Introduction: Ultimate AIO, Totally Over-Engineered, Dremel/Rotary Tool Drill Press / Sander / Grinder / Router
There are some really good Instructables showing how to make a Dremel/rotary tool drill press that inspired me to make one for myself. As I started designing, I wondered if I could combine the drill press functionality with a sander and while I was at it, also add the router functionality. And oh, make it flexible enough so it could be moved horizontally and vertically, swiveled and rotated. Basically, do everything except make me coffee (wait! no, never mind).
And here is the finished product. Chances are, I will never use most of its features. And if someone were to ask me why I did it anyway, I will look them in the eye and say with a straight face "Because it wasn't there".
This was made with scraps I had lying around the workshop, which is why you'll notice varying types of woods, some stained, others not, etc. That's also why it's not as polished as I would have liked it to be but it was meant more as a proof-of-concept.
The only things I bought were:
- 1/2" aluminum rod
- insert nuts
- wing nuts
- Jog knobs
As I don't have any plans to share beforehand, I'll start with what got finally made and how it's used. That should help you follow along the actual build.
Step 1: Using It
As a drill press, the height can be raised/lowered and then locked in place to accommodate varying height work pieces. Actual up/down motion is achieved by moving the tool up/down by hand with a travel of ~ 2 1/2".
It can be tilted and locked to any angle (45 degrees, flat, upside-down and any angle in-between).
Step 2: Using It: Router Table
Lower the entire assembly, slide it in so the collet is lined up with the hole and screw it to the base to immobilize the unit.
Flip it over and clamp it - together with the fence - to the workbench/table and voila, a functional router table.
Step 3: The Carriage
I did not plan this out beforehand and just started building with the Dremel carriage and built around it i.e. inside-out. As a result, the measurements are not very specific; I will mention the numbers as we go along but note that they are the result of decisions I took at each step and not based on a grand plan.
Started with
Step 4: Swivel
This sub-assembly enables the rotary tool to swivel and rotate in two planes.
Step 5: Horizontal Sliders
Two 9" pieces of 1/2" aluminum rods that get inserted and glued in to two wooden blocks.
Step 6: Connecting Block
I consider this the 'heart' of the project, which allows the rotary tool's height to be raised/lowered and moved forward/backward and also to lock it in place.
A lot going on here. My first attempt at the prototype worked fine but was built up and inelegant, so I made another one for the final version.
Step 7: Vertical Sliders
Two 18" pieces of the aluminum rod are inserted into the stacked ply base (6" x 1 1/2" x 2"). The two rods are ~3" apart on-center and are inserted all the way into the ply block. The back is 4" x 18" and is glued to the block base, which has a through hole in the middle to attach that sub-assembly to the overall base.
When I started, I thought it'd be useful to be able to take the overall base off but as things progressed, realized that may not happen. So this is one step where you can just glue/screw the ply stack to the overall base.
Step 8: Drill Press Base / Router Table
The drill press base is 18" x 17" and functions as the router table base when flipped over.
Step 9: Assembly: Putting It All Together
So now we start pulling it all together beginning with attaching the horizontal sliders to the swivel assembly with 2 wing nuts.
The slider part of the carriage is then connected with another wing nut.
Step 10: Assembly: Vertical Rods Sub-assembly
A 1/4" x 20 threaded bolt holds the vertical rods sub-assembly to the 3/4" ply base.
Step 11: Assembly: the 'heart' Brings It All Together
The 'heart' of the project is slipped on to the vertical rods and then the horizontal rods are in turn slipped in to it. All 4 rods can be secured in place with winged bolts.
Step 12: Assembly: Mounting the Tool
The slider assembly is slipped in and the rotary tool tightened in the strap clamps.
Step 13: Router Table Fence
A simple piece of 3/4" ply 3" high becomes the fence for the router table.
Step 14: Last Words
So that's that - hope you improve upon and find more uses for it!
And if you like the Instructable, please vote for me in First Time Author contest.
NJ: Designing, Building, Improving, Solving
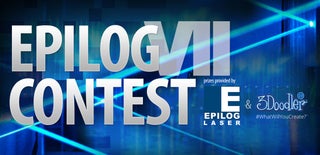
Participated in the
Epilog Contest VII
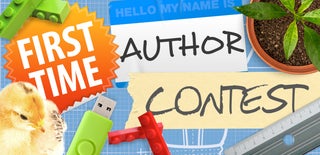
Participated in the
First Time Author Contest