Introduction: Stripping a Myford ML10 Lathe (Speed 10) Headstock - Taper Roller Bearings
Two teeth were broken on the 65T backgear (bull wheel) of my ML10. To replace it, I had to strip the headstock right down to the spindle. It is a similar process to change the drive belt, so I did that as well. Once stripped, I found that grease had been used with the spindle-pulley wheel oil nipple, so I cleared that of grease as well. I believe the whole process is the same for the Myford Speed 10 lathe.
This instructable, details the process in photographs. There is not much text, just a few suggestions.
I am a complete novice, so probably did some stupid things, however I hope those in-the-know will add comments where necessary. Step 4 makes a suggestion for producing a simple tool on the lathe in advance of the strip-down.
The ML10 user manual explains how to do the job and refers to the parts diagram - both of these are shown above. The instructions call the locking ring "number 230", my diagram shows it a 225.
The whole job - start to finish took 3 or 4 hours.
This instructable, details the process in photographs. There is not much text, just a few suggestions.
I am a complete novice, so probably did some stupid things, however I hope those in-the-know will add comments where necessary. Step 4 makes a suggestion for producing a simple tool on the lathe in advance of the strip-down.
The ML10 user manual explains how to do the job and refers to the parts diagram - both of these are shown above. The instructions call the locking ring "number 230", my diagram shows it a 225.
The whole job - start to finish took 3 or 4 hours.
Step 1: Strip Off the Peripherals
First task is to get access to the spindle. Remove the covers, chuck and get full access.
Step 2: Get the Spindle Ready to Remove
The spindle is extracted by sliding it towards the tailstock. So the left-hand end of the spindle needs clearing.
Remove the 25 tooth gear by completely unscrewing the grubscrew and unscrewing the gear wheel off the spindle.
Slacken off the grubscrew on the locking collar. You can see from the photographs where someone has used a wrench to tighten the locking ring; I didn't fancy that for undoing, so I left one thread of the grubscrew showing above the ring and used an aluminium 'drift' to tap the ring free. It does not take much effort.
There is a copper pad at the bottom of the hole - I did not investigate that!
Remove the 25 tooth gear by completely unscrewing the grubscrew and unscrewing the gear wheel off the spindle.
Slacken off the grubscrew on the locking collar. You can see from the photographs where someone has used a wrench to tighten the locking ring; I didn't fancy that for undoing, so I left one thread of the grubscrew showing above the ring and used an aluminium 'drift' to tap the ring free. It does not take much effort.
There is a copper pad at the bottom of the hole - I did not investigate that!
Step 3: Free-off the Items Mounted on the Spindle
Two grubscrews need slackening off next.
I knew that the right-hand bearing cover had to come off as the spindle is being 'tapped' out. After a first attempt at removing the spindle, I wondered whether the bearing cover was very tight, so I cleaned out the crud from around it. In reality, my understanding of 'tapping' and the user manual's understanding of 'tapping' are very different. The spindle needs 'driving' out and freeing the bearing cover is probably irrelevant.
I knew that the right-hand bearing cover had to come off as the spindle is being 'tapped' out. After a first attempt at removing the spindle, I wondered whether the bearing cover was very tight, so I cleaned out the crud from around it. In reality, my understanding of 'tapping' and the user manual's understanding of 'tapping' are very different. The spindle needs 'driving' out and freeing the bearing cover is probably irrelevant.
Step 4: 'Tap' Out the Spindle
I started with a rubber mallet and soon realised, that the spindle needs to be driven very firmly out of the bearing housings.
(Think car engine overhaul; think gear puller; think hydraulic press, and you are in the right ball-park). If I were doing this frequently, I would construct a clamp/threaded push rod affair to avoid any possibility of damaging the taper-bearing surfaces.
Perhaps a simpler tool for people who still have access to a working lathe immediately before the strip-down, would be to produce an aluminium bar with a shoulder turned down at one end which just fits inside the spindle. The bar could be used as a drift to hammer the spindle right the way through the bearing, rather than having to find something to use once the spindle had 'disappeared' inside the headstock casting (see photo 13? above).
In reality, I laid about the spindle with a heavy hammer and a wooden drift. You can see from the photographs, what happened to the wood. I had to apply some severe bashing.
I was very careful to check that the various items on the spindle WERE free to move, and that the applied force would be pushing the spindle through the bearings and not gouging a trough through the spindle due to a protruding grubscrew (or similar).
On occasion, I used a ruler to check progress (if it was particularly slow).
The right-hand bearing cover pops off, quite early in the process.
Eventually, the spindle enters inside the left-hand bearing, so you need a smaller diameter (soft) drift.
You can see the point at which the belt can be slipped off the spindle (and a new one inserted). If this was the required task, then there is no need to strip the headstock any further - start to put it back together!
(Think car engine overhaul; think gear puller; think hydraulic press, and you are in the right ball-park). If I were doing this frequently, I would construct a clamp/threaded push rod affair to avoid any possibility of damaging the taper-bearing surfaces.
Perhaps a simpler tool for people who still have access to a working lathe immediately before the strip-down, would be to produce an aluminium bar with a shoulder turned down at one end which just fits inside the spindle. The bar could be used as a drift to hammer the spindle right the way through the bearing, rather than having to find something to use once the spindle had 'disappeared' inside the headstock casting (see photo 13? above).
In reality, I laid about the spindle with a heavy hammer and a wooden drift. You can see from the photographs, what happened to the wood. I had to apply some severe bashing.
I was very careful to check that the various items on the spindle WERE free to move, and that the applied force would be pushing the spindle through the bearings and not gouging a trough through the spindle due to a protruding grubscrew (or similar).
On occasion, I used a ruler to check progress (if it was particularly slow).
The right-hand bearing cover pops off, quite early in the process.
Eventually, the spindle enters inside the left-hand bearing, so you need a smaller diameter (soft) drift.
You can see the point at which the belt can be slipped off the spindle (and a new one inserted). If this was the required task, then there is no need to strip the headstock any further - start to put it back together!
Step 5: Inspect - Clean - Etc
I was not too worried about cleaning off everything. Although the grease looks rather black, it is fairly new and the bearings had been 'flushed' out with copious amounts of grease a few weeks back. So, I was rather more worried about introducing dirt INTO them, than wanting to clean stuff out of them.
Nonetheless, I did get rid of the obvious filth! I also wiped off enough grease to be able to inspect the bearing surfaces, etc.
I removed the grease and oil nipples and checked that they looked OK. Grease had been used in the wrong place, so I spent some time cleaning off the pully wheel bearing surface (see next step).
Nonetheless, I did get rid of the obvious filth! I also wiped off enough grease to be able to inspect the bearing surfaces, etc.
I removed the grease and oil nipples and checked that they looked OK. Grease had been used in the wrong place, so I spent some time cleaning off the pully wheel bearing surface (see next step).
Step 6: Removing Grease From the Drive Pulley Wheel
The nipple on the drive pulley is for OIL not grease. Mine had been thoroughly greased! The pulley wheel does not normally rotate ON the spindle, it is locked to it, and no lubrication is needed. When the backgear is engaged to slow the spindle speed, the pulley does rotate relative to the spindle, so lubrication is then needed.
When I bought my ML10, the 65T backgear and the backgear cluster both had teeth missing (hence the need for the spindle removal). However, the owner said that he had never used the backgear at all, so this incorrect lubrication has presumably had no ill effect.
The photos of the pulley wheel show the path the oil takes.
When I bought my ML10, the 65T backgear and the backgear cluster both had teeth missing (hence the need for the spindle removal). However, the owner said that he had never used the backgear at all, so this incorrect lubrication has presumably had no ill effect.
The photos of the pulley wheel show the path the oil takes.
Step 7: Ready to Reassemble
All is relatively clean. Laid out and ready to reassemble.
Don't forget the new belt (I bet someone has reassembled and forgotten it!!).
Don't forget the new belt (I bet someone has reassembled and forgotten it!!).
Step 8: Put It Back Together
Reassembly is pretty straightforward.
A few things I was careful about:
The rubber mallet was sufficient force during the reassembly phase.
As the spindle is inserted, the left-hand bearing cover pops out, and the bearing pushes its way out of the taper housing. I don't know whether it would be possible/desirable to keep it in place and drive the spindle through?
In the final analysis, a tube is needed to drive the left-hand bearing back onto the spindle (I used a white plastic tube - see photo). Perhaps a copper tube would have been better. The hardest part is holding the spindle, so that you have something to hammer against - it is fairly free to travel towards the tailstock and needs to be clamped somehow. In the end, I wedged a length of wood between the threaded spindle nose (where the chuck fits) and the base of the tailstock (locked to the bed). I slowly, and carefully tapped the left-hand taper bearing onto the spindle with the rubber mallet and tube. I would have preferred to use some G-clamps and wood, to hold the nose against the casting - but my G-clamps had walked!
Once I had got it on a fair way, I put on the spacer and locking ring (thoroughly oiled) and used a wrench (horror) to slowly move the left-hand bearing onto the spindle. The manual suggests removing the grubscrew and replacing it with a threaded tommy bar, but I did not have anything like that. I stopped the spindle from rotating, by putting the chuck on, and gripping a piece of wood to stop it rotating.
Once the bearings were virtually fully seated (just a little play left), I just had to adjust the end-play and do a final assembly.
A few things I was careful about:
- There is a woodruff key for the 65T backgear, it needs to be carefully introduced into the keyway.
- The grubscrews on the locking ring and backgear locate onto flats. The keyway on the backgear forces its grubscrew to align with the flat on the spindle, and the locking ring grubscrew should align with the backgear grubscrew (ie the two flat areas on the spindle are aligned).
- The locking ring has a 'raised' or 'relieved' shoulder on one side (first of the two ring photos), this should be in contact with the pulley wheel.
The rubber mallet was sufficient force during the reassembly phase.
As the spindle is inserted, the left-hand bearing cover pops out, and the bearing pushes its way out of the taper housing. I don't know whether it would be possible/desirable to keep it in place and drive the spindle through?
In the final analysis, a tube is needed to drive the left-hand bearing back onto the spindle (I used a white plastic tube - see photo). Perhaps a copper tube would have been better. The hardest part is holding the spindle, so that you have something to hammer against - it is fairly free to travel towards the tailstock and needs to be clamped somehow. In the end, I wedged a length of wood between the threaded spindle nose (where the chuck fits) and the base of the tailstock (locked to the bed). I slowly, and carefully tapped the left-hand taper bearing onto the spindle with the rubber mallet and tube. I would have preferred to use some G-clamps and wood, to hold the nose against the casting - but my G-clamps had walked!
Once I had got it on a fair way, I put on the spacer and locking ring (thoroughly oiled) and used a wrench (horror) to slowly move the left-hand bearing onto the spindle. The manual suggests removing the grubscrew and replacing it with a threaded tommy bar, but I did not have anything like that. I stopped the spindle from rotating, by putting the chuck on, and gripping a piece of wood to stop it rotating.
Once the bearings were virtually fully seated (just a little play left), I just had to adjust the end-play and do a final assembly.
Step 9: Adjusting the Bearing End-play
The process was much as the manual suggests. The photos show what I did.
Before running the machine, I had to refill the bearings with grease. This takes a good number of pumps with the grease-gun. I knew when to stop because the grease starts coming out of the bearing.
I also engaged the teeth on the bull wheel - making sure they meshed fully. In addition, I had to adjust the tension on the new drive belt by adjusting the turnbuckle screw holding the motor.
In fact, I went through the locking-ring-tightening process (followed by running the lathe) a few times before the end-play became zero. I did not replace the chuck/wood to stop the spindle from rotating, but wedged a piece of aluminium between the bull wheel and headstock casting - the forces involved in tightening the locking-ring are not very great.
Finally, I tightened up the grubscrew on the locking-ring.
Before running the machine, I had to refill the bearings with grease. This takes a good number of pumps with the grease-gun. I knew when to stop because the grease starts coming out of the bearing.
I also engaged the teeth on the bull wheel - making sure they meshed fully. In addition, I had to adjust the tension on the new drive belt by adjusting the turnbuckle screw holding the motor.
In fact, I went through the locking-ring-tightening process (followed by running the lathe) a few times before the end-play became zero. I did not replace the chuck/wood to stop the spindle from rotating, but wedged a piece of aluminium between the bull wheel and headstock casting - the forces involved in tightening the locking-ring are not very great.
Finally, I tightened up the grubscrew on the locking-ring.
Step 10: Adjusting the Backgear Alignment
I inserted the backgear cluster on its shaft and tightened it up.
I don't think I was able to align the backgear in the way mentioned in the manual (see intro step ). If I made the left-hand side of the backgear flush with the left-hand side of the 21 tooth part of the backgear cluster, then the 56 tooth part of the cluster was not near the centre of the 30 tooth bronze gear. I just went for a compromise, with reasonable clearances on both sides of the cluster. I tightened up the backgear grubscrew when I was happy.
Finally, the pulley positioning collar needs to have a 0.005" clearance so I used a feeler gauge and tightened up its grubscrew.
I don't think I was able to align the backgear in the way mentioned in the manual (see intro step ). If I made the left-hand side of the backgear flush with the left-hand side of the 21 tooth part of the backgear cluster, then the 56 tooth part of the cluster was not near the centre of the 30 tooth bronze gear. I just went for a compromise, with reasonable clearances on both sides of the cluster. I tightened up the backgear grubscrew when I was happy.
Finally, the pulley positioning collar needs to have a 0.005" clearance so I used a feeler gauge and tightened up its grubscrew.
Step 11: Final Assembly and Lubrication
The bearing covers needed replacing (tapping them on with a piece of wood and rubber hammer), followed by more grease - waiting to see grease oozing out of the covers.
Then the 25 tooth gear was reattached.
Followed by the machine covers.
I was keen to test the operation of the backgear but remembered to lubricate the oil nipple using an oil gun (NOT grease) before I got too carried away.
Really looking forward to cutting some threads!
Then the 25 tooth gear was reattached.
Followed by the machine covers.
I was keen to test the operation of the backgear but remembered to lubricate the oil nipple using an oil gun (NOT grease) before I got too carried away.
Really looking forward to cutting some threads!
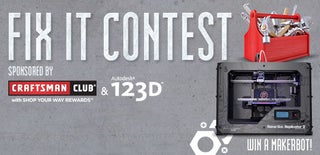
Participated in the
Fix It Contest