Introduction: The X End Table
A few months ago I stumbled across the Instructable by ewyka for a “Wood Quilt Square Wall Decoration” and instantly saw the potential to turn a piece of quilted wood into a crafty looking table top. I really loved ewkya's design and decided to to base my design off of theirs with a few small modifications to make it a more reasonable size for an end table. I put a few hours into a CAD design to figure out dimensions and amount of material needed, made a trip to Lowe’s, and went after it.
Step 1: Design
CAD designs help me realize the size of the piece I’m making and quantify the materials that will be needed. I try to create a 2D CAD drawing or at least a quick sketch on most things that I build before starting the build.
This design took a few tries. At first I was thinking of using exotic woods and 2" wide strips for each piece, but finding exotic woods is difficult and finding them in a 2" actual width is even harder. I thought about buying larger stock and ripping them down to the desired width but that would involve a table saw or a band saw and some re-sawing/ripping to desired width, neither of which are tools that I own or have access to. I decided to change the design to use only wood in stock at most hardware stores without the need to rip them all to size. I settled on using 1x2 as the main design wood as most big box hardware stores carry this and have a few different species of wood available which would help give the desired effect.
Note: the dimensions called our in the drawing of the X-design are exact sizes based on how it was drawn in CAD. When I cut these parts I rounded to the nearest fraction on an inch.
Step 2: Tools & Materials
The tools used for this are common tools that most homeowners and DIY’ers have around the house/shop:
Tools:
Measuring Tape & Roofing Triangle
Miter Saw
Router, Router Table, & Straight Cut Bit (Table is Optional)
Pocket Hole Jig (Kreg or Similar)
Clamps. Lots of Clamps
Drill
Rubber Mallet
Sanding Block and Sand Paper
1/4 Sheet Sander
Belt Sander (I used an old 1" table top belt sander for this)
Materials:
(5) 1”x2”x8’
(4) 1”x3”x8’
(1) 1”x4”x8’
(2) 2”x2”x3’
I bought white wood for all of the 1x3’s, 1x4, and (1) 1x2. These would all be used for the framing of the table and the bottom shelf. I bought red oak, poplar, and pine for the remaining (4) 1x2’s. I was trying to match the legs to the framing materials, but I could only find poplar 2x2’s and they were pretty close to the white wood in color so I bought those for the legs.
Step 3: Framing and Squaring
I started the table by cutting the legs and top and bottom skirts. By taking your time with the cutting and attaching all these parts the table legs as the first step, the table should come out square without any corner to corner wobble. I attached each skirt piece with (2) screws recessed into pocket holes. I also added a couple cross-braces to support the shelves (not pictured). Measure twice, cut once...
At first mine wobbled. A lot. This confused me for days as I was so careful when putting it together. It took me a couple days to realize it, but the problem was that the basement floor is not level. There are bumps and ridges all over it; very minor and not really noticeable to the naked eye, maybe only an 1/8-th of an inch or a little more, but enough to make the table wobble and me think I was crazy for a day or two. I moved it upstairs and tried it on the kitchen floor, and the living room carpet and it was all good.
Step 4: Top Frame
Next I went to the top frame (the part around the fancy X design). The idea for this frame was to mount the X to a piece of 1/4" plywood so that all pieces could be glued in place. The wood chosen for the X design was the same thickness as the top frame wood, so a routed channel was needed in the bottom half of the frame (the 1x4s) that was the same thickness as the plywood in order to keep the top of the table at a constant height. You can see this channel in a few of the pictures. The X-design will be supported by this 1" overlap in which the plywood will rest on the 1x4 frame around all the edges and by a single cross bar in the center. I used leftover Birch plywood from a previous project.
I then cut a similar frame out of 1x3s and the two halves of the frame would eventually be sandwiched around the X and plywood holding it all in place and maintaining a flat level top across the whole table.
Do as I say, not as I do: cut the mitered 45-degree bends before routing the channel in the 1x4 otherwise you will run out of wood and have to go back to the store for another 1x4 to get the last side of the frame. Rookie mistakes...
Step 5: Bottom Shelf
I went with a simple concentric square design for the bottom shelf. I cut the corners to 45-degree cuts and drilled some pocket holes to hold it all together then attached the shelving to the cross braces. I used pocket holes drilled into the skirt for the outer square of the shelf and used wood glue to hold the smaller squares in place. I don't plan on putting much weight on this shelf so the wood glue should be more than enough to hold it all together. To keep even spacing between the parts I used some scrap plywood as spacers to maintain a consistent 1/2” gap and some careful gluing and clamping.
Step 6: The X
This is where the CAD design helps. I was able to pull dimensions from the design drawing to plan the cuts. All four of the remaining 2x2s were needed for the X design.
This step definitely took me the longest. I don't have a table/station for my miter saw and therefore do not have a depth stop to use, so I needed to measure each cut before pulling the trigger. This step could be much faster with a proper depth stop.
With all the pieces cut I went back to the frame for a mockup to check the fit. This is basically a giant puzzle but the design drawing made short work of putting it all together. Some parts were a touch long so I took the whole mockup to the belt sander and carefully took the extra off of the pieces that needed a trim. This was also a very slow step since I wanted to make this as close to exact as possible. I checked it frequently while sanding each piece.
Once everything that needed it was sanded, it was all put back together for a final check. The 1/4" plywood was cut to fit inside the inlay of the 1x4's and the top frame, bottom frame, and X design were all clamped together. It all fit quite nicely. As you can see in the pictures there are a few small gaps and imperfections. I thought about using a wood filler to patch these but was worried about matching the wood color perfectly so that you couldn't tell there was any filler on it. In the end, I decided to not use the wood filler and leave the gaps.
I then glued and clamped the ply to the 1/4" inlay cut and left it for a few hours. Once the glue was set, I glued and clamped the top and bottom together. The edges were off by a little bit on every side, I cleaned this up with some sanding on the 1/4 sheet sander. Then I spread glue over the top of the plywood and carefully recreated the puzzled X-design over the glue. I had to use a rubber mallet to get the last few pieces in, then I threw a sheet of 1/2" plywood over the top, used some 2x4 as cross braces and clamped it and put heavy stuff on it overnight.
Step 7: Finishing and Lessons Learned
After unclamping the top surface it needed a little fine sanding to level out a couple high spots. I sanded the top surface and the top of the bottom shelf, high points were mostly located were corners didn't line up exactly. I also sanded down the outside top corners to a semi round finish that should hopefully prevent any splintering or sharp corners that could be bumped into once the table is done. I used a 1/4 sheet finishing sander with 120-400 grit paper for the surface sanding and a little elbow grease for the edge rounds. I thought about routing the corners, but after a few test pieces I couldn't find a bit that I liked for the corner round and it was just as easy to spend a few minutes to sand down the edges.
I clear coated everything with multiple coats of high gloss poly with a fine sand (400 grit) in between each coat on the table top. I used about 6-7 coats to get the shine on the top. I flipped to top upside down, lined up the base, measured a few times, and drilled the last few screws in to hold the top to the base. Finally I polished and buffed the top to a nice shine and it's done!
At first I was really hoping to have the legs the same type of wood as the rest of the frame; however, as this was coming together I really started to like the looks of the poplar legs. I also don't mind the looks of the small gaps in the top design. Some of the small ones filled in with poly as I was coating the top and the largest one is less than 1/8-th of an inch which is not perfect, but it's pretty tiny. The top is extremely smooth with no hangups at all despite these few gaps so I really can't complain at all about that.
Lessons Learned:
Don’t route the full length of the 1x4 before cutting the mitered 45-degree angles. As you cut the 45’s , the front edge of the first 1x4 piece will become the back edge of the second and so on and so on. I realized this after the fact and had to buy another board for the last 1”x4”x24” part.
Plywood scraps from old projects make great spacers when you need a 1/2" or 1/4" space on something.
You can never have too many clamps. I used heavy stuff when I felt like I didn't have enough clamps and dropped a 10lb weight on my foot. It hurt a lot. Clamps are much easier and less painful.
A pocket hole jig is an invaluable tool for anyone looking to build a furniture or cabinets. This was my first attempt at using one and it was pretty fool proof and worth every penny I spent on it.
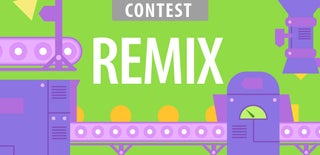
First Prize in the
Remix Contest 2016
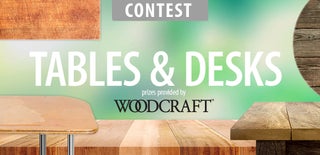
Second Prize in the
Tables and Desks Contest 2016
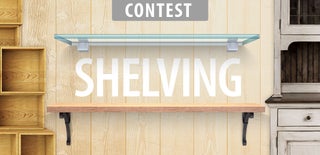
Participated in the
Shelving Contest 2016