Introduction: Turn a Washing Machine Into a Floor Lamp.
I have always liked to turn things that would normally be disposed of or thrown away into something new and usable. This project had been on my mind for quite a while and the opportunity came when a neighbor was replacing her old broken washing machine that had become too expensive to repair.
Step 1: Have a Look at the Video...
Have a look at the video above to see how I built the lamp or follow the instructions below.
Here is a list of the items needed to build the floor lamp.
Materials needed:
Washing machine (stainless drum)
Wood for the legs
Lamp holder
Electrical cable and plug
Lime scale remover
Polishing compound
Paint
Tools:
Saw
Drill/screwdriver
Wood glue
Wood screws
Drill bits
Sander
Paint brush
Step 2: The Washing Machine.
To begin, I with some help lifted the broken washing machine onto a table so it would be at a good height for working on. I took out all the screws that I could see around the machine and then removed the top to reveal all the insides of the machine.
Step 3: Disassembly
The stainless steel drum which is encased in a hard plastic shell was mounted on springs which were attached to the top and bottom of the washing machine frame. There are concrete counter weights attached to this plastic outer shell for which I believe are to reduce vibration when the machine is spinning. A good proportion of the weight in a washing machine comes from these weights.
I unbolted these weights and disconnected the mounting springs and any other wiring and pipe work. After doing all this I could now remove the stainless steel drum which was still inside the hard plastic shell from the surrounding frame.
Step 4: More Dismantling.
To get the drum out I removed all the bolts that were holding the plastic case together. There were about 18 of these altogether.
Step 5: Removing the Plastic Case.
I then removed the top section of the case revealing the drum inside. Getting the other part off would be a bit more difficult.
Step 6: Plastic Case.
I turned the case upside down and removed this wheel part to reveal a ball bearing on which the drum spins. I had to hit this part with a hammer to get it to separate. The drum was now free of the case. I then set it aside to start work on the legs.
Step 7: The Legs.
I had some 1 ¼ inch timber in my shed which had been left over from another project I did. I marked the length and all the intersections of the leg onto the wood.
Step 8: Leg Layout.
In this picture you can see the layout and sizes of the leg I used. I finished marking the leg layout with a long piece of wood.
Step 9: Cutting the Legs.
After clamping the wood to the table I cut out the leg shape freehand with a circular saw.
Step 10: Cutting the Legs Contd.
When I had the first leg cut out I used it to mark the other two, which I then cut out in the same way as before. The reason I went with three legs instead of 4 is that it won’t rock if the floor is slightly uneven.
I then clamped the three legs together and using my belt sander sanded them evenly.
Step 11: Center Piece to Join Legs.
I had to come up with a way to join all the legs together at the top. I went with this way as I think it was the easiest. It would have been easier to do all the cuts on a table saw but mine is broken and beyond repair so I used my circular saw set at 30 degrees.
Step 12: Center Piece Contd.
After cutting to length I drilled a 3/8 hole down the middle of this connecting piece. This is allow the electric cable to enter the steel drum.
Step 13: Attaching the Legs.
To attach the legs to the center piece I used glue and screws. I predrilled holes with a forstner bit and then attached with wood screws. Be careful the screws are not too long and block the hole for the electric cable. I learned the hard way!
Step 14: Attaching the Legs Contd.
When I had all the lags attached I inserted wood plugs to cover the screws and fill the holes. When all the glue had set I sanded them flush.
Step 15: Painting the Legs.
I decided to paint the legs black and gave them 3 coats of a satin finish. I gave a light sanding before the final coat.
Step 16: Cleaning the Stainless Steel Drum.
I live in a hard water area so the stainless drum was covered in limescale! I didn’t want to use anything that would scratch the stainless steel (steel wool) when removing the lime scale so I went with a powerful acid descaler. Be sure to use protective gear if using acid and use in a well ventilated area. As per instructions I let the acid sit for a while before neutralizing and removing it with water.
Step 17: Polishing the Drum.
The acid did a great job removing the limescale but it left the stainless steel with a dull finish in places. To fix this and bring the stainless steel back to a sheen I used a paste compound. Now the proper way to do this is probably with some sort of powered polishing wheel but I don’t have one so I ended up using a cloth and lots of elbow grease! I got a good work out that day.
Step 18: Marking Position of the Legs.
I turned everything upside down and marked the position of the legs on the drum. I then drilled holes for the screws to attach the legs and also in the center for the cable.(inset picture)
Step 19: Electrical Components.
In this picture you can see the 3 core electric cable a lamp bulb holder and a brass fitting to hold the bulb holder in place.
Step 20: Wiring the Bulb Holder.
I pulled the cable up through the hole drilled earlier and then through the hole in the drum before wiring the live, neutral and earth in the correct terminals and then reassembling the lamp holder back together.
Step 21: Inside the Drum.
This is a picture of the inside of the drum before and after the holder was screwed into place. You can see the brass fitting I mentioned earlier screwed to the drum. The lamp holder then screws onto this.
Step 22: Checking All Is Working.
I inserted a 60 watt light bulb, wired the plug correctly and inserted a 3 amp fuse and checked everything was working. Your electrical requirements may different where you are located so be sure to follow your local regulations.
Step 23: Trying It Out!
When all this was done it was time to bring it inside to check it out! Standing at a total height of 67 inches and a shade diameter of 19 inches it is quite a futuristic looking floor lamp and it won’t suit everyone’s taste but I like it!
Step 24: Cool Patterns.
It throws some amazing shapes and patterns onto the walls of a room.
Step 25: And That's It!
And that is that! I would love to know what you think of it good or bad. As I said before it may not be to everyone’s taste but I love how something that would normally be discarded or possibly be broken down to be recycled can be salvaged and turned into something totally different than its intended use to create something that is functional and modern looking.
The remains of the washing machine were brought to a recycling center.
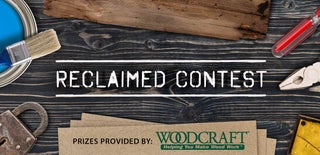
Participated in the
Reclaimed Contest 2017