Introduction: Table Saw Blade Gauge (& Router Too!)
How many of you have gone to notch out something, or perhaps planned on cutting a dado or rabbet out on your table saw and stared down at that cold blade knowing the chore that lay before you? First you'll have to guess about where that blade belongs, then you'll have to find the exact center of where that blade comes up. If that's not bad enough, you'll have to measure in a nice 90° angle from the tabletop to the very tip of the blade, at the exact center of the table where the crest of the blade hits its zenith.
How about making a gauge that'll tell you exactly when you need to stop cranking to get that blade exactly where it needs to be? It's quick and small enough that you can attach it with magnets to the side of your table saw; and besides all that, it's safer than holding a ruler to the blade, especially when your prankster buddy sits nearby with that look in his eyes...
Step 1: Materials List / Equipment Used
Materials
- (2) 1 1/2" x 8 1/2" x 1/4" section of wood (I used walnut)
- (2) 1 1/2" x 3" x 1/4" section of wood (I used walnut)
- (2) 3 1/4" x 8 1/2" x 1/4" section of wood (I used hard maple)
- 7/8" x 13/16" x 3" rectangular piece of wood (I used padauk)
- (8) 1/4" x 1-7/8" compression springs (Wire Diameter: .019 WG)
- (4) 2" aluminum Screw Posts
- (4) 1" aluminum Screw Post Extension
- epoxy
- thread locker
- wood glue
- (3) #8 1/2" wood screw
General Tool® 6" Stiff Ruler (should be a 1/16")
Equipment
- table saw (ha!)
- miter saw
- drill press
- step drill bit (has to contain 7/16" and 5/16" step)
- steel center punch
- (2) 15/64th drill bits
- 1/16th drill bit
- 1/8th drill bit
- 7/8 Forestner bit
- 1/2" drill bit
- file
- bar clamps
- right angle clamps
- ruler or a straight edge
- coping saw (optional)
- countersink bit
Step 2: Perfect Base, Perfect Ceiling
We're going to start this project by making sure that both the top and bottom of this contraption have holes that line up perfectly. If they don't line up, the entire project is a waste, the ocean's will rise, the earth will be doomed. At least, that's how you'll feel when you're finished and it doesn't function properly. And you don't want that. So let's make this work juuuust right.
With our tablesaw, let's cut 2 rectangles out with these dimensions:
8 1/2" x 1 1/2" x 1/4"
Make sure that the edges are nice and straight and that it is completely parallel. This is a critical step. Oceans rising, earth doomed...remember that feeling of complete ruin if we mess this up?
We'll now use our homemade marking gauge to measure out 4 marks that both rectangles will be inked with.
Wait, you mean you don't have a homemade marking gauge? Well if you don't have a homemade marking gauge, I guess you can use a ruler or possible a carpenter's square this time. But do give it a look (it worked well at marking this project)!
All joking aside, you're going to want to make 4 marks on both pieces of wood. I've put the dimensions neatly in a picture. This is my first sketchup attempt, so forgive me if it doesn't look professional. (We'll just blame that on Google...)
We'll drill these holes out with a 15/64th drill bit and make the wood pieces you have match the picture. Be sure that you take your time, measure each center for each hole and drill the pieces separately...no cheating by double stacking.
Step 3: Gluing the Top to the Back
We'll take one of the 3 1/4" x 8 1/2" x 1/4" pieces and we'll glue it to the one of the prepared boards you made in the last step. Before adding the clamps and the glue, we'll use our Super Easy Wood Spline Jig. Because butting up board against board can be weak, the Super Easy Wood Spline Jig will give it more strength and a much more attractive look. Wait, you don't HAVE the Super Easy Wood Spline Jig to make the splines?! Well, let's put that on the to do list. Splines give strength, not functionality, so you'll be safe, this time.
Using right angle clamps, we'll glue the top to the back. If you used splines, now is the time to pop them puppies in.
Note: look at the sketchup drawing and make sure you glue it up correctly.
Step 4: Cutting the Shelf to Size
I'm calling the platform that performs the measurement...the 'shelf'. This would be the second plank of wood you prepared back in step 2 (the duplicated piece you glued in the last step). In the video, I used the caveman way to mark the wood by laying the 'shelf' 1 1/2" end down and drawing a line across it using a scrap of wood that the walls were used from. Since the 'shelf' will slide between both newly created walls, we need to cut off a 1/4" on both sides. NOT a 1/2" off one side, that would be silly.
Some 'shelf' clarification
Once both sides of the 'shelf' have been cut, run a 15/16" drill bit through both the ceiling piece and the 'shelf'. Do that on both sides as can be seen in the video. This will give us a good index to help glue the sides on and keep the 'shelf' perfectly straight. And here I bet you thought I told you to grab to 15/16" drill bits in case one of them broke.
Step 5: Building Half of a Box
I've included another diagram in sketchup to give you the best understanding of what a half box is, dimensions without all the yada yada. The sides (both 1 1/2" x 3" x 1/4") are, once again, glued on, edge to sides. The drill bits will help keep things straight, so gluing should be easy. You'll use a few bar clamps to make sure it's snug, just be careful that everything is straight and check back often to see if anything moves. It's not exactly the strongest way to glue a box. Of course you could use the Super Easy Wood Spl...(okay, I'll stop). You could use finger joints, you could make your own rabbets, but when the sun sets at the end of the day, what's really important is that you have a half box.
Step 6: The Tenon...
Okay, so we've built a box, we have a platform in it that I've dubbed a 'shelf'. Look at the 4 holes (well 8, if you look at the top and the 'shelf'). Those 4 holes are not going to give us an accurate reading unless we can perfectly center the item we're measuring, which defeats the idea of not having to find the center of the blade. But even if you could find the center every time, there are other mechanical limitations that the springs and even the screw posts have. So what we'll need to do next is create something that will only allow the 'shelf' to extend upwards in a straight path. Enter the glorious over sized Tenon and his beautiful wife, The Mortise. (Please, no connotations here, this is a 'G' platform after all).
I used a piece of padauk and cut it down on the table saw. This isn't a perfect square, as you'll notice by the dimensions: 7/8" x 13/16" x 3"
One wall will have a 1/16" ruler attached to it.
We'll cut the block a 7/8" wide one side and a 13/16" on its perpendicular side.
Step 7: ...And His Beautiful Wife Mortise.
We'll take our ruler and throw some lines across the top of the half box, in a diagonal fashion. Be sure that you only mark on the piece that you glued on, and not the perpendicular piece attached. I've made a sketchup picture showing exactly what I mean. In the middle, where both lines intersect, take something sharp and puncture it. That's where we'll be drilling next with the drill press.
This is where the 1/16" drill bit comes in. We're going to drill a hole right where that 'X' comes together, but it's only going to be a reference point. After the hole has been drilled, we'll flip the half box over and lay it face down on a scrap of wood. We'll grab our 7/8" Forestner bit and we'll place the point in the freshly drilled 1/16" hole. Just a tip, slowing down your drill press is much safer on your project when using large Forestner bits.
After we have a beautifully carved out hole, we'll use our file to square it into a nice mortise. You may have noticed in the video that I used a coping saw, but it is not necessary and could lead to a mistake that might ruin your project, so use it at your own risk. Constantly take the tenon you cut out in the last step and check it to the opening until you're sure you have a perfect fit. A perfect fit is C R I T I C A L!
Note: Remember, again, that you will be working with a tenon that is a rectangle. After we add a ruler to it, it'll be a nice even square. Until then, you'll need to rotate the piece to check that each side fits into the square hole you've created.
Step 8: Tenon and Measuring Stick
Remember how our tenon was more of a rectangle than a square? Now it's time to make it square. We'll first start off by placing the tenon through the mortise and placing the 'shelf' on the underside of the half box (you have to love all my fancy made up words). We'll do this so that we can run a pencil across the tenon, above the box. We'll cut off the excess and sand until the top of the tenon sits flush with the half box. Perfectly flush.
Next we'll pull out the tenon and place our ruler (General Tool® 6" Stiff Ruler is what I used ) up next to it. We'll position the zero of the ruler to be on the end of the tenon and head to the other end of the tenon where we'll mark a line on the ruler. We'll use an angle grinder to cut off the metal excess and check to make sure that the ruler is not longer than the tenon. If it is, we'll grind the side opposite of the zero until it is slightly shorter than the tenon.
Phew! Let common sense be your friend on the ruler. Obviously we don't want to cut off the beginning part of the ruler as the excess. Also obvious that we don't want any part of the ruler to stick out of the top of your contraption or we'd have a bad reading when it's time to set it on a blade.
Now that that's done, I used a steel center punch and put a couple dents about a 1/2" from the top and bottom of the ruler. I used those to guide my step drill bit and cut up to the 5/16" step, not going all the way through but leaving a slightly larger pilot hole where the tip of the #8 screw will sit slightly below the metal ruler. We don't want that screw to rub as it passes through the mortise.
Finally, in this step, we'll attach the ruler we cut against the 13/16" side. We'll move the zero of the ruler flush with the end of the tenon, find the center of the holes we just drilled in the metal, and mark the center with an awl. We'll use an 1/8" drill bit to drill a pilot hole and drive the screws in, very carefully, maybe even with a screw driver (of all things!). Be sure the zero edge of the ruler is flush with the end of the tenon before cinching the metal tight against the tenon.
Check to make sure it fits and slides easily and that it's tight in the mortise, and head onto the next step.
Step 9: Dry Assembling the 'Shelf' to the Tenon
That's right, before we make the connection between the 'shelf' and the tenon permanent with wood glue, we'll put a pilot hole through the 'shelf' and the tenon. This will be used later as clamping pressure once we have put the glue on and need it to sit tightly against each other. Use your step drill bit to once again carve out a larger pilot hole allowing the cone of the screw to be flush with the board.
Step 10: Aluminum Screw Post Assembly
Get out that thread lock and those screw posts...and let's have a party! An assembly party. Not so much fun now, huh?
We'll take the 2" aluminum screw posts and attach the 1" extensions on. There will be 4 screw post assemblies altogether. We'll do all of these and set them aside. Not really a party when everyone rests after the first screwdriver (now that was a good bit of alcohol humor, and I don't even drink!).
After a few hours, we'll use a file and scuff the heads of these new, extended aluminum posts. We'll do this to give the epoxy something to grip tightly to.
The next step...it get's a bit hairy. If you're squeamish...or just serious about making this, continue onward...
Step 11: Depthing Out Previous Holes for the Aluminum Posts
This could get tricky. I used harry in the last step, but maybe tricky is a better word. Problematic? Thorny? Let's stick with harry.
In this step, you'll have to figure out the depth that the aluminum posts will need to have for the included screw to be tight without the 'shelf' being drawn up. That is, you'll have to make sure that the shelf stays flush with the bottom of the half box. This means you'll have to drill a little, check it by inserting the aluminum posts through the bottom and tightening the screws on top. Oh, and the bottom has to remain flush (deeper than flush is probably better), or, again, it'll be inaccurate.
On the 'shelf' I used a countersink bit that was larger than the head of the aluminum post. I sank the bit pretty low (about an 1/8") as that was what was needed for mine. On the top, where the screws will tighten, I used a 1/2" drill bit, being extremely careful not to drill to far down, as well as keeping it straight and free from tear out. This doesn't need to be complicated, but if you play strictly to instruction and not much to a little outside of the box logic, it might be frustrating.
After you find the sweet spot where the screws are screwed in all the way and both the top and the bottom are recessed, put all four posts in and tighten the included screws (that came with the aluminum posts) in the top. Make sure the shelf is flush and the bottom heads are recessed nicely. Now flip the box over so that the bottom is up and head on over to the next step.
TIP: Its okay to sand both broad edges (8" length) of the 'shelf' just a hair. It will have to be able to slide easily. The narrower edges (1 and 1/2" length) need to make contact with the sides of the half box.
Step 12: Gluing, Epoxying, Attaching, Screwing
Now it's time to attach the tenon to the 'shelf' (made up terms are bad enough, but all those quotation marks...). With the half box still positioned upside down, we'll simply add a bit of glue to the side opposite of the zero on the tenon, slide it through the mortise (lower ruler side up), slide the shelf in and add the screw back.
Once the screw is tight and secured, we'll flip it upright. All 4 posts will be in at this stage and we'll slide 2 springs over each post. If you can find a 4" spring with the spring dimensions I gave (maybe even a 3" spring), use them. In my part of the world I had a very difficult time finding anything other than the 1 7/8" spring lengths (again, be very sure you use the exact wire gauge thickness and side that I included in materials).
This part can be a little tricky as well, but I found it easier just to leave the 'shelf' sitting upright with all the springs up in the air, and then carefully sliding the half box on top of it. Ease the springs down until the aluminum posts protrude from the holes, and screw in your screws. Once all 4 are secure, we'll flip the half box upside down and add epoxy to the heads of the aluminum posts. We don't want to put too much in, or allow the epoxy to be anywhere in the hole. This, again, is the bottom side of the 'shelf'. It is also important to note, again, that the screws are on the top of this gauge so that it can be taken apart if there's any problems.
Check times for glue and epoxy cures before heading over to the next step.
Step 13: Finishing Our Box
Well it's time to stop calling it a half box. We are well on our way to finishing this box by adding the final wall. You'll notice in the video that I cut away a part of it, but I did that mostly to show how the mechanics work. It is absolutely useless to add a window (oh the things I do for my fans) as all measurements will protrude through the top.
We'll glue the final side on and make sure that the bottom is flush with the bottom of the half box. It is critically important that you make sure that the 'shelf' doesn't get any glue on it...or it obviously won't slide. Use clamps and allow all of that to dry. Congratulations, you have a Table Saw Blade Height Gauge. The nice thing about this is that you can place the tip of the saw blade anywhere in side and get a good reading, thanks to the mortise and tenon and the sides of the 'shelf' fitting very neatly inside the box, as well as the springs that put constant downward pressure.
Step 14: Thank You!
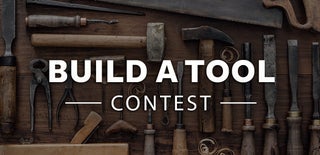
Runner Up in the
Build a Tool Contest