Introduction: Ultrasonic Array
In this project we will show you how to build a phased-array controller and a flat array of 8x8 elements. These systems can be used for acoustic levitation, haptic feedback or directional speakers.
This is quite a complex project so I would recommend a little bit of knowledge on ultrasonics, computer science and electronics.
Do not forget to check the other Instructables for more information
More detailed information in our open paper: http://ieeexplore.ieee.org/document/8094247/
All the detailed steps are in the attached video.
Step 1: Gather the Components
The source code is available here: https://github.com/asiermarzo/Ultraino
You can get precompiled versions of the simulator V1.1 for java 8 and v2 for java 11.
You will also find the STL files for the 3D printed arrays and the AI files for the laser-cut arrays.
The PCB files for manufacturing are also there here I recommend to use PCB Shopper to look for a cheap manufacturer. The dimensions of the board are 62mm by 115mm and it has 4 layers. It would be a good idea to order an stencil if you do not want to solder the components by hand.
The BOM can be found here.
Step 2: Assemble the Driver Board
You can solder by hand, or use solder paste and a reflow oven. I am not the most proficient SMD solderer, there are lots of goods tutorials on the Internet.
The code for the Arduino Mega is here
If the output signal on the ports is not 40kHz you can try to use IDE 1.6.0 or the Optimization -O3 flag.
Step 3: Assembling a 8x8 Flat Array
You can find how to mark the polarity of the transducer in the previous Instructable In that Instructables there is also a guide to buy transducers for a reasonable price.
The components can be found here
- You can also use the great integrated PCB from Thomas Grooten.
The last image shows the pin numbers of each pin, luckily you will not need to do the pin assignment manually but using the semi-automatic method shown in the video.
Attachments
Step 4: Single-sided Levitation
I used a 2mm styrofoam particle and a metallic grid to place it in the trap.
The base of the array is laser-cut: link to github
The simulation file is here:
Step 5: Standing-wave Levitation
Step 6: Haptic Feedback
Step 7: Directional Speaker
I used this audio amplifier TDA7492P but anything that you can find will probably do the job.
* This is just a quick way of getting a directional speaker, the sound quality is not great and it is not very powerful. I am working on a dedicated directional speaker that will be released soon.
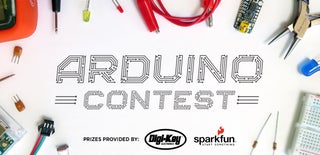
Participated in the
Arduino Contest 2017