Introduction: Thane Krios - Mass Effect - Costume Build
Thane Krios was a DREAM cosplay for me. I loved his character in the original Mass Effect series and his outfit was pretty cool too. Since most of what I did to create this costume was fairly new to me I researched before committing to this endeavor. I visited prop makers, Reynold's Materials (for casting/molding advice) and reviewed any morsel of information I could find online about Mass Effect cosplays. Research is IMPERATIVE to the creation of this cosplay. I will include the materials I used in this tutorial along with some site suggestions for those who are unfamiliar with the techniques utilized in this build.
For reference art I searched "Thane Krios Concept Art" AND "Thane Krios Turn Around" on google. There are plenty of reference images for this character so that was definitely a bonus. If you are looking for a mask...good luck. There are few Thane Krios cosplayers and a majority made their masks from foam, silicone or they simply painted a bald cap and added some cheek frills for detail to the sides.
Be forewarned, this costume cost me around $300 in materials and that was me going as frugal as I could (shopping from whole sellers, pushing my supplies to the edge, etc.). $300 is likely a minimum for this costume and it will exceed that once I start crafting his sniper rifle later this year. If you are comfortable moving forward then let's begin!
Step 1: Sculpting
Sculpting Materials
- Monster Clay (wax based clay) in Medium Hardness
- Mannequin Head (that matches your measurements) OR a Head Cast
- Sculpting Tools (loop tools are especially important)
- A Heat Gun (for softening the Monster Clay)
- A drop cloth or table you don't mind damaging
To start I heated my Monster Clay up in a microwave safe bowl and set my microwave to 2 1/2 minutes on high (watch the clay as it may require more or less time). Monster clay CAN become molten so be careful when handling after it is heated. I took the softened clay and apply large swaths of it to the mannequin head. This mannequin's face is almost identical to my own except along the jaw line; as I was not sculpting that low it did not bother me however, if you DO sculpt lower make sure your mannequin/head cast is identical to you.
Don't focus on the details in the beginning, just try to get the basic forms in place. You can always smooth out weird or uneven areas with a loop tool later. Once you have your forms start to scrape away excess material with a large loop tool. Take pictures as you go and flip them/mirror them to get an idea of where proportions may be skewed on offset. Once you have a nice, smooth sculpt you can add details.
Adding details on Monster clay is far more effective when the clay is NOT warm. I would advise taking a piece of spare clay and testing your detail/texture work on that with different tools to determine what works best. With your details added hit the sculpt, at about 6 inches away, with some heat from your Heat Gun to smooth out any deformities.
Allow your sculpt to cool/settle for about 3 hours before you proceed with molding. You can expedite this time frame by placing your sculpt in the refrigerator (NOT the freezer). This sculpture took me around 12 hours to complete (after a few revisions).
Sculpting References
Step 2: Molding
Mold Making Materials
- Smooth Cast 305 (fast curing resin)
- Gloves (latex free preferred)
- Mask/Respirator
- Safety Goggles/Glasses
- A table you don't mind damaging OR a drop cloth
- Mold Release (I prefer the aerosol kind)
- Sculpey OR Water Based Clay (for building your mold wall)
- Paint Brushes you don't mind throwing away OR Tongue Depression Sticks
- Mixing Containers with fluid measurement indicators
- Mixing sticks
- Ure-Fil 11 (this helps thicken the resin)
I started by building a separation from right/left sides of the sculpt using Sculpey. This division will help you when you need to split the mother mold. Once that division was built up I filled in the eyes with clay (this is to help the mold release) then built walls underneath where the sculpt ended. Next I sprayed the left side of my sculpt with Mold Release 200 and waited for it to settle (follow the directions for applying mold release). After the release was set I gloved up and mix my 1:1 Parts A/B Smooth Cast 305 together. When they were evenly mixed I slowly began to add Ure Fil 11 until the consistency was that of toothpaste. I then applied the paste to the left side of the mold making sure not to get any excess on the opposing side.
I repeated this process on the left side 3 more times before I was comfortable with the mother shell I had built. I allowed the resin to fully cure (usually cures in 20 minutes or less) then I rotated the mannequin head and sprayed mold release on the right side. I repeated my mixing steps and applied the resin paste to the right side of the sculpt. This took about 4 layers as well. Once both sides were fully covered in resin I allowed them to cure for about 30 minutes then I took a flat head tool and a hammer and carefully began to split the mold down its middle. If you are uncomfortable starting with a flat head you can use a chisel OR a hot knife to create a line for following down the middle. You WILL hear cracking and may have some minor breakage from the top.THIS IS NORMAL. Just take your time, keep tapping away (slowly) and you will finally split the mold in half.
After splitting the mother shell/mold I carefully pulled it off one side, inspected it, then I removed the other side. Your clay/sculpt may experience some damage so if you want to keep understand that fixing is required. I did not need mine so I removed the clay from the mannequin and moved on to casting the mask/facial appliance.
Molding References
Step 3: Casting
Casting Materials
- EcoFlex 50 (or some form of Platinum Cure Silicone)
- Silc Pig (for pigment)
- Gloves (latex free)
- Mask/Respirator
- Safety Glasses/Goggles
- Clamps (to hold your mother mold together)
- Mixing Bowls with liquid measurement indicators OR a scale
- Mixing Sticks
- Mold Release 200 (or some form of aerosol mold release)
- Clothing you don't mind getting dirty
- Sticks to help put pigment into silicone
Spray your mold released into your clamped Mother Shell and wait for it to settle. Next, take your mixing containers and pour your Part A amount in first. Open your Silc Pig container of preference (I used green and yellow) and mix a drop of each into Part A. With the pigment thoroughly mixed you can add Part B to Part A and evenly mix the two. I added a bit of Ure Fil 11 to thicken this but it is not a requirement, it only helps your silicone go further. Once you have everything mixed pour the entire content of the bowl into the mother mold (be sure you have clamped the two halves together securely) then start "slushing" the silicone in the mold by slowly rotating it. You will want to stick to one side per pour so you do not have large drops pouring off the opposite end as you roll the mold.
I completed this four times. I started with the bottom of the mold and rolled all of my product into the back, top and top-front of the head. Then I poured another batch into the right side and slushed the material around until it fully covered all of the right side. My third step was pouring the product into the left side and repeating my slush technique. Once I was certain that the sides and top were covered I poured my remaining product into the back of the mold and slushed it around until it was fully covered.
Eco Flex 50 has around a 20 minute working time so you do not have to rush but you will need to be diligent. I used an entire box of this product and about 1/8 of a box of Ure Fil 11. If you do not use a filler with your mask you WILL need two boxes of Eco Flex 50. Also, I should note that the Silc Pig pigments go a LONG way. A tiny amount will color an entire mask. I used less than 1/4 of my container for yellow, green and black during this casting process.
When you have filled the mold to the point where you are comfortable (all areas covered) then rest it somewhere safe and allow it to cure for 3 hours (I let mine cure over night). To remove the silicone from the mold first, remove the clamps from the Mother Shell. Next, gently pull one side of the shell away from the other. Some people find that their silicone rolls right out where others (such as this mask where undercuts were larger) may have to gently tug and wiggle to get the mask out. Once your mask is removed you can use soap and water to wash away any residue from the appliance. Place it on your mannequin/head cast and allow it to settle for 3-5 hours before painting (silicone needs to breathe a bit after it is removed from its mold).
Casting References
Step 4: Jacket
Jacket Materials
- 4 Way Stretch Pleather (Black)
- 4 Way Stretch Spandex (YaYa Han Hex Heroes)
- White Piping (stretch preferred but non-stretch is ok if you are experienced)
- Black and White Thread
- Sewing Needles
- Sewing Machine
- Painter's Tape (for patterning details)
- Velcro OR Snaps
- Tailor's Chalk OR Fabric Markers
- Patterns OR Ability to Create Patterns off of Measurements
- Measuring Tape
For starters I took an old work blazer, with 3/4 sleeves and that fit only when open, to use as my mockup for the jacket. I studied the intricacies of the blazer to better understand its structure then proceeded with drawing a pattern on the back side of the 4 way stretch black pleather. If you are not experienced in pattern drafting or it is not something that makes you comfortable you could use THIS pattern and lengthen the bottom for this costume.
With my pattern drafted I pinned everything together and sewed along the seams (just a loose stitch for starters) then tried on the jacket. After a few adjustments I finished up the seams and had my base structure in place (no interfacing and no sleeves at this point). Next I measured along the edge of the entire jacket (from neck to bottom and around to the back) so I would know how much interfacing I needed. I cut 2" thick rectangles at the proper length and placed them face to face (pleather side to pleather side) along the edges of the jacket and sewed everything together. Then I flipped the fabric over (so I had a hidden hem) and sewed the inside of the interfacing to the jacket (take care when sewing on top of pleather, you may need to change your foot OR add packaging tape to the bottom so the fabric glides smoothly). For those unfamiliar with interfacing on jackets please review THIS tutorial.
Now that I had smooth seams/edges I placed the jacket on my dress form (you can do this on yourself with help from a friend) and began to use Painter's tape to apply my overlay designs. I used a brightly colored frog tape so it was easy for me to see the definition between the two surfaces. When the pattern was drafted I carefully peeled the paint off and then stuck it to the 4 way stretch YaYa Han Hex Spandex. You will need to cut two for the front (make sure to flip your pattern) and one for the back. With those patterns cut out I took my no-stretch white piping and applied it to the edges of the overlays. Next, I folded the piping edge (flat edge) under the fabric and pinned it to the areas of the jacket where it belonged.
I did another test fit (on myself) to validate that the jacket was laying as I wanted; then I proceeded with carefully stitching along the edge of the piping so the patterns were secured onto the jacket's base. You may want to use a zipper foot for this so you can get as close to the edge without revealing too much of your stitching. With the patterns applied to the jacket (in areas without piping use a black thread and a tight zigzag stitch to secure the overlay onto the jacket) it was time for the sleeves.
I have made MANY sleeves so I drew my pattern out, tested the length, then drew another pattern on the back side of the fabric to help me determine what size overlay I needed on the sleeves. I repeated the pattern onto the hex fabric and cut it out (cut one, flip the pattern, then cut a second - this is so the sleeves mirror properly). I ran out of piping during this process (I used A LOT on the leggings/shirt) so I switched to bias tape. With the bias secured to the overlay I pinned the overlay to the pleather side of each sleeve (make sure to test the fit by pinning and sliding the sleeve on) then I sewed the overlay to the sleeve (do NOT sew your sleeve seams together before sewing the overlay on or you WILL have issues with applying the overlay). Finally, I sewed the sides of the sleeves and attached them to the jacket.
My last step was securing the chest/waist bands to the jacket. Unfortunately I forgot to sew the one side of each band to the jacket BEFORE applying the overlay so I had use hot glue to secure them. I would suggest sewing them on before you place the front overlays, this way you can hide your buckle/strap stitching behind the front overlays. After one side was permanently secured I use high temperature hot glue to secure velcro on the opposing, underside of the jacket. Next, I sewed velcro on one end (the loose end) of each of the three vinyl straps. Now I had a means of easily removing my straps without pulling the jacket over my head.
It was here that I meant to add gloves however; I decided against it as the mesh suit I was wearing underneath would have experienced pulling. I may add gloves to the sleeves in the future (you are most welcome to) but this completed my build of the jacket.
Sewing Basics
Step 5: Shirt and Leggings
Sewing Materials
- 4 Way Stretch Pleather (Black)
- 4 Way Stretch Spandex (YaYa Han Hex Heroes)
- White Piping (stretch preferred but non-stretch is ok if you are experienced)
- 4 Way Stretch Spandex/Lycra (Brown)
- Black and White Thread
- Sewing Needles
- Sewing Machine
- Painter's Tape (for patterning details)
- Velcro OR Snaps
- Tailor's Chalk OR Fabric Markers
- Patterns OR Ability to Create Patterns off of Measurements
- Measuring Tape
- Small, White Plastic rings (for details)
- White Embroidery Thread
For starters you must be familiar with either creating OR using a pattern for sewing by this point. If you are not, you can get started with a basic brown spaghetti strap shirt and add pleather to that but sewing from scratch helps with proportions for this part of the costume. An easy way to create a pattern for a form fitting top is using THIS method of pattern mockup. I measured my bust, underbust, waist, hips, torso length and shoulder width to get started with the shirt. Once I had to brown shirt sewn together I used fabric markers to drawn the lower pleather pattern mockup (you can use the painter's tape drafting method referenced in the jacket instructions instead). After my mockup was tested I cut out the pleather, added white piping to it then sewed it to my brown shirt. Next I added velcro on the under side of the shirt bottom so I had a means of securing it to my leggings (since it was spandex on spandex I knew there was a chance that the fabric would try to roll or shift when worn).
With the shirt completed I began on the leggings. I had a pair of leggings at home that I enjoyed the comfort of so I used those as reference. I placed the spandex face to face then cut out opposing sides and sewed the edged together. I added a 2" waist band with elastic inside and tried the base leggings on. Once I was certain of the fit I placed them on my mannequin (you can do this on yourself if you do not have one) and drew with a fabric marker where I wanted the pleather inserts to lay. I cut out the sections, traced them onto the pleather fabric, cut those out then sewed the sides of each pleather insert together (right to right and left to left - I inserted the piping on the sides at this point as well). Next I attached the left insert to the left leg and the right insert to the right leg.
After a few alterations I was ready for attaching the bottom of the legs to the new pleather top. With all legging pieces re-attached/attached I tested the fit then drew (using a fabric marker) where I wanted to add the circle details. I used small, 2" plastic white rings and some embroidery thread to attach the circles to the leggings (three on each leg - one on each side and one at the knee). Finally, I added the marks for where the shirt met the leggings, added my velcro partner sides and secured the two together during a test fit.
You can accelerate this process by purchasing leggings and splicing them together. You could also use fabric puff paint instead of embroidered on rings should you so choose.
Step 6: Painting
Painting Materials
- Airbrush OR Makeup Sponge OR Soft Bristle Paint Brush
- Alcohol Based Paints (Endura, Wolf, Body Ink, etc.)
- Silc Pig
- Fast Cure Silicone (paste or ecoflex 5 minute cure)
- Gloves
- Respirator
- Safety Glasses
- Ventilated room
- Makeup Sealant (alcohol suspended)
I chose to airbrush my mask with Body Ink airbrush makeup after using Silc Pig to add a basic, green pigment. There are SCORES of airbrush tutorials out there and I would suggest referencing them but, for starters, Amber Brite has a guide on where to begin. There is also THIS guide that helps teach how you can paint a silicone appliance for permanent color (the alcohol paint will flake off silicone over time).
I used ProAiir hybrid sealant (alcohol and silicone) to seal the makeup on my mask. I had minor flaking around the eyes (where there was loads of movement) however; the rest of my paint lasted an entire day at the convention I attended with this and is STILL on the mask.
Airbrush Tutorials
Step 7: Final Result & Lessons Learned
Lessons Learned
- While wearing the mask/facial appliance I learned that I could NOT turn my head (think 90's batman).
- Solution: I am separating the neck from the head at the tip of the last V mark on my mask. The neck will be glued down first using Skin Tite (a GREAT glue and blender for silicone appliances); then I will attach the top part of the mask, keeping the back part of it unglued so I can turn my head.
- There is little ventilation and sweat pools in the mask which fogged up the sunglass lenses I used for the eyes.
- Solution: I am purchasing high gloss athletic mesh that I will use for the eyes. This will increase air flow and keep my field of vision open.
- Spandex World 4 way stretch pleather is AMAZING. ALWAYS use this pleather (well...at least I will).
- Keep some spare paint on you (for eyes/cheeks) because movement may cause cracking or fading during your event.
- Have someone help you (a handler or friend is great when wearing a complicated costume like this).
Overall I had a GREAT time in this costume. I plan on adding the final touches (gloves and some minor shin details) but this is DEFINITELY a costume I plan on wearing again.
If you have questions about the build, products or techniques please feel free to ask them and good luck on your own builds!
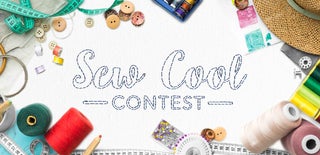
Participated in the
Sew Cool Contest
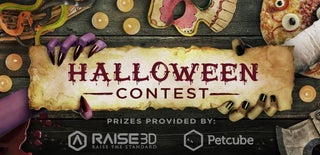
Participated in the
Halloween Contest 2017