be extremely cautious when polishing. You are dealing with unusual shapes, and it is extremely easy to get tips and corners caught on your wheels.
I chose to do a general polish on all my pieces before welding, to save me a little work later on. Some of this polishing will get lost when we begin welding, but we can always come back and polish away any discoloration from the heat.
Step 9: Face Mask
It's time to move on to your face mask. I patterned out my face mask in three pieces. The triangular nose piece gets welded to the center front of the helmet first, then the bottom piece which forms the lower shapes of the eyes, and then the eyebrow shapes go on top. For a really clean looking finished product, we want to avoid weld seams. So what we are going to do is plug weld our pieces--Plug welding is when you drill a hole through your piece, weld through the hole, and then grind and polish away the weld. So to sum up: Cut out your 3 face visor pieces, and figure out placement. Use vice grips to your advantage here, you want to make sure you are satisfied with the placement of each piece before you weld it on. The eye brow piece and the lower eye piece can be bent and welded along the length with relative ease. Once you are satisfied with your placement, do a light tracing in sharpie, and then drill holes in each piece where they are going to make contact with the helmet, weld them in, grind the welds, and then polish away the welds. Its particularly important to double check your pattern in cardstock, because if you have a prominent nose like mine you want to make sure it wont hit your nose piece when you put on the helmet.
To grind and polish away your weld, you want to start with your roughest abrasive first and work your way to the finest. So I use my grinding wheel to grind the weld flush, my abrasive flap wheel to smooth it out, a random orbital sander with 100-120 grit to get finer abrasions, and then the flap wheel on the Baldor grinder to get a satin finish. I am going to wait until the whole helmet is completed to do a mirror finish.
Attachments
Step 10: Details
Okay, we are getting close! My reference image had some etching along the eyebrow piece of the face mask which I thought looked pretty cool. Using a small square, I measured out in each direction from the center line of the eyebrow, and symmetrically marked diagonal lines in sharpie.
Go ahead and chuck a carbide bit into your dremel. Set your dremel on a moderate speed, and very carefully etch in along your sharpie lines. You want to use a very steady and firm hand for this. If your dremel slips it will be a pain to polish away.
Once the eyebrow lines are etched in, its time to move on to the mirror polish. Use your flap wheel to give a nice solid satin polish around the whole piece. As I said earlier, use caution with your grinder--it is very powerful and can very easily catch errant tips and pointy parts. You should be very comfortable with grinder safety. After the satin polish, hit your buffing wheel with some abrasive and polish that puppy until you can see your reflection.
Step 11: Ear Cops
Your helmet is looking pretty snazzy! Now its time to add some ear cops.These are pretty simple to pattern and build. Pattern them out, cut out two, and give them a slight dish and planish. They only need a very mild curvature. We want to add a rim to these--I did this by using some 1/8 inch steel rod which I oxyacetylene welded along the perimeter, but you can also just use a mig welder for this. Tack your rod and bend it to the shape of the ear cop as you weld along the perimeter. Its not a bad idea to just leave it long, and trim it once you get close to the end. Then weld the rod at the seam.
To attach the ear cops, you will need a couple scraps of leather and some rivets. Carefully mark the placement of your ear cops, drill two holes, and set your rivets through the helmet and leather straps. Do the same on the ear cops. I just drilled all of these holes freehand with a cordless drill and a sharp drill bit.
Attachments
Step 12: Chainmail
I knew I wanted to add a length of chainmail along the back of my Viking helmet. This might or might not be historically accurate, but it definitely looks badass. To do this we want some plain old 3/16 galvanized wire. Grab a length of steel rod the diameter you want your rings to be. We are going to use this as a mandrel. Use a vice grip to clamp one end of your wire onto the steel rod, but leave some room to chuck up the rod in your drill. Once your wire is clamped onto the rod, chuck your rod in your drill and tighten it down, and then squeeze the trigger. The wire will begin to coil along your mandrel--guide it with your fingers. Once you run out of mandrel, snip the other end of the wire, and slide the coil off the mandrel. I think I ended up needing around 10 coils worth of rings for my chainmail weave, but how many you need will depend on what type of weave, how big your rings are, and how long you want your chainmail weave to be.
Once you have made your coils, you can go down the line and snip your rings. I used heavy duty wire cutters for this, to save myself the hand fatigue, but any standard wire cutters should do you fine.
After you have cut your rings, you can now start weaving your chainmail rings using a couple sets of pliers.
To attach your chainmail, once the weave is finished, I carefully measured out the distance between the ends of each ring along the edge and drilled corresponding holes along the back of the helmet. I did this very carefully, as any mistakes at this point will be a pain to fix. Once the holes are drilled, its a simple matter of using an extra ring to attach each chainmail ring along the weave.
Step 13: Padding +Wrap Up
The inside of your helmet is going to be full of tons of welds and tacks. You can try to grind these away if you'd like, but I found that it was too cumbersome to fit my grinder inside the helmet. I knew I was going to add padding anyway, so I didn't worry about it too much. You can pad the helmet with pretty much anything cushiony--a little bit of upholstery foam would work great. Just hot glue it in there. I opted to do a fancier padding job, but I'm not going to go into the details here--maybe on a future instructable.
Apart from that your helmet is good to go! You know have a piece which will look great on display and provide an authentic flair for any medieval costume you could care to wear for Halloween. I sincerely hope you enjoyed this instructable. If so, please VOTE!!!!
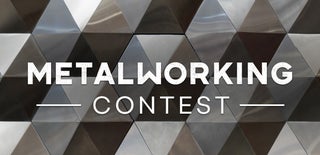
Second Prize in the
Metalworking Contest